Customizable plastic electronic medical equipment molding for sale solutions. Precision, efficiency, and reliability for medical devices. Plastic electronic medical equipment molding for sale plays a crucial role in modern healthcare and electronics manufacturing. Precision and quality are essential in these industries, where safety, reliability, and durability cannot be compromised. Advanced injection molding technology ensures components meet strict standards, providing functionality and longevity for critical applications. This technology excels in producing intricate designs and complex shapes with high accuracy, which is key for advanced medical devices. The use of precision mold medical techniques ensures that every component is manufactured with the exact specifications required for seamless integration and optimal performance in medical environments.
Low-Volume to High-Volume Production Capabilities
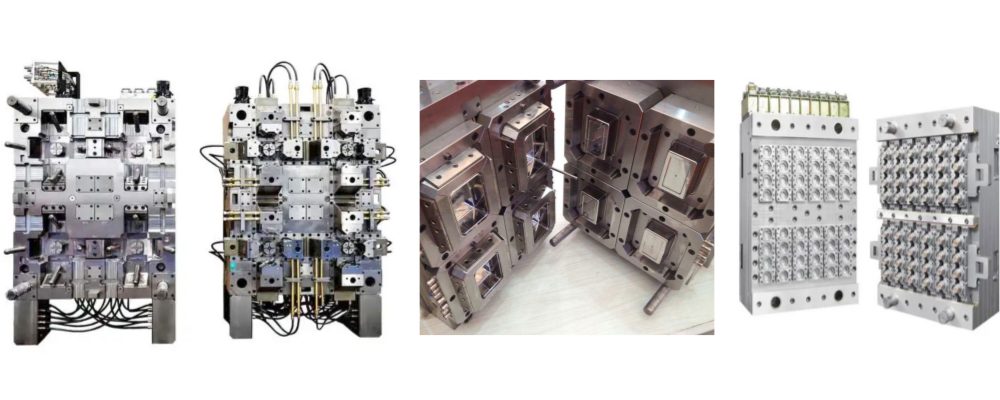
Attributes | Details |
---|---|
Place of Origin | Dongguan, Guangdong, China |
Brand Name | LY Medical Injection Mold |
Product Name | Medical Silicone Injection Molding |
Molding Mode | Plastic Injection Mold |
Product Material | Plastic; ABS/PC/PP/HDPE/POM/PA6/PA6+GF/PVC/NYLON/PMMA/PET, etc. |
Surface Treatment | Customized Surface Texture |
Tolerance | 0.01-----0.05mm |
Features | High Precision, Environmentally Friendly, Durable |
Color | Customized |
Size | Customized |
Length | Customized |
Style | Customized |
Service | OEM ODM |
Processing Service | Molding, Cutting |
Logo | Customized Logo Acceptable |
Quality Control | 100% Inspection |
Mould Life | 250000-500000shots |
Minimum Order Quantity | Accept Small Orders |
Packing Details | Outer Packaging Carton Inner Packaging According to Customer Requirement |
Port | According to Your Requirement |
Types of Plastic Electronic Medical Equipment Molding for Sale
Plastic electronic medical equipment molding involves various techniques to create precise, durable, and biocompatible components for medical devices. Below is a detailed description of the types of molding processes used in this field:
Injection Molding
- Description: Injection molding is the most common method for producing plastic components. It involves injecting molten plastic into a mold cavity under high pressure. Once the material cools and solidifies, the mold opens, and the part is ejected.
- Applications: Used for manufacturing housings, connectors, syringe components, and other intricate parts.
- Advantages: High precision, repeatability, and scalability. Suitable for high-volume production.
- Materials: Thermoplastics like polycarbonate (PC), polypropylene (PP), and acrylonitrile butadiene styrene (ABS).
Insert Molding
- Description: Insert molding involves placing a pre-formed component (e.g., metal or electronic parts) into a mold, followed by injecting plastic around it to create a single integrated part.
- Applications: Commonly used for embedding sensors, connectors, or circuitry into medical devices.
- Advantages: Enhances device functionality, reduces assembly steps, and improves durability.
- Materials: Thermoplastics combined with metal or electronic inserts.
Overmolding
- Description: Overmolding is a two-step process where a substrate part is first created, and then a second layer of material is molded over it. This can involve different materials or colors.
- Applications: Used for creating ergonomic grips, seals, or multi-material components in medical devices.
- Advantages: Improves comfort, aesthetics, and functionality. Provides better sealing and insulation.
- Materials: Thermoplastic elastomers (TPE) or silicone over rigid plastics.
Blow Molding
- Description: Blow molding uses air pressure to inflate molten plastic into a mold cavity, creating hollow parts.
- Applications: Ideal for producing bottles, containers, and fluid reservoirs used in medical devices.
- Advantages: Cost-effective for hollow parts and lightweight designs.
- Materials: Polyethylene (PE) and polypropylene (PP).
Rotational Molding
- Description: Rotational molding involves rotating a mold while heating it to evenly distribute plastic material along the mold walls.
- Applications: Used for large, hollow components like medical equipment housings or storage tanks.
- Advantages: Low tooling costs and uniform wall thickness.
- Materials: Polyethylene (PE) and polyvinyl chloride (PVC).
Thermoforming
- Description: Thermoforming involves heating a plastic sheet until pliable, then forming it over a mold using vacuum or pressure.
- Applications: Used for producing trays, covers, and disposable medical device components.
- Advantages: Cost-effective for low to medium-volume production.
- Materials: Polystyrene (PS), polyethylene terephthalate (PET), and polyvinyl chloride (PVC).
Compression Molding
- Description: Compression molding involves placing a pre-measured amount of plastic material into a heated mold cavity, then applying pressure to shape the material.
- Applications: Suitable for producing large, flat, or moderately complex parts like medical device housings.
- Advantages: Low waste and suitable for thermosetting plastics.
- Materials: Thermosetting plastics like epoxy and phenolic resins.
