Precision is a cornerstone in the manufacturing of medical devices, as even the slightest deviation can impact safety and performance. Precision machining for medical, including precision mold medical applications, plays a pivotal role in meeting the rigorous standards required by the healthcare industry. From surgical instruments to implantable devices, this technique ensures the reliability and durability of critical components.
But what exactly is precision machining for medical? It refers to a specialized manufacturing process that leverages advanced technologies, such as CNC (Computer Numerical Control), to create intricate, high-tolerance parts. These components often feature complex geometries and must adhere to strict tolerances, making precision machining indispensable for producing cutting-edge medical solutions that improve patient outcomes and uphold safety standards. Precision machining for medical uses CNC technology to produce complex, accurate parts with tight tolerances, ensuring high quality and reliability.
What is Precision Machining for Medical Devices?
Definition of Precision Machining for Medical Devices
Precision machining for medical refers to a highly specialized manufacturing process designed to produce intricate and high-tolerance components used in medical devices. Molding definition medical involves the precise shaping of materials to create parts that adhere to the stringent standards required in the healthcare industry. This method involves removing material from a workpiece with incredible accuracy, ensuring that each part meets exact specifications. Precision machining is particularly vital in healthcare due to the strict safety and performance requirements of medical tools, implants, and instruments.
Necessity for Tight Tolerances in Medical Applications
Medical devices often operate within the human body, where even the slightest dimensional deviation can lead to critical failures. Precision machining for medical ensures the tight tolerances needed to meet these exacting standards. Whether it’s a surgical instrument or a prosthetic implant, the precision required minimizes risks, enhances functionality, and ensures the device’s compatibility with biological systems.
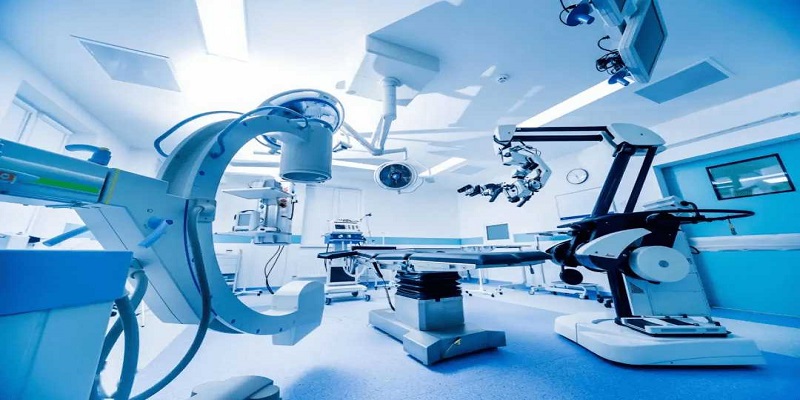
Repeatability and Consistency
One of the standout benefits of precision machining for medical is its ability to deliver consistent results across high-volume production runs. This repeatability is essential for mass-produced medical devices like syringes, implants, and diagnostic tools, where uniformity is critical to performance and safety compliance. Processes like medical injection molding complement precision machining by enabling efficient production of complex components, ensuring both accuracy and scalability in medical manufacturing.
Smooth Finishes and Polishing
Medical devices often require smooth finishes to prevent tissue damage and reduce the risk of contamination. Precision machining for medical employs advanced polishing techniques to achieve ultra-smooth surfaces, which are crucial for surgical tools and implantable devices. These finishes also contribute to improved patient comfort and device longevity.
Role of CAD/CAM Software
The use of CAD (Computer-Aided Design) and CAM (Computer-Aided Manufacturing) software is integral to precision machining for medical. These technologies enable manufacturers to design highly accurate prototypes and translate them seamlessly into production. With CAD/CAM, medical device developers can test and refine their designs virtually, reducing development time and ensuring the final product meets stringent regulatory standards.
Challenges and Limitations
Despite its advantages, precision machining for medical faces challenges such as high initial costs and the need for skilled operators to manage sophisticated equipment. Additionally, maintaining strict quality control throughout the manufacturing process can be time-consuming but is essential to uphold industry certifications and patient safety.
Case Studies in Medical Applications
Examples of precision machining for medical include the production of orthopedic implants, dental components, and surgical instruments. For instance, CNC-machined titanium implants have revolutionized joint replacement surgeries by offering unparalleled strength and biocompatibility. Another example is the creation of micro-scale components for minimally invasive surgical tools, which demand extraordinary accuracy and reliability.
Key Processes in Precision Machining for Medical Applications
Precision machining for medical involves intricate and carefully controlled manufacturing techniques to produce components for healthcare applications. Precision medical machining ensures that every part meets the stringent standards of precision medical device manufacturing, focusing on high accuracy, smooth finishes, and repeatability. Below, we explore the six essential processes involved.
