Plastic medical parts play a crucial role in transforming modern healthcare by replacing traditional materials like metal, glass, and ceramics. These materials offer significant advantages, such as reduced weight, increased durability, and lower production costs. As a result, plastic medical parts have become essential in devices like syringes, catheters, implants, and drug delivery systems, enhancing patient care and safety. Precision mold medical manufacturing, especially in a China medical plastic parts factory, is a key aspect of this transformation, enabling the production of highly accurate, high-quality components that meet the complex requirements of the healthcare sector. Key trends in medical plastics focus on innovations like micro molding, which allows for precise, small-scale components, ideal for advanced medical applications. Additionally, the development of advanced materials such as PEEK, polycarbonate, and silicone provides healthcare manufacturers with versatile options for customization, ensuring plastic medical parts meet the stringent demands of the industry and regulatory standards. Plastic medical parts, made from biocompatible, sterilization-resistant polymers, are vital in devices like implants and surgical tools, and factories in China play a significant role in providing cost-effective, high-quality solutions for the global healthcare market.
Key Advantages of Plastic Medical Parts
Plastic medical parts offer numerous benefits that make them indispensable in modern healthcare. These advantages enhance both the functionality and safety of medical devices, from surgical instruments to implants.
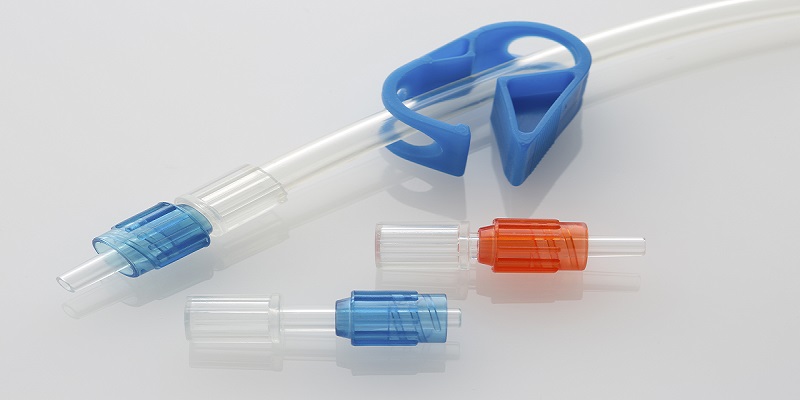
Here are the key benefits of plastic medical parts:
Biocompatibility: Ensuring Safety for Patient Contact
One of the most crucial advantages of plastic medical parts is their biocompatibility. Materials used in plastic medical parts are designed to interact safely with the human body, ensuring that they do not cause adverse reactions when in contact with tissue or fluids. This makes plastics ideal for long-term use in implants, catheters, and other medical devices that are inserted into the body.
Customization and Scalability: Perfect for Small-Scale Prototypes and Mass Production
Plastic medical parts are highly customizable, allowing manufacturers to create devices tailored to specific medical needs. The versatility of plastics, combined with advanced manufacturing processes like medical injection molding and micro molding, makes it easy to produce small-scale prototypes for testing or scale up to mass production. Whether for a unique, patient-specific implant or a standard medical tool, plastic medical parts offer excellent scalability.
Sterilization and Durability: Resistance to High-Temperature, Impact, and Repeated Sterilization Cycles
Plastic medical parts are engineered for durability and resistance to the harsh conditions found in medical environments. They can withstand high temperatures and repeated sterilization cycles without degrading, making them ideal for use in hospitals and clinics. Materials such as polypropylene and polycarbonate are commonly used in surgical tools and medical containers that require frequent sterilization.
Regulatory Compliance: Meeting ISO 10993, USP Class VI, and Other Global Standards
Plastic medical parts must comply with strict regulatory standards to ensure their safety and effectiveness. Materials used in medical device plastic manufacturing need to meet standards such as ISO 10993 for biocompatibility and USP Class VI for medical device materials. Manufacturers of plastic medical parts must ensure that their products conform to these regulations to guarantee the safety and reliability of the devices they produce. This compliance is essential for gaining FDA approval and ensuring that products meet global healthcare standards.
Applications of Plastic Medical Parts
Plastic medical parts are integral to a wide range of medical applications, thanks to their versatility, biocompatibility, and cost-effectiveness. From surgical instruments to drug delivery systems, the use of plastic medical parts has revolutionized the healthcare industry, improving patient outcomes and enhancing device functionality. Prototypes medical molded plastic are often used in the early stages of design to test and refine these parts, ensuring they meet the strict functional and safety standards required in medical applications. These prototypes help manufacturers optimize designs before full-scale production, ensuring reliability and performance in the final product. Below are some key applications where plastic medical parts are commonly used:
Surgical Instruments and Components
Plastic medical parts are frequently used in surgical instruments, providing lightweight, durable, and sterilizable components. Handles, housings, and casings made from high-performance plastics such as polyetherimide (PEI) and polysulfone (PSU) offer excellent strength and thermal resistance, ensuring they can withstand repeated sterilization cycles without degrading. These materials are ideal for surgical tools because they are resistant to chemical corrosion and high temperatures, making them both safe and long-lasting in demanding hospital environments. The lightweight nature of these plastic parts also helps reduce the strain on healthcare professionals during lengthy surgeries, enhancing both comfort and precision.
