Purchase Precision Mold Medical Elevating Healthcare
Low-Volume to High-Volume Production Capabilities
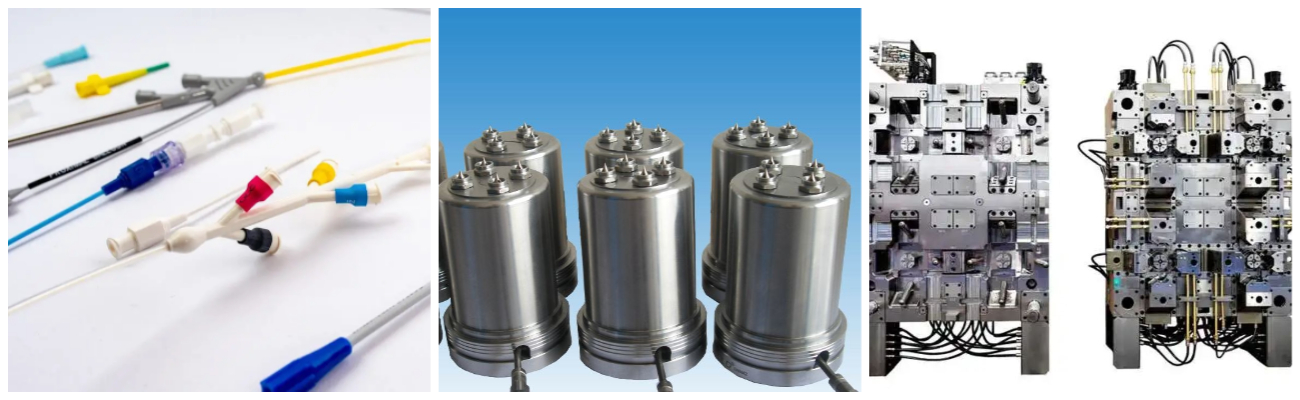
Attributes | Details |
---|---|
Place of Origin | Dongguan, Guangdong, China |
Brand Name | LY Medical Injection Mold |
Molding Mode | Plastic Injection Mold |
Product Name | Plastic Injection Medical Parts Plastic Injection Mold Medical |
Model | Customizable |
Product Material | Plastic |
Material | ABS, PP, PEEK, PC, PMMA, POM, etc. |
Surface Treatment | Original, Matte or Customized Surface Texture |
Cavity | Customizable |
Color | White, Black, Gray or Customized Color |
Molding Mode | Plastic Injection Mold |
Size | Customized Size |
Processing Service | Molding, Cutting |
Logo | Customizable Logo |
Service | OEM/ODM Customization |
Packing | Plastic Bag Packaging or Packaging According to Customer Needs |
Shipping | By Sea or Air According to Customer Requirement |
In today’s fast-paced medical industry, the demand for high-quality medical devices has never been greater. At FUJIU Medical Injection Mold, we recognize that precision is not merely a benefit but a necessity when it comes to manufacturing medical products. Utilizing cutting-edge fabrication methodologies and technologies, we provide Precision Mold Medical services that prioritize attention to detail.
When your medical device designs demand the highest levels of fabrication quality and tight tolerances, partnering with an expert is essential. FUJIU Medical Device Injection Mold stands out as your strategic partner in overcoming challenges related to design, production, development, and distribution. Our commitment to precision mold medical services ensures that your projects achieve the highest standards in quality and compliance.
Why You Need a Strategic Partner for Precision Mold Medical Services
At FUJIU Medical Injection Mold, we provide expertise in mold tooling that allows you to leverage several advantages:
Cost-Effective Precision Mold Tooling Mastery
Cutting-Edge Processing Techniques: Our advanced methodologies enable effective work with high-performance materials, ensuring precision and quality.
Micro-Scale Detail and Tolerances: Our capabilities allow us to produce intricate components with tight tolerances, ensuring compliance with regulatory standards.
Flexible Production and Logistics for Injection Molded Devices
With our extensive expertise and commitment to world-class quality, we support various production needs:
Low- to Mid-Volume Production: Our flexible manufacturing capabilities enable us to adapt to your specific project requirements.
Quick-Turn Overflow Work: We can manage urgent production needs, ensuring your project stays on track without compromising quality.
Offload Contract Manufacturing: By partnering with us, you can streamline operations and focus on core business activities while we handle manufacturing processes.
Prototype and Short Production Runs: Our agility in production facilitates rapid prototyping and short runs, helping you bring new medical devices to market quickly.
Shipping and Packaging Logistics Support: We provide comprehensive logistics services, ensuring your products are packaged and shipped according to industry standards, reducing your supply chain burden.
Precision Molding Expertise
Our engineers offer complete design, prototyping, and prototype support, backed by:
Over 20 Years of Experience: Our extensive industry experience allows us to anticipate challenges and deliver effective solutions.
Expertise in the Medical Industry: With a deep understanding of medical regulations and standards, we ensure that your devices meet all compliance requirements.
Proven Stage-Gate Production Process: Our structured approach to project management enables effective control of the production process, ensuring high-quality outcomes.
Commitment to Quality Control
To protect and support the lives of patients and medical staff worldwide, the quality of medical components is paramount. At FUJIU Medical Injection Mold, quality control is integral to our operations. We adhere to stringent quality measures throughout the manufacturing process, including:
Installation Qualification (IQ): Verifying that all equipment and systems are installed correctly.
Operational Qualification (OQ): Ensuring that processes perform as expected under specified conditions.
Performance Qualification (PQ): Confirming that the final product performs as intended under actual operating conditions.
Lot Traceability: Every product batch is traceable to ensure accountability and quality assurance.
Precision Mold Medical Production Process
The precision mold medical production process is a rigorous, multi-step journey that transforms clinical needs into reliable, high-performance medical devices. This process involves collaboration between R&D engineers, clinical professionals, suppliers, and regulatory bodies to ensure the final product meets the highest standards of safety, durability, and effectiveness. From initial research to final regulatory testing, each phase focuses on precision, quality control, and the optimization of functionality to meet the unique demands of medical applications. Below is an overview of each stage in the process.
1. Determine Clinical Needs
The production of precision mold medical devices begins with understanding the real clinical needs. R&D engineers engage with professional audiologists, healthcare providers, and existing users of precision molds to identify pain points and areas where innovation is necessary. This helps in ensuring that the developed products truly address clinical challenges and enhance user experience.
2. Preliminary Research and Technical Solutions
After identifying the clinical needs, the R&D team conducts preliminary research and develops several technical solutions. These solutions consider various aspects such as chip selection, circuit design, signal processing algorithms, adaptation software, and accessory design, ensuring a comprehensive approach to meeting the project’s technical requirements.
3. Expert Verification and Project Launch
Once the technical solutions are proposed, they undergo strict verification by a multidisciplinary expert group, including clinical professionals, procurement specialists, production teams, and marketing experts. Only after these solutions are finalized is the project officially launched for further development.
