Plastic medical parts machining plays a crucial role in the healthcare industry by providing high-precision components for a wide range of medical devices. With the growing demand for medical applications, the need for durable, reliable, and biocompatible materials is paramount. Precision machining ensures that plastic parts meet strict requirements for functionality, safety, and performance. High-performance plastics, such as PEEK, PP, and PTFE, are often used for their exceptional resistance to heat, chemicals, and wear. Common machining medical parts processes for plastic parts include CNC milling, CNC turning, and medical injection molding, which offer accuracy and repeatability to meet the strict standards of medical device manufacturing. FUJIU Medical Injection Mold specializes in plastic medical parts machining, offering precision CNC services for durable, custom medical components.
Benefits of Using Plastic in Plastic Medical Parts Machining
Using plastics in medical devices offers several key advantages that contribute to their widespread use in the healthcare industry.
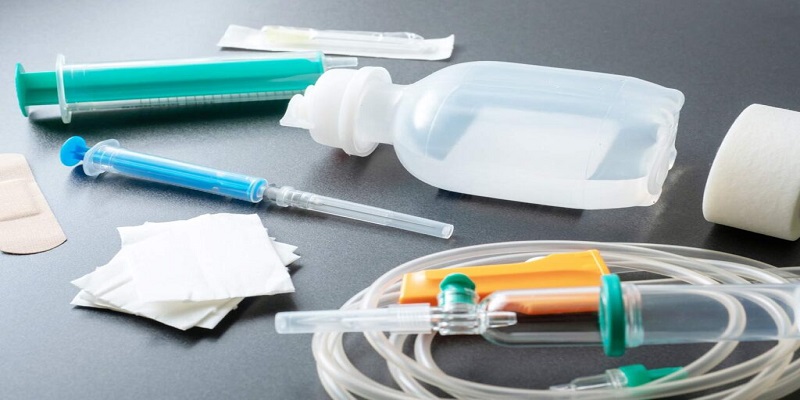
Below are the primary benefits:
Lightweight and Durable Properties
Plastic materials are inherently lightweight yet durable, making them ideal for medical devices that need to be easily handled while maintaining strength. Plastic medical parts machining ensures that these components retain their structural integrity over time without adding unnecessary weight to medical devices.
Cost-effective Compared to Metals
Plastic materials are typically more affordable than metals, making them a cost-effective choice for manufacturing medical devices. Plastic machined medical components can be produced at a lower cost while still meeting stringent quality standards.
Versatility for Complex Shapes and Intricate Designs
Plastics can be easily molded into intricate shapes, allowing for the creation of complex designs that may be difficult to achieve with metals. Plastic medical parts machining enables manufacturers to produce components with precise dimensions and complex geometries required for modern medical applications.
Resistance to Corrosion and Sterilization Methods
Plastic materials, such as PEEK and PTFE, offer excellent resistance to corrosion and can withstand various sterilization methods. This makes them suitable for use in medical devices that require frequent cleaning and sterilization, ensuring longevity and reliability.
Biocompatibility for Medical Applications
Plastics used in medical devices must be biocompatible, meaning they can interact safely with the human body. Plastic machined medical components are designed to meet biocompatibility standards, ensuring that they do not cause adverse reactions when used in medical environments.
Common Plastic Materials Used in Plastic Medical Parts Machining
In plastic medical parts machining, various plastic materials are used to create high-performance, reliable medical components. These materials are chosen based on their unique properties, ensuring they meet the rigorous demands of the medical industry. Additionally, precision mold medical processes are employed to ensure the accuracy and quality of the machined parts, enhancing their functionality and durability in medical applications. Below are some of the most common plastic materials used in medical parts machining:
PEEK (Polyetheretherketone)
PEEK is a high-performance thermoplastic with excellent high-temperature resistance, making it ideal for sterilizable parts such as surgical instruments and implantable devices. It can withstand extreme conditions without degrading, ensuring durability and reliability in medical applications. Plastic medical parts machining processes are highly effective with PEEK, allowing for the production of precise and robust components.
