The medical device industry is experiencing rapid growth, driven by advancements in technology and the increasing demand for innovative healthcare solutions. Plastic components play a vital role in this sector due to their versatility, durability, and cost-effectiveness. From intricate catheters and tubing to sterile packaging, plastics are fundamental to creating reliable and efficient medical devices. Medical device assembler are crucial in this process, as they ensure that plastic components are correctly assembled and integrated into finished products that meet strict regulatory standards. Plastic Medical Device Manufacturers design & development including medical molded plastics and medical injection molded plastics. Plastic medical device manufacturers are at the forefront of this innovation, enabling the production of high-quality components that meet stringent regulatory standards. These manufacturers not only drive the development of cutting-edge technologies but also ensure scalability and customization to address diverse medical needs. Their contributions are essential for improving patient outcomes and advancing global healthcare systems.
Key Plastic Medical Device Manufacturers
The field of plastic medical device manufacturers is integral to the healthcare industry, featuring a wide range of companies that lead in innovation, scalability, and quality. From global corporations to agile small-scale enterprises, these manufacturers deliver critical components used across various medical applications.
Leading Plastic Medical Device Manufacturers
Several top companies set the standard for excellence in this industry, offering advanced capabilities and comprehensive services:
FUJIU Medical Injection Mold
FUJIU Medical Injection Mold, a leading manufacturer headquartered in China, specializes in precision medical injection molding. Our company integrates precision mold medical technology into our operations, ensuring the highest standards in manufacturing and quality. Located in a strategic industrial hub, we have easy access to global supply chains and advanced technology, with our headquarters serving as the center for R&D, production, and quality control processes.
- Expertise: With a state-of-the-art facility, our company ensures high standards in the production of medical-grade injection-molded components, such as syringes, IV connectors, and diagnostic equipment.
- Capabilities: FUJIU Medical Injection Mold prides Ourselves on offering both high-quality products and reliable medical molding services, which has contributed to its reputation in the medical manufacturing industry.
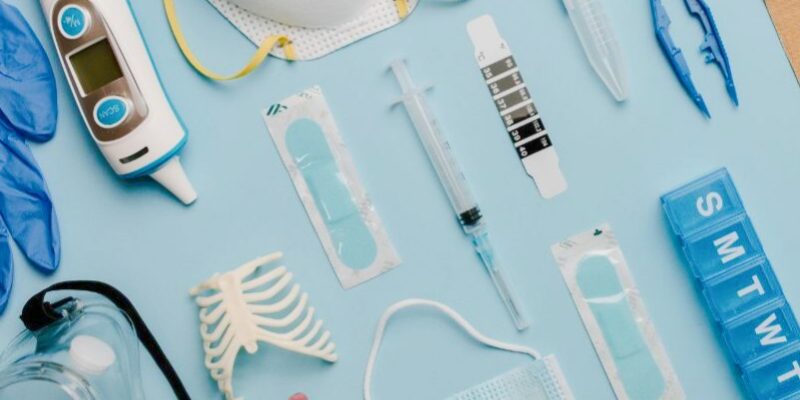
Plastic Medical Device Manufacturers: Medical Device Components for Every Need
Medical Device Components for Every Need
In the rapidly evolving healthcare and medical technology sectors, the demand for high-quality, reliable, and versatile medical device components has never been greater. These components form the backbone of countless medical devices, playing a pivotal role in diagnosing, treating, and monitoring patient health. Whether for small-scale, portable devices or complex hospital systems, the right components ensure functionality, durability, and patient safety.
Key Categories of Medical Device Components
- Electronic Components
- Sensors: Vital for capturing data such as temperature, pressure, oxygen levels, and heart rate in monitoring devices.
- Microprocessors and Controllers: Serve as the brain of devices, enabling precise operation and real-time data processing.
- Battery Solutions: Powering devices ranging from handheld diagnostic tools to implantable devices like pacemakers.
- Connectors and Switches: Ensuring seamless communication between various device parts.
- Mechanical Components
- Housings and Casings: Designed to protect sensitive components and provide ergonomic use for healthcare providers.
- Gears and Actuators: Essential for motion control in devices like infusion pumps or surgical robots.