CNC Machining Techniques
CNC Swiss Machining for Ultra-Precise Components
CNC Swiss machining is a critical process in precision machining for medical, ideal for creating ultra-precise components with small diameters. This technique allows for simultaneous operations on multiple axes, reducing cycle time while achieving exceptionally tight tolerances. It’s particularly beneficial for parts like screws, pins, and stents used in precision medical device manufacturing.
CNC Milling and Turning for Complex Shapes
CNC milling and turning are versatile processes that produce complex geometries required in precision medical machining. While milling is used for shaping parts with intricate features, the turning such as turning of medical parts specifically creates cylindrical components with smooth finishes. Both processes are essential for manufacturing surgical instruments, prosthetics, and other precision medical devices, ensuring the required accuracy and functionality in critical applications.
Steps in the Manufacturing Workflow
Design and CAD Modeling
The first step in precision machining for medical is designing the component using CAD software. CAD modeling allows for the visualization and optimization of intricate designs, ensuring they meet the specifications of precision medical device manufacturing. This step minimizes errors and accelerates prototyping.
Material Selection and Preparation
Material selection is critical in precision medical machining, as it impacts biocompatibility, durability, and performance. Common materials include titanium, stainless steel, and medical-grade plastics. These materials are carefully prepared to eliminate impurities, ensuring their suitability for precision medical devices.
Machining, Quality Control, and Post-Processing
The core of the workflow involves machining the part to exact specifications. Advanced equipment ensures precision, while strict quality control processes verify tolerances and compliance with industry standards. Post-processing, such as deburring or heat treatment, is conducted to enhance the part’s performance and longevity.
Additional Services
Surface Finishing, Polishing, and Coating
To ensure durability and sterilization, precision medical machining includes additional services like surface finishing, polishing, and applying specialized coatings. These steps enhance the appearance, functionality, and resistance of precision medical devices to corrosion and wear, making them suitable for surgical and implantable use.
Precision Medical Devices in Focus
Precision medical devices are a category of tools and components created through precision machining for medical. These devices, including implantable prosthetics, surgical instruments, and diagnostic tools, require exceptional accuracy and performance. The role of precision medical machining in manufacturing these devices is pivotal, as it ensures the highest standards of safety and efficacy are consistently met.
Challenges and Innovations in Precision Medical Devices
The production of precision medical devices often involves overcoming challenges like meeting biocompatibility standards and achieving consistent quality at scale. Recent innovations, such as multi-axis CNC machines and advanced materials, have improved the speed and accuracy of manufacturing, ensuring that these devices continue to evolve with medical advancements.
Materials Used in Precision Machining for Medical Devices
Materials play a fundamental role in precision machining for medical, as they directly impact the safety, reliability, and functionality of the finished products. Selecting the right material is crucial in medical precision machining, ensuring compatibility with healthcare environments and compliance with stringent industry standards.
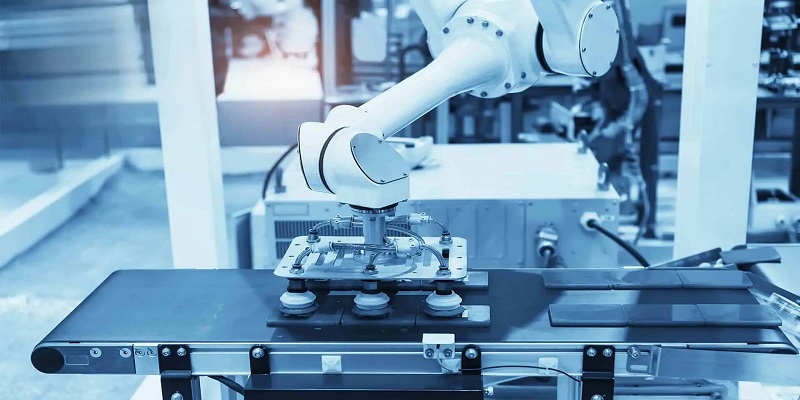
Common Materials in Medical Manufacturing
Stainless Steel
Stainless steel is a staple material in medical precision machining due to its exceptional strength, corrosion resistance, and affordability. It is commonly used in surgical instruments, such as scalpels and clamps, and medical devices like catheters. Stainless steel’s biocompatibility and ability to withstand sterilization make it ideal for precision machining for medical applications.
Aluminum
Aluminum’s lightweight nature and excellent machinability make it an attractive choice for medical devices requiring precision machining. Its application ranges from diagnostic tools to lightweight components for mobility aids. Additionally, aluminum’s non-corrosive properties ensure longevity and reliability in medical environments.
