FUJIU Medical Injection Mold is specializes in Precision Medical Machining Manufacturers delivering quality parts and services. Precision medical machining refers to the highly accurate and specialized process of creating medical device components and surgical instruments. It involves the use of advanced machining technologies like CNC milling, Swiss turning, and EDM to produce intricate parts with tight tolerances. These components are essential in medical devices, implants, and diagnostic equipment, ensuring that each piece functions safely and reliably. Similar to precision mold medical manufacturers, precision medical machining manufacturers play a critical role in transforming raw materials into high-performance products. The medical industry requires precision machining manufacturers to meet stringent standards, ensuring medical devices are made from high-quality materials like stainless steel, titanium, and specialized alloys. Tight tolerances are crucial for patient safety, as even the smallest deviation can affect device functionality. Precision directly impacts device performance, enhancing patient outcomes and reducing risks associated with medical procedures.
Low-Volume to High-Volume Production Capabilities
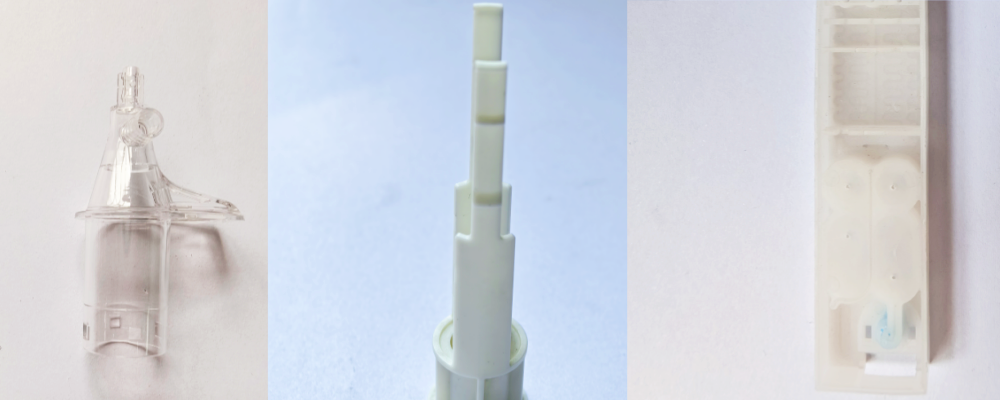
Attribute | Details |
---|---|
Brand Name | LY Medical Injection Mold |
Place of Origin | Dongguan, Guangdong, China. |
CNC Machining or Not | Options: CNC or Non-CNC Machining based on the specific product requirements. |
Material Capabilities | Aluminum, Brass, Bronze, Copper, Hardened Metals, Precious Metals, Stainless Steel, Steel Alloys, Titanium, Cobalt Chrome, Plastic, and other alloys. |
Machining Types | Broaching, Drilling, Etching/Chemical Machining, Laser Machining, Milling, Turning, Wire EDM, Rapid Prototyping, and other customized machining services. |
Micro Machining | Available for products requiring intricate and detailed work. |
Tolerance | ±0.005mm to ±0.1mm |
Surface Treatments | Polishing, Anodizing, Nickel Plating, Zinc Plating, Electroplating, Sandblasting, Painting, Powder Coating, Clear Anodizing, and Oil Printing. |
Service Options | OEM/ODM, One-Stop Services (includes Machining, Assembly, Packaging), Custom Logo Acceptance, and Small Order Accommodations. |
Inspection & Quality | 100% Inspection (Dimension and Quality Control for each product). |
Equipment Used | 3/4/5 Axis CNC Machining Centers, Advanced 3D Printing Equipment, and Precision Tools for Surface Treatments. |
Applications | Medical Devices |
Drawing Formats | 2D (PDF/CAD), 3D (IGES/STEP). |
MOQ | Small Orders Accepted. |
Quotation Lead Time | Within 24 hours. |
Production Lead Time | 12–15 days (may vary depending on the complexity of the order). |
Payment Methods | PayPal, Western Union, Trade Assurance...... |
Core Capabilities of Precision Medical Machining Manufacturers
Material Handling and Expertise
Precision medical machining manufacturers involved in wholesale precision medical machining must be skilled in handling a variety of materials, each carefully chosen for its suitability to specific medical applications. Common materials used in medical machining include stainless steel, titanium, Inconel, aluminum, and various medical-grade plastics. These materials are essential in the production of implants, surgical tools, and diagnostic equipment, where strength, corrosion resistance, and biocompatibility are paramount. Stainless steel and titanium are often selected for their durability and strength in implants and surgical instruments, while lighter materials like aluminum are favored for diagnostic equipment that requires precision without adding significant weight. Wholesale precision medical machining manufacturers are equipped with the expertise to handle these diverse materials while maintaining strict industry standards.
Machining Processes and Technologies
Precision medical machining manufacturers employ a range of advanced machining processes to create medical components that meet tight tolerances and complex specifications.
- CNC Milling and Turning: CNC (Computer Numerical Control) milling and turning are essential for the creation of medical parts that require precision and repeatability. These processes are particularly effective for producing components with intricate geometries, such as surgical instruments or implant parts, where even minor deviations can impact performance and patient safety. CNC machines provide the necessary accuracy, allowing manufacturers to achieve precise cuts, shapes, and finishes with minimal human intervention.