PP (Polypropylene)
PP is a versatile, chemically resistant material widely used in medical devices like syringes, IV bags, and medical containers. Its durability and resistance to a range of chemicals make it a popular choice for disposable medical items. The ease of machining PP ensures consistent quality in mass production for medical applications.
Delrin (Acetal)
Delrin, or acetal, is known for its excellent precision machining capabilities, which makes it perfect for producing high-precision, wear-resistant parts. It is commonly used for gears, medical connectors, and other components that require strong mechanical properties and dimensional stability.
PTFE (Teflon)
PTFE is a non-stick, chemically resistant plastic that is widely used for seals, gaskets, and other components that come into contact with fluids or chemicals in medical devices. Its unique properties make it ideal for maintaining cleanliness and preventing contamination in sensitive medical environments.
Polycarbonate (PC)
Polycarbonate is a highly impact-resistant plastic that is commonly used in the production of medical device housings and protective covers. Its transparency and strength make it ideal for devices where visibility and durability are key factors.
Ultem (PEI)
Ultem, or Polyetherimide (PEI), is known for its high strength and thermal stability, making it ideal for sterilizable medical equipment. It can withstand high temperatures and harsh sterilization processes without compromising its mechanical properties, making it a critical material in medical device plastic manufacturing.
Nylon (PA)
Nylon is a strong, flexible plastic used in medical device components like catheters, surgical tools, and other parts that require both flexibility and strength. Its durability and resistance to wear and tear make it ideal for high-performance medical applications.
CNC Machining Plastic Parts for Medical
CNC machining plastic parts for medical equipment provides an efficient way to produce high-precision, high quality medical plastic parts for the healthcare industry. CNC plastic parts for medical equipment can be custom-machined to meet the exact specifications of a particular device, ensuring optimal performance and safety. The precise control offered by CNC machining allows for the creation of intricate, complex designs that are essential for modern medical applications.
Plastic Medical Parts Machining in Various Medical Fields
Plastic medical parts machining plays a crucial role in the healthcare industry by providing high-precision components used in a variety of medical devices and instruments. These components are essential for the functionality and safety of medical equipment, and their manufacturing requires advanced techniques such as CNC machining. This machining process is particularly valuable in areas that demand high precision, reliability, and durability, ensuring that the medical devices function correctly and meet stringent regulatory standards. Below, we explore the main medical fields where plastic medical parts machining is used.
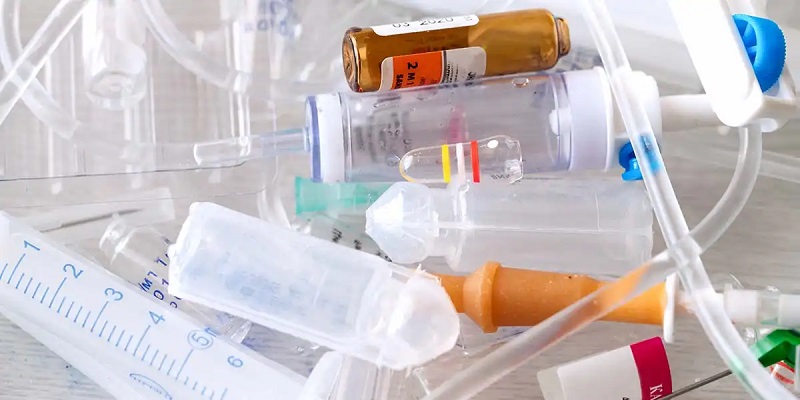
Orthopedic Devices
Orthopedic devices, which help to support, align, or correct musculoskeletal deformities, often rely on precision-machined plastic parts. These components are critical for the performance of devices like prosthetics, orthotic braces, joint implants, and spinal fusion systems. The materials used in these parts must be strong, lightweight, and biocompatible to ensure that they can withstand wear and tear while remaining safe for long-term use in the human body.
Plastic parts machining is used to create custom components such as socket liners, implantable devices, and spinal surgery tools, with high tolerance levels ensuring proper fitting and functionality.