Micro Molding
- Description: Micro molding is a specialized form of injection molding used to produce extremely small and precise components.
- Applications: Used for microfluidic devices, tiny connectors, and components for minimally invasive surgical tools.
- Advantages: High precision and ability to produce parts with intricate geometries.
- Materials: Engineering thermoplastics like PEEK and liquid crystal polymers (LCP).
Gas-Assisted Injection Molding
- Description: This process involves injecting nitrogen gas into the molten plastic to create hollow sections or reduce material usage.
- Applications: Used for producing lightweight, rigid components with complex geometries.
- Advantages: Reduces material costs and cycle times while maintaining structural integrity.
- Materials: Polycarbonate (PC) and ABS.
Two-Shot Molding
- Description: Two-shot molding uses two different materials or colors in a single molding cycle to create a multi-material or multi-colored part.
- Applications: Used for creating soft-touch grips, seals, or multi-functional components in medical devices.
- Advantages: Eliminates secondary assembly steps and enhances design flexibility.
- Materials: Combinations of rigid and soft thermoplastics.
Reaction Injection Molding (RIM)
- Description: RIM involves mixing two reactive liquid components (e.g., polyurethane) and injecting them into a mold, where they chemically react and solidify.
- Applications: Used for producing large, lightweight, and durable components like medical device enclosures.
- Advantages: Low pressure requirements and design flexibility.
- Materials: Polyurethane and other reactive polymers.
3D Printing (Additive Manufacturing)
- Description: While not a traditional molding process, 3D printing is increasingly used for prototyping and low-volume production of medical device components.
- Applications: Custom prosthetics, surgical guides, and patient-specific implants.
- Advantages: High design flexibility and rapid prototyping capabilities.
- Materials: PLA, ABS, PEEK, and biocompatible resins.
Key Considerations for Plastic Electronic Medical Equipment Molding
- Biocompatibility: Materials must meet regulatory standards (e.g., ISO 10993) for contact with the human body.
- Precision: Medical devices often require tight tolerances and high-quality finishes.
- Sterilization Compatibility: Components must withstand sterilization methods like autoclaving, gamma radiation, or ethylene oxide.
- Regulatory Compliance: Manufacturing processes must adhere to standards like ISO 13485 and FDA regulations.
By selecting the appropriate molding technique and material, manufacturers can produce high-quality plastic components that meet the stringent requirements of the medical industry.
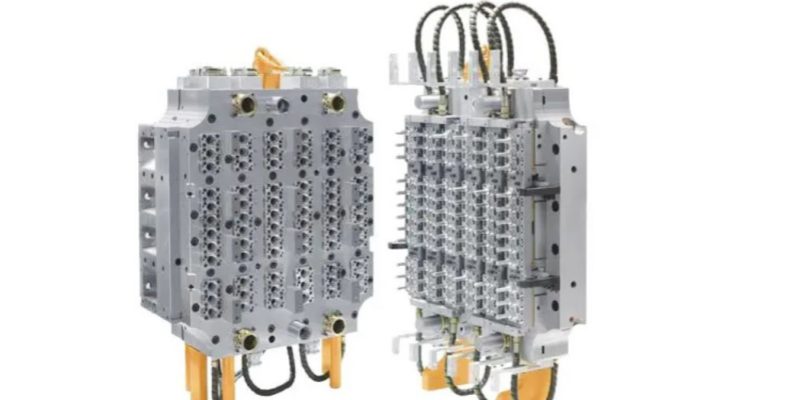
Different Materials for Plastic Electronic Medical Equipment Molding for Sale
Plastic electronic medical equipment molding requires materials that are not only durable and lightweight but also meet stringent safety, performance, and regulatory requirements. The choice of material depends on the specific application and the desired characteristics of the molded parts. Below are various materials commonly used for molding plastic electronic medical equipment:
Polycarbonate (PC)
Polycarbonate is a transparent and strong thermoplastic material with high impact resistance, making it ideal for medical electronic devices that need both durability and clarity. It is commonly used in equipment such as housings for medical monitors, diagnostic devices, and protective covers for electronic components.
Advantages:
- Excellent impact resistance
- High dimensional stability
- Can be easily molded into complex shapes
- High transparency (important for visual monitoring)
Disadvantages:
- Sensitive to scratching, though coatings can be applied to reduce this
- Prone to yellowing when exposed to UV light over time
Acrylonitrile Butadiene Styrene (ABS)
ABS is a versatile and commonly used thermoplastic that offers good mechanical properties, including strength, toughness, and impact resistance. It is often used in the production of external parts of medical electronic devices, such as battery covers, control panels, and enclosures.
Advantages:
- Good impact strength and resistance to physical stress
- Relatively low cost
- Easy to mold into intricate shapes
- Good electrical insulating properties
Disadvantages:
- Sensitive to UV degradation
- Not as heat-resistant as some other plastics
Polypropylene (PP)
Polypropylene is another widely used plastic material in medical electronics molding due to its excellent chemical resistance, electrical insulation properties, and high-temperature stability. It is ideal for components like connectors, casings, and housings that require chemical resistance and sterilization capabilities.
Advantages:
- High chemical resistance
- Excellent electrical insulation
- Resistant to fatigue and stress
- Can withstand high temperatures
Disadvantages:
- Lower impact resistance compared to polycarbonate
- Less suitable for clear or transparent parts
Polyethylene (PE)
Polyethylene, particularly high-density polyethylene (HDPE), is often used in medical applications requiring durable and chemically resistant materials. It is commonly used for molded parts that need to be sterilized or exposed to various environmental factors.
Advantages:
- Excellent chemical and corrosion resistance
- Lightweight and cost-effective
- Good resistance to impact
Disadvantages:
- Poor dimensional stability
- Lower tensile strength than other plastics
Thermoplastic Elastomers (TPE)
Thermoplastic elastomers (TPE) are materials that combine the characteristics of rubber with the processability of thermoplastics. TPE is frequently used in electronic medical devices that require flexibility, such as handles, seals, and gaskets for medical equipment like diagnostic instruments and wearable devices.