4. Global Component Selection
For the development of precision mold medical devices, components are sourced globally according to rigorous quality and performance standards. This global sourcing ensures that the supply chain is reliable and that all components meet the necessary specifications for high-performance medical applications.
5. Comply with Standards
At every step of the precision mold medical production process, compliance with established standards is paramount. These standards cover various aspects of precision molding, ensuring that the materials, designs, and production processes adhere to safety and quality benchmarks required in the medical industry.
6. Durability and Fatigue Testing
During the development phase, products undergo a series of durability and fatigue tests. These include anti-fall, anti-salt spray, constant temperature and humidity testing, and high/low temperature impact tests. Additionally, nano-coating technology is often used to improve the waterproof capabilities of products, ensuring they can withstand harsh environmental conditions.
7. Advanced Testing
A comprehensive performance testing system is established to evaluate the effectiveness of signal processing algorithms and the overall performance of the product in different acoustic or functional scenarios. This stage ensures that the device meets the performance expectations set in the early development stages.
8. Clinical Trials
Once the product reaches an advanced stage, it is handed over to a trial group for preliminary clinical testing. The product must demonstrate superior performance in complex, real-world environments compared to existing products. If successful, further clinical trials are conducted with additional volunteers to verify the clinical effectiveness.
9. Expert Review and Acceptance
After clinical trials and interim testing, the results are submitted to an expert group for review. The experts use international precision mold subjective scoring scales to compare the new product’s performance with that of previous models. The product will only pass this stage if its performance shows statistically significant improvements.
10. Regulatory Testing
The final product samples are sent to government regulatory agencies or designated testing facilities for re-verification of their performance. The product must pass this regulatory testing, and the results are compiled into a test report that will be submitted for approval.
11. Medical Device Registration
Following successful regulatory testing, the product’s medical device registration information and test reports are submitted to government agencies for approval. After passing the approval process, a new product registration certificate is issued, and batch samples are retained for future reference.
12. Improve the Production Process
To maintain high standards of quality and safety, the production process is continuously improved. Compliance with ISO medical device quality management systems ensures that every component from design to production is traceable. This guarantees that each precision mold medical device meets strict quality control measures, providing the safety and reliability that healthcare professionals and patients rely on.
Each of these stages is critical in ensuring that the final precision mold medical devices meet stringent safety standards, offer superior performance, and are ready for widespread clinical use.
Why Precision Mold Medical Manufacturing is Essential in Medical Injection Molding
Precision mold medical manufacturing plays a vital role in the medical injection molding process, as even the smallest deviation in a medical device can have catastrophic consequences. Whether producing syringes, surgical instruments, or implantable devices, the accuracy of each component is crucial. Medical injection molding is strictly regulated to ensure that these devices function exactly as intended, minimizing the risk of harm to patients. Even a fraction of a millimeter’s error can result in a device malfunctioning, which is unacceptable in the medical field.
The significance of precision plastic molding in the medical industry cannot be overstated. Every product must meet stringent industry standards, and tolerances are so tight that even the most advanced molding machines are pushed to their limits. This ensures that the final products are safe, reliable, and effective in critical medical applications.
The molding process itself is a cornerstone in the production of medical devices used across clinics, hospitals, laboratories, research institutions, and educational settings. Precision molding guarantees that these devices adhere to strict tolerances, quality control measures, and regulatory compliance, all of which are necessary for ensuring patient safety and successful outcomes.
Looking to the future, continuous innovation in medical injection molding, particularly in micro molding and automation, promises even greater precision. As medical devices continue to shrink, become more complex, and integrate more closely with healthcare technologies, the importance of precision mold medical manufacturing will only grow.
Precision Mold Medical: New Materials Shaping the Future of Medical Devices
The world of medical device manufacturing is always in flux as exotic new materials redefine what’s possible. In the realm of precision mold medical applications, innovative materials are paving the way for the next generation of medical devices. These advanced materials not only enhance performance but also expand design possibilities, enabling manufacturers to create safer, more effective, and sustainable products.
One of the most exciting advancements in medical device manufacturing is the use of Cyclic Olefin Polymer (COP) as an alternative to traditional glass vaccine vials. COP offers several advantages: Lightweight and Durable: COP is significantly lighter than glass, making it easier to transport and handle. Its durability reduces the risk of breakage, which is a critical factor in the storage and distribution of vaccines. Excellent Clarity and Transparency: COP provides optical clarity, allowing for easy visual inspection of contents. This is essential for ensuring the integrity of the vaccine before administration. Chemical Resistance: COP exhibits superior resistance to various chemicals, including those found in vaccines, ensuring that the material remains stable and does not interact negatively with its contents. By leveraging COP in precision mold medical applications, manufacturers can create safer and more efficient vaccine delivery systems that meet the rigorous demands of the healthcare industry. Cyclic Olefin Copolymer (COC) is another revolutionary material transforming the design and functionality of medical devices, particularly in the realm of optics: High Optical Clarity: COC offers exceptional light transmission properties, making it ideal for intricate medical lenses used in diagnostic equipment and surgical instruments. Design Flexibility: The ability to mold complex shapes and features enables the production of sophisticated lens designs that enhance imaging quality and precision in medical applications. Thermal Stability: COC maintains its properties under a wide range of temperatures, ensuring that medical devices function reliably in various environments, from sterilization processes to everyday clinical use. The integration of COC into precision mold medical applications facilitates the development of advanced medical optics, enhancing the performance and accuracy of diagnostic and surgical procedures. Sustainability is a growing concern in the medical industry, and Polyhydroxyalkanoates (PHAs) present an eco-friendly alternative for medical device manufacturing: Biodegradable Properties: PHAs are naturally biodegradable, making them an excellent choice for disposable medical devices. This reduces environmental impact and aligns with the growing demand for sustainable practices in healthcare. Versatile Applications: PHAs can be processed into a variety of forms, including films, fibers, and rigid components, allowing for their use in a wide range of medical applications, from sutures to drug delivery systems. Compatibility with Body Tissues: PHAs exhibit biocompatibility, making them suitable for applications that involve direct contact with biological tissues, such as implants and surgical devices. By incorporating PHAs into precision mold medical applications, manufacturers can create innovative medical devices that not only meet performance standards but also contribute to a more sustainable future. Polypropylene (PP) is another widely used material in the realm of precision mold medical applications. Its unique properties make it an excellent choice for a variety of medical devices and equipment: Polystyrene (PS) is a rigid, transparent thermoplastic that offers a range of benefits for medical device manufacturing: Polycarbonate (PC) is a high-performance thermoplastic that plays a crucial role in medical optics and other precision mold medical applications: Polymethyl Methacrylate (PMMA), commonly known as acrylic, is a transparent thermoplastic frequently used in medical optics and diagnostic applications: Custom blending of polymers enables the creation of materials with specific properties tailored to the needs of medical device manufacturers: Acrylonitrile Butadiene Styrene (ABS) is a tough, impact-resistant material that is widely used in medical devices: Polyethylene (PE) is a versatile polymer used extensively in medical applications, particularly in devices requiring flexibility and chemical resistance: Polyethylene Terephthalate (PET) is a strong, durable material with excellent chemical resistance, often used in medical applications that require both strength and transparency:Cyclic Olefin Polymer (COP)
Cyclic Olefin Copolymer (COC)
Polyhydroxyalkanoates (PHAs)
Polypropylene (PP)
Chemical Resistance: PP has exceptional resistance to a wide range of chemicals, including acids, bases, and solvents, making it ideal for medical applications where exposure to various substances is common.