Titanium Alloys
Titanium is a standout material in medical precision machining due to its unparalleled biocompatibility and strength-to-weight ratio. It is a preferred choice for implants such as joint replacements and dental fixtures. Titanium’s resistance to body fluids and exceptional durability make it indispensable in precision machining for medical.
Medical-Grade Plastics
Medical-grade plastics, such as PEEK (polyether ether ketone) and polycarbonate, are widely used in medical precision machining. These materials are non-toxic, lightweight, and easily molded into intricate shapes. Applications include single-use devices, imaging components, and housings for electronic medical equipment.
Gold and Bronze
Gold and bronze are used in specialized medical devices requiring superior electrical conductivity or aesthetic qualities. These materials are often employed in precision machining for medical devices such as high-performance connectors, implants, or prosthetics, adding unique functionality and durability.
Biocompatibility and Durability in Material Selection
The importance of biocompatibility cannot be overstated in precision machining for medical. Materials must be non-toxic and inert to avoid adverse reactions when in contact with the human body. Simultaneously, durability ensures that devices maintain performance over time, even under demanding conditions such as repeated sterilization or mechanical stress.
Stock Availability for Custom and Large-Volume Orders
Medical precision machining often requires flexibility in material sourcing to accommodate both custom prototypes and high-volume production. Suppliers ensure consistent stock availability of certified medical-grade materials, allowing manufacturers to scale production without compromising quality or delivery timelines.
Precision Medical Fittings in Focus
What are Precision Medical Fittings?
Precision medical fittings are components that ensure seamless connections in medical systems, such as IV lines, ventilators, and diagnostic equipment. These fittings are manufactured using medical precision machining techniques to meet strict dimensional accuracy and smoothness standards.
Materials Used in Precision Medical Fittings
Stainless steel and medical-grade plastics dominate the production of precision medical fittings due to their biocompatibility and resistance to wear. For example, PEEK is often used for disposable fittings, while stainless steel is preferred for reusable components requiring high durability.
Advantages of Precision Medical Fittings
The precision achieved in manufacturing these fittings ensures leak-free performance, reliable fluid delivery, and easy assembly. These advantages are critical in life-saving applications where even minor deviations could compromise patient safety.
Research and Innovations in Precision Medical Fittings
Recent innovations in medical precision machining have enabled the integration of antimicrobial coatings into fittings, reducing the risk of infections. Studies have also explored the use of advanced alloys and composites, enhancing the performance and lifespan of these components.
Applications of Precision Machining for Medical Technology
Precision machining for medical plays a transformative role in healthcare by enabling the creation of highly specialized and reliable components. Its applications span a wide range of medical devices and solutions, ensuring that every part meets the rigorous standards required in medical environments. Below, we detail the significant applications and their benefits.
CNC Medical Parts
Orthopedic Implants and Prosthetics
Precision machining for medical is pivotal in manufacturing orthopedic implants and prosthetics. Components like joint replacements, bone screws, and spinal implants require exceptional accuracy and biocompatibility. These parts are tailored to fit individual patients, ensuring comfort, durability, and enhanced mobility. For example, CNC machining ensures smooth finishes and precise dimensions, critical for minimizing tissue irritation.
Surgical Instruments and Diagnostic Equipment
Surgical tools such as scalpels, forceps, and retractors are crafted using precision machining for medical to ensure sharpness, balance, and ergonomic design. Diagnostic equipment like imaging device components also benefits from precision machining, which guarantees consistent performance and reliability in critical healthcare settings.
Medical Pumps and Device Enclosures
Precision machining for medical is essential in producing components for medical pumps and enclosures for sensitive devices. Pumps used in infusion systems or dialysis machines rely on precision machining to maintain fluid flow accuracy. Medical enclosure molding plays a crucial role in creating device enclosures made from materials like aluminum or medical-grade plastics. These molded enclosures protect delicate electronics while ensuring compliance with sterilization protocols and maintaining the device’s overall functionality and safety.
Custom Medical Solutions
Patient-Specific Components
Medical precision machining allows for the production of patient-specific prosthetics and implants, such as dental crowns or maxillofacial implants. By integrating advanced scanning and CAD technologies, these components are customized to match individual anatomy, improving outcomes and reducing recovery times.
Miniaturized Devices for Minimally Invasive Surgery
The growing demand for minimally invasive surgical procedures has driven innovations in precision medical manufacturing. Tiny, intricate components used in endoscopes, laparoscopic tools, and micro-robotic systems are manufactured with extraordinary precision, enabling advanced surgical techniques and reducing patient trauma.