Medical Tubing and Drug Delivery Systems
Plastic medical parts are essential in the production of medical tubing and drug delivery systems, particularly for devices that require flexibility, chemical resistance, and precision. Medical tubing, used in applications such as catheters and intravenous (IV) lines, needs to be flexible to navigate the human body while maintaining strength and durability. Plastics like polyurethane, PVC, and polyethylene are commonly used to manufacture these tubes, providing the necessary flexibility and resistance to chemical degradation. Additionally, plastic medical parts play a key role in wearable drug delivery devices, such as insulin pumps and infusion systems. Companies use advanced plastic materials to create precision components that deliver medication accurately and safely. These plastic parts are designed to meet stringent regulatory standards while offering comfort and ease of use for patients.
Implants and Prosthetics
In the field of implants and prosthetics, plastic medical parts are utilized to create durable, lightweight components that improve the functionality and longevity of medical devices. Materials such as PEEK (polyether ether ketone) and UHMW-PE (ultra-high molecular weight polyethylene) are ideal for joint replacements and spinal implants due to their exceptional biocompatibility, strength, and resistance to wear. PEEK, in particular, offers high performance in load-bearing applications, while UHMW-PE is widely used in applications requiring impact resistance and durability, such as hip and knee replacements. These plastic materials help create prosthetic limbs and implants that are both functional and comfortable, contributing to improved patient mobility and quality of life.
Wearable Devices and Sensors
Wearable devices, including sensors for monitoring vital signs and drug delivery systems, benefit greatly from the use of plastic medical parts. Plastics such as PET (polyethylene terephthalate) and silicone are commonly used in the manufacturing of these devices. PET is known for its excellent transparency, strength, and chemical resistance, making it ideal for applications where clear monitoring or flexibility is necessary. Silicone, on the other hand, is prized for its flexibility, comfort, and durability, making it an excellent material for wearable sensors and medical patches that require prolonged skin contact. The integration of these plastic materials ensures that wearable medical devices are not only durable and comfortable but also capable of withstanding the harsh conditions of daily wear while providing accurate and reliable data.
Challenges and Future Opportunities in Plastic Medical Parts
The use of plastic medical parts has transformed healthcare, providing innovative solutions for devices and treatments. However, the growing demand for these parts comes with its own set of challenges. These challenges present opportunities for growth and innovation in the industry, particularly for medical plastic parts companies that are driving advancements in materials and manufacturing techniques. Below, we explore the key issues currently facing plastic medical parts and the future opportunities that may shape the next generation of healthcare solutions.
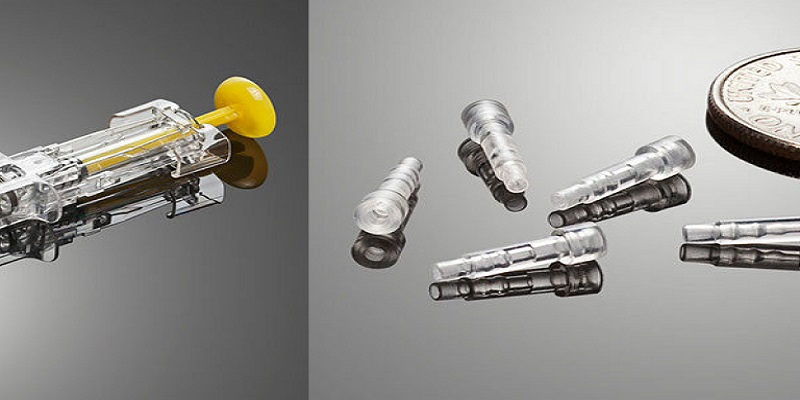
Material Selection and Sustainability
One of the primary challenges in the production of plastic medical parts is finding the right balance between performance and sustainability. Medical devices require materials that meet high standards of durability, biocompatibility, and resistance to wear and sterilization. However, these properties are often associated with plastics that are not environmentally friendly, posing a dilemma for manufacturers who seek to reduce their environmental impact. The growing pressure for sustainability in the healthcare sector has led to the exploration of eco-friendly alternatives for plastic medical parts. Manufacturers are looking into biodegradable plastics, recyclable materials, and sustainable production processes. In addition, double injection plastics for medical parts wholesale offer a potential solution by enabling the use of multiple materials in a single part, optimizing both functionality and sustainability. The challenge lies in maintaining the superior performance and safety characteristics of plastic medical parts while integrating sustainable practices. Finding these sustainable solutions will be a crucial step in ensuring that the growth of medical plastic usage does not come at the cost of the environment.
Meeting Regulatory Standards
Plastic medical parts must adhere to stringent regulatory standards to ensure they are safe for patient use. This includes compliance with ISO 10993, USP Class VI, and other international certifications. However, navigating the complexities of regulatory approvals, particularly from the U.S. Food and Drug Administration (FDA), can be a daunting process. Manufacturers of molded medical components must ensure their products meet a wide range of standards for safety, quality, and efficacy, and this often requires extensive testing and validation. The challenge of regulatory compliance becomes even more complex as new materials and innovative manufacturing processes are introduced. Adapting to the evolving regulations for plastic medical parts, while ensuring that the materials and designs meet the required standards, is a continual process for medical device companies. Companies must invest in quality control systems and rigorous testing protocols to achieve regulatory approval and ensure that their products are safe for healthcare applications.