Thermal Stability: This material can withstand high temperatures, making it suitable for sterilization processes like autoclaving without degrading.
Durability: PP is highly durable and resistant to wear, which ensures that medical devices made from this material maintain their performance over time.
Versatility in Molding: The material can be molded into complex shapes, which makes it useful for various medical products, such as syringes, lab equipment, and drug delivery systems.
Biocompatibility: Polypropylene is biologically inert, which minimizes any adverse reactions when used in contact with the human body, making it safe for medical applications.Polystyrene (PS)
High Clarity: PS is highly transparent, making it ideal for applications where clear visibility is essential, such as diagnostic trays and laboratory testing equipment.
Ease of Molding: Due to its simple processing capabilities, PS can be easily molded into complex shapes, enabling the production of disposable medical devices and instruments.
Low Cost: PS is relatively inexpensive compared to other materials, making it a cost-effective option for disposable medical products, such as test tubes and petri dishes.
Brittleness: While PS provides excellent optical clarity, it is prone to brittleness under stress, limiting its use in high-impact medical applications.
Sterilization Compatibility: It can be sterilized using autoclaving, ensuring its reliability in clean and controlled medical environments.Polycarbonate (PC)
Optical Clarity: PC offers exceptional light transmission, making it suitable for lenses used in diagnostic instruments and surgical tools where high-quality imaging is essential.
Impact Resistance: PC is known for its superior impact resistance, which is vital for medical devices exposed to physical stress or those in active surgical environments.
Thermal Stability: The material can withstand high temperatures without deforming, making it ideal for sterilization and use in various medical procedures.
Design Flexibility: Polycarbonate can be molded into complex shapes and intricate designs, enabling the creation of advanced medical components like diagnostic lenses and surgical instruments.
Biocompatibility: It is biocompatible, ensuring safe interaction with the human body, which is critical for medical implants and devices.Polymethyl Methacrylate (PMMA)
Excellent Optical Clarity: PMMA is valued for its high optical clarity, ensuring that medical devices like lenses and endoscopes provide precise imaging.
Lightweight: The material is lighter than other optical materials, making it ideal for lightweight medical devices and tools.
Shatter Resistance: While it is less impact-resistant than polycarbonate, PMMA is more resistant to breaking than glass, making it a safer option for lenses in medical instruments.
Ease of Processing: PMMA is easy to mold into complex shapes, which allows for the creation of sophisticated optical systems.
Sterilization: It is compatible with common sterilization techniques, such as autoclaving, ensuring that devices made from PMMA remain safe for medical use.Custom Blending
Optimized Material Properties: By blending different materials, manufacturers can optimize the properties of the polymer, such as improving flexibility, impact resistance, or chemical resistance.
Design Flexibility: Custom blends allow for the production of complex medical device components that require specific characteristics that cannot be achieved with a single material.
Cost Efficiency: By combining cheaper base materials with higher-performance additives, custom blends can offer cost-effective solutions for high-performance medical devices.
Thermal and Chemical Resistance: Blends can be tailored to improve performance in extreme conditions, such as exposure to high temperatures or harsh chemicals.
Biocompatibility: Custom blends can also be designed to meet strict medical standards for biocompatibility, ensuring patient safety.Acrylonitrile Butadiene Styrene (ABS)
High Impact Resistance: ABS is known for its strength and impact resistance, making it suitable for durable medical device housings, such as for diagnostic equipment.
Chemical Resistance: ABS can withstand exposure to many chemicals, making it suitable for devices used in environments where chemical resistance is important.
Ease of Processing: ABS can be easily molded into complex shapes, allowing for the efficient production of medical devices with intricate designs.
Non-Transparent: While ABS is excellent for structural components, it is not ideal for applications where optical clarity is required, such as lenses or optical systems.
Durability: ABS is highly durable and resistant to wear and tear, which ensures a long service life for medical devices made from this material.Polyethylene (PE)
Flexibility: PE is highly flexible, making it ideal for medical devices like catheters, surgical gloves, and flexible tubing.
Chemical Resistance: PE is resistant to many chemicals, ensuring that medical devices made from this material will not degrade when exposed to substances commonly found in clinical settings.
Moisture Resistance: The material is highly resistant to moisture, which is important for maintaining the integrity of medical devices like syringes and drug delivery systems.
Biocompatibility: Polyethylene is safe for contact with the human body, making it a reliable material for a wide range of medical applications, from implants to disposable medical products.
Sterilization: PE can withstand common sterilization methods such as gamma radiation, autoclaving, and ethylene oxide, making it ideal for use in sterile environments.Polyethylene Terephthalate (PET)
Strength and Durability: PET is known for its high strength, which makes it ideal for applications where structural integrity is essential, such as in medical tubing and implantable devices.
Transparency: The material’s transparency allows for clear visibility in medical products like blood bags, diagnostic containers, and IV solutions.
Chemical Resistance: PET is resistant to many chemicals and solvents, ensuring that it remains stable even in environments exposed to harsh chemicals.
Sterilization Compatibility: PET can undergo sterilization processes without degrading, which is important for ensuring the safety and effectiveness of medical devices.
Lightweight: PET is lighter than many other materials, making it a preferred choice for applications like medical packaging where weight is a concern.
Examples of Precision Mold Medical Applications in Medical Devices
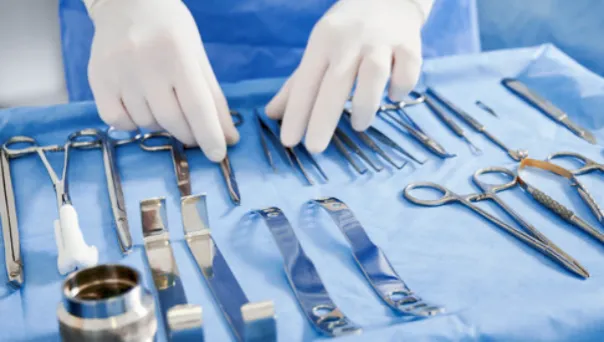
Precision mold medical processes are essential in the manufacturing of a wide range of medical devices. These advanced molding techniques ensure high levels of accuracy, consistency, and quality, which are crucial in the healthcare industry. Below are some key examples of medical devices that benefit from precision molding:
1. Dental Instruments
Precision molding is extensively utilized in the production of dental instruments, such as scalers, forceps, and impression trays. These tools must be manufactured to exact specifications to ensure their effectiveness during dental procedures. The use of precision molds allows for the creation of ergonomic designs that improve the comfort and functionality of the instruments, ultimately enhancing the patient experience.