Advantages:
- Soft, flexible, and rubber-like properties
- Excellent resistance to wear and tear
- Good chemical and UV resistance
- Can be easily molded and processed
Disadvantages:
- May have lower temperature resistance compared to other materials
Polyphenylene Oxide (PPO)
PPO is a high-performance thermoplastic often used in medical devices that require low moisture absorption, high strength, and good dimensional stability. It is frequently utilized in complex and precision medical electronic components.
Advantages:
- Excellent dimensional stability and mechanical properties
- Low moisture absorption
- High electrical insulation properties
Disadvantages:
- Poor UV resistance
- Can be more expensive than other materials
The material selection for plastic molding in electronic medical equipment is crucial for ensuring that the device performs safely and effectively. Factors such as chemical resistance, electrical insulation, transparency, durability, and biocompatibility must all be considered when choosing the best plastic material for a given medical device. For high-performance applications, materials like PEEK and polycarbonate are ideal, while materials like ABS, polypropylene, and TPE are often suitable for general use. Each material has specific advantages and limitations, so choosing the right one depends on the device’s function and the environmental conditions it will face.
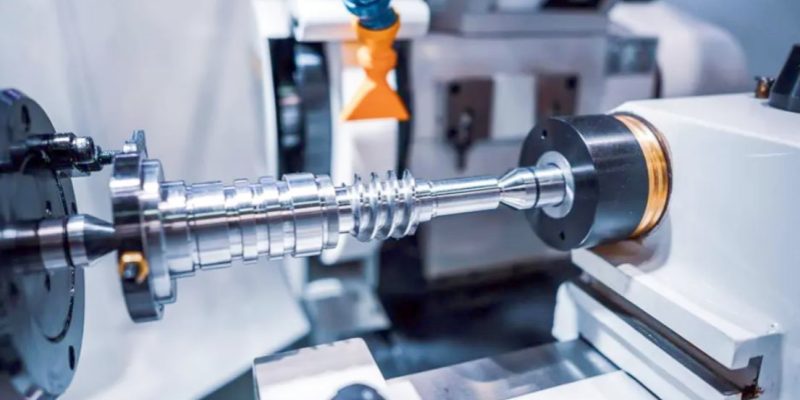
Applications of Plastic Electronic Medical Equipment Molding for Sale
Plastic electronic medical equipment molding for sale offers diverse applications across healthcare sectors, ensuring precision, reliability, and efficiency. This advanced manufacturing process meets the critical demands of medical facilities by delivering high-quality components essential for various medical and electronic uses. In particular, medical device automation is increasingly integrated into the molding process, enhancing production efficiency and ensuring that components are manufactured with consistent quality and precision. This automation not only streamlines the manufacturing workflow but also supports the high standards required in the medical industry.
Surgical Disposable Items
Surgical disposable items such as syringes, IV sets, and pipette tips are vital for safe and effective medical procedures. Plastic electronic medical equipment molding for sale ensures these items are produced with exceptional precision and sterility, which are crucial for preventing contamination and ensuring patient safety. The ability to create intricate designs with smooth surfaces supports functionality and comfort during medical procedures. Additionally, the scalable production capabilities make it possible to meet high demand while maintaining quality.
Medical Consumables
Examples of medical consumables created using plastic electronic medical equipment molding for sale include petri dishes, centrifuge bottles, and sampling tubes. These products benefit from the durability and consistency achieved through plastic molding techniques. For laboratory and diagnostic environments, these items must withstand rigorous usage without compromising performance. Injection molding allows for mass production, making these consumables readily available for critical applications while keeping costs manageable.
Custom Medical Equipment
Custom solutions are increasingly important in today’s medical landscape, addressing the specific needs of hospitals, laboratories, and diagnostic centers. Plastic electronic medical equipment molding for sale enables the production of tailored components, with custom medical molding components playing a key role in creating specialized housings for electronic medical devices and diagnostic tools. By integrating electronic components within molded plastic enclosures, manufacturers can enhance functionality while ensuring robust and lightweight designs. These custom applications demonstrate the versatility of injection molding in delivering innovative solutions for healthcare.
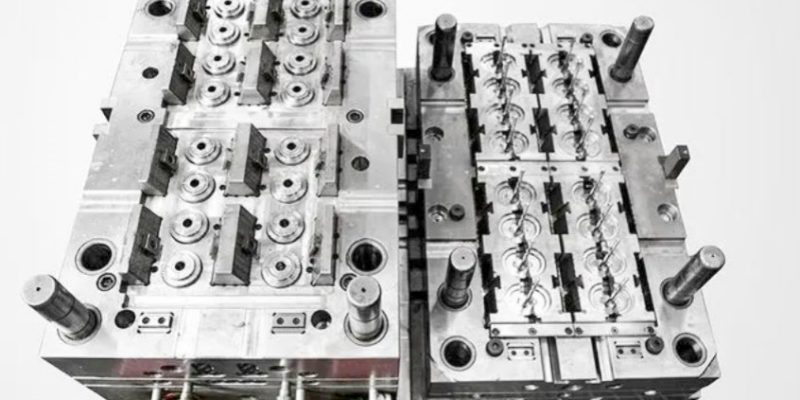
Capabilities of Modern Plastic Injection Molding for Plastic Electronic Medical Equipment Molding for Sale
Modern injection molding technology provides unparalleled capabilities for creating high-quality medical and electronic components. Plastic electronic medical equipment molding for sale benefits from advanced techniques and tools that ensure precision, scalability, and adherence to stringent medical standards. Below are key aspects of its capabilities:
Design and Prototyping
The design phase is critical to the success of plastic electronic medical equipment molding for sale. Free mold design services and 3D prototyping enable manufacturers to tailor solutions to specific needs, whether for medical devices or electronic enclosures. Using state-of-the-art software and simulation tools, engineers create prototypes that mimic the final product with high accuracy.