- Bearings and Springs: Allowing smooth mechanical movements in intricate surgical and diagnostic tools.
- Optical Components
- Lenses and Mirrors: Key for devices like endoscopes, microscopes, and imaging systems.
- Fiber Optics: Used in minimally invasive surgeries and advanced diagnostic equipment.
- Lasers: Found in surgical, cosmetic, and ophthalmic applications.
- Fluidic Components
- Tubes and Fittings: Used in devices that manage the flow of liquids or gases, such as IV systems or ventilators.
- Valves and Pumps: Critical for controlling and directing fluids in medical infusion systems or dialysis machines.
- Filters and Reservoirs: Ensuring the purity and accuracy of fluid systems.
- Materials and Coatings
- Biocompatible Materials: Such as silicone, stainless steel, and medical-grade plastics used in implantable devices.
- Antimicrobial Coatings: Enhancing hygiene and reducing infection risks, especially in hospital environments.
- Conductive Coatings: For devices requiring precise electrical transmission.
- Software and Connectivity Components
- Firmware and Embedded Systems: Enabling device control and customization for specific medical applications.
- Wireless Modules: Facilitating connectivity for remote patient monitoring systems.
- Data Integration Systems: Supporting interoperability between devices and hospital information systems.
Advantages of Choosing High-Quality Components
- Reliability: Ensures uninterrupted performance during critical medical operations.
- Compliance: Meets stringent industry regulations and standards (e.g., FDA, ISO).
- Customization: Tailored solutions for specific applications and devices.
- Durability: Long-lasting materials reduce maintenance costs and improve patient outcomes.
- Safety: Minimized risks due to advanced design and manufacturing processes.
The choice of medical device components can make or break the performance of a medical device. Partnering with trusted suppliers ensures access to cutting-edge technology, robust support, and scalable solutions for any healthcare need.
Whether you are developing a next-generation surgical robot, upgrading diagnostic tools, or enhancing patient care with wearable devices, there’s a perfect set of components designed to meet your unique requirements.
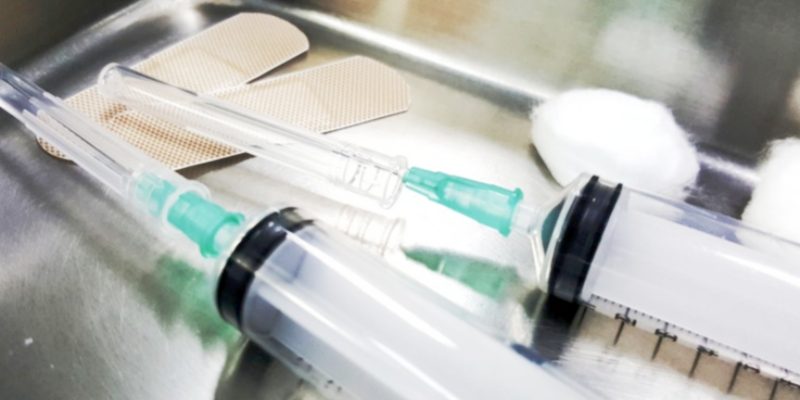
Plastic Medical Device Manufacturers: Extrusion Technologies for Catheters and Device Assemblies
Extrusion technology is a critical manufacturing process in the medical device industry, especially for the production of catheters and other intricate device assemblies. This advanced technique allows for the creation of high-performance components with precision tolerances, complex geometries, and biocompatible materials. These features are essential for ensuring functionality, safety, and reliability in medical applications.
Key Features of Extrusion Technology
- High Precision
- Enables production of components with exact dimensions and tight tolerances.
- Ideal for intricate medical devices requiring micro-dimensions.
- Custom Design Capabilities
- Supports multi-lumen, co-extrusion, and braided or reinforced tubing.
- Facilitates unique geometries tailored to specific medical needs.
- Material Versatility
- Compatible with a wide range of medical-grade polymers, including:
- Polyurethane (PU)
- Polyethylene (PE)
- Polyether ether ketone (PEEK)
- Thermoplastic elastomers (TPE)
- Silicone
- Compatible with a wide range of medical-grade polymers, including:
- Biocompatibility
- Meets stringent medical standards, ensuring compatibility with the human body.
