OEM medical injection molding is a specialized manufacturing process that plays a pivotal role in producing high-precision medical devices. This advanced technique allows healthcare innovators to create custom medical components, ensuring both quality and reliability. As the demand for cutting-edge medical technologies grows, OEM medical injection molding has become indispensable for streamlining production and maintaining stringent regulatory compliance. Renowned companies at the forefront, delivering solutions tailored to diverse healthcare needs, leverage precision mold medical technologies to enhance efficiency. OEM medical injection molding manufacturer develop high precision medical injection molded products devices and components competently. From surgical tools to diagnostic equipment, this method continues to revolutionize medical device manufacturing, fostering innovation and enhancing patient care. Its impact extends across the global healthcare industry, ensuring the development of safer and more efficient medical technologies.
Low-Volume to High-Volume Production Capabilities
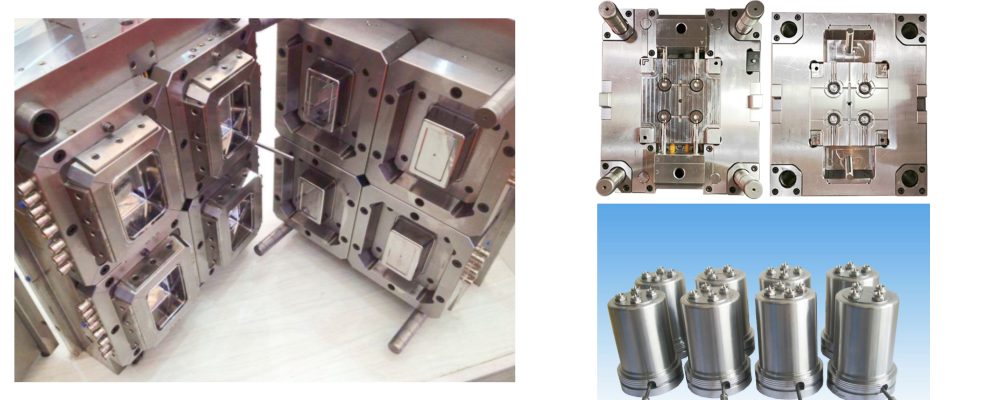
Attribute | Details |
---|---|
Brand Name | LY Medical Injection Mold |
Place of Origin | Dongguan, Guangdong, China |
Shaping Mode | Plastic Injection Mould |
Processing Services | Moulding, Cutting, CNC Milling, CNC Lathe, Drilling |
Materials | ABS, PA66, PP, PC, PVC, PMMA, PEEK, POM, TPU, PE, PPS, PTFE, Silicone Rubber, Nylon, etc. |
Surface Treatments | Polish, Texture, Etching, Electroplating, UV Coating, Painting, Rubberizing, Logo Engraving |
Tolerance | ±0.003mm ~ ±0.1mm |
MOQ | 1 Piece |
Mold Life | 200,000 ~ 10,000,000 shots |
Technology | Injection Molding, CNC Injection, Extruding, 3D Printing |
Drawing Formats Accepted | STEP, IGS, DWG, PDF, CAD, STL, SLDPRT, UG, X-T |
Certifications | ISO9001:2015, ISO13485:2016 |
OEM Services | Fully supported |
Lead Time | 7-14 days |
Packaging Details | Foam wrap protection, followed by carton packaging |
Applications | Medical Devices |
Quality Control | 100% Inspection, Process Checking, Final Inspection before Shipping |
What Is OEM Medical Injection Molding?
Definition
OEM medical injection molding is the manufacturing process where Original Equipment Manufacturers (OEMs) design and produce medical components or devices using injection molding techniques. This process involves melting plastic or other specialized materials, injecting them into precise molds, and cooling them to create finished parts. Medical molding engineers are essential in ensuring that these components are manufactured with high precision, meeting the rigorous standards required for medical applications. Known for its ability to produce complex, high-precision, and durable components, OEM medical injection molding is a key solution for cost-effective and scalable production in the healthcare sector.
Why OEM Services Are Critical in Medical Device Manufacturing
The healthcare industry requires strict adherence to quality and safety standards, making OEM medical injection molding a cornerstone of medical device production. By outsourcing to OEMs, medical companies gain access to advanced molding expertise, precision engineering, and a faster time-to-market. These services also ensure compliance with stringent regulatory frameworks, such as ISO 13485, while reducing operational costs.
OEM Injection Molding Medical Industry: Benefits and Applications
The OEM injection molding medical industry has transformed healthcare manufacturing by offering several advantages:
- Factors Driving Its Use: The need for mass production, accuracy, and material compatibility in medical devices drives the adoption of OEM injection molding.
- Benefits for Healthcare: This process enhances device reliability, minimizes production waste, and ensures consistent quality in items like syringes, catheters, and surgical instruments.
- Impact and Examples: Cases such as implantable devices and diagnostic equipment showcase how this industry meets the demand for innovation and safety.
Industries Benefiting From OEM Injection Molding
Although its primary focus is on healthcare, OEM medical injection molding also finds applications in industries like automotive and industrial manufacturing. These sectors rely on the process for producing high-precision components such as fuel injectors, gear assemblies, and custom industrial parts. The medical industry, however, stands out as the most significant beneficiary, leveraging the technology for creating life-saving devices that meet the highest quality standards.