- Swiss Machining: Swiss machining is ideal for producing small, intricate parts that demand high accuracy and tight tolerances. This technique is commonly used in the production of medical components molding such as micro-sized surgical tools, connectors, and valve components, where traditional machining methods may fall short. Precision medical machining manufacturers utilize Swiss machining to produce components that are both reliable and high-performing in critical medical applications.
- EDM (Electrical Discharge Machining): EDM is a non-traditional machining process that uses electrical discharges to erode material and create complex geometries. This method is particularly useful for cutting hard metals, which are often required in medical implants and surgical instruments. EDM allows medical precision machining manufacturers to achieve fine details and smooth surfaces that would be impossible with conventional machining techniques, making it indispensable in medical device manufacturing.
- Multi-axis Machining: Multi-axis machining offers the ability to create highly complex medical components in a single setup. By using multiple axes of movement, this technique reduces the need for retooling and ensures the accuracy of parts that feature complex shapes. This process is crucial for manufacturing medical devices such as orthopedic implants, cardiovascular devices, and diagnostic equipment, where intricate designs are needed for optimal functionality. Precision medical machining manufacturers use multi-axis machining to streamline production and reduce the risk of errors.
These core capabilities enable precision medical machining manufacturer to deliver high-quality, reliable components that meet the stringent demands of the medical industry.
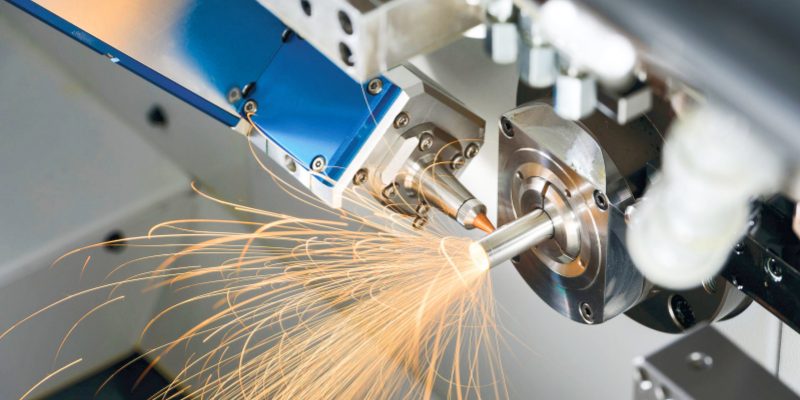
Precision Medical Machining Manufacturers: Machining Capabilities
Factors Affecting Machining Capabilities
When it comes to precision medical machining, several factors influence the capabilities of manufacturers in the industry. These factors determine the quality, efficiency, and cost-effectiveness of the manufacturing process. The primary factors include:
- Material Types: Medical devices require machining of a wide range of materials, from metals like stainless steel and titanium to polymers and ceramics. Different materials have different machinability characteristics, such as hardness, toughness, and thermal conductivity, which affect how easily they can be machined.
- Tolerances: Precision machining for medical applications often requires tight tolerances. Even minute deviations can affect the performance and safety of medical devices. Manufacturers must be capable of achieving micrometer-level accuracy.
- Surface Finish: The surface finish is critical in medical device components, especially those that come into contact with the human body. A smooth finish reduces the likelihood of contamination or adverse reactions.
- Machining Techniques: Manufacturers need to be familiar with advanced techniques like CNC machining, EDM (electrical discharge machining), laser cutting, and water jet cutting, all of which play a role in ensuring high precision.
Benefits of Advanced Machining Capabilities
- Enhanced Precision: The primary advantage of precision machining is the ability to produce highly accurate components, often with tolerances in the micron range. This ensures that each part fits seamlessly into a medical device assembly, ensuring functionality and safety.
- Consistency: Advanced machining technologies allow for the mass production of identical parts. Consistency is crucial in the medical field, where even slight variations in components can lead to failures in device performance.
- Material Versatility: With the use of various machining methods, manufacturers can work with a wide range of materials. This flexibility is important in creating medical devices that must meet specific functional and biocompatibility requirements.
- Cost-Efficiency: Although initial setup costs can be high, precision machining can result in cost savings in the long run due to high efficiency and the ability to automate much of the production process.
Types of Machining Techniques Used in the Medical Field
CNC Machining
CNC (Computer Numerical Control) machining involves the use of computerized systems to control machine tools, allowing for high precision and repeatability in manufacturing. CNC is widely used in the production of medical device components, such as implants, surgical tools, and diagnostic equipment.
- Application: CNC machining is used to create components that require complex geometries and tight tolerances. Common applications include orthopedic implants, dental instruments, and surgical instruments.
- Advantages: The precision and repeatability of CNC machining reduce errors and improve the overall quality of medical parts. The ability to work with a variety of materials is also a key advantage.
EDM (Electrical Discharge Machining)
EDM is used for machining hard metals and materials that are difficult to machine using traditional methods. It works by using electrical sparks to erode material, allowing for extremely precise cuts.
- Application: EDM is particularly useful in the production of fine details, such as small holes or intricate features in medical devices, including surgical instruments and implants.
- Advantages: EDM can work with very hard materials and can achieve fine, detailed features that may not be possible with other machining methods. It’s especially useful for components with very tight tolerances.
Laser Cutting and Laser Engraving
Laser cutting involves using a high-powered laser to cut materials with high precision. It is used for thin, flat materials and is ideal for creating intricate designs without generating heat that can affect the material.
- Application: Laser cutting is often used for cutting small medical device components or for engraving identifying marks, serial numbers, or other essential data on implants or surgical tools.