- Resistance to sterilization methods such as autoclaving, gamma radiation, and ethylene oxide (EtO).
- Scalability
- Suitable for both prototype development and mass production.
Types of Extrusion Techniques
- Single-Lumen Extrusion
- Produces simple tubing with a single channel.
- Commonly used for drug delivery systems and diagnostic devices.
- Multi-Lumen Extrusion
- Creates tubing with multiple channels for fluid or wire passage.
- Essential for complex catheters and endoscopy devices.
- Co-Extrusion
- Combines different materials into a single extrusion.
- Provides unique properties like flexibility on the exterior and rigidity on the interior.
- Tapered Extrusion
- Produces tubing with variable diameters along its length.
- Useful for access devices or tapered catheters.
- Braided and Reinforced Extrusion
- Integrates fibers or metal wires within the tubing for added strength and flexibility.
- Applied in high-pressure environments, such as angioplasty or surgical procedures.
- Micro-Extrusion
- Designed for producing extremely small diameters and thin walls.
- Ideal for minimally invasive devices.
Applications of Extrusion in Catheters and Device Assemblies
- Catheters
- Cardiovascular catheters (e.g., angiographic, balloon)
- Urological catheters (e.g., Foley, intermittent)
- Neurovascular catheters for minimally invasive surgery
- Drug Delivery Systems
- Infusion pumps
- Intravenous tubing
- Minimally Invasive Surgical Tools
- Endoscopic components
- Laparoscopic instrument channels
- Diagnostic Devices
- Microfluidic channels for lab-on-a-chip devices
- Imaging probes and optical fiber tubing
- Implantable Devices
- Long-term drainage tubing
- Vascular grafts and stents
Advantages of Using Extrusion for Medical Devices
- High Performance and Durability
- Tubing can withstand mechanical stress and environmental exposure.
- Materials optimized for flexibility, rigidity, or both as needed.
- Consistency and Reproducibility
- Advanced extrusion techniques deliver uniformity across production batches.
- Enhanced Patient Safety
- Biocompatible materials and precision engineering reduce risks of infection or malfunction.
- Design Flexibility
- Custom extrusion allows manufacturers to meet diverse and complex device specifications.
- Cost Efficiency
- Scalable production processes ensure economic feasibility for small and large runs.
Extrusion technology continues to push the boundaries of innovation in catheters and medical device assemblies. By leveraging advanced materials and sophisticated manufacturing techniques, this process ensures that medical devices meet the rigorous demands of modern healthcare.
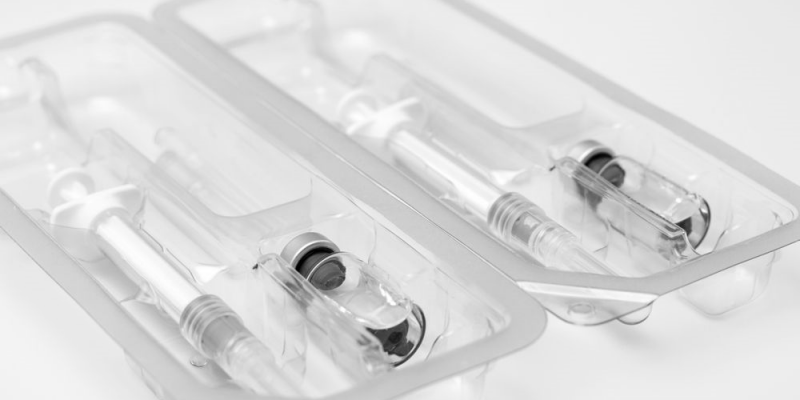
Types of Plastic Medical Devices and Applications
The diversity of products created by plastic medical device manufacturers highlights their importance in modern healthcare. These manufacturers design and produce a wide range of plastic components essential for various medical procedures and treatments. Their expertise spans standard items like tubing to highly customized, injection-molded parts and advanced packaging solutions.
Common Products Manufactured by Plastic Medical Device Manufacturers
Catheters and Tubing
Catheters and tubing are among the most critical products produced by plastic medical device manufacturers. These components are used for fluid management, surgical procedures, and diagnostic tools.