Precision Design and Assembly Manufacturing for the Medical Device Industry
The Role of Precision Design
Precision design and assembly manufacturing for the medical device industry involve the creation of complex assemblies where accuracy and functionality are critical. This process ensures seamless integration of multiple components into devices such as ventilators, pacemakers, and imaging systems.
Advancements in Assembly Techniques
Recent innovations in precision design and assembly manufacturing for the medical device industry include robotic assembly and laser-guided positioning. These advancements improve the reliability and consistency of medical devices, ensuring optimal performance under demanding conditions.
Medical Device Precision Machining
What is Medical Device Precision Machining?
Medical device precision machining refers to the use of advanced machining technologies to produce high-precision components for medical tools and equipment. This includes machining intricate parts with tight tolerances, such as catheter connectors and surgical staplers.
Case Study: Precision in Robotic-Assisted Surgery
A notable example of medical device precision machining is the development of robotic surgical systems. These systems rely on micromachined components for enhanced dexterity and accuracy, enabling surgeons to perform complex procedures with minimal invasiveness.
Precision Machining Medical Furniture
Applications in Medical Furniture
Precision machining medical furniture focuses on creating components for hospital beds, surgical tables, and examination chairs. These parts require durability, smooth operation, and ergonomic design to support patient care effectively.
Benefits of Precision Machining for Medical Furniture
By leveraging precision machining medical machined components in medical furniture, manufacturers achieve superior quality, reduced maintenance needs, and enhanced user comfort. For instance, machined parts ensure seamless adjustment mechanisms in hospital beds and reliable locking systems for mobility aids.
Future Innovations in Medical Furniture
Ongoing research in precision machining medical furniture includes incorporating smart features like integrated sensors and antimicrobial surfaces. These innovations aim to improve hygiene and provide real-time data to healthcare professionals, ensuring better patient care.
Advantages of Precision Machining for Medical Devices
Precision machining for medical devices offers unparalleled benefits to the healthcare industry. It combines advanced technologies with stringent standards to produce components that meet the demands of modern medicine.
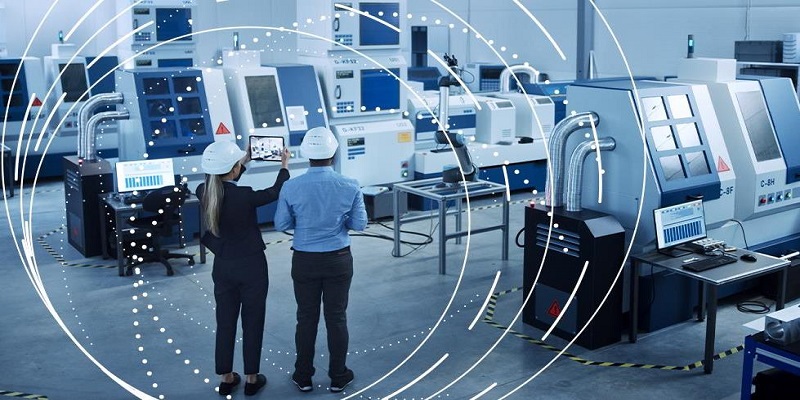
Precision and Accuracy
Precision machining for medical ensures the highest level of accuracy for manufacturing intricate components with tight tolerances. Whether creating parts for surgical instruments or diagnostic devices, the process guarantees uniformity and consistency across batches. For instance, precision CNC machining for medical allows the production of ultra-small features with micron-level precision, essential for minimally invasive surgical tools. Mold core pins for medical industry play a vital role in achieving such precision, ensuring the correct formation of cavities and details in the molded components, which are crucial for the accuracy of medical devices.
Customization
One of the standout features of precision machining medical applications is the ability to create highly customized components. This adaptability is vital for patient-specific prosthetics, implants, and dental solutions. Using advanced CAD/CAM technologies, precision medical device manufacturing enables engineers to design and produce unique components that cater to individual anatomical and procedural requirements.
Efficiency and Scalability
Precision machining for medical achieves remarkable efficiency and scalability in production. High-speed CNC systems enable rapid machining while maintaining quality. For large-scale manufacturing, this reduces costs and minimizes material waste. For example, in precision cnc machining for medical, automation streamlines the process, making it ideal for both prototyping and mass production.
Safety Compliance
Safety is paramount in healthcare, and precision medical device manufacturing adheres to stringent regulations and ISO certifications. By ensuring that materials and processes comply with biocompatibility and sterilization standards, manufacturers uphold the safety and reliability of medical devices. This includes precision machining medical instruments such as scalpels and retractors, which must meet rigorous cleanliness and structural integrity requirements.