- Advantages: Laser cutting offers a high level of accuracy, minimal material waste, and no physical contact between the machine and the material, reducing the risk of contamination.
Water Jet Cutting
Water jet cutting uses a high-pressure stream of water, often combined with abrasives, to cut through materials. It is used for a variety of materials and is particularly effective for complex shapes.
- Application: Water jet cutting is ideal for cutting delicate medical materials, such as certain plastics and composites, that cannot withstand the heat generated by other cutting methods.
- Advantages: Water jet cutting is a non-thermal process, which helps to preserve the integrity of the material. It also allows for intricate cuts and complex shapes.
Challenges in Precision Medical Machining
- Material Properties: Some medical-grade materials, such as titanium alloys, are highly resistant to machining, requiring specialized tools and techniques to achieve the required precision. Manufacturers must choose the right tools and settings to optimize efficiency without damaging the material.
- Regulatory Compliance: Medical device manufacturers must comply with strict regulatory standards, such as ISO 13485 or FDA regulations. Precision machining must be done in controlled environments, ensuring that the processes meet the required specifications.
- Cost and Time Constraints: Precision machining often involves expensive equipment and highly skilled labor, making it a costly process. Balancing cost-effectiveness with the need for high precision can be a challenge, especially when scaling up production.
- Complex Geometries: Some medical devices require components with complex geometries, which can be difficult to machine accurately. Advanced techniques, such as multi-axis CNC machining or 3D printing, may be necessary for such designs.
Trends in Precision Medical Machining
- Automation and Robotics: Increasingly, medical machining is becoming automated with the use of robotics. Automation improves efficiency, reduces human error, and enhances the overall quality of medical devices.
- Additive Manufacturing: While not a traditional machining method, 3D printing or additive manufacturing is becoming an increasingly viable solution for creating complex and custom medical parts. This technology allows manufacturers to print prototypes and small runs of parts with intricate geometries.
- Integration of AI and Machine Learning: AI and machine learning are starting to play a role in predictive maintenance, process optimization, and quality control. These technologies help manufacturers ensure that their machining processes are running as efficiently and accurately as possible.
Case Studies and Examples
Example 1: Titanium Knee Implants
Manufacturers producing knee implants often use CNC machining to achieve the precise shape and smooth surface required for the implants. These components must be produced with high accuracy to ensure that they fit properly within the human body and function correctly under stress.
- Challenge: The titanium alloy used for knee implants is difficult to machine, and the component must meet stringent regulatory standards.
- Solution: The manufacturer uses a combination of multi-axis CNC machining and EDM to achieve the desired results, ensuring both precision and compliance with medical device standards.
Example 2: Surgical Instruments
Surgical instruments, such as scalpels and forceps, require ultra-sharp edges and smooth surfaces. These components are often produced through a combination of CNC machining and laser cutting.
- Challenge: Achieving the right level of sharpness while maintaining overall component integrity.
- Solution: Laser cutting is used for precision edges, while CNC machining ensures that the overall shape of the instrument is within the required tolerances.
Precision medical machining manufacturers need to leverage advanced machining technologies to meet the stringent requirements of the medical industry. The ability to work with a variety of materials, achieve tight tolerances, and deliver high-quality finishes is essential to ensuring the safety and performance of medical devices.
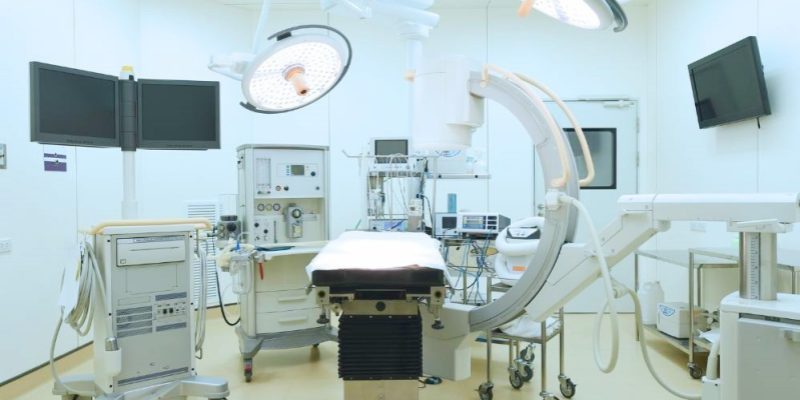
Precision Medical Machining Manufacturers: Medical Machining Materials
Factors Influencing Material Selection
Choosing the right material for medical machining is crucial, as it directly impacts the safety, functionality, and longevity of medical devices. Several factors influence the selection of materials in the precision machining process, including:
- Biocompatibility: Materials must be compatible with the human body to prevent adverse reactions when they come into contact with tissue, blood, or bones.
- Strength and Durability: Materials must withstand the mechanical stresses they will encounter in use, such as weight-bearing in implants or resistance to wear in surgical tools.
- Corrosion Resistance: Given that many medical devices are exposed to bodily fluids, materials need to resist corrosion and degradation over time.
- Machinability: The ability of a material to be easily machined with high precision without causing excessive tool wear or degradation of the material itself.
- Sterilization Requirements: Medical materials must be able to withstand various sterilization processes like autoclaving, gamma radiation, or chemical sterilization without degrading.
- Cost and Availability: The material should be cost-effective, available in sufficient quantities, and capable of being processed at the required scale.