- Types of Tubing: Includes microbore tubing, multilumen designs, PEEK tubing for high-performance needs, and silicone tubing for flexibility and biocompatibility.
- Applications: Widely used in cardiovascular procedures, urinary catheters, and neurovascular interventions.
Surgical Components
Surgical devices such as retractors, dilators, and complex sheaths are also created by plastic medical equipment manufacturers.
- Precision and durability make plastics ideal for these tools, ensuring reliability during delicate surgical procedures.
Custom Injection-Molded Parts
Injection molding enables the production of intricate, high medical precision parts tailored to specific medical applications.
- Examples: Handles for surgical tools, diagnostic device casings, and bioresorbable implants.
Packaging Solutions
Sterile packaging solutions are another critical offering from plastic medical device manufacturers.
- Materials: High-performance films, and lids designed for sterilization and durability.
- Purpose: Protecting sensitive devices from contamination and ensuring sterility until use.
Applications Across Medical Fields
Cardiovascular and Neurovascular Applications
Plastic components such as tubing, catheters, and packaging play a crucial role in cardiovascular and neurovascular treatments, including angioplasty, stenting, and aneurysm repair.
Orthopedics and Sports Medicine
Devices used in joint replacements, braces, and surgical aids are frequently crafted by plastic medical device manufacturers to offer lightweight and durable solutions.
Pharmaceutical and Diagnostic Fields
Custom injection-molded parts and diagnostic tools are integral to laboratories and hospitals for sample collection, drug delivery, and testing procedures.
Other Applications
- Gastrointestinal and Enteral Feeding: Flexible tubing and connectors.
- Trauma and Wound Care: Plastic components in vacuum-assisted closure systems and wound dressings.
By providing versatile, biocompatible, and high-performance products, plastic medical device manufacturers enable breakthroughs across a broad spectrum of medical fields, improving outcomes and advancing healthcare innovation.
Materials Used by Plastic Medical Device Manufacturers
Materials play a critical role in the production of medical devices, with plastic medical device manufacturers relying on a variety of medical-grade plastics to meet the demands of durability, flexibility, and biocompatibility. Each material brings unique properties suited to specific applications, ensuring the safety and efficacy of medical devices.
Overview of Popular Medical-Grade Plastics
Material | Key Properties | Applications |
---|---|---|
Polyethylene (PE) | High impact resistance, corrosion resistance, cost-effective | Prosthetics, fluid containers |
Polypropylene (PP) | Stress and cracking resistance, high melting point | Syringes, connectors, oxygenator membranes |
Polycarbonate (PC) | High strength, heat resistance, biocompatible | IV connectors, surgical instruments, renal dialysis components |
Polyvinyl Chloride (PVC) | Flexible (sterility and durability) and rigid options (strength and reliability) | Catheters, tubing, hemodialysis devices |
Nylon (Polyamide) | High tensile strength, flexibility, abrasion, and chemical resistance | Sutures, artificial joints, surgical instruments |
PEEK (Polyetheretherketone) | Excellent mechanical properties, heat resistance, advanced biocompatibility | Implants, high-performance surgical components |
Innovations Driving Plastic Medical Device Manufacturers
Innovation is the cornerstone of progress for plastic medical device manufacturers, enabling them to meet the growing demand for precision, efficiency, and scalability in the healthcare sector. Through cutting-edge technologies like 3D printing, laser processing, and advanced prototyping, these manufacturers are transforming how medical devices are designed and produced.
3D Printing and Additive Manufacturing
3D printing, also known as additive manufacturing, has revolutionized the way plastic medical device manufacturers approach product development and production.
- Rapid Prototyping: 3D printing enables manufacturers to create prototypes quickly, allowing for faster iterations during the design phase. This significantly reduces the time-to-market for new medical devices.
- Customization: The technology facilitates the creation of patient-specific devices, such as custom orthopedic implants, dental aligners, and prosthetics, improving patient outcomes.
- Cost Efficiency: By reducing material waste and eliminating the need for expensive molds, additive manufacturing lowers production costs, particularly for small-batch and complex designs.
