Prototypes medical molded plastic play a crucial role in the development of innovative medical devices. Prototypes medical molded plastic solutions enable rapid testing, cost-effective production, and superior biocompatibility. These prototypes serve as essential models that allow designers and engineers to test and refine their concepts before mass production. The use of medical molded plastic ensures that the prototypes meet stringent regulatory compliance standards, which is vital for patient safety and industry approval. Additionally, advancements in manufacturing technologies by companies like FUJIU Medical Injection Mold Medical Devices have significantly enhanced the precision and efficiency of producing these prototypes. By leveraging state-of-the-art injection molding techniques, FUJIU Medical Injection Mold Medical Devices facilitates the creation of high-quality prototypes medical molded plastic, driving forward medical device innovation and enabling the swift transition from concept to market-ready products.
Low-Volume to High-Volume Production Capabilities
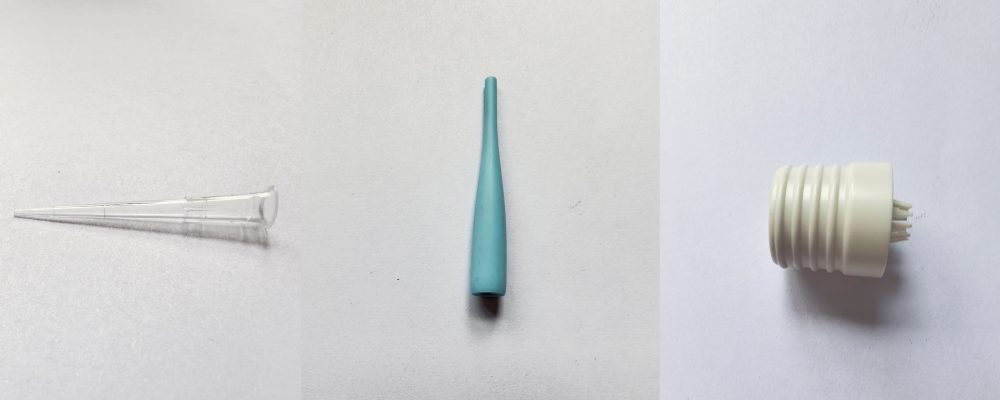
Attributes | Details |
---|---|
Place of Origin | Dongguan, Guangdong, China |
Brand Name | LY Medical Injection Mold |
Product Name | Medical Injection Mold |
Color | Customized Colors |
Certification | ISO9001:2015 |
Service | OEM\ODM |
Plastic Material | ABS/PP/PS/PE/PVC/PA6/PA66.....etc |
Mold Life | 300000~1000000 Shots |
Tolerance | 0.005~0.1mm |
Customized Surface Process | Polishing, Die Custing, Brushing, Anodizing Etc |
Feature | Sustainable |
Selling Units | Single item |
What Are Prototypes Medical Molded Plastic?
Definition and Purpose of Prototypes Medical Molded Plastic
Definition:
Prototypes medical molded plastic are preliminary models of medical devices created using plastic injection molding techniques. These prototypes replicate the design, functionality, and aesthetics of the final product.
Purpose:
- Design Validation: Allow designers to assess the form and fit of the medical device.
- Functionality Testing: Enable engineers to evaluate the operational aspects and performance.
- Regulatory Preparation: Ensure the prototype meets necessary regulatory standards before mass production.
- Stakeholder Feedback: Provide a tangible model for presentations to investors, healthcare professionals, and regulatory bodies.
Types of Prototypes Medical Molded Plastic
Alpha Prototypes
- Description: Early versions used primarily for initial design validation.
- Purpose: Identify major design flaws and make necessary adjustments.
Beta Prototypes
- Description: More refined models that closely resemble the final product.
- Purpose: Conduct extensive testing and gather feedback from a broader audience, including potential users.
Pilot Prototypes
- Description: Finalized prototypes used for small-scale production runs.
- Purpose: Validate manufacturing processes and ensure consistency before full-scale production.