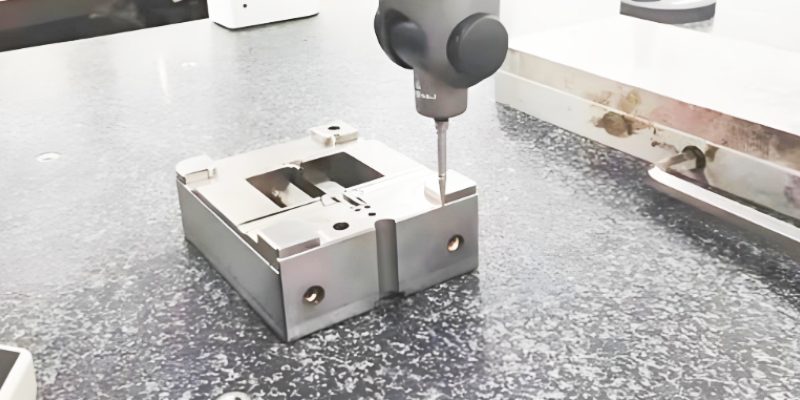
How Does OEM Medical Injection Molding Work?
OEM (Original Equipment Manufacturer) medical injection molding is a specialized process for producing precision medical components and devices using advanced injection molding techniques. This method ensures strict compliance with the regulatory and functional demands of the healthcare industry. Below is a detailed explanation of the process:
Design and Prototyping
The process begins with the creation of a custom design tailored to the specific medical device or component. Key steps include:
- Requirements Analysis: Collaborating with OEMs to define specifications, including material choice, dimensions, tolerances, and functionality.
- CAD Modeling: Developing a 3D model using computer-aided design (CAD) software to visualize the component.
- Prototyping: Creating a prototype through rapid prototyping techniques like 3D printing or CNC machining for testing and validation.
Tooling Development
After the design is finalized, a mold tool is developed. This step involves:
- Mold Design: Creating a detailed plan for the injection mold, ensuring it can produce high-precision parts with the required features.
- Material Selection: Using durable materials like stainless steel for the mold to withstand high-pressure injection and ensure long-term reliability.
- Mold Fabrication: Employing CNC machining and EDM (Electrical Discharge Machining) to create the mold cavity with intricate details.
Material Selection
Material choice is critical in medical injection molding due to the need for biocompatibility, durability, and compliance with medical standards such as ISO 10993 or USP Class VI. Common materials include:
- Thermoplastics: Such as Polyethylene (PE), Polypropylene (PP), or Polycarbonate (PC).
- High-Performance Polymers: Like PEEK (Polyether Ether Ketone) for components requiring extreme durability.
- Silicone: For flexible and soft components like seals or tubing.
Post-Molding Operations
To meet stringent medical standards, additional steps are often required:
- Trimming and Deflashing: Removing excess material or burrs to ensure smooth edges.
- Surface Treatments: Applying coatings or sterilization processes for biocompatibility.
- Assembly: Integrating molded parts into complete medical devices, if applicable.
- Quality Control: Performing rigorous inspections, including dimensional checks, material testing, and functional validation.
Regulatory Compliance
OEM medical injection molding adheres to strict regulatory standards to ensure the safety and efficacy of the produced components:
- ISO 13485 Certification: Ensuring compliance with quality management standards specific to medical devices.
- Cleanroom Manufacturing: Many medical components are molded in cleanroom environments to maintain sterility and reduce contamination risks.
- FDA Approval: For products destined for the U.S. market, meeting FDA regulations is essential.
OEM medical injection molding is a cornerstone of modern healthcare manufacturing, enabling the production of reliable, high-quality medical devices that improve patient care. This meticulous process ensures that components meet the highest standards of safety, precision, and functionality
OEM Medical Injection Molding Manufacturing Process
OEM (Original Equipment Manufacturer) medical injection molding is a highly specialized manufacturing process designed to produce precise and compliant medical components. Below is a detailed, process-oriented explanation focusing on each stage of the workflow.
Injection Molding Process
This is the core phase where medical-grade components are manufactured. It involves the following steps:
Material Preparation
- Feed pellets or granules into the hopper.
- Add colorants or functional additives if necessary.
- Preheat materials to achieve consistent viscosity.
Heating and Plasticization
- Raw material is moved into a heated barrel by a reciprocating screw.
- Temperatures typically range between 200°C to 400°C, depending on the polymer type.
- The material is melted into a homogenous liquid state under controlled conditions.
Mold Filling (Injection)
- The molten material is injected into the mold cavity under high pressure (up to 20,000 psi).
- A precision-controlled screw or ram ensures accurate shot sizes.
- Sensors monitor flow rates and pressures to prevent defects like short shots or sink marks.
Cooling and Solidification
- The mold, equipped with cooling channels, rapidly cools the injected material.
- Cooling time is optimized based on part geometry, wall thickness, and material thermal properties.
- Uniform cooling ensures dimensional stability and prevents shrinkage or warping.
Ejection
- Once cooled, ejector pins or plates carefully remove the part from the mold.
- Advanced systems like vacuum-assisted ejection are used for fragile or intricate parts.
- Ejection mechanisms are designed to avoid surface damage or deformation.