Innovation in Micro Molding and Automation
Advances in micro molding technology and automation have opened up new opportunities for producing plastic medical parts with high precision and efficiency. Micro molding involves producing very small, intricate plastic parts with tight tolerances, which is essential for many modern medical devices. The use of robotics and artificial intelligence (AI) in medical micro molding processes has enabled manufacturers to produce medical plastic components at scale while maintaining a high level of accuracy. Automation has also improved the speed of production, reduced human error, and lowered costs, all of which are critical factors in the rapidly growing medical device market. The ability to create highly complex and detailed plastic medical parts at a fraction of the cost and time compared to traditional manufacturing methods is a game changer for the industry. As the demand for personalized and specialized medical devices increases, the role of advanced manufacturing technologies will continue to grow, providing manufacturers with the tools to meet the evolving needs of healthcare.
Plastic Medical Parts: Plastic Injection Molding in Medical Parts Manufacturing
Plastic injection molding plays a crucial role in the production of high-quality plastic medical parts. Plastic injection molding medical parts companies leverage this versatile and cost-effective manufacturing technique to create intricate and highly precise parts that are essential in the healthcare industry.
Plastic Injection Molding Medical Parts
Plastic injection molding is commonly used in the production of medical components due to its ability to create complex, high-precision medical parts efficiently. From surgical instruments to medical enclosure molding, this method ensures that parts meet the necessary performance and regulatory standards while maintaining cost-effectiveness.
Best Plastic Injection Molding Medical Parts
The best plastic injection molding medical parts are those that combine quality, precision, and regulatory compliance. Materials like polycarbonate, polypropylene, and polyetherimide are often used in injection molding for medical parts due to their durability, biocompatibility, and ability to withstand sterilization processes. These parts are vital in ensuring the safety and effectiveness of medical devices.
Plastic Injection Molding Medical Parts Re+
Plastic injection molding medical parts Re+ refers to the production of reusable, high-quality medical components designed for multiple uses. These parts are engineered for durability and can endure repeated sterilization cycles. Reusability in medical components helps reduce waste while providing cost-efficient solutions for healthcare applications.
Manufacture of Plastic Parts for the Medical Sector
The manufacture of plastic parts for the medical sector involves a highly specialized approach to ensure that the parts meet the stringent demands of healthcare applications. Plastic injection molding is often the go-to method for producing components such as drug delivery systems, catheters, and implants, as it provides a precise, repeatable process that ensures product consistency.
Plastic Injection Moulded Parts for Medical Technology
Plastic injection moulded parts for medical technology are integral to the development of advanced medical devices. These parts must meet specific functional and safety requirements, including biocompatibility, durability, and ease of sterilization. Injection molding enables manufacturers to produce parts with the exact specifications required for medical applications, making it a preferred method for creating custom parts in medical technology. This process is widely used in producing medical moulded products, which range from intricate components like surgical instrument housings to essential items such as sterile packaging and diagnostic tools, all of which require precision and reliability.
Plastic Medical Parts: Technologies Driving Medical Plastic Innovation
The continuous evolution of medical plastic parts is fueled by innovations in manufacturing techniques and materials. Advances in technologies such as medical tubing manufacturing, as well as the use of specialized materials, are pushing the boundaries of what is possible in the creation of plastic medical parts. These innovations help meet the growing demand for more precise, durable, and customizable medical devices.
Medical Tubing Manufacturing
Medical tubing is a fundamental component used in various healthcare applications, including catheters, drug delivery systems, and respiratory devices. It plays a crucial role in ensuring the safe and effective transfer of fluids, medications, and gases within the human body. The manufacturing of plastic medical tubing requires high precision, flexibility, and reliability to meet the stringent requirements of medical molding industry.
Manufacturers are pioneers in this field, providing advanced solutions for medical tubing that offers superior performance in terms of flexibility, chemical resistance, and sterilization capabilities. Their cutting-edge technology ensures that plastic medical parts such as tubes can withstand various stresses during medical procedures while maintaining their integrity over time. Additionally, medical tubing must comply with international regulatory standards such as ISO 10993 and USP Class VI to ensure biocompatibility, making it suitable for use in sensitive medical applications.
Advanced Materials and Techniques
The development of advanced materials and innovative manufacturing techniques plays a significant role in enhancing the functionality and performance of medical plastic parts. One such method is SMC (Sheet Molding Compound) molding, a process used to create durable and complex shapes that are essential for certain medical devices. SMC molding enables manufacturers to produce high-strength plastic medical parts that can withstand harsh environments, such as high temperatures and chemical exposure, while maintaining their structural integrity.
Additionally, the selection of high-performance materials like silicone, PEEK (Polyetheretherketone), and polycarbonate allows for the creation of plastic medical parts with specific properties tailored to different medical applications.
- Silicone is commonly used for medical devices that require flexibility, biocompatibility, and the ability to withstand extreme temperature variations. It is widely used in wearable medical devices, sensors, and seals.