Commonly Used Materials in Medical Machining
Precision medical machining manufacturers typically work with a range of materials, each selected for its unique properties suited to different medical applications. Here are some of the most commonly used materials:
Stainless Steel
Stainless steel, particularly grades 304 and 316L, is one of the most common materials used in medical machining due to its excellent balance of strength, corrosion resistance, and biocompatibility.
- Application: Used in surgical instruments, implants, prosthetics, and medical devices such as pacemaker cases.
- Advantages: Highly corrosion-resistant, easy to machine, and able to withstand repeated sterilization cycles. It also provides a good balance of mechanical strength and flexibility.
- Disadvantages: Stainless steel can be prone to scratching and can be difficult to machine to the most precise tolerances, particularly in harder grades.
Titanium and Titanium Alloys
Titanium is highly regarded for its biocompatibility, lightweight nature, and strength-to-weight ratio. It is particularly useful in medical applications where a material needs to resist corrosion, be lightweight, and integrate well with bone or tissue.
- Application: Frequently used in orthopedic implants (such as hip and knee replacements), dental implants, surgical tools, and bone fixation devices.
- Advantages: Excellent biocompatibility, exceptional corrosion resistance, and high strength relative to its weight. Titanium alloys (like Ti-6Al-4V) are also favored for their superior mechanical properties.
- Disadvantages: Titanium is challenging to machine due to its low thermal conductivity and toughness, which can lead to increased tool wear. Specialized tooling and techniques like EDM (electrical discharge machining) or water jet cutting are often required.
Cobalt-Chromium Alloys
Cobalt-chromium alloys are highly durable materials used in medical applications where strength and wear resistance are essential. They are often used for high-stress implants and medical devices that require extended wear life.
- Application: Commonly used in orthopedic implants, dental prosthetics, and heart valve components.
- Advantages: These alloys are highly resistant to corrosion, wear, and fatigue. They also offer excellent mechanical properties and strength, making them suitable for load-bearing implants.
- Disadvantages: Cobalt-chromium alloys can be difficult to machine due to their hardness and strength. Special tools and processes are required to maintain tight tolerances.
PEEK (Polyetheretherketone)
PEEK is a high-performance polymer known for its exceptional strength, stiffness, and biocompatibility. It is often used in medical applications where a combination of lightweight and high strength is needed.
- Application: Used in spinal implants, orthopedic devices, and components in diagnostic equipment.
- Advantages: High strength, resistance to chemical degradation, excellent biocompatibility, and radiolucency (ability to be transparent to X-rays). It is also capable of withstanding high-temperature sterilization processes.
- Disadvantages: PEEK can be more expensive than other polymers and can be challenging to machine to precise tolerances, requiring specialized CNC machines and tooling.
Ceramics
Medical-grade ceramics, such as alumina (Al₂O₃) and zirconia (ZrO₂), offer high strength, wear resistance, and excellent biocompatibility, making them suitable for specific medical applications.
- Application: Often used in dental implants, joint replacements (like hip and knee implants), and prosthetics.
- Advantages: Extremely hard, wear-resistant, and corrosion-resistant. Ceramics also have the advantage of being highly biocompatible, making them ideal for long-term implantation.
- Disadvantages: Ceramics are brittle and can fracture under certain stresses. Machining ceramics is also a challenge due to their hardness, requiring specialized tools and techniques such as diamond-tipped cutters.
Aluminum Alloys
While aluminum is typically less common in medical implants due to its lower strength compared to stainless steel or titanium, aluminum alloys are used in some medical devices and instruments.
- Application: Often used for lightweight medical instruments, housing for diagnostic equipment, and in some non-load-bearing components.
- Advantages: Lightweight, corrosion-resistant, and relatively easy to machine compared to harder metals. Aluminum alloys can also be anodized to improve their corrosion resistance.
- Disadvantages: Lower strength and less biocompatibility compared to other materials like stainless steel or titanium. Not suitable for high-load-bearing applications.
Polymeric Materials (Medical-Grade Plastics)
Medical-grade plastics, such as ultra-high-molecular-weight polyethylene (UHMWPE), polycarbonate, and polypropylene, are used in a wide range of medical applications due to their versatility, biocompatibility, and ease of machining.
- Application: Used in packaging, diagnostic devices, surgical instruments, and certain prosthetics.
- Advantages: Lightweight, easy to machine, and capable of being sterilized. Polymeric materials are also relatively cost-effective compared to metals and ceramics.
- Disadvantages: Lower mechanical strength compared to metals, which limits their use in load-bearing applications. They can also be sensitive to environmental factors like UV exposure and certain chemicals.
Material Properties and Their Impact on Machining
The properties of a material significantly impact the machining process. For instance:
- Hardness: Harder materials require specialized cutting tools and slower speeds to avoid tool wear or material damage.
- Thermal Conductivity: Materials with low thermal conductivity (like titanium) can generate more heat during machining, which can lead to thermal deformation and require coolant systems.
- Machinability: Some materials, like stainless steel or aluminum, are relatively easier to machine compared to more challenging materials like titanium or cobalt-chromium alloys, which may require advanced techniques such as EDM or laser cutting.
Challenges and Considerations in Machining Medical Materials
- Tool Wear: Materials like titanium and cobalt-chromium are tough on machining tools, which can lead to rapid tool wear and the need for frequent tool replacement. High-quality cutting tools with coatings (like carbide or diamond) may be necessary to extend tool life.