Post-Molding Processes
Trimming and Deflashing
- Remove excess material or flash using laser trimming, ultrasonic knives, or manual techniques.
Surface Treatment
- Apply coatings or sterilization to improve performance and ensure biocompatibility.
- Common sterilization methods include ethylene oxide (EtO) and gamma radiation.
Assembly and Integration
- Multi-component parts are assembled into functional devices using techniques like ultrasonic welding or adhesive bonding.
OEM medical injection molding is a meticulous and innovation-driven process, ensuring the production of high-quality medical components critical to modern healthcare. By focusing on material properties, advanced tooling, and process control, it ensures efficiency and compliance at every stage.
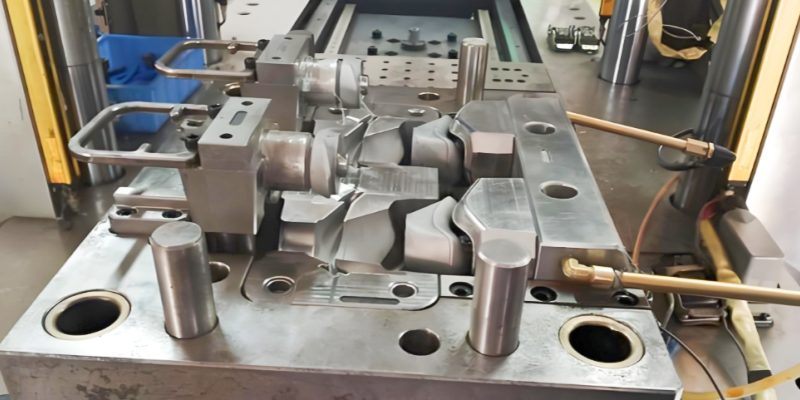
OEM Medical Injection Molding Production And Quality Standards
OEM (Original Equipment Manufacturer) medical injection molding plays a crucial role in manufacturing precise and reliable components for the medical industry. This process not only involves cutting-edge production techniques but also strict adherence to quality standards to ensure safety, durability, and regulatory compliance. Here’s an in-depth exploration of the production process and associated quality standards.
Quality Standards in OEM Medical Injection Molding
1. Regulatory Compliance
Medical devices must meet stringent global standards to ensure patient safety and efficacy:
- ISO 13485: Certification for quality management systems specific to medical device manufacturing.
- FDA Requirements: Adherence to U.S. Food and Drug Administration regulations for medical devices.
- ISO 10993 Testing: Validation of biocompatibility for all materials in contact with human tissue.
2. Cleanroom Manufacturing
To minimize contamination risks, production often occurs in controlled environments:
- ISO Class 7 or 8 Cleanrooms: Maintain strict environmental controls for airborne particles, temperature, and humidity.
- Hygiene Protocols: Enforce rigorous standards for personnel and equipment entering the cleanroom.
3. In-Process Monitoring
Ensure consistent quality during production with real-time monitoring systems:
- Sensors and Automation: Track key parameters such as pressure, temperature, and cycle time.
- Machine Calibration: Regularly calibrate molding machines to maintain precision.
4. Inspection and Testing
Components undergo detailed inspections to confirm they meet required standards:
- Dimensional Accuracy: Use coordinate measuring machines (CMM) or laser scanners to verify dimensions.
- Material Testing: Conduct chemical and mechanical tests to ensure material performance and safety.
- Functional Validation: Simulate real-world use cases to test component performance under stress.
5. Documentation and Traceability
Maintaining comprehensive records is essential for regulatory compliance and quality assurance:
- Batch Records: Document production details, including material lots, mold history, and inspection results.
- Serial Numbers: Apply unique identifiers to parts for traceability and recalls if needed.
6. Sterilization and Packaging
Final components are sterilized and packaged to ensure their integrity and usability:
- Sterilization Methods: Use processes like ethylene oxide (EtO) sterilization, gamma radiation, or autoclaving.
- Packaging Standards: Employ medical-grade materials and vacuum-sealing techniques to preserve sterility.
Benefits of Adhering to Quality Standards
- Patient Safety: Ensures all components meet stringent medical requirements.
- Reliability: Guarantees consistent performance in critical medical applications.
- Regulatory Compliance: Facilitates global market entry by meeting international standards.
- Cost Efficiency: Reduces waste and rework by maintaining high production quality.
OEM medical injection molding combines advanced manufacturing techniques with rigorous quality control to produce safe, precise, and reliable medical components. Adhering to these production and quality standards is essential for creating products that meet the demands of the medical industry while ensuring patient safety and regulatory compliance.

Capabilities of OEM Medical Injection Molding Manufacturers
OEM medical injection molding companies possess diverse capabilities to meet the stringent demands of the healthcare industry. Their advanced technologies, material expertise, and regulatory compliance ensure high-quality production for medical devices and components. Below is an in-depth exploration of the capabilities offered by leading companies.
FUJIU Medical Injection Mold
We are renowned for its expertise in working with high-performance medical-grade materials like PEEK, PPSU, and PSU. These materials are ideal for creating sterilizable and durable medical instruments.
- Technological Advantages: The company excels in overmolding, insert molding, and multi-component injection molding, allowing the creation of complex medical parts with enhanced functionality.