Diagnostic Equipment
Diagnostic equipment, such as ultrasound machines, MRI machines, and X-ray systems, requires complex plastic components that house and protect sensitive electronic equipment. Plastic medical parts machining ensures that these components are manufactured to precise specifications, enabling diagnostic tools to provide accurate results.
For example, plastic enclosures, connectors, and housings used in these diagnostic machines must be durable, resistant to wear, and able to protect the internal components from environmental factors. CNC machining allows for the creation of intricate designs and precise tolerances that are essential for the proper functioning of these diagnostic instruments.
Surgical Instruments
Surgical instruments, ranging from scalpels to forceps, often include components made from high-performance plastics. These plastics must be tough enough to handle repeated sterilization cycles, resistant to chemicals, and lightweight for easy handling during surgery. Plastic parts machining enables the production of ergonomic, sterile, and reliable surgical instruments with complex geometries that ensure the safety and efficiency of medical procedures.
CNC machining is used to create parts such as handles, grips, and surgical tips, which must be designed with precision to ensure ease of use and accurate performance during operations.
Infusion and Injection Systems
In fields such as anesthesia, diabetes care, and intravenous therapy, infusion and injection systems are essential for delivering fluids, medications, and nutrients to patients. These systems rely on plastic components, including needles, syringes, and infusion pumps, that are precisely machined to ensure accurate and safe delivery.
Plastic medical parts machining is used to produce parts with exact tolerances, such as the fluid path components in pumps or the needle tips for syringes, which must be sharp and free from defects. These components also need to meet high cleanliness and sterilization standards to prevent contamination.
Dental Instruments and Implants
The dental field also extensively uses plastic medical parts machining for creating instruments, tools, and implants. From orthodontic braces to dental drills and crowns, plastic components are crucial for the comfort and functionality of dental treatments. Dental implants often require custom plastic parts, such as abutments, which need to be machined with precise dimensions to ensure proper fitting and long-term durability.
Machining techniques ensure that dental instruments are both ergonomic and efficient, while dental implants are manufactured to match the specific needs of each patient.
Laboratory and Testing Equipment
Laboratory equipment used for testing and analysis often contains plastic components that need to be precisely manufactured. For example, pipettes, test tube racks, centrifuge parts, and laboratory automation systems all require plastic parts that are lightweight, chemically resistant, and easy to sterilize.
Plastic medical parts machining is crucial for the production of custom components used in laboratory equipment, enabling laboratories to carry out tests with high accuracy and reproducibility.
Plastic medical parts machining is integral to various medical fields, providing high-precision, custom parts that ensure the functionality, safety, and reliability of medical devices. Whether in orthopedic devices, diagnostic equipment, surgical instruments, infusion systems, dental implants, or laboratory tools, plastic machining meets the stringent demands of the healthcare industry. With its ability to produce durable and biocompatible components, plastic medical parts machining plays a vital role in enhancing the quality of healthcare delivery.
CNC Machining Processes for Plastic Medical Parts Machining
Plastic medical parts machining involves several advanced CNC machining processes to produce high-precision components for the healthcare industry. These processes allow for the manufacturing of complex, durable, and reliable medical parts that meet strict regulatory and performance standards. Below are the key CNC machining processes used for plastic medical parts:
CNC Milling
CNC milling is an essential process in plastic medical parts machining, ideal for creating detailed and complex geometries in medical device components. This process is particularly useful for manufacturing housings, surgical tools, and prototypes that require high precision. CNC milling allows for multi-axis movement, making it possible to shape intricate features and fine details essential in medical devices.
CNC Turning
CNC turning is used for producing cylindrical plastic medical parts such as implants, tubes, and shafts. This process involves rotating the workpiece while a cutting tool shapes the material. It is effective for creating parts with consistent diameters and lengths, making it a reliable method for producing high-quality cylindrical components for medical applications.
CNC Swiss Machining
CNC Swiss machining is a precision turning process that is ideal for producing small, intricate parts, such as connectors and fittings commonly found in medical devices. This process offers exceptional accuracy and can handle delicate parts with tight tolerances. It is particularly useful in the production of small components that require fine detailing and high consistency in plastic medical parts machining.