- PEEK is a high-strength, heat-resistant plastic that is ideal for medical implants, such as spinal and joint replacements, as it is chemically resistant and highly durable. PEEK plastic medical parts are especially valuable in applications that demand long-term performance and resistance to bodily fluids.
- Polycarbonate is known for its clarity, making it an excellent choice for parts that require optical transparency, such as endoscopes, surgical devices, and other diagnostic tools. It also offers durability, impact resistance, and ease of sterilization, which are crucial for maintaining the safety and reliability of medical devices.
By incorporating these advanced materials and manufacturing techniques into the production of plastic medical parts, manufacturers can meet the increasing demand for sophisticated medical devices that deliver better patient outcomes. These technologies not only enhance the performance of medical plastic parts but also enable customization and scalability for various healthcare applications.
Types of Plastic Medical Parts Used in Medical Injection Molding
Medical injection molding has revolutionized healthcare by enabling the mass production of precise and versatile plastic medical parts. These components are crafted from various plastics, each selected for specific applications based on their properties, safety, and compliance with stringent medical standards. Here’s an in-depth exploration of commonly used medical plastics:
Polypropylene (PP)
Polypropylene is a thermoplastic polymer widely used in medical applications due to its excellent chemical resistance, low cost, and versatility. It is lightweight and retains its strength even when exposed to sterilization processes like autoclaving. Polypropylene can also be copolymerized to improve impact resistance, making it suitable for high-performance medical devices.
Advantages:
- Chemically inert and resistant to moisture and solvents.
- Can be sterilized via autoclaving without significant degradation.
- Easy to mold and process, making it cost-efficient for large-scale production.
Disadvantages:
- Limited heat resistance compared to some other medical-grade plastics.
- Prone to oxidation when exposed to UV light over extended periods.
Applications:
- Syringes, disposable labware, surgical trays, and containers.
- Flexible packaging for pharmaceutical products.
Polyethylene (PE)
Polyethylene is another widely used plastic in medical applications, valued for its biocompatibility, flexibility, and moisture resistance. It is available in different densities, including low-density (LDPE) and high-density polyethylene (HDPE), catering to various medical needs.
Advantages:
- Biocompatible and resistant to microbial growth.
- Durable and flexible for tubing and prosthetics.
- Cost-effective and easy to process.
Disadvantages:
- Limited mechanical strength compared to other engineering plastics.
- Not suitable for high-temperature applications.
Applications:
- Catheters, prosthetics, and fluid containers.
- Packaging materials for sterile equipment and pharmaceuticals.
Other Information:
- Cross-linked polyethylene (PEX) is increasingly used in orthopedic implants due to its enhanced wear resistance.
Polycarbonate (PC)
Polycarbonate is a transparent, high-performance plastic known for its impact resistance and dimensional stability. Its optical clarity makes it ideal for medical devices that require visibility, such as oxygenators and surgical instruments.
Advantages:
- High optical clarity for precision devices.
- Excellent impact and heat resistance.
- Can be sterilized using various methods, including gamma radiation and ethylene oxide.
Disadvantages:
- Susceptible to stress cracking when exposed to certain chemicals.
- Higher cost compared to other medical-grade plastics.
Applications:
- Surgical instruments, IV connectors, and device housings.
- Optical components like lenses and diagnostic instruments.
Other Information:
- Polycarbonate can be blended with other plastics, such as ABS, to enhance specific properties like toughness or chemical resistance.
Polyvinyl Chloride (PVC)
PVC is one of the most versatile plastics in the medical field. It can be formulated into flexible or rigid forms, making it suitable for a wide range of applications. Medical-grade PVC is carefully produced to eliminate harmful additives like phthalates.
Advantages:
- High flexibility and durability.
- Excellent chemical and microbial resistance.
- Transparent, allowing for easy monitoring of fluids.
Disadvantages:
- Concerns over environmental impact during disposal.
- Additives must be carefully managed to ensure safety.
Applications:
- IV bags, blood storage systems, and catheters.
- Tubing for oxygen delivery and dialysis machines.
Other Information:
- PVC’s recyclability is improving with advancements in medical waste management technologies.
Polystyrene (PS)
Polystyrene is a rigid and cost-effective plastic used in disposable medical products. Its ease of molding allows for precise components, but its brittleness limits its use in high-stress applications.
Advantages:
- Affordable and easy to mold.
- Lightweight and rigid.
Disadvantages:
- Low resistance to impact and heat.
- Brittle, making it unsuitable for load-bearing applications.
Applications:
- Petri dishes, culture tubes, and diagnostic trays.
- Disposable labware for single-use scenarios.
Other Information:
- Expanded polystyrene (EPS) is used for packaging sensitive medical instruments.
Polyethylene Terephthalate Glycol (PETG)
PETG is a clear, tough, and sterilizable thermoplastic commonly used in medical device packaging. Its glycol modification improves toughness and clarity, making it suitable for applications requiring both durability and visibility.
Advantages:
- Transparent and impact-resistant.
- Can withstand sterilization processes without yellowing.
Disadvantages:
- Limited heat resistance compared to other high-performance plastics.