- Key Applications:Focuses on instruments used in minimally invasive surgeries, ensuring precision and safety. Their advanced capabilities address the challenges of creating reliable, long-lasting devices that meet healthcare standards.
Since 2004, we at FUJIU Medical Injection Mold have been dedicated to leading the medical injection molding industry. From mold design to automated assembly, we provide a one-stop solution for all your needs. With innovation and excellence at the core of our approach, we redefine success by delivering high-quality products and services tailored to meet your specific requirements.
Our Core Capabilities in OEM Medical Injection Molding
- Expertise in Medical Injection Molding
We specialize in manufacturing high-quality components for medical devices. With extensive knowledge of medical-grade plastics, we ensure that every product meets the stringent standards of the medical industry, including biocompatibility, durability, and reliability. - Precision Mold Medical Solutions
Our precision molds are crafted to meet the most demanding requirements of complex medical devices. Using advanced techniques and strict tolerance controls, we deliver molds that align perfectly with your design specifications while maintaining cost efficiency. - Automated Assembly Services
Beyond molding, we offer seamless automated assembly solutions that integrate production with final assembly. This ensures reduced lead times, lower costs, and consistent product quality—all critical for medical applications. - Material Expertise and Certification Compliance
Our team leverages deep expertise in medical-grade materials, ensuring compatibility with your specific applications. All our processes adhere to ISO certification standards, guaranteeing chemical resistance, sterilization durability, and structural integrity in our products.
What We Offer
- Fast Prototyping and Sampling
We provide rapid prototyping services to help you test and validate designs before full-scale production, significantly reducing development timelines. - Flexible Low MOQ Options
Whether your project is large or small, we accommodate your needs with low minimum order quantities, making it accessible for startups and small-scale operations. - Efficient Delivery
Thanks to optimized processes, we ensure fast and reliable delivery without compromising quality. - Strict Cleanliness Standards
Our manufacturing facilities adhere to rigorous cleanliness and hygiene requirements, ensuring that every product meets the high standards of the medical industry.
With over two decades of experience, we combine innovation, precision, and reliability to provide unmatched OEM medical injection molding solutions. From initial design to final delivery, we focus on ensuring product quality and exceeding customer expectations. Partnering with us means choosing a team that is as committed to your success as you are.
OEM Medical Molding Manufacturer: Expertise and Innovation
An OEM medical molding manufacturer combines cutting-edge technology with precision engineering to deliver tailored solutions for the medical industry.
- Factors Influencing Success: Material innovation, quality control, and scalability are key drivers for manufacturers. Companies prioritize state-of-the-art machinery and skilled personnel to maintain their competitive edge.
- Advantages: By partnering with an experienced OEM medical molding manufacturer, clients gain access to customized solutions, streamlined production, and compliance with global medical standards.
OEM Medical Molding Company: Bridging Quality and Efficiency
An OEM medical molding company serves as a vital link between design and production in healthcare innovation.
- Critical Roles: Such companies bridge the gap between concept and mass production, ensuring precision, reliability, and cost-efficiency.
- Case Studies: Leading OEM medical molding companies have contributed to breakthroughs in diagnostic devices, implantable components, and single-use medical tools, showcasing their transformative role in modern healthcare.
OEM medical injection molding companies set industry benchmarks with their unparalleled expertise and innovation, driving advancements in healthcare manufacturing.
Applications of OEM Medical Injection Molding
OEM medical injection molding is a highly versatile and reliable manufacturing process used to produce a wide variety of medical molding products. This process involves the creation of precise and high-quality parts tailored to meet stringent medical industry standards. Below, we explore some of the key applications of OEM medical injection molding, highlighting the diverse range of products and innovations that it supports.
Examples of Medical Products
OEM medical injection molding is crucial for the production of numerous essential medical devices. Some of the most common examples of medical products produced through this process include:
- Catheters: These flexible tubes are used for various medical purposes, such as delivering medication, draining fluids, or performing diagnostic procedures. The precision and biocompatibility required for catheters make OEM medical injection molding a suitable method for their production. Injection molding for Class I medical products ensures that catheters are manufactured to high standards of quality, biocompatibility, and safety.
- Syringes: OEM medical injection molding ensures the production of high-quality, sterile syringes that are safe and effective for administering medications. The molding process allows for the production of syringes in different sizes and configurations to meet specific patient needs.
- Diagnostic Tools: OEM medical injection molding is integral in creating diagnostic tools such as test tubes, pipettes, and specimen collection containers. These tools must be manufactured with high precision to ensure accurate test results and patient safety.
- Surgical Implants: Surgical implants, such as orthopedic devices, dental implants, and joint replacements, are often produced using OEM medical injection molding. The process allows manufacturers to create durable, precise implants that fit a patient’s specific requirements.
- Labware: Laboratory equipment such as petri dishes, test tubes, and other medical-grade plastic containers are produced through OEM medical injection molding, ensuring that they meet the strict standards required for safe and reliable use in medical testing and research.
Emerging Applications in Advanced Medical Devices
As the medical industry continues to innovate, OEM medical injection molding plays a vital role in the development of advanced medical devices. Some of the emerging applications include:
- Organ-on-a-Chip: This technology mimics the human organ environment on a small chip, allowing researchers to test drugs and treatments on a cellular level. OEM medical injection molding provides the precision needed to create these complex devices, which require intricate microstructures.