5-Axis Machining
5-axis machining allows for the production of complex, multi-faceted plastic medical parts with tight tolerances, making it an essential process in the medical device industry. This advanced technique enables the simultaneous movement of the tool along five different axes, which is ideal for creating intricate, highly detailed medical components that require precision from all angles. It is particularly useful for manufacturing medical devices with complex geometries or challenging designs.
Importance of Precision and Tolerances in Plastic Medical Parts Machining
In plastic medical parts machining, precision and tight tolerances are paramount to ensure that medical devices perform effectively, safely, and reliably. The critical nature of these requirements stems from the fact that even the slightest deviation from specifications can compromise the functionality of the medical device, potentially putting patients’ health at risk. Here’s why precision and tolerances play such a significant role:
Ensuring Functionality and Safety
Medical devices, particularly those used in critical procedures or implanted in the human body, require high precision medical components to ensure their correct operation. For example, parts such as surgical instruments, implants, and catheters must be manufactured within exact tolerances to guarantee they fit and function as intended. Even minor inaccuracies in measurements can result in malfunctions, reduced device effectiveness, or even harm to the patient.
Meeting Industry Standards
The healthcare industry maintains strict standards to ensure that medical parts meet the necessary quality and safety requirements. One of the key certifications is ISO 13485:2016, which sets the international standard for quality management systems in the production of medical devices. For manufacturers involved in plastic medical parts machining, achieving ISO 13485 certification demonstrates that their processes meet stringent quality controls and are capable of producing parts that comply with regulatory guidelines.
CNC Router Machine Plastic Parts for Medical
An important tool in achieving high precision in plastic medical parts machining is the CNC router machine. This advanced equipment can manufacture intricate, complex parts for medical devices with exceptional accuracy. CNC router machines are particularly beneficial in the production of large medical components or parts that require high consistency. With the ability to handle tight tolerances, CNC routers play a vital role in ensuring that plastic medical parts meet the necessary specifications for safety and performance.
Precision and tolerances are non-negotiable in the medical device industry. Achieving the highest standards in plastic medical parts machining ensures that medical devices are functional, safe, and compliant with industry regulations, ultimately safeguarding patient health.
Why CNC Machining is Chosen for Plastic Medical Parts Machining
Plastic medical parts machining requires the use of advanced manufacturing techniques to create high-quality, precise, and durable components. Among the various methods available, CNC machining stands out as the ideal choice for producing medical device components and instruments. The benefits of CNC machining, such as speed, precision, and flexibility, make it the go-to process for producing custom plastic parts for the medical industry. Below, we explore why CNC machining is preferred for plastic medical parts machining.
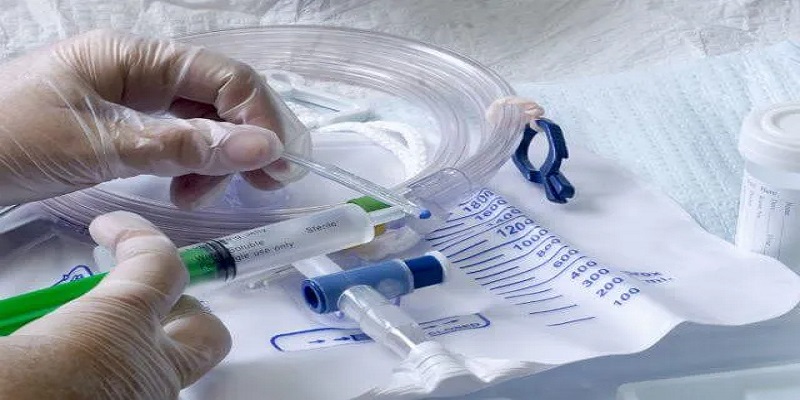
Speed and Efficiency in Production
One of the primary reasons CNC machining is chosen for plastic medical parts machining is its speed. The medical industry demands quick turnaround times for component production, especially in critical applications such as surgical instruments, diagnostic devices, and prosthetics. CNC machining significantly reduces production time compared to traditional methods, making it ideal for creating components in a short period.