Applications in Product Development, Testing, and Clinical Trials
- Product Development:
- Facilitate iterative design improvements based on real-world testing and feedback.
- Testing:
- Conduct mechanical, chemical, and usability tests to ensure the device meets all specifications and safety standards.
- Clinical Trials:
- Provide a reliable model for clinical evaluations, allowing for the assessment of the device’s effectiveness and safety in real medical settings.
Benefits of Plastic Prototypes in Medical Device Manufacturing
- Cost-Effective Development:
- Reduce expenses by identifying and addressing design issues early in the development process.
- Enhanced Precision:
- Achieve high levels of detail and accuracy, ensuring the prototype closely matches the intended design.
- Faster Time-to-Market:
- Streamline the development process, enabling quicker transitions from concept to market-ready products.
- Regulatory Compliance:
- Ensure prototypes medical molded plastic adhere to stringent medical standards, facilitating smoother regulatory approvals.
- Improved Collaboration:
- Provide a tangible model that enhances communication and collaboration among design teams, engineers, and stakeholders.
By utilizing prototypes medical molded plastic, medical device manufacturers can efficiently navigate the complexities of product development, testing, and regulatory compliance, ultimately leading to the successful introduction of innovative medical solutions.
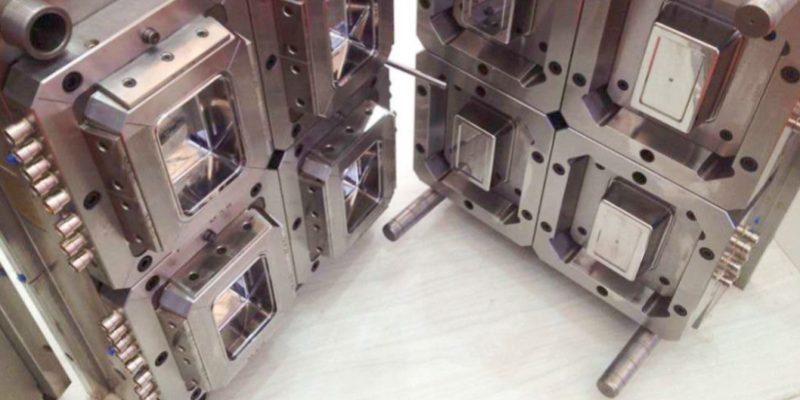
Benefits of Prototypes Medical Molded Plastic in Medical Plastic Manufacturing
Early-Stage Testing to Reduce Risks in Full-Scale Production
- Risk Mitigation:
Prototypes medical molded plastic allow for the early identification of design and functionality issues, minimizing risks before large-scale manufacturing begins. - Performance Validation:
Testing prototypes early ensures that the medical devices perform as intended under real-world conditions, preventing costly recalls and modifications later.
Cost-Effectiveness: Avoiding Expensive Tooling Investments Early On
- Reduced Initial Costs:
Developing prototypes medical molded plastic is significantly more affordable compared to investing in expensive tooling required for mass production. - Efficient Resource Allocation:
Addressing design flaws during the prototyping phase prevents the wastage of resources on flawed designs, ensuring that investments are made wisely.
Improved Designs Through Feedback from Users and Clinical Evaluations
- User-Centric Enhancements:
Gathering feedback from actual users during the prototype stage leads to design improvements that better meet user needs and enhance usability. - Clinical Insights:
Clinical evaluations of prototypes medical molded plastic provide valuable data on the device’s safety and effectiveness, guiding further refinements.
Accelerated Time-to-Market
- Streamlined Development Process:
Prototypes medical molded plastic facilitate quicker iterations and refinements, enabling faster progression from concept to final product. - Responsive Adjustments:
Rapid prototyping allows manufacturers to swiftly incorporate feedback and make necessary adjustments, reducing overall development time.
Enhanced Collaboration and Communication
- Stakeholder Engagement:
Physical prototypes medical molded plastic serve as effective tools for communicating design concepts to stakeholders, including investors and regulatory bodies. - Interdisciplinary Cooperation:
Prototypes foster better collaboration among design teams, engineers, and healthcare professionals by providing a tangible reference point for discussions.