Advanced CNC machining ensures precision in both small and large parts, delivering components that meet exact specifications. This capability is especially important for intricate medical equipment, where small deviations can affect functionality. For applications like medical enclosure molding, precision is crucial to ensure proper fit and performance. The iterative prototyping process also reduces risks by allowing for adjustments before full-scale production.
Materials for Medical Molding
One of the strengths of plastic electronic medical equipment molding for sale lies in the diverse range of medical-grade materials available. Commonly used plastics include ABS, TPE, TPU, and polycarbonate, among others. These materials are chosen for their unique properties, such as durability, flexibility, and resistance to chemicals. For medical applications, selecting the right material ensures compatibility with the intended use, such as sterilization methods and exposure to bodily fluids.
For instance, TPE and TPU offer excellent elasticity and are often used in devices requiring flexible components, while ABS provides rigidity for robust enclosures. The versatility of medical molding allows manufacturers to select and process the ideal materials for each specific application, ensuring reliability and performance.
Cleanroom Manufacturing
Sterile production environments are essential for plastic electronic medical equipment molding for sale, especially for products used in critical medical applications. Cleanroom manufacturing facilities provide Class 7 and Class 8 environments to maintain hygiene and prevent contamination during production.
This capability is vital for items like surgical disposables and laboratory consumables, where sterility is non-negotiable. Cleanrooms adhere to strict international medical standards, ensuring that products meet regulatory requirements and are safe for use in healthcare settings. This controlled environment also supports the production of high-precision components, further enhancing the quality of the final product.
By combining advanced design, diverse material options, and cleanroom manufacturing, plastic electronic medical equipment molding for sale delivers reliable solutions for the healthcare and electronics industries.
Key Benefits of Plastic Medical Equipment Molding for Plastic Electronic Medical Equipment Molding for Sale
Plastic electronic medical equipment molding for sale provides a host of benefits, making it a preferred choice for manufacturing medical and electronic components. From efficiency and cost-effectiveness to the use of advanced techniques, this manufacturing process ensures high-quality results that meet industry standards. Below are the detailed advantages:
Efficiency and Scalability
One of the most significant advantages of plastic electronic medical equipment molding for sale is its efficiency and scalability. Injection molding allows for high-volume repeatability, meaning manufacturers can produce thousands or even millions of identical components with consistent quality. This is critical in the medical industry, where uniformity can directly impact performance and safety.
The process also offers short lead times, making it ideal for urgent production needs. Whether producing surgical disposables or complex electronic device enclosures, injection molding ensures timely delivery without compromising quality. This level of efficiency helps manufacturers meet tight deadlines, especially during periods of high demand, such as public health emergencies.
Cost-Effectiveness
Plastic electronic medical equipment molding for sale is renowned for its cost-effectiveness. It provides economical solutions for both large and small production runs, making it suitable for a wide range of applications. For high-volume orders, the cost per unit decreases significantly due to the reusability of molds and the automation of the medical injection molding process.
Additionally, reduced material wastage is another cost-saving advantage. Injection molding uses precise amounts of raw material, minimizing scrap and lowering production costs. This feature also contributes to environmental sustainability, aligning with modern manufacturing goals.
Advanced Techniques
Advanced techniques employed in plastic electronic medical equipment molding for sale further enhance its capabilities. Overmolding and micro-injection molding are two standout methods used to create complex, multi-layer designs. Overmolding involves combining multiple materials into a single component, which is ideal for products requiring ergonomic grips or integrated sealing features.
Micro-injection molding, on the other hand, specializes in the production of miniature components with extreme precision. This technique is particularly valuable for intricate medical and electronic devices, such as diagnostic tools and sensors. Furthermore, the ability to integrate various functionalities into a single component simplifies assembly and improves the overall performance of the final product.
By leveraging these key benefits, plastic electronic medical equipment molding for sale stands out as a versatile and reliable solution for manufacturers in the healthcare and electronics industries. It not only meets the high demands of these sectors but also ensures cost savings and technological innovation.
Custom Solutions for Medical Equipment Production Using Plastic Electronic Medical Equipment Molding for Sale
The versatility of plastic electronic medical equipment molding for sale extends to offering custom solutions tailored to the unique needs of the medical and healthcare industries. By incorporating secondary operations, rigorous product validation, and sustainable manufacturing practices, this process delivers end-to-end solutions for a wide range of medical applications.
Secondary Operations for Comprehensive Solutions
Plastic electronic medical equipment molding for sale goes beyond molding to include a variety of secondary operations that ensure the components are ready for immediate use. Services like assembly, labeling, packaging, and welding provide a complete solution to manufacturers, eliminating the need for additional steps in the production chain.
For instance, intricate assemblies such as multi-part surgical devices or electronic medical tools are seamlessly integrated during the post-molding phase. Custom labeling and packaging ensure that products meet regulatory requirements and are market-ready upon delivery. Welding techniques, such as ultrasonic welding, create robust and sterile seals essential for medical-grade equipment.
Product Validation for Quality Assurance
A critical component of plastic electronic medical equipment molding for sale is product validation. Rigorous testing and verification ensure compliance with stringent safety and performance standards, which are crucial in the healthcare industry. Components undergo mechanical, thermal, and chemical testing to verify their durability and functionality under real-world conditions.
Validation processes also include inspection for dimensional accuracy and sterilization compatibility, guaranteeing that every piece meets medical-grade specifications. This attention to detail provides healthcare professionals with reliable tools, fostering trust in critical environments where precision and safety are paramount.
Sustainability in Production
Sustainability is a growing priority in modern manufacturing, and plastic electronic medical equipment molding for sale embraces environmentally responsible practices. Material selection focuses on biodegradable or recyclable medical-grade plastics that reduce environmental impact without compromising quality or performance. Additionally, the use of multi component injection molding medical allows for the efficient integration of multiple materials, reducing the need for additional manufacturing steps and minimizing waste.