For example, depending on the complexity of the part, CNC machines can produce a finished medical component in just a few hours. This rapid production capability is especially beneficial in medical device prototyping and low-volume production, where fast iterations and quick access to parts are crucial for meeting market demands or regulatory deadlines.
Unmatched Precision for Medical Components
Medical devices and instruments require extremely tight tolerances to ensure functionality, safety, and patient outcomes. CNC machining is known for its ability to achieve the high levels of precision needed for medical components. The tight tolerances that CNC machines can maintain are essential in fields such as orthopedics, dental implants, and diagnostic equipment, where even minor variations can affect the performance of the device or procedure.
CNC machines can produce parts with an accuracy of up to 0.0001 inches, making them ideal for complex and precision medical devices. Whether manufacturing small components like surgical tool handles or large parts like implantable devices, the ability to achieve such high precision ensures that plastic medical parts are perfectly tailored to meet the strict requirements of the healthcare industry.
Flexibility to Handle Complex Designs and Materials
Another key advantage of CNC machining is its flexibility. Medical devices often require components with intricate designs and complex geometries. CNC machining allows for the production of custom parts with various shapes, sizes, and features, providing the flexibility to meet the diverse needs of the medical industry.
Moreover, CNC machines can handle a wide variety of materials, including medical-grade plastics that are commonly used in medical device production. These materials must meet stringent standards for biocompatibility, strength, and durability, and CNC machining can accommodate different material types, ensuring that parts are made to the specific requirements of each device. Additionally, double injection plastics for medical parts wholesale offer the ability to combine multiple materials in a single part, enhancing both functionality and durability.
For instance, parts like infusion pump housings, dental implants, or surgical instrument grips can be produced with precise features, such as threads, slots, and holes, in a range of materials such as ABS, polycarbonate, or PEEK. The versatility of CNC machining allows manufacturers to adapt to new material advancements and ensure that their medical parts meet evolving industry standards.
Customization for Medical Device Prototyping
Customization is another key benefit of CNC machining in plastic medical parts machining. Medical devices often require prototypes for testing and evaluation before mass production, and CNC machining allows for the rapid production of customized parts. This capability is particularly important for testing new designs or developing personalized medical devices tailored to individual patients.
CNC machines can produce prototypes with the same precision as final production parts, enabling manufacturers to perform tests and make adjustments based on real-world performance. This reduces the time and cost associated with design iterations and ensures that the final product is optimized for its intended use.
CNC machining is the preferred process for plastic medical parts machining due to its speed, precision, flexibility, and ability to handle complex designs and materials. These benefits make CNC machining an ideal choice for producing high-quality, custom medical device components. Whether for rapid prototyping, low-volume production, or high-precision parts, CNC machining ensures that plastic medical parts meet the stringent standards required in the healthcare industry.
Industry Standards and Regulations for Plastic Medical Parts Machining
Plastic medical parts machining involves manufacturing highly precise and durable components for medical devices, which are subject to stringent industry standards and regulations. These standards ensure that the manufactured parts meet safety, quality, and performance requirements for use in healthcare applications. Following these standards is critical to ensuring that medical devices are safe for patient use and comply with regulatory requirements for both domestic and international markets. Below, we discuss the key industry standards and regulations that should be followed during the entire plastic medical parts machining process.
ISO 13485: Medical Device Quality Management System
ISO 13485 is an international standard that specifies the requirements for a comprehensive quality management system (QMS) for the design and manufacture of medical devices. It applies to manufacturers of medical devices, including those involved in the machining of plastic parts for medical applications.
This standard ensures that manufacturers consistently produce medical components that meet both customer and regulatory requirements. For plastic medical parts machining, ISO 13485 sets guidelines for maintaining effective processes, traceability, documentation, and control over product design and production. Adhering to ISO 13485 helps mitigate risks, improve product quality, and ensure compliance with regulatory requirements for medical devices.