2. Implants Medical implants, including orthopedic screws, plates, and joint replacements, are critical components in various surgical procedures. Precision mold medical techniques are vital for manufacturing these implants with the necessary mechanical strength and dimensional accuracy. This precision ensures that the implants fit securely within the body and perform reliably over time, contributing to successful surgical outcomes. 3. Prosthetics The manufacturing of prosthetic limbs and devices heavily relies on precision molding. Custom-fit prosthetics require intricate designs tailored to each patient’s anatomy. Precision molding allows for the production of lightweight, durable components that enhance the comfort and functionality of the prosthetic devices, significantly improving the quality of life for users. 4. Medical Instruments A variety of medical instruments, such as syringes, pipettes, and diagnostic tools, are produced using precision molding techniques. These instruments require high levels of accuracy to ensure proper dosing and reliable performance. The consistency achieved through precision mold medical processes helps maintain the safety and effectiveness of these essential tools. 5. Pacemaker Parts Pacemakers are critical devices used to regulate heartbeats, and their components must be manufactured to exacting standards. Parts such as housings, leads, and connectors require precision molding to ensure reliability and safety. The high-quality manufacturing provided by precision molding contributes to the overall performance and effectiveness of pacemakers. 6. Surgical Equipment Surgical instruments, including scalpels, scissors, and forceps, benefit significantly from precision molding. The accuracy and consistency of molded components, such as medical precision components, ensure that surgical tools perform reliably during operations, reducing the risk of complications. High-quality surgical equipment is essential for successful patient outcomes, making precision molding a vital aspect of medical device manufacturing. 7. Catheters Catheters, used for various medical applications such as drainage and drug delivery, require precision molding to achieve consistent diameters and smooth surfaces. These characteristics are crucial for ensuring patient comfort and the effectiveness of the procedure. Precision mold medical techniques allow manufacturers to produce catheters that meet strict regulatory standards. 8. Needles Precision molding is critical in the production of needles, including syringes and hypodermic needles. Each needle must be manufactured with a sharp point and precise dimensions to ensure accurate medication delivery. The high level of precision achieved through molding techniques enhances the safety and reliability of these vital medical devices. 9. Orthopedic Devices Precision molding is widely used in the orthopedic field for creating various components, such as joint replacements and surgical guides. The ability to produce parts with intricate designs and tight tolerances is essential for ensuring that orthopedic devices function correctly and provide the necessary support and stability to patients. 10. Precision Molded Housing Precision molded housing is essential in the medical industry for protecting sensitive electronic and mechanical components in devices such as diagnostic equipment, surgical instruments, and medical imaging systems. The ability to create custom, durable, and accurate housings through precision molding ensures that these devices function reliably in critical environments. Precision molding allows for tight tolerances and specific material properties, such as impact resistance, thermal stability, and biocompatibility, ensuring that the housing protects internal components while withstanding sterilization processes, exposure to chemicals, and physical wear. These molded housings help enhance the safety, performance, and longevity of medical devices. 11. Laboratory Consumables Laboratory consumables are another key application of precision mold medical. Items like pipettes, test tubes, vials, and petri dishes require exact dimensions, surface smoothness, and biocompatibility to perform accurately in scientific testing and medical diagnostics. Precision molding enables the high-volume production of these disposable items with tight tolerances, ensuring consistency in laboratory procedures. Additionally, the ability to use various materials, such as polypropylene or polystyrene, helps meet specific needs for chemical resistance, clarity, and strength, ensuring the consumables maintain their integrity during use in laboratory settings. 12. Diagnostic Test Kits Diagnostic test kits rely heavily on precision mold medical techniques to ensure that all components, from reagent containers to sample collection tools, meet stringent quality standards. Precision molding allows for the accurate production of intricate parts such as microfluidic channels, chambers for sample collection, and small components for test strips, ensuring the functionality and reliability of diagnostic kits. With the ability to mold complex shapes and integrate different materials, precision molding ensures that diagnostic test kits are not only accurate but also easy to use and sterile. This level of precision is essential for delivering fast, reliable test results in medical environments.
The Importance of Precision Mold Medical for Medical Devices
The process of precision molding for medical devices is a crucial step in the development of items that are utilized across a diverse array of healthcare settings, including clinics, hospitals, laboratories, research facilities, and educational institutions. In an industry where the stakes are high and the margin for error is minimal, the significance of precision mold medical practices cannot be overstated.
Ensuring Compliance with Industry Standards
The medical industry mandates strict adherence to tolerances, quality control measures, and routine assurance reviews. These standards are not just regulatory requirements; they are essential for safeguarding patient safety and ensuring the efficacy of medical devices. Precision mold medical techniques enable manufacturers to produce components that meet these rigorous specifications, minimizing the risk of defects and ensuring that every part functions as intended.
Enhancing Product Reliability
Medical devices often operate in critical situations where failure can lead to severe consequences. Precision molding is vital in creating reliable components, such as surgical instruments, implants, and diagnostic tools. The ability to manufacture parts with tight tolerances ensures that these devices perform consistently under various conditions. This reliability is paramount in maintaining the trust of healthcare professionals and patients alike.
Streamlining Production Processes
Precision mold medical practices also streamline production processes, allowing for high-volume manufacturing without compromising quality. By using advanced molding techniques, manufacturers can achieve greater efficiency, resulting in faster turnaround times and reduced costs. This is particularly important in the medical sector, where timely delivery of products can impact patient care and treatment outcomes.
Supporting Innovation in Medical Technology
As medical technology continues to evolve, the demand for innovative devices grows. Precision molding facilitates the creation of complex geometries and intricate designs that are often required for modern medical applications. With the ability to incorporate new materials and manufacturing techniques, precision molding supports the development of cutting-edge medical devices that improve patient outcomes.
Let’s Create Great Things—Get a Quote Today
Contact our professional team now for a same-day quote and risk-free project evaluation. Benefit from ISO 8 cleanrooms, advanced machines, and 12-hour fast response in medical injection molding.
Innovative Mold Design to Ensure Precision Mold Medical Longevity
Optimizing a mold design for injection molding is vital to the overall success of any device, whether it is for medical applications or other industries. In the realm of precision mold medical manufacturing, selecting key elements such as gate location, runner system design, ejection method, and cooling technique is essential not only for the longevity of the mold but also for ensuring the quality of the final part.