Applications:
- Medical packaging, diagnostic components, and fluid containers.
Other Information:
- PETG is gaining popularity in 3D printing for custom medical devices.
Polyurethane (PU)
Polyurethane is known for its elasticity and biocompatibility. It is used in applications requiring flexibility and resistance to wear, such as catheters and wound dressings.
Advantages:
- High elasticity and wear resistance.
- Biocompatible and resistant to body fluids.
Disadvantages:
- Limited resistance to harsh chemicals.
- Can degrade under prolonged UV exposure.
Applications:
- Catheters, surgical dressings, and flexible implants.
Other Information:
- PU foams are used in cushions for medical devices and patient support systems.
Polyetheretherketone (PEEK)
PEEK is a high-performance thermoplastic used in demanding medical applications, particularly implants. It offers exceptional mechanical strength and chemical resistance.
Advantages:
- Superior strength and biocompatibility.
- Can replace metal in certain applications due to its rigidity and lightweight properties.
Disadvantages:
- Expensive and requires specialized equipment for processing.
Applications:
- Orthopedic implants, spinal cages, and dental components.
Other Information:
- PEEK is increasingly used in 3D-printed implants for custom patient solutions.
Each type of plastic used in medical injection molding brings unique properties to the table, making them indispensable for crafting high-quality plastic medical parts. From disposable labware to life-saving implants, these materials continue to drive advancements in healthcare technology.
Production Process of Plastic Medical Parts: From Design to Molding
The production of plastic medical parts involves a series of meticulously planned steps to ensure the final product meets stringent medical standards. Each phase, from design to production molding, plays a critical role. Below is a comprehensive breakdown of the process, including key considerations for each step:
Conceptual Design
The process begins with designing the plastic medical part based on its intended application, functionality, and regulatory requirements.
Key Considerations:
- Identify the medical application and requirements, such as biocompatibility and sterilization needs.
- Collaborate with medical professionals to ensure the design meets practical usage standards.
- Use CAD (Computer-Aided Design) software for detailed 3D modeling.
Material Selection
Choosing the right medical-grade plastic is critical to the performance and safety of the product. Common materials include polypropylene, polyethylene, polycarbonate, and PEEK.
Key Considerations:
- Evaluate properties like strength, flexibility, chemical resistance, and sterilization compatibility.
- Ensure the material complies with FDA, USP Class VI, and ISO medical-grade certifications.
- Balance cost-effectiveness with performance requirements.
Prototyping
Prototypes are created to test the design and functionality before full-scale production. Technologies like 3D printing or CNC machining are often used at this stage.
Key Considerations:
- Test prototypes for fit, function, and durability under medical conditions.
- Modify designs based on feedback from medical professionals and usability tests.
- Ensure prototypes meet regulatory standards for safety and effectiveness.
Tooling and Mold Creation
High-precision molds are developed for injection molding, ensuring accurate and consistent production.
Key Considerations:
- Use durable mold materials such as steel or aluminum for long-lasting performance.
- Optimize mold design for smooth material flow, reducing defects like warping or voids.
- Test molds with sample runs to ensure accuracy and efficiency.
Injection Molding
The selected plastic is melted and injected into the mold under high pressure, then cooled and solidified to form the medical part.
Key Considerations:
- Monitor temperature, pressure, and cooling time to avoid defects.
- Ensure cleanroom manufacturing to maintain sterility.
- Inspect parts for dimensional accuracy and surface quality.
Post-Processing and Finishing
After molding, parts undergo post-processing steps like trimming, polishing, or assembly.
Key Considerations:
- Remove excess material (flash) to ensure a smooth finish.
- Sterilize parts using methods such as autoclaving, gamma radiation, or ethylene oxide gas.
- Conduct additional quality control checks to ensure consistency.
Quality Control and Testing
Thorough testing is conducted to ensure the parts meet regulatory and performance standards.
Key Considerations:
- Perform physical, chemical, and mechanical tests for durability and compliance.
- Validate parts under real-world medical conditions.
- Document test results for regulatory approval and batch traceability.
Packaging and Sterilization
Plastic medical parts are packaged in sterile conditions to ensure safety during transport and use.
Key Considerations:
- Use medical-grade packaging materials that maintain sterility.
- Label packages with clear product information and lot numbers for traceability.
- Conduct final checks to confirm packaging integrity.
The production process of plastic medical parts is a highly detailed workflow that emphasizes precision, quality, and compliance. By carefully addressing each step, manufacturers ensure that these components meet the rigorous demands of modern healthcare.
Molding Technologies for Plastic Medical Parts
The molding process of plastic medical parts employs advanced production technologies to achieve the precision, consistency, and quality required in the medical field.