Efficient production processes further enhance sustainability by minimizing material waste and energy consumption. Advanced injection molding techniques, such as optimized cycle times and energy-efficient machinery, contribute to eco-friendly operations. This approach not only supports global sustainability goals but also aligns with the values of healthcare institutions prioritizing green initiatives.
By integrating secondary operations, robust product validation, and sustainable practices, medical equipment parts plastic mould for sale provides comprehensive solutions that meet the high standards of the medical industry. These features ensure that every product delivered is ready for use, reliable, and environmentally conscious.
Custom Plastic Electronic Medical Equipment Molding Solution
As a leading provider of OEM services specializing in medical device injection molding, FUJIU is committed to delivering tailored solutions that meet the unique requirements of our clients. Our extensive experience and expertise in the field enable us to provide unmatched precision and quality in every molded component we produce. We are dedicated to exceeding your expectations by offering highly customizable solutions designed to meet the specific demands of your medical electronic equipment.
Precision and Quality Assurance
At FUJIU, we understand the critical role that precision and quality play in the production of medical device components. Our team is deeply involved in every project, ensuring that every molded part is crafted with unparalleled accuracy. Whether it’s for diagnostic equipment, surgical instruments, or patient monitoring devices, we ensure that each part meets stringent industry standards for safety and reliability.
Customization to Meet Unique Needs
We know that each medical facility, hospital, and diagnostic center has its own set of specific needs. Our expertise in custom molding enables us to offer solutions that are not only accurate but also perfectly aligned with your requirements. We collaborate closely with our clients throughout the design and manufacturing process, ensuring that each product meets both functional and regulatory standards.
Material Expertise
As a leading manufacturer of customized medical device parts, we understand the importance of selecting the right materials for each application. We are well-versed in the properties of various plastics and polymers, including their flexibility, durability, and resistance to medical-grade standards. Whether it’s for sensitive electronic components or rugged external casings, we ensure that every material we use is the most suitable for the intended use. Our team’s material expertise guarantees that we deliver products that are safe, durable, and meet the highest standards of performance.
Cleanroom
For sensitive electronic applications, traditional molding solutions may not always suffice. That’s why FUJIU has dedicated years to establishing ourselves as a preferred provider of cleanroom injection molding solutions. We operate state-of-the-art facilities that have achieved ISO 6 and ISO 7 certification for secondary processing, as well as ISO 8 certification for full-size injection molding. This ensures that all molded components are manufactured in a controlled, contaminant-free environment, preserving the integrity of sensitive electronics and medical components.
Our cleanroom facilities are equipped with both hard-wall and soft-wall cleanrooms, providing the flexibility and scalability necessary to accommodate your specific production needs. We offer cleanroom molding solutions that are adaptable to your project size, whether you require high-volume production or smaller, more specialized runs.
Flexible and Scalable Manufacturing
FUJIU’s cleanroom molding solutions are designed to be flexible and scalable, catering to the diverse needs of our clients in the medical device industry. From small-scale prototypes to large-scale production runs, our team ensures that your project is handled with the utmost care and precision. We prioritize delivering solutions that are tailored to your exact requirements, whether it’s optimizing part designs, ensuring material compatibility, or adhering to strict regulatory standards.
Your Trusted Partner for Custom Medical Injection Molding
As one of the top manufacturers of custom medical device components, FUJIU is committed to providing you with the most advanced and reliable molding solutions. We understand that in the medical field, precision, safety, and compliance are of utmost importance. Our dedication to quality and innovation ensures that we remain a trusted partner in the development and production of plastic electronic medical equipment.
At FUJIU, we don’t just manufacture parts; we create solutions that meet your needs and exceed your expectations. Whether you require cleanroom molding, material expertise, or high-precision manufacturing, we are here to provide you with the best-in-class service and support.
FAQs about Plastic Electronic Medical Equipment Molding for Sale
What is cheaper than injection molding?
In the medical device manufacturing industry, some alternatives to injection molding are generally cheaper in terms of setup costs, especially for low-volume production. These alternatives include processes like thermoforming, 3D printing, and casting. Thermoforming, for example, is often cheaper than injection molding when dealing with simple medical device parts. The process involves heating a sheet of plastic until it’s soft, then forming it into a mold. It’s suitable for low-volume production runs, and the tooling costs are considerably lower than injection molding, which requires expensive molds and precise machinery.
Additionally, 3D printing is becoming an increasingly popular alternative to injection molding for medical device prototyping and low-volume production. While 3D printing does not yet have the capacity for high-volume manufacturing like injection molding, it can be much cheaper in the early stages of development, particularly when a design is being iterated upon quickly. The main advantage here is the lack of a mold, which can be costly and time-consuming to create in injection molding. Similarly, casting may be cheaper for smaller production runs in the medical field, where materials like silicone are used to create molds and parts for medical devices. However, it’s important to note that casting usually lacks the precision and consistency required in the production of complex, high-volume medical devices.
While these alternatives may be cheaper in certain contexts, injection molding remains the go-to choice for high-volume, high-precision medical device manufacturing due to its ability to produce large quantities of parts at a relatively low cost per unit.
How long does it take to make a plastic injection mold?
Creating a plastic injection mold for medical device manufacturing can take anywhere from a few weeks to several months, depending on the complexity of the part, the type of plastic used, and the manufacturer’s capabilities. The mold-making process involves several stages, including design, prototyping, material selection, and final adjustments. Typically, a simple mold might take around 4 to 6 weeks, while more intricate designs with complex geometries can take up to 8-12 weeks or longer.
The first step is designing the mold, which often involves 3D CAD software to create detailed specifications. Once the design is approved, the mold is manufactured using precise machining equipment, typically involving the use of CNC machines. The materials used for the mold are often high-grade steels or other durable alloys to ensure the mold can withstand the high pressure of the injection molding process.
In medical device manufacturing, where precision is critical for regulatory compliance and functionality, the process may take longer due to the need for detailed testing and validation. Some molds also need to undergo additional steps like polishing, surface treatment, or coating, which can add to the overall time frame.