Durability and Longevity
Components produced through precision machining medical techniques boast exceptional durability and longevity. This is crucial for implants, such as titanium bone plates or dental fixtures, which must endure constant wear and stress within the human body. Using advanced materials and machining processes, these parts retain their functionality over time, reducing the need for replacements.
Innovation and Technological Advancement
Precision machining for medical drives innovation in the industry by enabling the creation of cutting-edge medical devices. Techniques such as precision cnc medical machining empower manufacturers to develop components for robotic surgical systems, wearable health devices, and next-generation imaging equipment. These advancements are pivotal in addressing the growing demands of modern healthcare.
Precision CNC Medical Machining: A Cornerstone of Healthcare Manufacturing
What is Precision CNC Medical Machining?
Precision cnc medical machining combines computer-aided design and high-speed CNC technology to create intricate components with unmatched precision. This technique is essential for developing complex parts such as catheter connectors, valve components, and miniature screws used in implantable devices.
Why Choose CNC Machining for the Medical Industry?
CNC machining offers numerous advantages for the medical device manufacturing sector, ensuring precision, efficiency, and high-quality results. Here’s why it’s the preferred choice:
- Precision and Accuracy: CNC machining can produce medical components with tight tolerances and complex geometries, meeting the stringent demands of the medical industry.
- Design Flexibility: CNC machines accommodate a wide range of complex designs, allowing manufacturers to create custom parts tailored to specific medical applications.
- Component Integration: By incorporating complex shapes, CNC machining can reduce the need for multiple parts, simplifying assembly and enhancing the overall design.
- Material Compatibility: CNC machining handles a variety of materials, including metals, plastics, and composites, ensuring durability and resistance to harsh environments like chemicals and high temperatures.
- Miniaturization: CNC technology allows for the production of smaller, highly functional medical devices, keeping up with the growing demand for miniaturized products.
- Higher Production Capacity: Whether producing small batches or large volumes, CNC machining offers efficient production at a lower cost.
- Enhanced Productivity: Automated CNC processes increase production speed, reduce turnaround times, and enhance overall efficiency.
- Repeatability: CNC machining ensures consistent quality with high repeatability, reducing variations in production runs.
- Reduced Material Waste: CNC technology minimizes material waste by performing precise cuts and operations, leading to more sustainable production.
- Rigorous Quality Control: CNC machining incorporates strict inspection processes, ensuring that parts meet necessary specifications and quality standards.
In summary, CNC machining for the medical industry combines precision, efficiency, and flexibility, making it the ideal solution for producing high-quality, reliable medical components.
Applications of Precision Medical Machining Service
From orthopedic implants to micromachined surgical tools, precision cnc medical machining supports a broad range of applications. Its ability to handle diverse materials, including metals and medical-grade plastics, makes it indispensable in manufacturing durable, biocompatible components for the healthcare sector.
Case Study: Advances in Robotic Surgery
Precision cnc medical machining precision medical machining has revolutionized robotic surgical systems. By producing ultra-precise components, it enhances the accuracy and reliability of these systems, enabling surgeons to perform intricate procedures with minimal invasiveness and improved outcomes.
Selecting a Partner for Precision Machining in the Medical Field
Choosing the right partner for precision machining for precision cnc machining for medical devices is critical to ensuring the quality, reliability, and compliance of medical components. A trusted partner can streamline production, meet stringent healthcare standards, and drive innovation in precision manufacturing for medical devices.
Criteria for Selecting a Precision Machining Service
ISO Certifications and Healthcare Compliance
Medical manufacturing partners, such as precision medical machining manufacturers, must hold ISO certifications, such as ISO 13485, which demonstrate their adherence to healthcare regulations and quality management systems. Compliance ensures that precision machined medical instruments and devices meet global safety and performance standards, reducing the risk of product recalls and ensuring patient safety.
Proven Expertise in Medical Manufacturing
Experience in precision manufacturing for medical devices is essential. A partner with a proven track record of producing surgical tools, implants, and diagnostic equipment can offer valuable insights into design optimization and material selection, ensuring the best outcomes for your project.
Capacity for Prototyping and Mass Production
A versatile partner should handle both prototyping and large-scale production. Prototyping enables rapid testing and refinement of designs, while scalable manufacturing ensures that high-quality precision machined precision machining medical devices and components are delivered efficiently for market demand.
Medical Titanium Precision Machining: A Specialized Focus
Advantages of Medical Titanium Precision Machining
Medical titanium precision machining is a critical service for manufacturing implants and surgical tools. Titanium is biocompatible, corrosion-resistant, and incredibly strong, making it a top choice for precision machining for medical applications. Specialized techniques ensure that this challenging material is shaped with the accuracy required for medical use.