Gate Location: The placement of the gate influences the flow of plastic into the mold cavity and significantly impacts the part’s appearance and structural integrity. In precision mold medical applications, careful consideration of the gate location can help minimize flow marks, reduce cycle time, and enhance the overall finish of the component. Runner System Design: The runner system is responsible for directing molten plastic from the injection unit to the mold cavities. An efficient runner design is crucial for achieving uniform fill rates and minimizing waste. For medical devices, where consistency and precision are paramount, an optimized runner system can enhance the mold’s longevity and the quality of the molded parts. Ejection Method: Selecting the appropriate ejection method is critical to prevent damage to the mold and the final product. Precision mold medical applications often require gentle ejection techniques to avoid distorting delicate components. Incorporating features like ejector pins or plates can facilitate smooth part removal while maintaining the integrity of the mold. Cooling Technique: Effective cooling is essential for maintaining a consistent mold temperature, which in turn affects the cycle time and dimensional accuracy of the medical parts mold. In precision mold medical manufacturing, utilizing advanced cooling techniques, such as conformal cooling channels, can enhance the mold’s performance and extend its lifespan. Gating and runner sizing are critical aspects of mold design that directly influence the efficiency and effectiveness of the injection molding process. Properly sized gates and runners ensure that the plastic flows smoothly into the mold cavity, reducing pressure loss and ensuring consistent filling. Gate Sizing: The size of the gate must be carefully calculated to balance the need for rapid filling with the requirement for controlled flow. A gate that is too small may restrict flow, leading to incomplete parts, while one that is too large can create excess material that must be trimmed post-production. Runner Sizing: Similar to gating, the runner size must be optimized for the specific material being used and the design of the part. An appropriately sized runner minimizes the amount of plastic waste and contributes to efficient mold operation, which is especially important in the production of precision mold medical components.Key Considerations in Mold Design
The Importance of Gating and Runner Sizing
Steel Selection and Advanced Machining for Precision Mold Medical Fabrication
Steel Selection for Precision Mold Fabrication
The selection of steel for precision mold fabrication is critical for ensuring the performance, longevity, and quality of molds used in medical device manufacturing. Key factors influencing steel selection include:
Project Complexity: Intricate mold designs often require high-strength steel that can withstand the stresses of detailed machining and extended production runs, ensuring accuracy and reliability.
Annual Production Volume: High-volume production necessitates tougher, more durable steel to resist wear and deformation. In contrast, lower volume production may allow for less expensive, softer steels that are easier to machine but may not provide the same longevity.
Abrasion Resistance: The abrasiveness of the resin used can significantly affect mold wear. Selecting a steel with good abrasion resistance ensures that molds remain effective over time, particularly with materials like glass-filled or carbon-filled resins.
Corrosion Resistance: Medical devices often encounter bodily fluids or sterilizing agents, making corrosion resistance an important factor. Using stainless steels or specially treated alloys can enhance mold lifespan and maintain integrity.
Understanding Resin Behavior
Understanding the behavior of various resins is crucial for informed steel selection:
Polymer Compatibility: Different polymers interact uniquely with different metals. Knowledge of these interactions helps prevent issues like sticking, excessive wear, or chemical degradation of the mold.
Thermal Properties: The thermal behavior of the resin during molding can impact steel selection. Materials that expand significantly when heated may require more robust steel to prevent warping or cracking.
Advanced Machining Considerations
Choosing the right materials and employing advanced machining techniques are fundamental to the success of precision mold medical components. Common materials and techniques include:
Material Selection:
Steel Alloys: Tool steels like D2 or H13 are favored for their hardness and wear resistance, suitable for high-volume production.
Aluminum Alloys: Lightweight and easy to machine, aluminum molds are ideal for prototyping and low-volume production.
Specialty Alloys: Used for applications requiring high corrosion resistance to ensure mold longevity.
Precision Machining Techniques:
CNC Machining: Allows for high-precision cutting and shaping of mold components, producing complex geometries with repeatable accuracy.
EDM (Electrical Discharge Machining): Ideal for intricate features and fine details in hard materials, producing complex cavities required in medical mold.
Surface Grinding: Ensures smooth and dimensionally accurate mold surfaces, critical for performance and sterility in medical applications.
Tolerances and Quality Control
Adhering to tight tolerances is paramount in precision mold fabrication:
Dimensional and Geometric Tolerances: Understanding acceptable tolerances for mold components ensures proper fit and function of molded parts.
Quality Control Measures: Rigorous quality control throughout the machining process includes:
In-Process Inspection: Regular inspections during machining to identify deviations early.
Final Inspection and Testing: Comprehensive checks to verify compliance with tolerances and specifications, including dimensional checks and functional testing.
Post-Machining Considerations
Once the mold is fabricated, additional considerations include:
Surface Treatments: Applying treatments such as hardening, coating, or polishing can enhance mold performance and longevity by reducing wear and improving release properties.
Assembly and Integration: If the mold is part of a larger system, ensuring seamless functionality with other components is essential during the machining process.
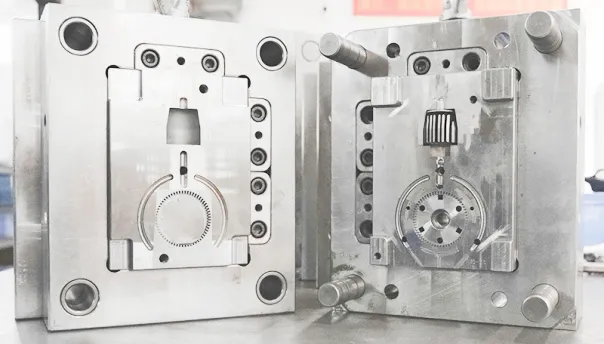
Considerations When Purchasing Precision Medical Molds
Purchase Precision Mold Medical is a specialized service or product offering focused on the acquisition of high-precision molds designed for the medical industry. These molds are critical for manufacturing medical components and devices that require exceptional accuracy, repeatability, and compliance with stringent regulatory standards. Below is a detailed description of what Purchase Precision Mold Medical entails, its importance, and the benefits it provides to the medical manufacturing sector.
Selecting A Supplier for Precision Medical Molds
When selecting a supplier or manufacturer for precision medical molds, consider the following factors:
Expertise and Experience
- Choose a supplier with a proven track record in designing and manufacturing molds for the medical industry.
- Look for experience with materials and processes specific to medical applications.
Certifications
- Ensure the supplier complies with relevant standards such as ISO 13485 and ISO 9001.
Design and Engineering Support
- A good supplier will offer Design for Manufacturability (DFM) services to optimize mold designs for efficiency and performance.
- Prototyping and testing capabilities are essential for validating mold designs before full-scale production.
Material and Tooling Quality
- Verify that the supplier uses high-quality materials and advanced tooling technologies to create durable and precise molds.
Cleanroom Capabilities
- For medical applications, molds should be produced and maintained in cleanroom environments to prevent contamination.
The Purchase Process for Precision Medical Molds
The process of purchasing precision medical molds typically involves the following steps:
- Requirement Analysis: Define the specifications, including part design, material, volume, and regulatory requirements.
- Supplier Selection: Evaluate potential suppliers based on their expertise, certifications, and capabilities.
- Design and Prototyping: Collaborate with the supplier to design the mold and create prototypes for testing.
- Tooling and Production: Once the design is finalized, the mold is manufactured and tested for performance.
- Quality Assurance: Conduct rigorous quality checks to ensure the mold meets all specifications and standards.