- Surface Finish: Achieving the required surface finish for medical components, especially those that will be implanted in the human body, is crucial. Rough surfaces can lead to biofilm formation, increasing the risk of infection or implant rejection. Polishing and fine finishing techniques are often employed.
- Material Removal Rates: Some medical materials, like ceramics or titanium alloys, have low material removal rates, making them slower and more costly to machine compared to easier-to-machine metals and plastics.
Trends in Material Use for Medical Machining
- Biodegradable Materials: There is growing interest in biodegradable materials for medical applications, particularly for temporary implants or drug delivery systems. These materials break down in the body over time and eliminate the need for a second surgery to remove the implant.
- Composite Materials: Composites, combining polymers with metals or ceramics, are increasingly being explored for medical devices. These materials can offer the best properties of multiple materials, such as enhanced strength, reduced weight, and improved biocompatibility.
- 3D Printing of Medical Materials: Additive manufacturing (3D printing) technologies are being employed to create custom implants or prototypes. Materials such as titanium, PEEK, and certain biocompatible polymers are being developed for 3D printing applications, offering new possibilities for medical device manufacturers.
The choice of material for precision medical machining is determined by various factors such as biocompatibility, strength, corrosion resistance, and machinability. Manufacturers must select materials that not only meet the stringent requirements of the medical field but also ensure that the components can be produced efficiently, precisely, and cost-effectively.
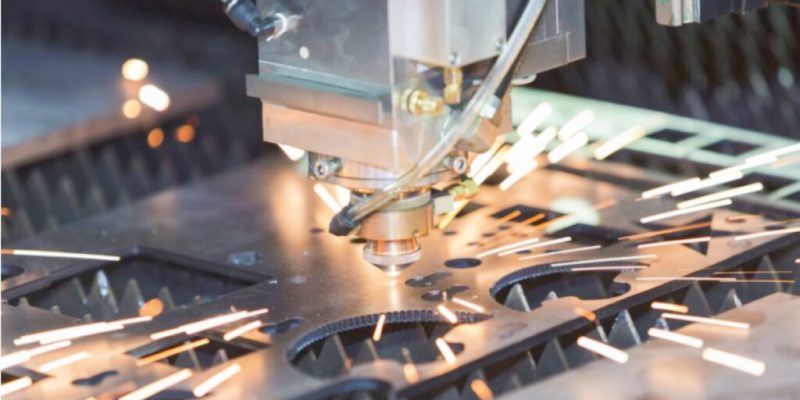
Custom Machined Components for Precision Medical Machining Manufacturers
Factors Driving the Need for Custom Machined Components
In the medical industry, precision is paramount, and off-the-shelf components often cannot meet the specific requirements of medical devices. Custom machined components are crucial for ensuring that each part is tailored to the exact needs of both the medical application and patient requirements. Several factors influence the demand for custom components in medical machining:
- Unique Medical Device Requirements: Medical devices often require specialized components to fit specific functions, geometries, and material properties. Custom machining ensures that each part is designed to meet the unique needs of the medical application.
- Patient-Specific Devices: As the demand for personalized medical treatments grows, custom machined components are increasingly used to produce patient-specific implants, prosthetics, and surgical tools. This growing trend in personalized care underscores the rising need for customized precision medical apparatus components, which are crafted to meet the individual requirements of patients and ensure better outcomes. These tailor-made components play a pivotal role in enhancing the effectiveness of personalized treatments, from joint replacements to custom prostheses.
- Complex Geometries and Tight Tolerances: Many medical devices feature intricate geometries, fine details, and very tight tolerances that cannot be achieved using off-the-shelf components. Custom machining allows manufacturers to achieve the precision needed for these complex parts.
- Regulatory and Compliance Requirements: Custom components ensure that all parts meet the stringent regulatory standards required by bodies like the FDA and ISO. Customization ensures better control over material properties, quality, and performance.
- Material and Surface Finish Optimization: Custom machining allows manufacturers to select the most appropriate materials and surface finishes for specific applications, whether it’s biocompatibility, strength, or resistance to wear and corrosion.
Benefits of Custom Machined Components
- Precision and Accuracy: One of the greatest benefits of custom machining is the ability to produce parts with extremely high precision. Components for medical devices often require tolerances within a few microns to ensure proper function and safety.
- Enhanced Performance: Custom parts can be designed for optimal performance in specific medical applications. Whether it’s reducing friction in surgical instruments or ensuring a perfect fit for an implant, custom machining guarantees the component works as intended.
- Improved Biocompatibility: Custom machined components can be tailored to use the best materials for the specific medical application, enhancing the biocompatibility of implants, surgical tools, or diagnostic equipment.
- Faster Time to Market: With custom machining, manufacturers can produce prototypes or low-volume runs of medical parts quickly, helping to accelerate the development cycle and reduce time to market for new medical devices.
- Cost-Effective in the Long Run: While custom machining can have higher initial costs compared to mass-produced components, it can be more cost-effective in the long term. This is especially true for high-precision components or low-volume production runs where off-the-shelf options are not viable.
Key Custom Machined Components in the Medical Industry
Custom machined components are used across a wide range of medical applications. Some of the most common types include:
Orthopedic Implants
- Types: Hip replacements, knee implants, spinal fusion devices, and joint replacements.
- Materials: Titanium, cobalt-chromium alloys, stainless steel, PEEK, and ceramics.
- Machining Techniques: CNC machining, EDM, and surface finishing methods like polishing and coating.