Laser Processing
Laser processing is another breakthrough technology widely adopted by plastic medical device manufacturers. This technique offers unparalleled precision, making it ideal for creating intricate components required in advanced medical devices.
- Cutting: Lasers are used to create fine cuts in plastics, ensuring high accuracy and smooth edges, which is essential for devices like catheters and surgical instruments.
- Drilling and Ablation: Laser drilling enables the creation of micro-holes in tubing and other components, enhancing functionality in devices such as fluid delivery systems. Ablation techniques are used to remove material with extreme precision without damaging surrounding areas.
- Wire Stripping and Tipping: In catheter manufacturing, lasers provide precise stripping and tipping, ensuring the reliability of the device.
Scalability with Rapid Prototyping and Quick-Turn Services
Scalability is critical for meeting the diverse demands of the healthcare industry, and plastic medical device manufacturers have embraced rapid prototyping and quick-turn services to achieve this.
- Seamless Transition to Mass Production: Rapid prototyping allows manufacturers to test designs and materials efficiently before scaling up to full production. This ensures quality and reduces potential errors in mass manufacturing.
- Adaptability: Quick-turn services enable manufacturers to respond promptly to changing demands, such as the need for new devices during health crises or to accommodate patient-specific requirements.
Through these innovations, medical device injection molding manufacturer are not only improving production capabilities but also pushing the boundaries of what is possible in medical technology, ultimately enhancing patient care and driving industry growth.
Evaluating the Best Plastic Medical Device Manufacturers
Selecting the right plastic medical device manufacturers is a critical decision for healthcare organizations and medical device companies. The best manufacturers are those that consistently deliver high-quality, innovative, and scalable solutions while meeting stringent industry standards. This section explores the key factors to consider and highlights companies that excel in these areas.
Factors Considered by Plastic Medical Device Manufacturers
Durability and Performance
Medical devices often face demanding conditions such as exposure to pressure, chemicals, and varying temperatures. Materials like polycarbonate and PEEK offer exceptional durability, ensuring the device remains functional throughout its lifecycle.
Biocompatibility
Biocompatibility is a fundamental requirement for any material used in medical applications. Plastics like polypropylene and nylon are widely used because they do not induce adverse biological reactions, making them suitable for use in implants, catheters, and surgical instruments.
Sterilization Compatibility
Medical-grade plastics must withstand sterilization processes such as autoclaving, gamma radiation, and chemical treatments. PVC and polyethylene excel in this aspect, maintaining their structural integrity and sterility even after repeated cycles.
Flexibility and Adaptability
Certain devices require flexible yet strong materials. Flexible PVC and nylon are preferred for applications like tubing and catheters due to their ability to bend and adapt without breaking.
Advanced Applications
High-performance materials like PEEK are used in specialized applications, including implants and minimally invasive surgical tools, due to their exceptional mechanical properties and compatibility with human tissues.
By selecting the right material for each application, plastic medical device manufacturers ensure that their products meet stringent medical standards, improving patient safety and device performance.
Quality Assurance
Quality assurance is paramount in the medical device industry, where patient safety and regulatory compliance are non-negotiable.
- Certifications: Leading plastic medical device manufacturers hold ISO 13485 certifications, ensuring that their quality management systems meet international standards for medical device production.
- Regulatory Compliance: Manufacturers must comply with FDA regulations in the U.S., CE marking requirements in Europe, and other global standards. This guarantees that their products are safe, reliable, and effective.
Customization
The ability to provide tailored solutions is a distinguishing feature of the best plastic medical device manufacturers.
- Design Expertise: Top manufacturers offer collaborative design and engineering services, enabling them to meet specific client requirements. For example, they can create custom tubing, unique catheter designs, or specialized injection-molded components.
- Material Versatility: Expertise in handling a wide range of medical-grade plastics, such as PEEK, PVC, and polycarbonate, allows manufacturers to customize products for various applications.
Scalability
The best plastic medical device manufacturers are capable of adapting their production processes to handle projects of any size.
- Small-Batch Production: For pilot projects or highly specialized devices, small-scale manufacturing capabilities ensure precision and quality.
- Mass Production: Advanced facilities equipped with automated systems allow for efficient mass production without compromising quality.