- Delivery and Support: Receive the mold and ongoing technical support for maintenance and optimization.
Purchase Precision Mold Medical represents a critical step in the production of advanced medical devices and components. By investing in high-quality, custom-designed molds, manufacturers can ensure the precision, consistency, and compliance required for medical applications. Partnering with an experienced and certified supplier is key to achieving success in this highly specialized field. Whether you are producing surgical instruments, implantable devices, or diagnostic equipment, precision medical molds are the foundation of innovation and quality in the medical manufacturing industry.
What is the Difference Between Conventional and Precision Mold Medical Injection Molding
Injection molding is a widely used manufacturing process for producing a variety of plastic components. However, there are distinct differences between conventional injection molding and precision injection molding, particularly when it comes to applications in the medical field.
Conventional Injection Molding
Conventional injection molding is a standard technique employed to create plastic parts of various shapes, sizes, and complexities. The process involves several key steps:
Melting the Plastic: Plastic pellets are heated until they melt into a viscous liquid.
Injecting into the Mold: The molten plastic is injected into a mold cavity, where it cools and solidifies, taking on the shape of the mold.
Ejection: Once the plastic has cooled and hardened, the part is ejected from the mold.
This method is suitable for a wide range of applications, from simple parts to more complex designs, and is often used in industries like consumer goods, automotive, and general manufacturing. However, conventional injection molding typically allows for looser tolerances and may not always meet the stringent requirements of specialized applications, such as those found in the medical sector.
Precision Injection Molding
Precision medical injection molding, on the other hand, is a specialized form of injection molding that focuses on producing components with extremely tight tolerances and high levels of accuracy. This process is particularly critical in precision mold medical applications, where the quality and performance of parts can significantly impact patient safety and device efficacy.
High-Quality Mold Materials: Precision molding requires the use of high-quality, durable mold materials that can maintain their shape and integrity under rigorous production conditions. This ensures that cavity dimensions are accurate and consistent.
Advanced Machinery: The machinery used in precision molding is typically more advanced than that used in conventional methods. This equipment is capable of maintaining tighter control over the injection process, which is vital for achieving the desired precision.
Skilled Operators: Achieving the high precision necessary in this process demands skilled operators who understand the intricacies of both the materials and the machinery involved. Their expertise is crucial in managing the process and ensuring that tolerances are met.
Key Differences
The primary difference between conventional and precision injection molding lies in their tolerance levels:
Tolerance Levels: Conventional injection molded parts typically have tolerances of approximately ±0.005 inches. This level of accuracy is suitable for many applications but may not be sufficient for critical medical devices. In contrast, precision molded parts require tolerances between ±0.002 inches and ±0.001 inches, or even less in some cases, making them ideal for applications where precision is paramount, such as in precision mold medical components.
Applications: While conventional injection molding can produce a wide range of products, precision medical injection molding applications are specifically designed for that require a high degree of accuracy and reliability. This includes medical devices like implants, surgical instruments, and diagnostic equipment, where even the smallest deviation can lead to significant issues.
FAQs about Precision Mold Medical
What is better than injection molding?
While injection molding is an effective and widely used manufacturing method, there are alternative processes that may be better suited for specific applications depending on the requirements. For instance, blow molding is often preferred for producing hollow parts, such as bottles and containers, because it can create lightweight structures with uniform wall thickness.
3D printing is another alternative that may be better for low-volume production or rapid prototyping. This additive manufacturing technique allows for complex designs to be created without the need for expensive molds, making it a cost-effective solution for testing new concepts or producing customized items.
Compression molding may also be more suitable for certain applications, especially when working with thermosetting plastics or rubber materials, as it can produce larger parts without the need for high-pressure injection.
Ultimately, the best manufacturing process depends on various factors, including production volume, material requirements, part complexity, and cost considerations. Each method has its strengths and weaknesses, and manufacturers should evaluate these factors to determine the most appropriate method for their specific needs.
What is one disadvantage of injection molding?
One significant disadvantage of injection molding is the high initial cost associated with mold design and fabrication. Creating precision molds can require substantial investment in both time and resources. The mold-making process itself can take several weeks or even months, depending on the complexity of the design. This upfront cost can be a barrier for small businesses or startups that are looking to produce low volumes of products.
Moreover, once a mold is created, any modifications or adjustments can be costly and time-consuming. This inflexibility can pose challenges when product designs need to change after the mold has been manufactured, leading to potential delays and additional expenses.
Another disadvantage is that injection molding may not be cost-effective for low-volume production runs due to the high setup costs associated with mold creation. As a result, manufacturers must carefully assess their production needs and determine whether injection molding is the right choice for their specific applications.
Why is injection molding better than compression molding?
Injection molding is often considered superior to compression molding for several reasons, particularly when it comes to producing high volumes of intricate parts. One of the primary advantages of injection molding is its ability to create complex geometries and fine details with high precision. The injection molding process involves injecting molten material into a mold under high pressure, allowing for excellent control over the material flow and ensuring that the mold cavity is filled completely.
In contrast, compression molding involves placing a pre-measured amount of material into an open mold, where it is then heated and compressed to shape it. While compression molding can be effective for larger parts or those made from thermosetting plastics, it may not achieve the same level of detail and precision as injection molding.
Another significant advantage of injection molding is its efficiency in high-volume production. Once the molds are created, injection molding can produce thousands of identical parts in a short period, reducing cycle times and overall production costs. This makes injection molding particularly appealing for manufacturers looking to scale production quickly and cost-effectively.
Furthermore, injection molding can accommodate a broader range of materials, including various thermoplastics, which can be selected based on specific performance characteristics. Overall, while both methods have their applications, injection molding is generally preferred for producing high-precision parts in large quantities.
Why is injection molding so popular?
Injection molding is one of the most widely used manufacturing processes in the world due to its numerous advantages. One of the primary reasons for its popularity is its ability to produce high volumes of parts quickly and efficiently. Once the mold is created, the injection molding process allows for rapid cycles, often producing hundreds or thousands of identical parts within a short time frame.
Another key factor contributing to the popularity of injection molding is its versatility. The process can accommodate a wide range of materials, including various thermoplastics and thermosetting plastics. This material flexibility allows manufacturers to choose materials based on specific performance criteria, such as strength, durability, and resistance to chemicals.
Injection molding also enables the production of complex geometries and intricate designs, which would be challenging to achieve with other manufacturing methods. The precision and consistency of the parts produced through injection molding are crucial in industries such as medical devices, where quality standards are stringent.
Additionally, the high level of automation in injection molding processes reduces labor costs and improves efficiency. As a result, businesses can scale their production to meet market demands while maintaining cost-effectiveness. Overall, the combination of speed, versatility, precision, and cost efficiency makes injection molding a popular choice across various industries.
How much does a mold cost for injection molding?