Custom machined orthopedic implants need to meet high precision and biocompatibility standards. These implants must be tailored to fit individual patient anatomy, which is often done through CAD modeling and 3D imaging.
Surgical Instruments
- Types: Scalpels, forceps, scissors, bone saws, and retractors.
- Materials: Stainless steel, titanium, and specialized alloys.
- Machining Techniques: CNC milling, turning, grinding, and polishing.
Surgical instruments are often custom machined to meet specific ergonomic needs and to ensure that they can perform complex procedures with precision. Sharpness, weight, and balance are critical factors that are optimized through custom machining.
Medical Implants and Devices
- Types: Cardiac devices (e.g., pacemaker casings), vascular stents, dental implants, and custom prosthetics.
- Materials: Titanium, stainless steel, ceramics, PEEK, and biodegradable polymers.
- Machining Techniques: CNC machining, laser cutting, and water jet cutting.
Medical implants, including those for the heart, vascular system, and teeth, often require unique shapes and materials to ensure proper fit and functionality. Custom machining allows for the production of implants tailored to the patient’s anatomy and specific medical needs.
Diagnostic Equipment Components
- Types: Components for ultrasound machines, MRI devices, and diagnostic tools.
- Materials: Aluminum, stainless steel, and specialized polymers.
- Machining Techniques: CNC machining, turning, and precision grinding.
The components used in diagnostic equipment require precision machining to ensure reliable performance in medical imaging and other diagnostic functions. Custom machining ensures that each component can withstand the mechanical and environmental stresses during use.
Custom Surgical Guides
- Types: Guides for implant placement, bone cutting templates, and alignment aids.
- Materials: Biocompatible plastics, PEEK, and titanium.
- Machining Techniques: CNC machining, 3D printing, and laser cutting.
Custom surgical guides are designed to help surgeons perform precise operations, such as implant placement or bone resection. These components need to be accurately designed and machined to fit the specific patient anatomy.
Machining Techniques for Custom Medical Components
To achieve the precision required for custom medical components, manufacturers use a variety of advanced machining techniques, including:
CNC Machining
- Description: CNC (Computer Numerical Control) machining allows for highly precise cutting, milling, turning, and drilling operations on a variety of materials. CNC machines are programmed to perform exact movements, ensuring that each part is produced to the exact specifications.
- Advantages: CNC machining is ideal for creating custom medical components with intricate geometries and tight tolerances. It is versatile, capable of working with a variety of materials, and can produce parts quickly and consistently.
Electrical Discharge Machining (EDM)
- Description: EDM uses electrical sparks to erode material and is particularly useful for machining hard metals and intricate shapes that are difficult to achieve with traditional cutting tools.
- Advantages: EDM is effective for achieving complex shapes with fine details, particularly in materials such as titanium or cobalt-chromium alloys. It is commonly used for components like medical implants and surgical instruments that require high precision.
Laser Cutting and Engraving
- Description: Laser cutting uses high-powered lasers to cut or engrave materials with exceptional precision. Laser engraving is often used to mark components with serial numbers, logos, or other identifying features.
- Advantages: Laser cutting is ideal for creating custom components with intricate shapes or detailed engravings without contact between the machine and material. This minimizes the risk of contamination and damage to delicate components.
Water Jet Cutting
- Description: Water jet cutting involves using a high-pressure stream of water, sometimes combined with abrasives, to cut through materials. This process is ideal for materials that cannot withstand the heat generated by other cutting techniques.
- Advantages: Water jet cutting is a non-thermal process that preserves the integrity of the material. It is particularly effective for cutting through materials like plastics, composites, and certain metals used in medical devices.
3D Printing/Additive Manufacturing
- Description: Additive manufacturing or 3D printing involves creating components layer by layer from digital models. This method is used for rapid prototyping, custom implants, and small production runs.
- Advantages: 3D printing offers high flexibility in design and can produce highly complex and customized parts. It is especially valuable for creating patient-specific implants and prototypes for testing before full-scale production.
Challenges in Manufacturing Custom Medical Components
- Material Selection and Biocompatibility: Ensuring that the material selected for custom components is biocompatible and meets the specific performance requirements of the device is critical. Some materials may be difficult to machine or may require special treatments to ensure they do not degrade in the human body.
- Tight Tolerances: Custom components often require tight tolerances, which can be challenging to achieve with traditional machining methods. Advanced techniques like multi-axis CNC machining and EDM are often necessary to meet these precise specifications.
- Regulatory Compliance: Medical components must meet strict regulatory requirements from bodies like the FDA and ISO. This often means extensive testing, documentation, and validation throughout the design and manufacturing process.
- Cost and Lead Time: Custom machining can be expensive due to the complexity of the parts and the specialized equipment required. Additionally, lead times can be longer compared to mass-produced components, especially when prototypes are involved.
Trends in Custom Medical Machined Components
- Personalized Medicine: As the demand for personalized medical treatments grows, custom machined components are increasingly used to produce patient-specific implants, prosthetics, and surgical tools.
- Miniaturization: Medical devices are becoming increasingly smaller and more complex. Custom machining is essential to create the tiny, intricate components needed for devices like pacemakers, stents, and minimally invasive surgical tools.
- Integration of Advanced Manufacturing Technologies: The use of additive manufacturing (3D printing) and AI-driven automation is growing, allowing for faster and more precise custom component production. This is especially useful in creating prototypes or small-batch runs of specialized components.