- Wearables: Wearable medical devices, such as heart rate monitors, glucose trackers, and other health-monitoring gadgets, often rely on OEM medical injection molding. The ability to create small, lightweight, and durable components makes injection molding ideal for these devices, which are designed for continuous use and patient comfort.
Cross-Industry Applications in Automotive and Industrial Sectors
OEM medical injection molding isn’t limited to medical applications. The precision and versatility of the process also make it highly valuable in other industries, such as automotive and industrial sectors. Some of the cross-industry applications include:
- Automotive Components: OEM medical injection molding is used to create custom precision components for the automotive industry, such as fluid connectors, valves, and safety components. The high tolerance and durability required for these parts make them suitable for injection molding.
- Industrial Components: Industries that require precise, durable parts, such as aerospace, electronics, and manufacturing, also benefit from OEM medical injection molding. Components such as enclosures, seals, and structural elements are produced to exact specifications, ensuring reliability and performance across different applications.
The Role of OEM Medical Molding Factory in Medical Device Manufacturing
An OEM medical molding factory is a critical player in the production of medical devices through injection molding. These specialized facilities are equipped with advanced molding machines and technologies that can meet the stringent quality standards required for medical products. An OEM medical molding factory is responsible for producing consistent, high-quality components that meet regulatory requirements such as FDA approvals and ISO certifications.
OEM medical molding factories often work closely with medical device companies to develop custom solutions for specific products. By collaborating with experts in the field of medical injection molding, these factories can create molds tailored to the precise dimensions and specifications needed for each application. Whether it’s producing a small batch of specialized surgical instruments or a large volume of disposable medical supplies, the role of the OEM medical molding factory is indispensable in the healthcare sector.
Key Benefits of OEM Medical Injection Molding
OEM medical injection molding offers a range of advantages, particularly in the production of medical-grade components. The precision, cost-effectiveness, customization capabilities, and compliance with industry standards make it a vital process in the medical device manufacturing industry. Below, we explore the key benefits of this advanced manufacturing technique and how it contributes to the production of reliable and high-quality medical devices.
Precision and Accuracy: Essential for Medical-Grade Components
One of the standout benefits of OEM medical injection molding is its exceptional precision and accuracy. Medical devices often require parts with intricate designs and strict tolerances to ensure they function correctly and safely. OEM medical injection molding allows manufacturers to produce components with tight dimensional control, which is critical for medical-grade products like syringes, surgical instruments, and implants. Mold core pins for medical industry are essential in this process, helping to create precise cavities and ensuring that the final parts meet the exact specifications required for medical applications.
- Benefits of Precision: The high accuracy achieved through OEM medical injection molding ensures that each part meets the required specifications. This precision is vital for ensuring the safety and efficacy of medical devices, particularly when components must fit together seamlessly or interact with sensitive biological systems.
- Applications: From catheters to diagnostic tools, the ability to achieve such accuracy makes OEM medical injection molding the preferred method for producing parts that need to be reliable and consistent in performance.
Cost-Effectiveness: Economical for High-Volume Production
OEM medical injection molding is known for its cost-effectiveness, especially in high-volume production runs. Once the initial mold is created, the process allows for the rapid production of large quantities of medical components at a relatively low per-unit cost. This makes OEM medical injection molding an ideal solution for manufacturers producing disposable medical devices like syringes, test tubes, and packaging materials.
- Economic Advantages: The cost efficiency of OEM medical injection molding is due to its high production speed and low labor costs. It is a scalable process, meaning that costs decrease as production volumes increase, providing significant savings for large-scale manufacturing.
- Long-Term Savings: In addition to the low unit cost, the high efficiency of the process reduces the likelihood of defects, leading to fewer production interruptions and less waste. This contributes to overall cost savings and allows manufacturers to offer competitive pricing on medical products.
Customization and Scalability: Tailored Solutions for Diverse Applications
OEM medical injection molding offers excellent flexibility in terms of customization and scalability. Manufacturers can produce parts in a variety of shapes, sizes, and materials, tailored to meet specific medical applications. The customization possibilities are vast, making it ideal for developing both standard medical devices and specialized, high-tech solutions like implantable devices and organ-on-a-chip systems.
- Customization: OEM medical plastic injection molding enables manufacturers to design and create unique components that meet precise specifications. Whether it’s a custom surgical tool or a specialized housing for medical electronics, the molding process can accommodate a wide range of materials and design complexities.
- Scalability: As demand for a product increases, OEM medical injection molding allows manufacturers to scale production without compromising on quality. This scalability is beneficial for manufacturers that need to meet fluctuating demand or enter new markets with rapidly rapid injection molding medical devices.
Compliance with Industry Standards: Ensures Safety and Reliability
Ensuring that medical products comply with stringent regulatory standards is essential for maintaining safety and reliability. OEM medical injection molding plays a crucial role in meeting these industry standards, such as FDA regulations and ISO certifications. The precision and quality control inherent in the molding process help ensure that products are not only safe for use but also perform reliably over time.
- Regulatory Compliance: OEM medical injection molding adheres to the highest industry standards, ensuring that products meet regulatory requirements. For example, medical devices must be made from biocompatible materials, which the injection molding process can precisely control.
- Quality Assurance: By using certified materials and adhering to established protocols, OEM medical injection molding guarantees that the produced components will be durable, safe, and suitable for their intended medical applications.