The cost of an injection mold can vary significantly based on several factors, including the complexity of the part, the size of the mold, the materials used, and the expected production volume. On average, a standard injection mold can range from $1,000 to $100,000 or more. For simple parts with basic geometries, the cost may be on the lower end of this spectrum, while complex designs requiring intricate features, high precision, or multiple cavities can drive costs up substantially.
The initial investment in mold design and fabrication is critical, as high-quality molds are essential for producing parts that meet stringent quality and tolerance requirements. Additionally, factors such as the type of steel or aluminum used in mold construction, surface finishes, and the inclusion of features like cooling channels or automated ejection mechanisms can also influence the final cost.
It’s also important to consider that the mold cost is a one-time expense, and as production volumes increase, the cost per part decreases, making injection molding a cost-effective solution for large-scale manufacturing. Companies should conduct thorough cost assessments and budget accordingly to ensure they are making informed decisions regarding their injection molding projects.
What is the hourly rate for injection molding?
The hourly rate for injection molding can vary based on factors such as the type of machinery used, the complexity of the molding process, and the specific requirements of the job. Generally, the average hourly rate for running an injection molding machine ranges from $50 to $150 per hour. This rate typically includes costs associated with labor, machine operation, maintenance, and overhead expenses.
In addition to the machine’s hourly rate, it’s essential to factor in the cost of materials and the mold itself. Material costs can fluctuate based on the type of plastic or composite being used, which can significantly affect the overall production cost.
For manufacturers, understanding these costs is crucial for pricing their products competitively while ensuring profitability. It’s also advisable for companies to negotiate rates with their molding partners and assess all associated expenses to get a comprehensive understanding of their total manufacturing costs.
What is the lifespan of an injection mold?
The lifespan of an injection mold varies significantly depending on several factors, including the material used for the mold, the complexity of the design, the maintenance performed, and the type of materials being molded. On average, a well-constructed injection mold can last anywhere from 500,000 to several million cycles before requiring repair or replacement.
Molds made from high-quality steel are typically more durable and can withstand more cycles compared to those made from aluminum. However, aluminum molds are often used for shorter production runs and may have a shorter lifespan, averaging around 50,000 to 100,000 cycles.
To maximize the lifespan of an injection mold, it is essential to conduct regular maintenance and inspection. Proper care, such as keeping the mold clean, lubricated, and free from contamination, can significantly extend its operational life. Manufacturers should also consider the specific application and production volume when assessing mold lifespan, as these factors will ultimately influence maintenance strategies and overall costs.
Why are injection molds so expensive?
Injection molds are often considered expensive due to several factors involved in their design, manufacturing, and maintenance. The complexity of the mold plays a significant role in determining its cost. Molds designed for intricate parts with tight tolerances require advanced engineering, specialized materials, and precision machining, all of which contribute to higher costs.
The materials used in mold construction also significantly impact pricing. Molds made from high-quality steel or other durable materials are more costly but offer a longer lifespan and better performance than those made from lower-quality materials. The need for additional features such as cooling channels, hot runner systems, or automated ejection mechanisms further adds to the complexity and cost of the mold.
Additionally, the time required to design and fabricate a mold can be substantial, often taking several weeks or even months to complete. This extended lead time and the expertise required for mold makers result in increased overall costs. Finally, the initial investment in injection molding can be justified by the high volume of parts produced over time, leading to lower costs per unit as production scales up.
How profitable is injection molding?
Injection molding can be a highly profitable business model, especially when producing high volumes of parts. The profitability of injection molding depends on several factors, including production volume, part complexity, material costs, and operational efficiency. When manufacturers can produce large quantities of identical parts, the initial costs associated with mold creation can be spread out, resulting in lower costs per unit and increased profit margins.
Additionally, the ability to create complex and high-quality components makes injection molding appealing to a wide range of industries, including automotive, medical, and consumer products. Companies that can offer value-added services, such as custom designs, rapid prototyping, and high-quality materials, can further enhance their profitability.
However, profitability can also be influenced by market demand, competition, and the efficiency of production processes. Manufacturers must continuously optimize their operations and keep up with industry trends to remain competitive and maximize profit potential. Overall, while the injection molding business can be lucrative, it requires careful management of costs, production processes, and market positioning to achieve sustained profitability.
What is the cost per hour for an injection molding machine?
The cost per hour for operating an injection molding machine can vary significantly depending on several factors, including the type of machine, the complexity of the parts being produced, and the cost of labor and materials. On average, the hourly cost for running an injection molding machine typically ranges from $50 to $150 per hour. This cost generally includes expenses related to machine operation, maintenance, and labor.
More advanced and specialized injection molding machines may incur higher hourly rates due to their capabilities and the technology involved. For instance, machines equipped with features such as robotics or automated processes may have increased operational costs but can also lead to enhanced efficiency and reduced labor costs.
In addition to the machine’s hourly rate, manufacturers should also consider other associated costs, such as material expenses and mold costs. Understanding these costs is crucial for manufacturers to ensure they can price their products competitively while maintaining profitability. By accurately assessing the total operating costs, companies can make informed decisions regarding production volumes and overall manufacturing strategies.
Is casting cheaper than injection molding?
Casting and injection molding are both manufacturing processes used to create parts and components, but their costs can vary significantly based on several factors. Generally, casting can be cheaper than injection molding for certain applications, especially for lower-volume production runs or larger, simpler parts. The initial costs for creating molds in casting processes, such as sand casting or investment casting, are typically lower than those for injection molds, which require precision machining and high-quality materials.
However, when it comes to high-volume production, injection molding usually becomes more cost-effective. Once the initial investment in the mold is made, injection molding can produce parts rapidly and consistently, leading to lower costs per unit as production scales up. This efficiency is particularly beneficial in industries requiring a large number of identical parts, such as automotive or consumer goods.
Ultimately, the decision between casting and injection molding should consider the specific requirements of the project, including production volume, part complexity, and material properties. For large quantities of complex parts, injection molding is often more economical in the long run, while casting may be suitable for simpler designs or lower production needs.
How long does it take to make a mold for injection molding?
The time required to make a mold for injection molding can vary significantly depending on several factors, including the complexity of the design, the type of mold materials used, and the manufacturing capabilities of the mold maker. On average, the process of designing and fabricating an injection mold can take anywhere from a few weeks to several months.
For simple molds with straightforward geometries, the design and production can be relatively quick, often taking around four to six weeks. However, more complex molds that require intricate features, multiple cavities, or advanced cooling systems can extend the timeline significantly. In some cases, the development of highly specialized molds may take three months or longer.
Additionally, the mold-making process includes several steps, such as design, machining, assembly, and testing. Each stage must be executed carefully to ensure that the final mold meets the required specifications and tolerances. Companies aiming for quicker turnaround times may consider working with experienced mold makers who can streamline the process while maintaining quality.
Is injection molding more expensive than 3D printing?
The cost comparison between injection molding and 3D printing largely depends on the specific application and production volume. Generally, injection molding has a higher initial setup cost due to the need for creating molds, which can range from thousands to tens of thousands of dollars, depending on complexity and material requirements. However, once the mold is created, injection molding is highly efficient for large production runs, leading to a lower cost per unit.