Though the upfront mold creation time is substantial, injection molding remains the most efficient method for large production runs once the mold is ready, as the cost per unit decreases significantly with increased production.
Is injection molding cheaper than machining?
Injection molding is generally cheaper than machining for high-volume production of medical device components, especially when considering per-unit costs. Machining, which involves removing material from a block using tools like mills or lathes, is well-suited for creating prototypes or low-volume runs of complex medical parts, but it becomes more expensive as the production scale increases. This is because machining typically requires more time and labor, and the process is more material-intensive.
On the other hand, injection molding has high initial setup costs due to the need for mold creation, but the cost per part decreases significantly as the volume of production increases. For large runs of identical parts, injection molding becomes much more cost-effective. Once the mold is created, each part can be produced quickly and with high precision, which lowers labor costs and reduces material waste, making it the preferred method for large-scale production of medical devices.
Machining is still useful for low-volume runs or when producing parts with intricate features that injection molding cannot replicate. However, when medical manufacturers need to produce large quantities of parts that require consistency and precision, injection molding is typically more cost-effective. Additionally, for medical components that require specific certifications, such as biocompatibility and regulatory compliance, the predictability and control over part quality in injection molding make it the more viable long-term choice.
What is the best plastic for injection molding?
The best plastic for injection molding in medical device manufacturing depends on the specific requirements of the device, such as biocompatibility, strength, flexibility, and sterilization ability. Some of the most commonly used plastics for medical injection molding include:
Polycarbonate (PC): This is a highly versatile plastic with excellent impact resistance and clarity. It is often used for medical devices like IV connectors, surgical instruments, and diagnostic equipment. Polycarbonate can withstand sterilization processes like autoclaving and is known for its ability to be molded into precise, complex shapes.
Polypropylene (PP): Polypropylene is a cost-effective and lightweight plastic commonly used in medical device applications. It is particularly known for its chemical resistance and high resistance to fatigue, making it ideal for items like syringes, medical bottles, and sterile packaging. It’s also easy to sterilize, which is critical for medical applications.
Polyethylene (PE): High-density polyethylene (HDPE) is often used for medical containers and equipment that require strength and resistance to chemicals and moisture. It’s also used in drug delivery devices. Low-density polyethylene (LDPE) is more flexible and is used in packaging and some disposable medical devices.
ABS (Acrylonitrile Butadiene Styrene): ABS is another widely used plastic in the medical industry due to its strength, impact resistance, and ease of processing. It’s typically used for devices that require high precision and robustness, such as dental instruments, surgical tools, and medical trays.
POM (Acetal or Delrin): POM is known for its excellent mechanical properties, such as strength, stiffness, and low friction, which make it ideal for medical devices that involve moving parts, such as pumps or valves.
Each of these materials has its own set of advantages, so manufacturers must consider factors like material strength, chemical compatibility, and biocompatibility before choosing the right plastic for the injection molding process.
Is plastic injection molding difficult?
Plastic injection molding, particularly in the medical device sector, can be quite complex, but it is not necessarily difficult once the correct tools, molds, and expertise are in place. The process involves injecting molten plastic into a precisely engineered mold to form the desired shape. While the basic concept of injection molding is straightforward, the difficulty often arises in the high level of precision required, particularly for medical devices, where tolerances must be tight and specifications strict.
One of the challenges is designing the mold, which must be tailored to the specific geometry of the medical part being produced. Molds need to be extremely durable and able to withstand hundreds of thousands of cycles without wear. Precision is crucial, especially when dealing with parts that need to meet FDA and ISO regulatory standards. Ensuring the finished product meets the required biocompatibility, functionality, and performance standards adds another layer of complexity.
Additionally, selecting the appropriate material and adjusting the molding process to ensure proper flow, cooling, and solidification of the plastic is vital for producing high-quality parts. The cycle time, injection speed, pressure, and temperature all need to be monitored and adjusted to achieve optimal results.
In summary, while plastic injection molding is a highly automated and efficient process, it does require a combination of specialized knowledge, precise engineering, and strict quality control, particularly in the medical device industry. Therefore, it can be challenging for those who are unfamiliar with the complexities of medical manufacturing.
What is the cost per hour for an injection molding machine?
The cost per hour for an injection molding machine in the medical industry varies widely depending on the size and complexity of the machine, as well as the type of plastic being molded. Generally, the hourly rate for running an injection molding machine ranges from $20 to $150 or more. The cost is influenced by factors such as energy consumption, machine maintenance, operator wages, and the intricacies of the mold design.
For high-precision medical components that require stringent quality control and high-volume production, the cost per hour can be on the higher end of the spectrum. High-tonnage machines that produce larger parts or have more advanced capabilities can increase the hourly cost due to more intensive operational requirements. Additionally, if the medical devices require expensive or high-performance materials (such as biocompatible plastics), the material cost can add to the overall expense.
Another factor that influences cost is the machine’s automation level. Fully automated machines typically reduce the need for manual labor, which lowers the overall cost per part in the long run. However, for specialized medical device manufacturing, machine operators may still need to perform inspections or adjustments, which adds to the labor cost.
In the context of medical device production, manufacturers often look to balance the cost of running the machine with the efficiency of the injection molding process, since the overall cost can be offset by producing high-quality, high-volume parts at lower per-unit costs.
What is the most damaging plastic?
The most damaging plastic from an environmental perspective is polyvinyl chloride (PVC), particularly due to the harmful additives and its difficulty to recycle. PVC is widely used in medical applications such as medical tubing and blood bags. However, its production and disposal can release harmful chemicals, including dioxins, which are toxic and pose serious environmental and health risks. In addition, PVC is not easily recyclable compared to other plastics like polypropylene and polyethylene, contributing to its negative environmental impact.
In terms of biodegradability, PVC is also a problem since it takes hundreds of years to break down in landfills, contributing to long-term environmental pollution. Furthermore, the burning of PVC releases chlorine gas, which can be harmful to human health and the environment.