The Role of OEM Medical Device Injection Molding in Healthcare
An OEM medical device injection molding process is integral in the production of complex medical devices. These factories utilize specialized techniques and equipment to manufacture a wide range of medical products, from small single-use items like syringes to large, intricate devices like prosthetics and implantable devices.
- Importance of OEM Medical Device Injection Molding: OEM medical device injection molding enables the manufacturing of devices that require high-precision parts. For example, surgical instruments or diagnostic tools often require parts that must meet exact tolerances for proper function.
- Applications: This technique is crucial for the production of items that are critical to healthcare, ensuring that medical devices are reliable, effective, and compliant with safety standards. With advanced molding technologies, OEM medical device injection molding factories can meet the growing demands for both standard and custom medical products.
The Role of OEM Medical Molding in the Oem Medical Plastic Molding Factory
An OEM medical molding factory is key to ensuring that medical products are produced efficiently and meet all necessary quality standards. These factories specialize in manufacturing medical components with precise specifications, using advanced injection molding technologies to produce everything from simple parts to complex multi-functional devices.
- Benefits of OEM Medical Molding: The expertise within an OEM medical molding factory allows for the creation of high-quality products at scale. Whether it is a custom medical tool or a disposable item, these factories ensure that every product is made to the highest standards of quality and safety.
- Reliability in Production: OEM medical molding factories use state-of-the-art machinery and employ strict quality control measures to ensure that products are produced consistently and in compliance with medical regulations. This reliability is essential for the healthcare sector, where even the smallest manufacturing errors can have significant consequences.
Innovations in OEM Medical Injection Molding
OEM medical injection molding continues to evolve with technological advancements and innovations that improve the production of high-quality medical devices. These innovations help address the increasing demands for more durable, functional, and sustainable medical components. Below, we explore the latest innovations in OEM medical injection molding that are transforming the industry.
Use of High-Performance Thermoplastics for Enhanced Durability and Functionality
One of the significant innovations in OEM medical injection molding is the use of high-performance thermoplastics. These materials are chosen for their enhanced durability, flexibility, and ability to withstand harsh environments. High-performance thermoplastics, such as PEEK (Polyetheretherketone), PPSU (Polyphenylsulfone), and medical-grade LCP (Liquid Crystal Polymers), are used to manufacture medical devices that require superior strength, chemical resistance, and biocompatibility.
- Benefits of High-Performance Thermoplastics: These advanced materials provide medical devices with improved functionality, making them more suitable for demanding applications such as surgical implants, drug delivery systems, and diagnostic tools. They offer superior resistance to high temperatures, chemicals, and wear, ensuring that devices maintain their performance over long periods. Through thermoplastic injection molding medical, these materials can be precisely shaped to meet the exact specifications required for such critical applications, enhancing both durability and reliability.
- Applications: The use of high-performance thermoplastics is particularly beneficial in the production of components like surgical instruments, implantable devices, and diagnostic equipment that need to function reliably in a variety of environments, from hospitals to research labs.
Advanced Techniques like Liquid Silicone Injection Molding and Multi-Component Processes
OEM medical injection molding has seen the introduction of advanced techniques such as liquid silicone injection molding and multi-component molding. These processes enable manufacturers to create highly complex and customized medical devices with multiple materials or components integrated into a single product.
- Liquid Silicone Injection Molding: Liquid silicone rubber (LSR) is a flexible and durable material often used in medical applications where flexibility, biocompatibility, and sterilization are critical. LSR molding allows for the creation of parts with intricate designs, including seals, gaskets, and flexible tubing, which are crucial in devices such as pacemakers and respiratory systems.
- Benefits of Liquid Silicone Injection Molding: LSR offers a combination of flexibility, resistance to extreme temperatures, and biocompatibility, making it ideal for use in critical medical devices. Additionally, the liquid silicone injection molding process enables manufacturers to create parts with high precision and low waste, making it a cost-effective solution for complex medical components.
- Multi-Component Processes: Multi-component injection molding involves using two or more materials to create a single part, allowing for the integration of different properties such as rigidity, flexibility, and chemical resistance. This technique is widely used to produce medical components that require different materials for various functions, such as drug delivery systems, where one part might need to be flexible, while another part needs to be rigid and durable.
Sustainability Efforts: Recyclable Materials and Energy-Efficient Manufacturing
Sustainability is becoming an increasingly important consideration in the manufacturing of medical devices, and OEM medical injection molding is no exception. With growing demand for environmentally friendly practices, manufacturers are exploring ways to reduce waste, improve energy efficiency, and utilize recyclable materials in the production of medical components.
- Recyclable Materials: One of the major innovations in OEM medical injection molding is the use of recyclable thermoplastics and other sustainable materials, such as medical injection molding polymers. These polymers can be reused or recycled at the end of their life cycle, significantly reducing environmental impact. Materials like medical-grade polypropylene (PP) and polyethylene (PE) are being used in medical applications to reduce the environmental footprint of single-use devices.
- Benefits of Sustainability: By incorporating recyclable materials into the production process, manufacturers not only contribute to environmental conservation but also reduce production costs associated with raw materials. This move toward sustainability aligns with the increasing regulatory pressures for the medical device industry to adopt greener practices.