Highlighting Companies with Strong Track Records
FUJIU Medical Injection Mold
FUJIU Medical Injection Mold is a leader among injection molding medical device manufacturers, known for its comprehensive capabilities and innovation.
- Full-Service Expertise: The company excels in medical tubing, catheter production, injection molding, and packaging solutions. They provide end-to-end services, from rapid prototyping to large-scale production.
- Certifications and Compliance: With ISO-certified facilities and a proven track record of regulatory compliance, FUJIU Medical Injection Mold ensures the highest quality standards.
BMP Medical
BMP Medical specializes in injection molding and offers a strong focus on precision and customer satisfaction.
- Injection Molding Excellence: BMP is renowned for its ability to produce high-quality molded components, including tissue grinders, centrifuge bottles, and other critical medical devices.
- Custom Solutions: Their expertise in cleanroom manufacturing and process validation ensures they meet the most stringent client specifications.
By evaluating plastic medical device manufacturers based on quality, customization, and scalability, organizations can confidently choose partners that align with their specific needs. Companies like FUJIU Medical Injection Mold and BMP Medical exemplify the excellence and reliability that define this industry, making them ideal collaborators in advancing medical technology.
Investing in Plastic Medical Device Manufacturers
The growing demand for innovative medical devices and the increasing reliance on advanced materials make plastic medical device manufacturers an attractive sector for investors. These companies play a crucial role in developing critical components for healthcare applications, offering significant growth potential for those looking to capitalize on this expanding market.
Overview of the Market Trends and Growth Potential
The global medical device market is projected to grow at a compound annual growth rate (CAGR) of approximately 5-6% through 2030, driven by:
- Rising Healthcare Needs: An aging population and the prevalence of chronic diseases have increased the demand for advanced medical devices, many of which rely on high-quality plastic components.
- Technological Advancements: Innovations in 3D printing, biocompatible materials, and precision manufacturing have enhanced the capabilities of plastic medical device manufacturers, opening new avenues for growth.
- Focus on Sustainability: Manufacturers are adopting eco-friendly practices and materials, aligning with global trends for sustainable healthcare solutions.
This steady growth positions plastic medical device manufacturers as a resilient and profitable sector, appealing to both long-term and short-term investors.
Plastic Medical Device Manufacturers Stock
Investing in publicly traded plastic medical device manufacturers provides an opportunity to benefit from the industry’s expansion. Here are some key players and their potential impact on the market:
FUJIU Medical Injection Mold
With a state-of-the-art facility, FUJIU Medical Injection Mold ensures high standards in the production of medical-grade injection-molded components, such as syringes, IV connectors, and diagnostic equipment. FUJIU’s location also supports its international expansion and ability to serve clients across North America, Europe, and other regions.
Industry Outlook for Investors
The investment outlook for plastic medical device manufacturers remains strong, with several key factors driving growth:
- Healthcare Expansion in Emerging Markets: Increased access to medical care in developing countries is boosting the demand for affordable and reliable medical devices.
- Integration of Advanced Manufacturing Technologies: Companies investing in 3D printing, laser processing, and sustainable practices are likely to see accelerated growth.
- Mergers and Acquisitions: Consolidation within the industry provides opportunities for investors to capitalize on synergies and expanded capabilities.
Investing in plastic medical device manufacturers offers a unique opportunity to participate in the growth of a critical sector within healthcare. By targeting companies with strong market positions, innovative technologies, and a focus on sustainability, investors can align their portfolios with long-term industry trends while supporting advancements in global healthcare.
Why Choose US-Based Plastic Medical Device Manufacturers?
When selecting a partner for medical device production, plastic medical device manufacturers based in the United States offer numerous advantages. From high-quality standards to advanced technology, these manufacturers ensure reliability, efficiency, and superior outcomes, making them a top choice for companies worldwide.
Advantages of Working with US-Based Plastic Medical Device Manufacturers
High-Quality Standards and Advanced Technology
- Regulatory Excellence: US-based medical device plastic injection molding manufacturers adhere to stringent quality standards, such as ISO 13485 certification and FDA compliance. These rigorous requirements ensure the production of safe and reliable medical devices.