For medical device manufacturers, however, there are increasing efforts to use more sustainable alternatives to PVC. Medical-grade plastics like polypropylene (PP) and polyethylene (PE) are often favored as they are more environmentally friendly and less harmful to human health, especially when used in disposable medical devices. The medical industry is gradually moving toward these plastics to reduce their environmental footprint.
What is the most resilient plastic?
In the medical industry, polycarbonate (PC) is widely regarded as one of the most resilient plastics due to its exceptional toughness, impact resistance, and ability to withstand high temperatures. Polycarbonate is used for medical devices that require high durability and strength, such as surgical instruments, diagnostic equipment, and medical housings. It can endure repeated sterilization cycles, such as autoclaving, without significant degradation in properties.
Another highly resilient plastic is polyamide (PA), commonly known as nylon, which is often used in medical applications like medical tubing and surgical instruments. Nylon has high resistance to wear, chemicals, and moisture, making it suitable for parts that experience mechanical stress or need to function in challenging environments.
Polyethylene (HDPE) is also known for its resilience, particularly in high-stress applications where resistance to fatigue, wear, and chemicals is essential. It is commonly used for medical containers, drug delivery devices, and prosthetics.
Overall, when selecting the best resilient plastic for a medical device, factors such as mechanical stress, sterilization compatibility, and the environment in which the device will be used must be considered.
What is the most conductive plastic?
The most conductive plastic is polyetheretherketone (PEEK), a high-performance engineering plastic that can be compounded with conductive fillers to enhance its electrical conductivity. While PEEK itself is not naturally conductive, it can be modified to meet specific requirements in medical devices that need controlled conductivity, such as sensors or medical electronics. PEEK is also highly resistant to heat and chemicals, making it a durable choice for medical implants or diagnostic devices.
Another conductive plastic is polyaniline (PANI), which is inherently conductive. Polyaniline is used in medical devices that require specific electrical properties, such as biosensors, electrostatic shielding, or in components that need to interface with electrical signals in medical diagnostics.
For medical devices that require both electrical conductivity and biocompatibility, specialized materials like carbon-loaded polycarbonate or conductive polypropylene can be used. These materials are often incorporated in wearable devices, diagnostic sensors, or components that interact with the human body and must adhere to strict health and safety standards.
What is the most wear-resistant plastic?
The most wear-resistant plastic is polyoxymethylene (POM), also known as acetal or Delrin. POM is highly resistant to friction and wear, making it an ideal choice for medical devices with moving parts, such as pumps, gears, or valves. It has excellent dimensional stability and resistance to abrasion, ensuring long-term durability under heavy use. Additionally, POM performs well in high-temperature environments and is chemically resistant, which is essential for medical applications involving liquids or bodily fluids.
Another wear-resistant plastic is polyamide (nylon), especially when used in medical devices like surgical tools, prosthetics, and tubing. Nylon is known for its resistance to wear and fatigue, as well as its high tensile strength and durability under mechanical stress.
For extreme wear resistance, plastics can also be blended with fillers such as glass fibers or carbon black to further enhance their resistance to wear and abrasion.
What is HDPE for medical devices?
High-density polyethylene (HDPE) is a durable, chemical-resistant plastic commonly used in medical devices. It is especially well-suited for applications that require robustness, strength, and resistance to environmental stress, such as medical containers, drug delivery systems, and surgical instruments. HDPE is also widely used in the production of medical packaging, such as bottles, tubes, and vials, due to its excellent resistance to chemicals and moisture.
In addition to its durability, HDPE is highly biocompatible, which makes it suitable for use in devices that come into contact with the human body. It is easy to sterilize, a critical factor for medical devices that need to meet rigorous hygiene standards.
Because of its cost-effectiveness, biocompatibility, and favorable material properties, HDPE continues to be a popular choice in the medical industry for both disposable and reusable devices.
What is the most protective plastic?
For applications where protection from external factors is a priority, polycarbonate (PC) is considered one of the most protective plastics. Its exceptional impact resistance, optical clarity, and ability to withstand high levels of stress make it ideal for protective medical components such as face shields, helmets, and enclosures for medical equipment. Polycarbonate is also highly resistant to breaking or shattering, which is critical in medical environments where the protection of both the device and the patient is paramount.
Another protective plastic is ABS (Acrylonitrile Butadiene Styrene), which is known for its toughness and resistance to physical damage. ABS is commonly used for medical device housings and components that require impact resistance.
What are the two most commonly used types of plastic?
The two most commonly used types of plastic in medical device manufacturing are polypropylene (PP) and polyethylene (PE). Both are versatile, cost-effective, and offer a range of properties suitable for various medical applications.
Polypropylene (PP) is widely used for medical packaging, syringes, medical trays, and IV containers. It is known for its chemical resistance, mechanical strength, and excellent ability to withstand sterilization methods like autoclaving. Its cost-effectiveness and ability to meet biocompatibility standards make it a popular choice for disposable medical devices.
Polyethylene (PE), particularly high-density polyethylene (HDPE), is also widely used in medical device applications. HDPE is known for its strength, durability, and resistance to chemicals and moisture, which is why it is used for medical containers, drug delivery devices, and prosthetics. Its easy sterilization process and good biocompatibility make it an excellent choice for devices that need to meet strict hygiene standards.
Both of these materials are ideal for applications that require high-performance characteristics, such as chemical resistance, biocompatibility, and durability, which are essential in the medical field.
What size injection molding machine do I need?
The size of the injection molding machine you need depends on the size and complexity of the medical components you plan to produce. Generally, the size of the machine is determined by the clamp force (measured in tons) required to properly hold the mold together during injection.
For small, simple medical parts, such as disposable syringes or medical packaging, a machine with a lower clamp force, typically in the range of 50-200 tons, might be sufficient.
For larger, more complex components like medical housings, diagnostic equipment, or implants, you’ll likely need a larger machine, typically in the range of 300-500 tons or more.