- Energy-Efficient Manufacturing: OEM medical injection molding manufacturers are also adopting energy-efficient technologies to reduce energy consumption during the production process. Innovations such as advanced molding machines, optimized cycle times, and the use of heat recovery systems are helping to lower the overall energy requirements of manufacturing while still maintaining high levels of precision and quality.
The Role of OEM Precision Medical Machining in Innovations
An important component of these innovations in OEM medical injection molding is the role of OEM precision medical machining. This advanced manufacturing technique focuses on producing highly precise and detailed parts that are integral to the medical device industry. OEM precision medical machining enables the production of complex and tight-tolerant parts that cannot be achieved with traditional molding techniques alone.
- Importance of OEM Precision Medical Machining: OEM precision medical machining is essential for producing parts that require high accuracy and reliability, such as components for implantable devices, surgical instruments, and diagnostic tools. This process ensures that each part is produced to exact specifications, meeting the stringent regulatory standards required in the medical field.
- Applications in Medical Devices: The integration of precision machining with OEM medical injection molding allows for the production of hybrid components that combine the benefits of both processes. For example, a surgical tool may have molded plastic components for lightweight and flexibility, combined with precision-machined metal components for strength and durability. This approach provides manufacturers with a more comprehensive and efficient solution for creating high-performance medical devices.
Choosing the Right OEM Medical Injection Molding Partner
When it comes to OEM medical injection molding, selecting the right partner is a critical decision that can significantly impact the success of your medical device manufacturing process. The right partner will not only ensure high-quality production but also contribute to the efficiency, safety, and compliance of your products. Below, we explore key factors to consider when choosing an OEM medical injection molding partner and how specific providers can benefit your business.
Factors to Consider: Experience, Certifications (e.g., ISO 13485), and Quality Systems
Choosing the right OEM medical molding partner begins with assessing their experience and capabilities in the medical injection molding industry. The medical field demands strict standards, and the right partner must demonstrate proficiency in producing medical-grade products that comply with relevant regulations.
- Experience: It is essential that your OEM medical injection molding partner has significant experience in the medical device industry. Experienced partners understand the unique challenges involved in medical device manufacturing, such as the need for precision, sterility, and biocompatibility. They are familiar with the regulatory requirements for medical products, including FDA approval and CE marking, and have a track record of delivering reliable and safe products.
- Certifications: Certifications, such as ISO 13485, are essential when selecting an OEM medical injection molding supplier. ISO 13485 is an international standard that ensures a medical device manufacturer adheres to stringent quality management systems. This certification demonstrates that the manufacturer maintains a high standard of quality control in the production process, which is crucial for the safety and reliability of medical devices.
Benefits of Partnering with Companies Like FUJIU Medical Injection Mold
Partnering with established companies, such as us, can provide numerous advantages for your medical device manufacturing needs. Our companies have extensive experience in the field and offer comprehensive services that streamline the production process.
- Expertise in Medical Device Manufacturing: We has a deep understanding of the medical device industry’s specific requirements. We specialize in producing high-precision components using advanced OEM medical injection molding techniques. This ensures that every part meets the highest standards of quality and performance.
- Advanced Technologies and Capabilities: Leading companies like FUJIU are equipped with state-of-the-art molding equipment and advanced technologies that enhance the manufacturing process. We utilize high-performance thermoplastics, liquid silicone rubber, and multi-component molding processes, all of which contribute to the creation of durable and reliable medical devices.
How OEM Providers Ensure Product Lifecycle Management from Design to Delivery
- Design and Prototyping: OEM medical injection molding partners collaborate with you from the early stages of product development. This involves creating prototypes, testing various materials, and refining the design to ensure that the medical device meets both functional and regulatory requirements. The partner’s expertise in design optimization can help streamline the process and minimize potential manufacturing issues later on.
- Manufacturing and Scaling: Once the design is finalized, the OEM provider uses advanced injection molding techniques to begin production. Whether you need small batch runs or large-scale manufacturing, they can scale the process to meet demand while maintaining consistent quality and compliance.
- Post-Production Support: OEM medical molding suppliers typically offer post-production services, including product packaging, sterilization, and logistics management, ensuring that the final product reaches its destination in a timely and safe manner. They may also provide ongoing support for product revisions, maintenance, or upgrades.
- Lifecycle Management Tools: Many OEM providers employ lifecycle management software to track the entire journey of the medical device, ensuring that all stages are documented, compliant, and optimized. This allows for better coordination between design, manufacturing, and delivery teams, enhancing the overall efficiency and success of the product.
The Role of OEM Medical Molding Supplier in Product Success
The choice of an OEM medical molding supplier plays a crucial role in the successful development and production of medical devices. A reliable supplier ensures not only the technical quality of the device but also its compliance with industry standards and regulations. Working with an experienced and certified supplier like our Injection Mold, or another trusted provider, can help navigate the complexities of medical device manufacturing and provide solutions that meet both commercial and regulatory requirements.
FAQs about Oem Medical Injection Molding
Medical injection molding is a specialized manufacturing process used to produce precise and high-quality components and devices for the medical industry. This process involves injecting molten materials, such as medical-grade plastics, into a mold cavity to form parts that meet stringent medical and regulatory standards. These components are often used in medical devices, surgical instruments, diagnostic equipment, and laboratory tools. The process is renowned for its ability to produce complex shapes with high precision, consistency, and relatively low cost at high volumes. It is critical for applications where reliability and biocompatibility are essential.