On the other hand, 3D printing, or additive manufacturing, has lower upfront costs and can be a cost-effective solution for low-volume production or prototyping. It allows for quick iterations and design changes without the need for expensive molds. However, 3D printing can be less economical for large-scale production, as the cost per part often increases due to longer production times and material expenses.
Injection molding is generally more cost-effective for high-volume production runs, while 3D printing offers flexibility and lower costs for smaller quantities or complex designs. The best choice will depend on the specific requirements, including volume, material, and design complexity.
Is compression molding cheaper than injection molding?
Compression molding can be cheaper than injection molding under certain circumstances, but the cost comparison depends on various factors, including production volume, part complexity, and material type. Compression molding is often used for larger parts or products made from thermosetting plastics and rubber. The initial tooling costs for compression molds are typically lower than those for injection molds, making it a more cost-effective option for low-volume production runs.
However, for high-volume production, injection molding generally becomes more economical. While injection molds require a higher initial investment, they can produce thousands of identical parts quickly and consistently, resulting in lower costs per unit as production scales up.
Compression molding may also involve longer cycle times compared to injection molding, which can affect overall production efficiency. Additionally, injection molding allows for the creation of complex geometries and intricate designs that may be challenging to achieve with compression molding.
What is the medical term for mold?
In the medical context, the term “mold” typically refers to fungal growth, which can occur in damp or humid environments. The term “mycosis” refers to any infection caused by fungi, including molds. Molds produce spores that can become airborne and, when inhaled, may cause allergic reactions or respiratory issues. In medical applications, molds are also used in the creation of medical devices, such as prosthetics and orthodontic appliances, through processes like precision molding. Precision molding in the medical field ensures that these devices fit the patient’s needs with high accuracy and safety.
What is the difference between injection molding and precision molding?
Injection molding is a manufacturing process where molten material (such as plastic or metal) is injected into a mold cavity under pressure to form a product. It’s widely used for producing parts with complex shapes, including medical devices.
Precision molding, on the other hand, refers to injection molding techniques specifically designed to create products with extremely high accuracy and tight tolerances. In the medical field, precision molding ensures that devices meet strict regulatory standards, fit seamlessly, and perform reliably in patient care. This involves advanced technologies and expertise in materials to produce components with minimal variation, such as surgical tools, implants, and diagnostic equipment.
What is the medical test for mold?
There are no specific “medical tests” designed solely to identify mold. However, mold-related illnesses are diagnosed through various methods, such as skin tests or blood tests. A skin test can identify allergies to mold, while a blood test measures the presence of mold-specific antibodies. If a mold-related infection or condition is suspected, doctors may order imaging tests like CT scans or X-rays to assess the damage to lungs or sinuses. Additionally, medical professionals may rely on a patient’s history of exposure to damp or moldy environments when diagnosing mold-related illnesses.
What does black mold smell like?
Black mold, scientifically known as Stachybotrys chartarum, often has a distinctive, musty odor. This smell is due to the volatile organic compounds (VOCs) released by the mold as it grows. The odor is typically described as damp, earthy, or rotting, which may be noticeable in areas with water damage or high humidity. In medical environments, the presence of black mold could indicate a contamination issue in the facility. Mold exposure, especially to black mold, can lead to respiratory problems and other health complications. Therefore, it’s critical for healthcare facilities to prevent mold growth and to address any water damage immediately.
How to detox mold from the body?
Detoxifying mold from the body involves a combination of medical treatments and lifestyle changes. Individuals who have been exposed to mold may experience symptoms of mycotoxicosis, where toxins from mold affect the body. The first step is to eliminate the source of exposure by removing the mold from the environment. Next, treatment may include the use of antifungal medications prescribed by a doctor. Chelation therapy may also be used in some cases to help remove mycotoxins from the bloodstream. Supportive care, such as hydration, a nutritious diet, and supplements that support liver function, may help the body eliminate toxins. It’s essential to consult with a healthcare provider before starting any detox regimen.
How long does mold stay in your system?
Mold itself does not “stay” in the body, but exposure to mold can result in symptoms that persist. The length of time mold-related symptoms last depends on the individual’s sensitivity and the level of exposure. For those with mold allergies or respiratory issues, symptoms like coughing, wheezing, or sinus congestion may resolve within a few days to weeks once exposure is removed. However, for those with chronic exposure or mold toxicity (mycotoxicosis), symptoms can last longer and may require medical intervention. It’s essential to remove mold from the environment to prevent ongoing health issues.
What are signs of mold sickness?
Mold sickness, also known as mold illness or mycotoxicosis, can cause a variety of symptoms, including respiratory problems, skin irritation, fatigue, headaches, and cognitive issues. People with mold allergies may experience more severe reactions, such as asthma exacerbation, coughing, and wheezing. Some individuals may also experience memory loss, dizziness, or difficulty concentrating, commonly referred to as “brain fog.” These symptoms can occur shortly after mold exposure or after prolonged exposure to moldy environments. Individuals with compromised immune systems or chronic respiratory conditions are at higher risk of developing severe symptoms.
Can mold cause a fungal infection?
Yes, mold can cause fungal infections, especially in individuals with weakened immune systems. Molds, including species like Aspergillus, Penicillium, and Candida, can cause infections such as aspergillosis or candidiasis. These infections typically affect the lungs, sinuses, or skin and may cause symptoms like cough, shortness of breath, and skin rashes. Invasive fungal infections may occur when mold spores enter the bloodstream and spread to other parts of the body. In medical settings, precision molds are often used for creating custom prosthetics and orthotics, and ensuring these devices are free from contamination is crucial to preventing infections.
How to tell if mold is behind walls?
To determine if mold is behind walls, start by checking for visible signs of mold or water damage. Look for discoloration, water stains, or a musty odor. If these signs are present, mold could be growing inside the wall. A moisture meter can be used to detect hidden moisture, which may indicate mold growth behind the wall. Additionally, professional mold inspections using thermal cameras or air sampling can help detect mold that isn’t visible to the naked eye. In medical environments, ensuring walls and other surfaces are mold-free is critical to maintaining a safe, sterile environment for patients.
Can mold trigger autoimmune disease?
While mold exposure does not directly cause autoimmune diseases, it may trigger immune responses in sensitive individuals, potentially leading to symptoms similar to autoimmune disorders. Mold exposure, particularly to mycotoxins, can activate the immune system, causing it to attack healthy tissues. In some cases, this may exacerbate or trigger the onset of conditions like rheumatoid arthritis or lupus. However, more research is needed to fully understand the relationship between mold exposure and autoimmune diseases. It’s essential for individuals with autoimmune conditions to minimize mold exposure to reduce the risk of triggering symptoms.
Let’s Create Great Things—Get a Quote Today
Contact our professional team now for a same-day quote and risk-free project evaluation. Benefit from ISO 8 cleanrooms, advanced machines, and 12-hour fast response in medical injection molding.