The machine size also depends on the volume of production. If you’re running large production batches, you’ll need a larger machine to accommodate the mold and ensure efficient production rates. Conversely, for low-volume or prototyping, smaller machines can suffice.
Additionally, the choice of machine size also depends on the material used, the design of the mold, and the precision required. Larger molds for intricate medical components may require more tonnage to ensure uniform part quality and dimensional accuracy.
Is injection molding a cheap process?
Injection molding is not typically considered a cheap process in terms of initial setup, particularly for small production runs. The primary cost drivers are the creation of the mold and the setup of the injection molding machine. Mold creation is expensive because it involves designing and manufacturing a mold, which can cost thousands to tens of thousands of dollars depending on the complexity of the part.
However, once the mold is created, injection molding becomes cost-effective for high-volume production. The cost per unit drops significantly with higher quantities because the mold can produce thousands, or even millions, of parts without requiring much additional labor. This makes injection molding a very cost-efficient process for large-scale production of medical devices or parts that need to be manufactured in bulk.
Overall, injection molding is a cost-effective solution for mass production of medical devices, especially when the production volume is high enough to offset the initial mold creation cost. For low-volume production, other methods like 3D printing or thermoforming may be more affordable, as they do not require the high upfront investment of creating molds.
Is casting cheaper than injection molding?
Casting can be cheaper than injection molding in some situations, especially for low-volume production or when manufacturing parts with simple geometries. Casting involves pouring a liquid material (often metal, silicone, or resin) into a mold and allowing it to set. The initial tooling costs for casting are often lower than those for injection molding, particularly when you’re working with soft metals, elastomers, or materials that don’t require precision molds.
For medical device prototypes or smaller production runs, casting may be a more cost-effective option. It’s also often used for parts that are too complex or expensive to produce through injection molding. For example, silicone molding is frequently used in medical devices like seals, gaskets, or parts that require a flexible material.
However, for high-volume production, injection molding generally becomes more cost-effective. While the initial cost of the mold is higher, the per-unit cost decreases significantly as production quantities increase. If you’re looking for precision, consistency, and the ability to produce parts at high speed, injection molding is usually more suitable than casting for medical device manufacturing.
How big is the plastic injection molding machine market?
The global plastic injection molding machine market is substantial and is projected to continue growing, with forecasts estimating it could reach over $20 billion by 2027. The market’s growth is driven by the increasing demand for injection molding in various industries, including automotive, consumer goods, packaging, and particularly in medical device manufacturing. As the medical industry increasingly relies on high-volume production of precise, durable components, the need for efficient injection molding machines has expanded.
Medical devices require materials and molds that adhere to strict quality control standards, and this drives the need for advanced and specialized injection molding equipment. The rise in demand for miniaturized, complex medical parts that require precise molding is further contributing to the market’s growth. Additionally, technological advancements, such as automated machines and multi-component molding technologies, are improving production efficiency, increasing the adoption of these machines in the medical sector.
As the healthcare sector continues to expand globally, particularly in emerging markets, the demand for plastic injection molding machines in medical device manufacturing is expected to rise, making it a key area of growth for the market.
What is the difference between 3D printing and injection molding?
3D printing and injection molding are both manufacturing processes used to produce plastic parts, but they differ in their methods, material usage, and best applications.
3D printing is an additive manufacturing process where material is deposited layer by layer based on a digital model. This process is highly flexible, allowing for complex geometries and quick prototyping without the need for molds. 3D printing is ideal for low-volume production, prototyping, and creating custom medical devices or components that are not mass-produced. It offers significant advantages in terms of design flexibility and fast iteration, which is particularly useful in medical device development.
Injection molding, on the other hand, involves injecting molten plastic into a pre-made mold to form the desired shape. It is a subtractive manufacturing process that excels in producing large quantities of consistent, high-precision parts. It is often used for mass production in industries like medical devices, where the parts need to meet high standards for quality, durability, and regulatory compliance. The upfront costs for injection molding are higher due to the need for specialized molds, but the per-unit cost drops significantly as production volume increases.
The key difference is that 3D printing is more cost-effective for low-volume and customized parts, while injection molding is the preferred choice for high-volume, precision manufacturing of medical devices or parts.
Is it cheaper to injection mold or 3D print?
The cost-effectiveness of injection molding versus 3D printing depends on the production volume and part complexity.
3D printing is typically cheaper for low-volume production or rapid prototyping because it does not require the upfront investment in molds. It is also ideal for producing customized or complex parts with intricate geometries that might be difficult or costly to mold. However, 3D printing can be slow and less efficient for mass production.
Injection molding is generally more cost-effective for high-volume production. While the initial cost of creating a mold can be expensive, the per-unit cost decreases significantly as production runs increase. For large-scale manufacturing of standardized parts (like medical devices), injection molding offers substantial savings in the long run.
In summary, if you’re producing a small number of prototypes or custom parts, 3D printing is cheaper. But if you need to produce a large number of identical parts with high precision and speed, injection molding will be more cost-efficient in the long term.
What is the strongest plastic for injection molding?
The strongest plastic commonly used in injection molding for medical applications is polycarbonate (PC). Polycarbonate is known for its high impact resistance, optical clarity, and heat resistance, making it an ideal choice for medical devices that require durability and strength. It’s often used in products such as surgical instruments, diagnostic equipment, protective medical housings, and medical containers. Polycarbonate’s toughness allows it to withstand mechanical stress without cracking or breaking.
Another strong plastic is acetal (POM), also known as Delrin. Acetal is highly resistant to wear, chemicals, and fatigue, making it ideal for moving parts in medical devices like pumps, valves, and gears.
Both materials offer excellent mechanical properties, which are essential in ensuring the durability and performance of medical components under demanding conditions.
Contact our professional team now for a same-day quote and risk-free project evaluation. Benefit from ISO 8 cleanrooms, advanced machines, and 12-hour fast response in medical injection molding.