Case Study: Orthopedic Implants
Precision machining of titanium has revolutionized the production of orthopedic implants. These implants are customized to fit patients’ specific anatomy, reducing recovery times and improving surgical outcomes. This example highlights the necessity of a partner skilled in medical titanium precision machining.
Precision Medical Machining Ventilators
Precision precision machining medical equipment played a pivotal role during the COVID-19 pandemic. High-precision components, including valves and regulators, are critical to ventilator performance. Selecting a partner experienced in manufacturing ventilator parts ensures reliability and compliance with emergency healthcare needs.
Factors in Precision Medical Machining Ventalators
Precision machining for medical ventilators requires an ability to deliver miniaturized, precise parts under tight deadlines. Quality control is critical, as these components directly impact patient care and survival.
Why Precision is Important in Medical CNC Machining
Ensuring Patient Safety
Why precision is important in medical CNC machining becomes evident in the production of surgical tools and implants. Any deviation in tolerances can lead to product failure, posing risks to patients. High quality precision medical CNC machining ensures functionality and safety across all medical applications, minimizing risks and improving patient outcomes.
Advancing Innovation
Precision enables the development of innovative medical technologies, such as minimally invasive surgical tools and wearable devices. Precision machining for medical facilitates these advancements by delivering the complex components required for cutting-edge healthcare solutions.
Precision in Medical Device Manufacturing
Importance of Precision in Medical Device Manufacturing
Precision in medical device manufacturing is essential for meeting regulatory standards and ensuring device reliability. From diagnostic equipment to prosthetics, precision guarantees that each device performs as intended, enhancing patient outcomes.
Research Highlight: Diagnostic Equipment
Recent studies demonstrate how precision machining for medical impacts diagnostic accuracy. For example, precision-manufactured imaging equipment delivers clearer results, aiding in early detection and effective treatment plans.
Selecting a partner for precision machining for medical is a strategic decision with far-reaching implications. Whether focusing on medical titanium precision machining, ventilator components, or other applications, the right partner ensures compliance, innovation, and success in the competitive medical industry. Through expertise in precision manufacturing for medical devices and commitment to quality, a trusted partner becomes an essential ally in advancing healthcare solutions.
Limitations of CNC Machining in Precision Machining for Medical
While precision machining for medical using CNC technology offers many advantages, including high accuracy and versatility, it also has some limitations that can impact the production of medical components. These challenges need to be addressed through process optimization, tool enhancements, and a clear understanding of the design requirements. Below, we explore the key limitations of CNC machining in the medical field.
Complexity of Shape
CNC machining is ideal for producing parts with relatively simple to moderately complex geometries. However, it has limitations when dealing with highly intricate or complex shapes. For example, parts with undercuts, deep cavities, or internal features that are difficult to access with standard cutting tools may be challenging to machine. To address this, manufacturers may need to use specialized tooling or additional operations like EDM (Electrical Discharge Machining) or wire cutting. This can increase the overall manufacturing time and cost, making the process less efficient for highly complex designs.
Material Limitations
While CNC machining can handle a wide range of materials commonly used in medical devices—such as titanium, stainless steel, aluminum, plastics, and composites—certain materials may present challenges. Ceramics and some polymers, for instance, can be difficult to machine due to their hardness, brittleness, or specialized tooling requirements. Additionally, heat-sensitive materials can suffer from thermal deformation during the machining process, leading to accuracy issues. Manufacturers may need to implement advanced cooling systems or select alternative manufacturing methods to handle these materials effectively.
Limited Production Speed
CNC machines are renowned for their precision, but they are not always the fastest method of production, particularly when dealing with complex or delicate medical components. The process can be slower than other manufacturing methods like injection molding or stamping, especially when working with intricate geometries or multi-step operations. For high-volume production, this slower pace can significantly impact delivery timelines and increase production costs. Optimizing toolpaths and using faster cutting speeds may help, but there is always a trade-off between speed and quality in precision machining.
Size Limitations
CNC machines come in various sizes, and the machine’s size limits the maximum size of the part it can accommodate. Large or bulky medical components, such as prosthetics or implants, may not fit within the capabilities of standard CNC machines. This constraint can require manufacturers to invest in larger machines or explore alternative manufacturing methods, like additive manufacturing (3D printing) or casting, for large-scale components. This can increase the overall cost of production, particularly for oversized parts.
Surface Finishing
CNC machining is highly precise, but the surface finish of parts may not always meet the stringent requirements of the medical industry, especially for components that need to be smooth and free of defects. Medical parts often require tight surface finish tolerances, which might necessitate additional processes such as polishing, coating, or surface treatments to achieve the desired results. These extra steps not only add time to the manufacturing process but also increase costs, impacting the overall efficiency and profitability of production.