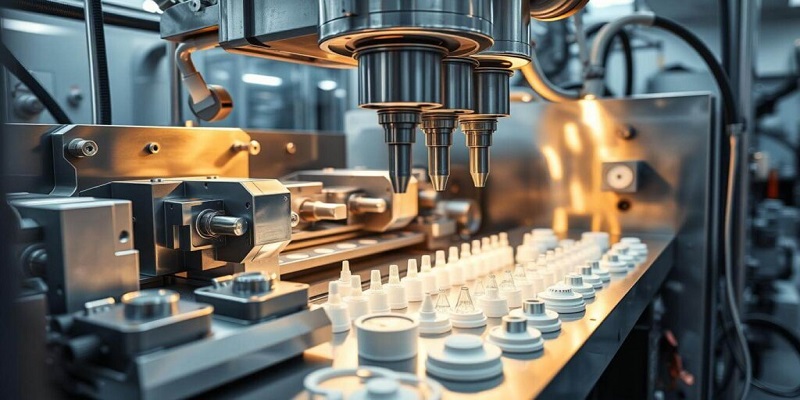
Below are the primary technologies used, with detailed descriptions of their specific applications and advantages:
Injection Molding
Injection molding is the most widely used technology for producing plastic medical parts. This process involves melting plastic pellets and injecting the molten material into a mold under high pressure. Once cooled, the mold is opened, and the part is ejected.
Applications:
- High-volume production of syringes, IV components, and diagnostic tools.
- Manufacturing of precise, complex parts with tight tolerances.
Advantages:
- High efficiency and scalability for mass production.
- Consistent quality with minimal material waste.
Technological Features:
- Multi-cavity molds enable the production of multiple parts simultaneously.
- Advanced servo-hydraulic systems optimize energy efficiency.
Blow Molding
Blow molding is used to create hollow plastic medical parts, such as containers and bottles, by inflating molten plastic inside a mold.
Applications:
- IV solution bags, fluid containers, and medical packaging.
Advantages:
- Ideal for hollow structures with uniform wall thickness.
- Cost-effective for medium to high production runs.
Technological Features:
- Extrusion blow molding for seamless parts.
- Injection blow molding for precise neck finishes.
Thermoforming
Thermoforming involves heating a plastic sheet and shaping it over a mold using vacuum or pressure. It is commonly used for producing large, thin-walled components.
Applications:
- Disposable trays, sterile packaging, and medical device housings.
Advantages:
- Quick setup and lower tooling costs compared to injection molding.
- Suitable for low to medium production volumes.
Technological Features:
- Vacuum thermoforming for simple shapes.
- Pressure thermoforming for intricate designs.
Compression Molding
Compression molding is a process where heated plastic material is placed into a mold cavity and compressed to form the desired shape. It is used for parts requiring high strength.
Applications:
- Orthopedic braces, prosthetics, and dental components.
Advantages:
- Produces parts with excellent strength and durability.
- Minimal material wastage.
Technological Features:
- Automated press systems for precision and repeatability.
- Multi-layer molding for enhanced mechanical properties.
Extrusion Molding
Extrusion molding involves forcing molten plastic through a die to produce continuous profiles, which are then cut to the desired length.
Applications:
- Tubing for catheters, IV lines, and oxygen delivery systems.
Advantages:
- High-speed production for continuous products.
- Excellent for consistent wall thickness.
Technological Features:
- Multi-lumen extrusion for complex tubing designs.
- Co-extrusion for combining multiple materials in a single product.
3D Printing (Additive Manufacturing)
3D printing is a rapidly growing technology for producing custom and complex plastic medical parts. It builds parts layer by layer using materials like medical-grade polymers.
Applications:
- Prototyping, custom implants, and small-batch production.
Advantages:
- High design flexibility and fast turnaround for unique designs.
- Reduces waste by using only the required material.
Technological Features:
- Stereolithography (SLA) for high-resolution parts.
- Fused Deposition Modeling (FDM) for cost-effective prototyping.
Rotational Molding
Rotational molding uses heat and rotation to evenly distribute molten plastic inside a mold, creating hollow or seamless parts.
Applications:
- Large, durable parts like tanks and specialized medical equipment casings.
Advantages:
- Uniform thickness and minimal stress in parts.
- Cost-effective for low to medium production volumes.
Technological Features:
- Multi-axis rotational systems for complex geometries.
- Ability to produce seamless parts without joints.
The production of plastic medical parts leverages diverse molding technologies, each tailored to specific applications and design requirements. From high-volume injection molding to innovative 3D printing, these methods ensure that medical-grade plastics meet the precise demands of modern healthcare.
How to Judge the Quality of Plastic Medical Parts Provided by Manufacturers
Evaluating the quality of plastic medical parts is essential to ensure their safety, reliability, and compliance with medical standards. Manufacturers are expected to meet specific criteria and standards to produce high-quality parts suitable for medical applications. Below are the key standards and factors to consider when judging the quality of plastic medical parts:
Compliance with Regulatory Standards
High-quality plastic medical parts must adhere to internationally recognized regulatory standards, ensuring safety and effectiveness.
Key Standards:
- FDA Approval (21 CFR): Ensures biocompatibility and suitability for medical use.
- ISO 13485: Certification for the design and manufacturing of medical devices.
- USP Class VI Compliance: Verifies that materials are non-toxic, non-irritant, and biocompatible.
How to Judge:
- Verify certifications and documentation from the manufacturer.
- Request testing reports to confirm compliance with required standards.
Material Quality and Specifications
The raw materials used in plastic medical parts play a significant role in their performance and reliability.
Criteria:
- Use of medical-grade plastics like polycarbonate, polypropylene, or PEEK.