FDA 21 CFR Part 820: Good Manufacturing Practices (GMP)
In the United States, the Food and Drug Administration (FDA) enforces regulations under 21 CFR Part 820, which covers Good Manufacturing Practices (GMP) for medical devices. These regulations establish requirements for the design, production, and maintenance of medical devices, ensuring that all medical products, including plastic parts, are safe and effective.
Plastic medical parts machining must comply with FDA’s GMP guidelines, which include provisions for quality control, risk management, validation, and documentation. This ensures that medical components are produced under controlled conditions, meet specified performance standards, and can be tracked throughout their lifecycle. GMP also ensures that manufacturers have robust systems in place to detect and address any potential issues during the machining and production process.
ISO 10993: Biocompatibility Testing
ISO 10993 is a series of international standards that assess the biocompatibility of materials used in medical devices. Since plastic medical parts are often used in direct contact with the human body, ensuring that the materials are biocompatible is essential. This series of standards outlines testing requirements for materials that may come into contact with blood, tissue, or other bodily fluids.
For plastic parts machining, compliance with ISO 10993 ensures that the materials used are safe for patient use. Manufacturers must conduct thorough testing to evaluate the biological effects of plastics, such as cytotoxicity, sensitization, and irritation. These tests are crucial for ensuring that plastic components will not cause adverse reactions when implanted, injected, or used in medical procedures.
Medical Device Directive (MDD) & MDR (EU Regulations)
For medical device manufacturers operating within the European Union, compliance with the Medical Device Directive (MDD) and the newer Medical Device Regulation (MDR) is mandatory. The MDR, which replaced the MDD in 2021, sets out rules for medical devices and in vitro diagnostic devices sold within the EU market.
Plastic medical parts machining must adhere to these regulations, which require manufacturers to demonstrate that their devices meet safety and performance standards before they can be marketed in Europe. The MDR also mandates strict documentation and reporting requirements, including detailed technical files and risk assessments. Manufacturers must conduct clinical evaluations and establish post-market surveillance systems to monitor the performance of their medical devices.
Cleanroom Standards and Contamination Control
During the machining of plastic medical parts, contamination control is paramount, as even minute particles or microbial contamination can compromise the quality and safety of medical devices. Manufacturing processes must take place in cleanroom environments that meet specific cleanliness standards, such as ISO 14644-1, which defines the cleanliness levels of air in controlled environments.
Plastic parts machining for medical applications must be conducted in environments that are free from dust, bacteria, and other contaminants. ISO 14644-1 categorizes cleanrooms into different classes based on particle concentration levels, and manufacturers must adhere to the appropriate class depending on the sensitivity of the device. Contamination control practices are also essential for ensuring that components are free from residues that could affect biocompatibility or performance.
FDA 21 CFR Part 11: Electronic Records and Signatures
For manufacturers in the U.S., FDA 21 CFR Part 11 outlines the criteria for using electronic records and electronic signatures in regulated industries, including medical device manufacturing. This regulation ensures that electronic documentation and signatures are trustworthy, accurate, and reliable for compliance with FDA requirements.
In the context of plastic medical parts machining, manufacturers must ensure that any data related to the production, testing, and quality control of medical components is accurately recorded, stored, and accessible. Compliance with Part 11 guarantees that the electronic documentation used in manufacturing processes is secure, auditable, and legally valid, ensuring transparency and traceability throughout the machining process.
Plastic medical parts machining is subject to a variety of industry standards and regulations that ensure the safety, quality, and performance of medical device components. Compliance with ISO 13485, FDA GMP, ISO 10993 for biocompatibility, EU MDR, cleanroom standards, and FDA 21 CFR Part 11 is critical to producing reliable and safe medical devices. These standards not only protect patients but also help manufacturers meet the stringent requirements necessary to enter and succeed in the global healthcare market. By following these regulations, manufacturers can ensure that their plastic medical parts are of the highest quality and meet all necessary legal and safety standards.