Custom machined components are essential for the production of medical devices that require high precision, biocompatibility, and tailored designs. By using advanced machining techniques such as CNC machining, EDM, laser cutting, and 3D printing, manufacturers can create components that meet the stringent requirements of the medical industry. Despite challenges like material selection, regulatory compliance, and cost, custom machining remains a vital part of developing safe, effective, and innovative medical devices.
Notable Medical Components Manufactured by Precision Machining Companies: Precision Medical Machining Manufacturers
Examples of Medical Parts
Precision medical machining manufacturers produce a wide range of critical medical components, including:
- Surgical Instruments: These include tools like scalpels, forceps, and scissors. Each instrument must be precisely crafted to ensure it functions safely and effectively in medical procedures.
- Diagnostic Equipment: Key components of MRI and CT scanners rely on the precision machining of various parts, which are essential for delivering accurate diagnostic imaging.
- Respiratory Devices: Components for ventilators, oxygen regulators, and other respiratory equipment must be manufactured with precision to ensure they operate reliably in critical care environments.
- Implants: Components like orthopedic implants, dental implants, and joint replacements must meet strict quality standards and be designed for both functionality and patient safety.
- Specialized Components:
- Catheters used in diagnostic or therapeutic procedures require highly precise machining to ensure safety and effectiveness.
- Ligation Devices are used to seal blood vessels in surgeries, and their reliability is directly tied to the precision in manufacturing.
- Miniature Gears for cardiac devices require exacting precision due to their small size and importance in ensuring the correct function of life-saving devices.
High-Precision Components in Action
Precision medical machining manufacturers ensure that the reliability and safety of critical medical devices are maintained through exact manufacturing processes. Key applications include:
- Orthopedic Implants: These must fit precisely within the human body to avoid complications and ensure long-term functionality. Precision machining guarantees that implants like hip replacements and spinal fusion devices perform optimally.
- Diagnostic Equipment Components: The accuracy of components in MRI and CT scanners is critical to ensure that imaging results are reliable and accurate. Any minor deviation in part specifications could lead to inaccurate diagnoses, which could severely affect patient care.
- Respiratory Devices: For medical devices like ventilators, precision machining ensures that critical components such as valves and regulators provide consistent, reliable performance, particularly in emergency or intensive care situations.
These examples demonstrate how precision medical machining manufacturers are essential to creating components that meet the highest standards of safety and performance across various medical fields.
The Role of Certifications and Quality Control in Medical Machining: Precision Medical Machining Manufacturers
Industry Certifications
Precision medical machining manufacturers must adhere to rigorous industry certifications to ensure that their products meet the highest standards for safety, quality, and regulatory compliance. These certifications serve as proof that the manufacturer is capable of producing high-quality medical components.
- ISO 9001: This certification ensures that manufacturers maintain a quality management system (QMS) that is internationally recognized. It sets out criteria for quality control systems that are crucial in producing reliable, high-performance medical parts. For precision medical machining manufacturers, maintaining this certification is essential for ensuring that their operations remain efficient and consistent.
- ISO 13485: Specifically designed for the medical device industry, this certification ensures that manufacturers meet the specific regulatory requirements for medical devices. Precision medical machining manufacturers with ISO 13485 certification demonstrate their ability to produce parts that are safe for use in medical applications. This is particularly important for components used in life-saving devices like implants and diagnostic equipment.
- ITAR Compliance: For manufacturers producing parts used in medical devices for military or government applications, ITAR (International Traffic in Arms Regulations) compliance is a must. This certification ensures that products meet strict export control regulations, which is vital for maintaining national security and ensuring that sensitive technologies are handled correctly.
- FDA Guidelines: The U.S. Food and Drug Administration (FDA) plays a critical role in regulating medical device manufacturing. Precision medical machining manufacturers must follow FDA guidelines, especially those related to quality control and safety, to ensure that the components they produce meet the standards required for medical applications. The FDA provides oversight for ensuring that medical devices are safe and effective for patient use.
Quality Assurance and Testing
Quality control is an essential component of the precision medical machining process. Manufacturers use a variety of advanced techniques to ensure that the components they produce meet or exceed industry standards.
- Dimensional Checks: Precision medical machining manufacturers use state-of-the-art metrology equipment to perform dimensional checks on parts. These checks ensure that all components are manufactured within the tight tolerances required for medical applications. Even the smallest deviation can compromise the functionality of a medical device, so dimensional accuracy is a key priority.
- Material Testing: To ensure the integrity and safety of the materials used, manufacturers often conduct material testing, including hardness tests, tensile tests, and fatigue testing. This is particularly important when working with materials like titanium or Inconel, which are used in critical medical applications such as implants and surgical tools.
- Inspection Using Advanced Equipment: To ensure parts meet all required specifications, precision medical machining manufacturers employ advanced inspection technologies such as coordinate measuring machines (CMM), laser scanning, and 3D imaging. These technologies provide a highly accurate, detailed analysis of each part, ensuring it adheres to the exact tolerances and specifications required for medical devices.
By following strict industry certifications and maintaining robust quality assurance processes, precision medical machining manufacturers ensure that every component produced is reliable, safe, and ready for use in critical medical applications. These practices are integral to maintaining the high standards required in the medical device industry.