- Resistance to sterilization processes (autoclaving, gamma radiation, etc.).
- Biocompatibility to prevent adverse reactions when in contact with human tissues.
How to Judge:
- Inspect material certifications provided by the manufacturer.
- Conduct independent lab tests for material verification if necessary.
Dimensional Accuracy and Consistency
Precision is critical for medical parts to fit and function as intended in medical devices or procedures.
Criteria:
- Tight tolerances for dimensions and uniformity in production.
- Smooth surface finishes to avoid irritation or contamination risks.
How to Judge:
- Use measuring tools like calipers or coordinate measuring machines (CMM) for accuracy.
- Examine parts under magnification for surface defects or inconsistencies.
Mechanical and Physical Performance
Plastic medical parts must withstand the stresses of their intended applications, such as repeated use or exposure to chemicals.
Criteria:
- Strength and durability to resist breakage during use.
- Flexibility and elasticity for components like tubing or catheters.
- Chemical resistance to avoid degradation from body fluids or cleaning agents.
How to Judge:
- Perform mechanical testing, such as tensile, compression, and impact tests.
- Evaluate chemical resistance through exposure tests with common sterilization chemicals.
Sterility and Cleanroom Manufacturing
The manufacturing environment significantly impacts the quality of plastic medical parts.
Criteria:
- Production in ISO Class 7 or higher cleanrooms to prevent contamination.
- Sterile packaging that ensures safety during transport and storage.
How to Judge:
- Verify cleanroom certification of the manufacturer.
- Request sterility validation reports and packaging integrity tests.
Traceability and Batch Control
Traceability ensures that each part can be tracked back to its production batch, which is critical for identifying issues in case of defects.
Criteria:
- Unique batch numbers and clear labeling.
- Documentation of manufacturing processes and materials used.
How to Judge:
- Inspect batch records and traceability reports.
- Confirm that the manufacturer maintains thorough documentation for audits.
Functional Testing and Simulation
The performance of plastic medical parts in real-world conditions is a vital indicator of quality.
Criteria:
- Functional testing under simulated conditions, such as temperature and pressure variations.
- Validation of part performance within medical devices.
How to Judge:
- Request detailed reports on functional testing.
- Conduct in-house testing for critical components, if feasible.
The quality of plastic medical parts can be judged by ensuring compliance with regulatory standards, assessing material and mechanical properties, and verifying manufacturing processes. Collaborating with reliable manufacturers who provide thorough documentation and testing reports ensures that medical-grade plastic parts meet the highest quality standards.
FAQs about Plastic Medical Parts
Plastic is a widely used material in the medical industry, with numerous products made from various types of plastic polymers. These include disposable items such as syringes, IV bags, and gloves, as well as more complex components like surgical instruments, medical tubing, and implantable devices. Commonly used plastics in the medical field include polyethylene (PE), polypropylene (PP), polycarbonate (PC), and polyetheretherketone (PEEK). Medical plastics are essential in the creation of items like catheters, respiratory masks, drug delivery systems, hearing aids, and even joint replacement components. Their versatility, durability, biocompatibility, and ability to withstand sterilization processes make them ideal for use in healthcare products. In fact, the use of medical-grade plastics has revolutionized the healthcare industry, replacing traditional materials like metal and glass in many applications.
Medical-grade plastic is a type of plastic specifically designed to meet the stringent requirements of the healthcare industry. It is typically referred to as “medical-grade polymers” or “biocompatible plastics.” These plastics are engineered to ensure that they do not adversely affect human health when used in medical applications. The most common medical-grade plastics include polyethylene (PE), polypropylene (PP), polycarbonate (PC), polyetheretherketone (PEEK), and polysulfone (PSU). These materials must meet specific standards for purity, strength, and biocompatibility. Medical-grade plastic is manufactured to comply with regulations such as ISO 10993 and USP Class VI, which govern the safety of materials that come into contact with the human body. These regulations ensure that the plastic materials used in medical devices do not cause toxic reactions or harm to patients when they are implanted or used in medical treatments.
Medical-grade polymers are specifically designed to be safe and non-toxic when used in healthcare products. These polymers are thoroughly tested to meet biocompatibility standards, ensuring they do not cause harmful reactions in the human body. In fact, one of the most critical factors in choosing the right material for medical devices is ensuring its non-toxicity. Polymers such as polyethylene (PE), polypropylene (PP), and polyetheretherketone (PEEK) are commonly used in medical applications because they are chemically inert and biocompatible. These materials do not leach harmful substances into the body and are designed to perform safely in long-term medical applications. Manufacturers follow strict regulatory guidelines, including testing for cytotoxicity, irritation, and sensitization, to guarantee that medical-grade plastics are non-toxic and safe for use in medical devices.
There is no single “best” medical-grade plastic, as the ideal material depends on the specific requirements of the application. Different medical products have varying needs in terms of flexibility, strength, durability, biocompatibility, and resistance to sterilization. Some of the most widely used medical-grade plastics include:
Polyethylene (PE): Known for its chemical resistance and biocompatibility, polyethylene is commonly used in medical packaging, syringes, and implantable devices.
Polypropylene (PP): This cost-effective material is resistant to high temperatures and sterilization, making it ideal for medical disposables and containers.