Post-Processing Options for Plastic Medical Parts Machining
After plastic medical parts machining, various post-processing methods are used to improve the safety, performance, and durability of the components. These techniques are essential to ensure that the parts meet the necessary standards for medical applications. Below are some key post-processing options:
Cryogenic Deburring
Cryogenic deburring is a process that uses extremely low temperatures to remove sharp edges, burrs, and other imperfections from plastic parts. This method is particularly important for medical components, where sharp edges can pose a safety risk to both patients and healthcare providers. Cryogenic deburring ensures that parts are smooth, reducing the likelihood of injury during use. Additionally, this process improves the overall functionality of the part by creating a more precise and clean finish.
Annealing
Annealing is a heat treatment process used to relieve internal stresses within plastic parts. When plastic materials are machined, they may experience warping or distortion due to residual stresses from the machining process. Annealing helps to reduce these stresses, resulting in improved strength, dimensional stability, and resistance to cracking. For plastic medical parts machining, annealing enhances the durability and reliability of the components, ensuring they maintain their integrity under use, especially in high-stress environments.
Plating and Coating
Plating and coating are used to add additional properties to plastic medical parts, such as improved biocompatibility, wear resistance, or protection against environmental factors. For example, gold or nickel plating can be applied to certain plastic components to improve their resistance to corrosion and enhance their aesthetic qualities. Coatings such as antibacterial or hydrophobic layers can also be applied to ensure the medical parts are safe and effective in healthcare environments. These post-processing options provide tailored solutions for specific medical applications, ensuring that plastic medical parts machining results in components that meet the necessary safety and functional requirements.
Post-processing techniques like cryogenic deburring, annealing, and plating/coating are crucial for ensuring that plastic medical parts machining produces high-quality, safe, and reliable components for medical use.
FAQs about Plastic Medical Parts Machining
Biocompatibility: The material must be non-toxic and not elicit an adverse response from the body.
Sterilization Compatibility: The plastic must withstand common sterilization methods, such as autoclaving, ethylene oxide gas, and gamma radiation, without degrading or releasing harmful substances.
Mechanical Properties: The plastic must possess the necessary strength, flexibility, and durability for the intended application.
Chemical Resistance: The material must resist degradation when exposed to various chemicals, including body fluids, drugs, and cleaning agents used in medical settings.
The primary machine used for making parts out of plastic is an injection molding machine. This equipment works by heating plastic granules until they are molten and then injecting the molten plastic into a mold cavity. The plastic solidifies in the shape of the mold, creating the desired part. Injection molding is highly efficient for mass production and can produce complex shapes with high precision. Other machines that also make plastic parts include extruders, which are used for continuous profiles like tubing, and blow molding machines, which are used to manufacture hollow containers such as bottles.
Yes, plastic can indeed be CNC machined. CNC (Computer Numerical Control) machining is a subtractive manufacturing process wherein material is removed from a solid block of plastic to create the desired shape. This method is highly precise and can produce complex geometries. Plastic materials such as ABS, polycarbonate, nylon, and PMMA (acrylic) are common choices for CNC machining due to their favorable machinability, strength, and durability. CNC machining is especially beneficial for producing prototypes and low-volume production runs where injection molding may not be cost-effective.
Several types of plastic are highly machinable and suitable for CNC machining or other manual machining techniques. Some of the most machinable plastics include:
Acetal (POM): Known for its high strength, low friction, and excellent dimensional stability, acetal is ideal for precision parts.
Nylon (PA): Offers good mechanical properties, wear resistance, and low friction. It’s commonly used for gears and bearings.
Polycarbonate (PC): This material is valued for its high impact resistance and optical clarity.
Acrylic (PMMA): Known for its clarity and ability to be polished to a high shine, making it suitable for optical applications.
PTFE (Teflon): Offers exceptional chemical resistance and low friction but is softer compared to other plastics, requiring careful handling.
Each of these plastics provides unique properties that make them suitable for specific applications in various industries, including aerospace, automotive, and medical devices.
Contact our professional team now for a same-day quote and risk-free project evaluation. Benefit from ISO 8 cleanrooms, advanced machines, and 12-hour fast response in medical injection molding.