- Cutting-Edge Technology: US manufacturers lead the industry in adopting innovative technologies such as 3D printing, laser processing, and advanced injection molding techniques. Their expertise in these areas enables them to produce complex components with unmatched precision.
- Material Expertise: Many US manufacturers have deep experience working with biocompatible materials like PEEK, polycarbonate, and flexible PVC, ensuring products meet the specific needs of diverse medical applications.
Streamlined Supply Chains and Faster Delivery
- Proximity to Markets: For companies based in North America, working with US-based plastic medical device manufacturers reduces shipping times and costs, ensuring faster delivery of products to market.
- Reliable Supply Chains: US manufacturers often maintain robust domestic supply chains, minimizing disruptions caused by global trade challenges or logistical delays. This reliability is crucial for maintaining continuous production.
- Customization and Responsiveness: Proximity to clients allows US manufacturers to work closely with partners, offering quick-turn prototyping and scalable production to meet evolving project requirements.
Leading manufacturers to consider
Several plastic medical device manufacturers were recognized for their innovation, quality and customer-centricity:
FUJIU Medical Injection Mold
FUJIU Medical Injection Mold is headquartered in China, where it operates as a leading manufacturer specializing in precision medical injection molding. The company is located in a strategic industrial hub, providing easy access to global supply chains and advanced technology. FUJIU’s headquarters serves as the center for its research and development (R&D), production, and quality control processes.
Choosing US-based plastic medical device manufacturers offers distinct advantages in quality, technology, and supply chain efficiency. These manufacturers bring unparalleled expertise and reliability to the table, making them ideal partners for companies seeking high-performance solutions in the medical device industry. For businesses looking to streamline operations while maintaining world-class standards, US-based manufacturers remain an excellent choice.
FAQs about Plastic Medical Device Manufacturers
Plastic is a fundamental material in modern medical equipment due to its versatility, durability, and cost-effectiveness. A wide range of medical equipment is made from plastic, including catheters, syringes, IV bags, and surgical instruments. Plastics like polyethylene, polypropylene, and polycarbonate are commonly used to manufacture prosthetics, diagnostic equipment casings, and fluid management systems. Advanced plastic materials such as PEEK and PVC are utilized in applications requiring high performance and biocompatibility, such as implants, tubing, and cardiovascular devices. Additionally, disposable medical items like gloves, test tubes, and pipettes are predominantly made of plastic, ensuring sterility and reducing the risk of contamination. From intricate components in robotic surgical systems to everyday tools like stethoscope parts, plastic plays a critical role in delivering safe and efficient healthcare solutions.
Determining the leading medical device maker depends on the specific criteria, such as revenue, innovation, or market share. Companies like Medtronic, Johnson & Johnson, and Abbott are often recognized as leaders in the industry. Medtronic, for example, is known for its extensive portfolio, ranging from cardiovascular and diabetes care devices to surgical instruments. Johnson & Johnson leads in orthopedic and surgical innovations, while Abbott excels in diagnostics and drug-delivery systems. When it comes to plastic medical device manufacturers, FUJIU Medical Injection Mold is a standout leader, offering comprehensive solutions from medical tubing and catheters to injection molding and packaging. Their expertise in design, scalability, and advanced manufacturing techniques sets them apart as a top innovator in the industry.
Polyvinyl chloride (PVC) is one of the most widely used plastics in the medical field, valued for its flexibility, durability, and biocompatibility. Medical devices made of PVC include blood bags, IV tubing, catheters, and dialysis equipment. Flexible PVC is commonly used for components requiring sterility and elasticity, such as oxygen masks and enteral feeding tubes. Rigid PVC is used in devices that need structural strength, like hemodialysis systems and certain cardiac catheters. PVC is also integral to surgical gloves and sterile packaging solutions, as it can withstand various sterilization processes, including autoclaving and gamma radiation. Its affordability and versatility make it a preferred material for both disposable and reusable medical devices.