Operator Skills and Training
CNC machining requires highly skilled operators who can program, operate, and maintain complex machinery. The process of programming CNC machines, especially for intricate medical components, requires specialized knowledge and training. The shortage of qualified CNC operators can make it difficult to find the right personnel and can slow down production. Manufacturers must invest in training and continuous education to ensure that operators are proficient and can troubleshoot issues efficiently. This reliance on skilled labor can lead to higher operational costs and potential delays if qualified workers are not available.
While precision machining for medical using CNC technology remains one of the most effective methods for producing high-quality, reliable medical components, it is not without its limitations. Challenges such as handling complex shapes, material constraints, slower production speeds, size restrictions, and the need for additional surface treatments can affect the efficiency and cost-effectiveness of CNC machining. However, with ongoing advancements in machining technologies and process improvements, many of these limitations can be mitigated, ensuring CNC machining continues to play a vital role in the production of medical devices.
Challenges, Technologies, and Future Trends in Precision Machining for Medical
The development of precision machining for medical devices has revolutionized the healthcare industry by enabling the production of highly complex, reliable, and precise components. However, several challenges persist in this specialized field. Medical precision machining factories are continuously working on overcoming these obstacles through advanced technologies, while future development trends continue to shape the industry.
Challenges in the Development of Precision Machining for Medical
Material Challenges
Medical devices often require materials that are biocompatible, durable, and resistant to harsh environments like heat, chemicals, and moisture. Working with such materials, such as titanium, stainless steel, and medical-grade polymers, presents significant challenges. Precision machining must not only account for the material’s properties but also ensure the part’s integrity after machining.
Tight Tolerances and Complex Geometries
Medical devices, especially those used in surgeries and implants, require incredibly tight tolerances (often within microns) to ensure safety and functionality. Achieving these precise dimensions with complex geometries, while maintaining part strength and integrity, is a major technical challenge.
Regulatory Compliance
The medical industry is heavily regulated, with strict standards such as ISO 13485 and FDA compliance that manufacturers must meet. These regulations require manufacturers to prove that their precision machining processes adhere to specific standards for safety, traceability, and quality.
Cost Efficiency
Developing and producing high-precision parts for the medical industry often involves high production costs. The challenge lies in maintaining cost efficiency while ensuring quality, especially for small-batch runs or custom-made components used in specialized medical applications. Obtaining accurate medical precision machining quotes is essential in this process, as it helps manufacturers evaluate pricing and select suppliers that can deliver both quality and value.
Technologies Developed for Precision Machining in Medical
Multi-Axis CNC Machining
Multi-axis CNC (Computer Numerical Control) machines allow for the production of intricate and highly detailed parts. These machines enhance precision, enabling manufacturers to produce medical components with complex geometries and tight tolerances, crucial for implants, surgical instruments, and diagnostic devices.
Advanced Materials and Coatings
To meet the demanding requirements of medical devices, innovations in material science have led to the development of specialized alloys, biocompatible polymers, and advanced coatings. These materials offer improved durability, corrosion resistance, and biocompatibility, which are essential for long-term medical device performance.
Additive Manufacturing (3D Printing)
Additive manufacturing, or 3D printing, is increasingly being used for creating prototypes, small batch production, and custom parts in the medical field. 3D printing offers flexibility in design, faster prototyping, and the ability to produce highly intricate and customized components, including personalized implants.
Laser Machining
Laser machining technology allows for extremely fine cuts and precision in difficult-to-machine materials. It is used for cutting, engraving, and marking medical components with high accuracy, often in situations where traditional machining methods fall short.
Precision Measurement and Inspection Tools
Technologies such as coordinate measuring machines (CMMs), laser scanning, and vision systems are now used to perform precise measurements and inspections of finished parts. These systems ensure that each component meets stringent quality and tolerance requirements and can provide real-time data for quality control.
Future Development Trends in Precision Machining for Medical
Miniaturization of Medical Devices
As medical devices become more advanced, the trend toward miniaturization is expected to grow. Precision machining for medical applications will evolve to accommodate smaller, more intricate components that retain full functionality while reducing size. The demand for micro-machining and the ability to create even smaller, more precise parts will continue to increase.
Integration of Smart Technologies
The future of precision machining will likely see the integration of “smart” technologies into medical devices, such as sensors or embedded electronics. CNC machines may evolve to produce components with embedded electronics or micro-sensors for monitoring patient conditions, revolutionizing medical device functionality.