Polyetheretherketone (PEEK): This high-performance plastic is used for implants and prosthetics due to its strength, chemical resistance, and ability to withstand high temperatures.
Polycarbonate (PC): Known for its optical clarity, polycarbonate is often used in diagnostic devices, surgical instruments, and housings that require transparency.
Silicone: Silicone is ideal for medical devices that require flexibility, such as seals, tubing, and wearables. It is also biocompatible and resistant to temperature extremes.
Each of these materials has its unique properties, and selecting the best plastic for a given medical product depends on factors such as durability, ease of sterilization, and biocompatibility. Manufacturers work closely with healthcare providers to choose the right plastic based on the specific needs of each device.
Plastics used in medical devices must meet stringent material requirements to ensure safety, functionality, and durability. The four primary requirements include:
Biocompatibility: The plastic must not cause adverse reactions when in contact with tissues or fluids, ensuring it is safe for use in or on the body.
Sterilizability: Medical plastics should withstand various sterilization methods, such as autoclaving, ethylene oxide gas, or gamma radiation, without degrading.
Durability: Medical-grade plastics must resist wear, chemical exposure, and environmental stress to perform reliably under demanding conditions.
Regulatory Compliance: Plastics must meet regulatory standards such as FDA approval or ISO certifications to ensure they are safe and effective for medical use.
These requirements make materials like polypropylene, polyethylene, and PVC ideal for various medical applications, from surgical instruments to implants and tubing.
Polyethylene (PE) is generally considered safe and non-carcinogenic. It is widely used in medical and food-grade applications due to its chemical inertness and resistance to leaching. The safety of polyethylene arises from its stable polymer structure, which does not break down into harmful substances under normal conditions.
However, safety concerns might arise during manufacturing, where additives or processing chemicals could pose risks if not properly controlled. Additionally, degraded polyethylene at very high temperatures can release harmful byproducts, though this is unlikely in medical applications.
In the context of plastic medical parts, polyethylene is commonly used for applications like prosthetics and packaging. Its biocompatibility, low toxicity, and inert nature make it suitable for medical devices, ensuring it does not pose carcinogenic risks when used appropriately.
Medical-grade PVC (Polyvinyl Chloride) is considered safe when properly formulated and used in medical applications. It is a versatile plastic commonly used for blood bags, IV tubing, and surgical gloves due to its flexibility, transparency, and durability.
The safety of PVC depends on the absence of harmful additives, such as phthalates used as plasticizers. Modern medical-grade PVC often uses alternative plasticizers that meet strict safety standards, ensuring no harmful substances leach into the body or fluids.
Regulatory agencies like the FDA monitor the use of PVC in medical devices to ensure compliance with biocompatibility and safety requirements. When designed and manufactured according to these standards, medical-grade PVC is a reliable and safe material for plastic medical parts.
Polymer plastics vary in safety depending on their chemical composition and intended application. In medical applications, polymers like polypropylene, polyethylene, and medical-grade PVC are rigorously tested for safety. Their biocompatibility, non-toxicity, and resistance to chemical degradation make them suitable for plastic medical parts.
Some concerns exist around certain polymers when additives or manufacturing byproducts pose risks. However, medical-grade plastics undergo extensive testing to ensure compliance with regulatory standards, such as FDA or ISO certifications, which confirm their safety for human contact.
In general, polymers used in medical devices are designed to be inert and free from harmful substances, making them safe for applications such as implants, tubing, and packaging. Their lightweight, durable, and cost-effective properties further enhance their suitability in healthcare.
Medical-grade plastics are made from specially formulated polymers designed to meet healthcare standards. Common materials include:
Polyethylene (PE): Used for prosthetics and packaging due to its inertness and flexibility.
Polypropylene (PP): Known for its durability and sterilizability, ideal for syringes and containers.
Polycarbonate (PC): A strong and transparent material used for surgical instruments and housings.
Polyvinyl Chloride (PVC): Flexible and durable, used for blood bags and IV tubing.
Thermoplastic Polyurethane (TPU): Elastic and biocompatible, used for catheters and surgical dressings.
These plastics are selected for their biocompatibility, resistance to sterilization processes, and compliance with medical regulatory standards. Additives, such as stabilizers and plasticizers, are carefully chosen to enhance properties without compromising safety.
The safety of plastic grades depends on their intended use and compliance with regulatory standards. Medical-grade plastics are among the safest, as they are specifically designed for healthcare applications. These materials undergo rigorous testing for biocompatibility, sterilization resistance, and durability.
Examples of safe medical-grade plastics include:
Polyethylene (PE): Non-toxic and widely used in packaging and prosthetics.
Polypropylene (PP): Durable and resistant to heat and chemicals, ideal for syringes and containers.
Medical-Grade PVC: Flexible and transparent, used in IV bags and tubing.
Polycarbonate (PC): Strong and impact-resistant, suitable for surgical instruments.
Always look for certifications like FDA approval or ISO compliance when evaluating the safety of plastic materials for medical or other sensitive applications.
Contact our professional team now for a same-day quote and risk-free project evaluation. Benefit from ISO 8 cleanrooms, advanced machines, and 12-hour fast response in medical injection molding.