In radiology, OEM (Original Equipment Manufacturer) refers to companies that design and manufacture medical imaging equipment or components, which are then rebranded and sold by other medical device companies. OEMs specialize in creating cutting-edge imaging technologies such as X-ray machines, CT scanners, MRI systems, and ultrasound devices. They also produce parts like detectors, coils, and software systems tailored for diagnostic applications. These manufacturers ensure compliance with strict medical and regulatory standards, delivering equipment that meets safety, precision, and reliability criteria. OEM partnerships are crucial for healthcare providers, as they allow access to high-quality imaging solutions without requiring direct investment in research and development.
Medical injection molding is a precision manufacturing process used to produce medical-grade components and devices. It involves injecting molten materials, typically biocompatible plastics or elastomers, into custom molds. The process is essential for creating a wide range of medical products, such as surgical instruments, syringes, catheters, and implantable devices. Cleanroom environments are often used during production to maintain sterility and prevent contamination. With the ability to produce complex shapes and maintain tight tolerances, medical injection molding ensures the creation of safe, reliable, and cost-effective components that meet stringent healthcare standards.
The medical injection molding market is a rapidly expanding industry driven by the increasing demand for advanced medical devices and disposable components. Key factors contributing to its growth include the rising incidence of chronic diseases, the preference for minimally invasive surgeries, and advancements in biocompatible materials. The market is valued in billions of dollars globally, with significant demand in regions such as North America, Europe, and Asia-Pacific. Medical injection molding supports the production of essential products like surgical tools, diagnostic kits, and drug delivery devices, making it an integral part of the healthcare sector.
Thermoplastic Injection Molding: Commonly used for medical applications, this process uses thermoplastic materials that can be melted, shaped, and cooled. It is ideal for creating syringes, diagnostic components, and surgical tools.
Thermoset Injection Molding: This process involves thermosetting polymers that solidify irreversibly when cured. It is suitable for creating durable, heat-resistant medical devices, such as dental tools and electronic enclosures for imaging equipment.
Moulding in medicine refers to the shaping of materials or anatomical structures. For instance, in medical manufacturing, injection molding is used to create precise components like surgical instruments or implantable devices. These processes ensure the production of sterile, reliable, and complex parts critical for healthcare applications. In obstetrics, moulding also describes the adaptation of a baby’s skull during childbirth to fit through the birth canal.
Injection molding involves heating and injecting plastic into a mold, commonly used for creating precise medical devices like syringes and surgical components. Reaction injection molding (RIM), on the other hand, combines two liquid reactants in a mold, forming a polymer through a chemical reaction. RIM is suitable for creating lightweight, flexible medical enclosures and devices that require durability and intricate designs.
Injection molding creates standalone medical components, such as syringes or vial caps. Insert molding integrates a pre-placed insert, like a metal rod or electronic sensor, within the molded plastic. This method is frequently used in medical devices that require combined materials, such as surgical tools with embedded electronics or handles with reinforced metal cores.
No, while plastic is the most common material, medical injection molding also uses elastomers and specialized materials like silicone, which are essential for biocompatible products. For example, silicone is widely used in catheters and prosthetics. Some advanced techniques also incorporate metal and ceramic injection molding for specialized medical components.
The medical injection molding market is a multi-billion-dollar industry and is growing due to advancements in healthcare and increasing demand for cost-effective, disposable medical products. North America and Europe are leading markets, while Asia-Pacific is emerging as a key growth region. Applications range from producing diagnostic equipment to creating surgical instruments and implantable devices.
One of the hardest plastics used in medical injection molding is polycarbonate (PC). It offers exceptional impact resistance, clarity, and durability, making it ideal for medical devices like oxygen masks and surgical instrument enclosures. Another option is PEEK (polyetheretherketone), a high-performance plastic often used for implantable devices due to its strength and biocompatibility.
Medical injection molding tooling is expensive due to the precision, durability, and complexity required for producing high-quality, sterile components. Molds are typically made from hardened steel or high-grade aluminum, with intricate designs tailored to exacting specifications. The tooling process involves advanced techniques like CNC machining and rigorous validation to meet medical regulatory standards.
The hourly cost of medical injection molding varies based on machine size, material, and cleanroom requirements. For smaller machines used in sterile production, costs may range from $75 to $200 per hour. Larger machines, capable of producing high-volume parts, may cost $250 to $500 per hour. Additional cleanroom operations add to the expense.
Injection molding is highly profitable in the medical industry due to its scalability, precision, and efficiency. While initial tooling costs are high, the cost per unit decreases significantly with large production volumes. Medical applications, such as syringes, catheters, and surgical instruments, have high demand, ensuring consistent profitability.
A 1300-ton injection molding machine for medical applications typically costs between $500,000 and $1,200,000. These machines are used for large-scale production of medical devices, including diagnostic equipment housings and surgical trays. The high cost reflects the precision, size, and advanced features required for sterile medical manufacturing.
Contact our professional team now for a same-day quote and risk-free project evaluation. Benefit from ISO 8 cleanrooms, advanced machines, and 12-hour fast response in medical injection molding.