Ensuring Regulatory Compliance
- Standards Adherence:
Prototypes medical molded plastic are designed to meet specific regulatory requirements, simplifying the approval process and ensuring compliance with industry standards. - Comprehensive Documentation:
Using prototypes aids in creating detailed documentation and validation reports necessary for regulatory submissions, facilitating smoother approvals.
By leveraging prototypes medical molded plastic, manufacturers can enhance the quality, safety, and efficiency of medical devices, ensuring successful product launches and compliance with industry standards.
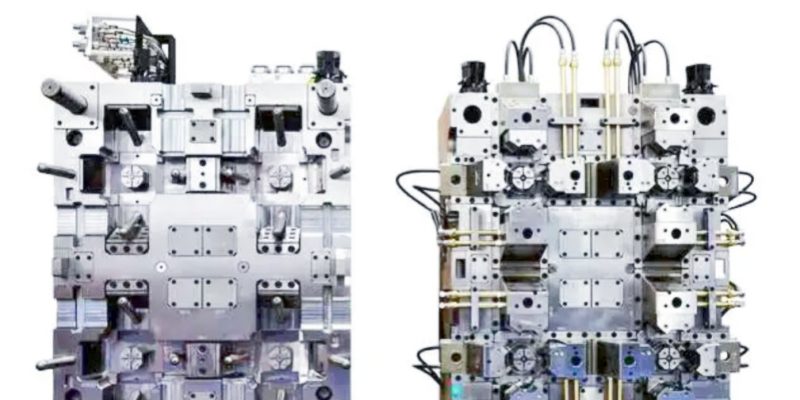
Material Selection of Prototypes Medical Molded Plastic
Material selection for prototypes in medical molded plastics is a critical step in the development of medical devices and components. The chosen materials must meet stringent requirements to ensure safety, functionality, and compliance with regulatory standards. Here’s a detailed look at the factors and considerations involved in material selection for medical molded plastic prototypes:
Biocompatibility
- Definition: Biocompatibility refers to the ability of a material to perform with an appropriate host response in a specific application. For medical devices, this means the material should not cause adverse reactions when in contact with the human body.
- Testing: Materials must undergo rigorous biocompatibility testing according to standards such as ISO 10993 to ensure they are safe for use in medical applications.
Chemical Resistance
- Exposure to Chemicals: Medical devices often come into contact with various chemicals, including disinfectants, drugs, and bodily fluids. The selected material must resist degradation and maintain its properties when exposed to these substances.
- Compatibility: Ensure that the material is compatible with the specific chemicals it will encounter during its lifecycle.
Mechanical Properties
- Strength and Durability: The material must have the necessary strength and durability to withstand the mechanical stresses it will encounter during use. This includes tensile strength, impact resistance, and fatigue resistance.
- Flexibility and Rigidity: Depending on the application, the material may need to be flexible (e.g., catheters) or rigid (e.g., surgical instruments).
Thermal Properties
- Heat Resistance: Medical devices may need to withstand sterilization processes such as autoclaving, which involves high temperatures. The material must maintain its integrity and performance after repeated sterilization cycles.
- Thermal Conductivity: For some applications, thermal conductivity may be a consideration, especially for devices that interact with temperature-sensitive tissues.
Sterilization Compatibility
- Methods: Common sterilization methods include autoclaving, gamma radiation, ethylene oxide (EtO) gas, and electron beam (E-beam) sterilization. The material must be compatible with the chosen sterilization method without degrading or losing its properties.
- Reusability: For reusable devices, the material must withstand multiple sterilization cycles without significant wear or degradation.
Regulatory Compliance
- Standards and Regulations: Materials must comply with relevant regulatory standards such as FDA (Food and Drug Administration) regulations in the U.S., CE marking in Europe, and other international standards.
- Documentation: Ensure that the material supplier provides comprehensive documentation, including material safety data sheets (MSDS), certificates of analysis (CoA), and biocompatibility test reports.