Sustainable Manufacturing
Sustainability will become a key focus in precision machining for medical devices. Manufacturers are likely to adopt more eco-friendly materials, processes, and waste-reduction techniques. Innovations in biodegradable materials and the ability to recycle surgical instruments or medical components will play a significant role in reducing the environmental footprint of the medical industry.
Automation and AI
Artificial intelligence (AI) and automation technologies will drive the future of precision machining for medical. AI will enable predictive maintenance for CNC machines, optimize machining processes, and enhance part quality control. Automation will reduce the risk of human error, increase throughput, and lower overall production costs.
Customization and Personalized Medical Devices
As personalized medicine and custom-made devices become more prevalent, precision machining will be critical in producing tailored components. Advanced machining technologies will enable the production of individualized implants, prosthetics, and surgical tools based on a patient’s specific needs.
The future of precision machining for medical devices is marked by innovation, with advancements in materials, technologies, and manufacturing processes driving the evolution of medical device production. Although challenges such as tight tolerances, material selection, and regulatory compliance persist, new technologies like multi-axis CNC machining, additive manufacturing, and AI are helping to overcome these obstacles. The industry’s future trends, including miniaturization, sustainability, and smart technology integration, promise to deliver even more sophisticated, efficient, and personalized solutions for the medical field.
FAQs about Precision Machining for Medical
The term CNC stands for Computer Numerical Control. In the medical field, CNC machines are integral in the manufacturing of a vast range of medical devices and components. These machines use computer programming to control the movement of tools and machinery, enabling the precise and consistent production of complex parts. They are particularly valuable in creating customized prosthetics, implants, surgical tools, and other critical medical devices. The high accuracy and repeatability of CNC machining ensure that each component meets strict regulatory standards and performance requirements crucial for patient safety and effective medical treatments.
Precision machining is the process of cutting, milling, turning, or shaving materials into precise shapes and dimensions. It is widely used in various industries, including aerospace, automotive, and especially in the medical field. In medicine, precision machining is employed to create intricate parts needed for medical devices, diagnostic equipment, and life-saving machinery. For instance, it is used to produce components for MRI machines, surgical instruments, implants, and customized prosthetics. The high level of accuracy and consistency that precision machining offers helps ensure the reliability and effectiveness of these medical devices.
CNC machining is used to manufacture a variety of surgical instruments that require high precision and consistency. Some of the common surgical instruments made using CNC machining include scalpels, tweezers, forceps, scissors, clamps, and bone saws. Additionally, CNC machines are also used to produce complex components of robotic-assisted surgical systems, which require intricate detailing and reliable functionality. The ability of CNC machining to work with various materials, such as stainless steel, titanium, and advanced polymers, makes it ideal for creating durable and sterile surgical tools that meet rigorous medical standards.
Machining precision can be incredibly high, often measured in micrometers (µm). Modern CNC machines can achieve tolerances as tight as ±0.001 mm (±1 µm), making them suitable for producing extremely precise components. This high level of precision is essential in the medical field where even minute deviations can affect the performance and safety of medical devices and instruments. Precision machining ensures that each part is manufactured to exact specifications, allowing for consistent and reliable functionality. The advanced technology used in CNC machining, including computer-aided design (CAD) and computer-aided manufacturing (CAM) software, further enhances its accuracy and capability to produce highly detailed and intricate parts.
The manufacturing of medical equipment requires strict adherence to quality standards, precision, and regulatory compliance to ensure both safety and functionality. Precision machining for medical applications is integral in producing high-quality, reliable medical devices such as surgical instruments, implants, and diagnostic equipment.
Material Selection:
Precision machining for medical devices starts with selecting biocompatible materials such as stainless steel, titanium, or specialized polymers. These materials must meet stringent regulations for safety and performance, particularly in medical environments.
CNC Machining:
Computer Numerical Control (CNC) machining plays a key role in the production of medical devices, offering extremely tight tolerances and repeatability. This process ensures parts are manufactured to precise specifications, crucial for the high-performance standards required in medical applications.
Quality Control and Testing:
Medical equipment manufacturers conduct rigorous testing, such as non-destructive testing (NDT), to ensure that each part meets specifications. The precision machining process must ensure consistent part integrity and functionality for patient safety.
Regulatory Compliance:
Manufacturers must comply with regulations such as ISO 13485 for medical devices and FDA guidelines to ensure that the equipment is safe for use in medical settings. Precision machining must meet these standards through controlled processes and documentation.
By following these steps and utilizing precision machining techniques, manufacturers can produce high-quality, reliable medical equipment that meets safety and regulatory standards.
Contact our professional team now for a same-day quote and risk-free project evaluation. Benefit from ISO 8 cleanrooms, advanced machines, and 12-hour fast response in medical injection molding.