Benefits of Precision Medical Machining for the Healthcare Industry: Precision Medical Machining Manufacturers
Improved Patient Safety
Precision medical machining manufacturers play a crucial role in enhancing patient safety by producing medical components with unparalleled accuracy. The level of precision achieved through advanced machining processes ensures that critical medical parts fit properly and function as intended, reducing the risk of malfunctions or complications during medical procedures.
- Better Fitting and Functionality: Many medical devices, such as orthopedic implants and surgical instruments, rely on precise dimensions to ensure they fit properly within the human body. If these components are manufactured with even the slightest inaccuracies, they can cause discomfort, improper functioning, or even failure. Precision medical machining manufacturers utilize state-of-the-art technologies to create parts that meet strict tolerances, ensuring optimal performance and reducing the likelihood of device failure. For example, implants like hip or knee replacements require exact measurements to ensure that they function seamlessly with the body’s natural mechanics.
- Preventing Malfunctions and Ensuring Safety: The consequences of malfunctioning medical components can be severe, often leading to extended recovery times, additional surgeries, or worse, harm to patients. By employing high-precision machining techniques, manufacturers reduce the likelihood of producing defective or subpar components. These processes help prevent issues such as poor tolerances, weak spots in materials, and other defects that could compromise the safety of medical devices. Furthermore, the use of high-quality materials ensures that the parts used in medical devices are durable and capable of withstanding the stresses they will face in the human body.
Cost Efficiency and Faster Turnaround
Precision medical machining manufacturers contribute to cost efficiency and faster production timelines, which are essential for meeting the ever-growing demand for medical devices and components.
- Reduced Production Time and Costs: Advanced machining technologies, such as CNC machining, Swiss machining, and multi-axis machining, allow precision medical machining manufacturers to streamline production processes, reducing both lead time and costs. These technologies allow for highly automated production, which increases productivity while maintaining high precision and minimizing waste. For example, multi-axis machining enables the creation of complex parts in fewer steps, reducing the time spent on setup, material handling, and quality checks. By cutting production time, manufacturers can keep costs lower while still providing high-quality components for medical devices.
- Streamlined Production Methods: The demand for medical devices continues to rise globally, with many manufacturers needing to produce large volumes of components in a short period of time. Precision medical machining manufacturers have adapted by implementing more efficient production methods, such as lean manufacturing techniques and rapid prototyping. These strategies help ensure that production timelines are adhered to, while still maintaining the rigorous standards required for medical devices. Faster turnaround times not only benefit manufacturers but also help healthcare providers get essential devices to patients more quickly, improving overall patient care.
By offering improved patient safety through precise component manufacturing and optimizing production processes for cost efficiency, precision medical machining manufacturers are vital to advancing the healthcare industry. Their contributions ensure that medical devices are safer, more reliable, and produced in a timely manner to meet the increasing demands of the medical field.
Specialized Roles of High Precision Medical Component Manufacturer and Precision Medical Molds and Plastic Parts Manufacturers
High Precision Medical Component Manufacturer
Precision medical machining manufacturers specialize in creating intricate, reliable, and safe parts for the healthcare industry. These manufacturers use cutting-edge technologies and processes, such as CNC machining, Swiss turning, medical injection molding, and multi-axis machining, to produce components with incredibly tight tolerances. They play a vital role in producing complex parts used in critical medical devices like pacemakers, surgical instruments, and implants.
- Manufacturing High-Precision Components for Medical Devices: These manufacturers are integral in making parts that require extreme precision, such as miniaturized components for cardiac devices, orthopedic implants, and diagnostic equipment. Their expertise ensures that each component fits seamlessly with other parts, contributing to the overall effectiveness and safety of medical devices.
- Ensuring Reliability in Critical Applications: For medical devices, failure is not an option. High precision medical component manufacturers ensure that each part they produce meets the exact specifications required for each application. Their attention to detail guarantees that components will perform under the demanding conditions of medical environments, whether it’s in a surgical operation or a life-saving procedure.
Precision Medical Molds and Plastic Parts Manufacturers
Precision medical molds and plastic parts manufacturers are responsible for producing the essential plastic components used in medical devices. These manufacturers focus on creating high-quality, durable, and precise molds and plastic parts that are essential for medical applications ranging from drug delivery systems to surgical tools.
- Creating Custom Medical Molds: Precision medical molds are used to produce plastic components that must meet high standards of accuracy and performance. Manufacturers of these molds ensure that each mold is designed and manufactured to fit the specific needs of the medical device, from syringes and catheter parts to housing for diagnostic equipment. The use of precision molding techniques guarantees that each plastic part, including custom medical molding components, is free of defects, making them safe and effective for medical use.
- Manufacturing Durable Plastic Parts for Medical Applications: Plastic is often used in medical devices because of its versatility, light weight, and durability. However, it must meet stringent quality standards. Precision medical molds and plastic parts manufacturers create plastic components that can withstand sterilization processes, resist chemicals, and maintain their integrity over time. These high-precision plastic parts play a critical role in a wide range of medical applications, ensuring that the devices they are part of continue to function reliably for extended periods.
By focusing on the production of highly accurate components and molds, both high precision medical component manufacturers and medical plastic components manufacturer significantly contribute to the development of safe, reliable, and effective medical devices. These specialized manufacturers are essential for ensuring that the healthcare industry has access to the highest-quality parts that meet both performance and safety standards.
Contact our professional team now for a same-day quote and risk-free project evaluation. Benefit from ISO 8 cleanrooms, advanced machines, and 12-hour fast response in medical injection molding.