BMP Medical is headquartered in Sterling, Massachusetts, USA. The company operates a state-of-the-art facility that specializes in custom plastic injection molding and blow molding for the medical and diagnostic industries. Their capabilities include cleanroom manufacturing, process validation, and the production of high-precision components such as centrifuge bottles, tissue grinders, and urine collection kits. As a trusted name among plastic medical device manufacturers, BMP Medical emphasizes quality, innovation, and customer satisfaction. Their location in the United States provides easy access to clients across North America, ensuring reliable supply chain management and fast delivery of products. With ISO 13485:2016 certification, BMP Medical adheres to the highest industry standards, making them a key player in the medical manufacturing sector.
Bioplastics used in medical devices primarily include polylactic acid (PLA), polyhydroxyalkanoates (PHA), and bio-based polyethylene (Bio-PE). These materials are valued for their sustainability and biocompatibility. PLA is commonly used in applications such as sutures, drug delivery systems, and biodegradable stents due to its ability to degrade safely within the body. PHAs, which are naturally produced by microbial fermentation, are used in wound care and tissue engineering. Bio-PE, derived from renewable resources like sugarcane, is used for durable medical devices such as surgical instruments and prosthetics. These materials align with the medical sector’s focus on reducing environmental impact while ensuring high safety and performance standards.
Polycarbonate (PC) is widely used in medical devices due to its strength, clarity, and resistance to sterilization methods such as autoclaving. Common applications include blood oxygenators, IV connectors, surgical instruments, and hemodialysis filters. Its optical clarity makes it ideal for devices like medical light guides and housings for diagnostic instruments. PC’s impact resistance and dimensional stability also make it suitable for wearable medical devices and durable enclosures for electronic medical equipment. Additionally, it is often used in combination with coatings to enhance biocompatibility and reduce microbial adhesion.
The fastest growing medical device market is wearable medical technology, driven by advancements in remote monitoring and personalized medicine. Wearable devices such as glucose monitors, ECG patches, and smart inhalers are gaining popularity due to their ability to provide real-time data for chronic disease management. Innovations in biosensors, miniaturization, and integration with mobile health platforms have spurred demand. The aging global population and the prevalence of conditions like diabetes and cardiovascular diseases are also accelerating market growth. This sector is projected to expand significantly over the next decade, especially in regions with increasing access to healthcare technologies.
Hydrophilic coatings are among the most widely used in medical devices. These coatings reduce friction and enhance the performance of devices in contact with bodily fluids. They are commonly applied to catheters, guidewires, and stents to improve patient comfort and reduce tissue damage during procedures. Other widely used coatings include antimicrobial coatings to prevent infections and drug-eluting coatings that deliver therapeutic agents locally. The choice of coating depends on the device’s function and the clinical environment, with innovations focusing on improving biocompatibility and durability.
Plastics are ubiquitous in medical devices, with applications in single-use products and complex systems. Common devices include syringes, IV bags, catheters, and blood storage containers. Durable plastics like polycarbonate, polyethylene, and polypropylene are used in surgical instruments, diagnostic equipment, and prosthetics. The flexibility of plastics like PVC makes them ideal for tubing and connectors. Their lightweight, moldability, and resistance to chemical sterilization contribute to their widespread use, particularly in reducing costs and improving design versatility.
Polyvinyl chloride (PVC) is primarily used in the medical industry for flexible tubing, blood bags, and IV containers. Its properties, such as flexibility, durability, and compatibility with sterilization techniques, make it ideal for critical healthcare applications. PVC is also used in protective gloves, surgical drapes, and medical packaging. Its adaptability to a wide range of formulations, including soft and rigid forms, supports diverse medical applications. The material’s affordability and ease of manufacturing further drive its extensive use in healthcare.
PVC (polyvinyl chloride) is manufactured using vinyl chloride monomer (VCM) through a polymerization process. Additives like plasticizers, stabilizers, and fillers are incorporated to modify its properties for medical applications. For example, plasticizers enhance flexibility, while stabilizers improve heat and light resistance. These additives are selected carefully to meet the stringent biocompatibility and safety standards required for medical use. The manufacturing process includes strict quality control to ensure that the final product is free from contaminants, making it suitable for applications such as blood storage bags and medical tubing.
Contact our professional team now for a same-day quote and risk-free project evaluation. Benefit from ISO 8 cleanrooms, advanced machines, and 12-hour fast response in medical injection molding.