Cost and Availability
- Cost-Effectiveness: While performance and safety are paramount, cost is also a consideration. The material should offer a good balance between performance and cost.
- Supply Chain: Ensure that the material is readily available and that the supply chain is reliable to avoid delays in production.
Aesthetic and Functional Requirements
- Color and Transparency: Some medical devices require specific colors or transparency for functional or aesthetic reasons. For example, transparent materials may be needed for devices where visual inspection is important.
- Surface Finish: The material should allow for the desired surface finish, whether it needs to be smooth, textured, or have specific coatings.
Environmental and Sustainability Considerations
- Environmental Impact: Consider the environmental impact of the material, including its recyclability and the sustainability of its production process.
- Regulatory Trends: Stay informed about regulatory trends and potential restrictions on certain materials due to environmental concerns.
Common Materials Used in Medical Molded Plastic Prototypes
- Polycarbonate (PC): Known for its strength, transparency, and impact resistance. Commonly used in surgical instruments and housings for medical devices.
- Polyethylene (PE): Offers good chemical resistance and is used in applications like tubing and containers.
- Polypropylene (PP): Known for its chemical resistance and sterilizability, used in syringes, IV components, and labware.
- Polyvinyl Chloride (PVC): Widely used in medical tubing and blood bags due to its flexibility and chemical resistance.
- Acrylonitrile Butadiene Styrene (ABS): Offers good impact resistance and is used in housings and enclosures for medical devices.
- Polysulfone (PSU) and Polyethersulfone (PES): High-performance thermoplastics used in applications requiring high thermal and chemical resistance, such as surgical instruments and sterilization trays.
- Silicone: Known for its flexibility, biocompatibility, and temperature resistance, used in catheters, seals, and gaskets.
Selecting the right material for medical molded plastic prototypes involves a comprehensive evaluation of biocompatibility, chemical resistance, mechanical and thermal properties, sterilization compatibility, regulatory compliance, cost, and aesthetic requirements. The chosen material must ensure the safety, functionality, and reliability of the medical device while meeting all regulatory standards and being cost-effective. Proper material selection is crucial for the successful development and commercialization of medical devices.
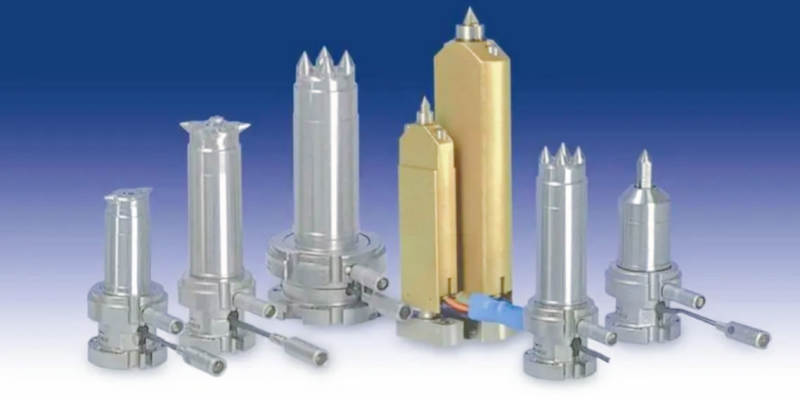
Manufacturing Process for Prototypes Medical Molded Plastic
Common Techniques
- Injection Molding for Production-Ready Parts
- Utilizes high-pressure injection of molten plastic into molds.
- Ideal for creating precise and durable prototypes medical molded plastic.
- Enables mass production once the prototype is finalized.
- Overmolding and Insert Molding for Integrated Designs
- Overmolding:
- Involves molding a secondary material over a primary substrate.
- Enhances functionality and aesthetics of prototypes medical molded plastic.
- Insert Molding:
- Incorporates metal or other materials into the plastic during the molding process.
- Provides added strength and functionality to the prototypes medical molded plastic.
- Use of Advanced Materials like PEEK, Polypropylene, and Silicone
- PEEK (Polyether Ether Ketone):
- Offers high strength and chemical resistance.
- Suitable for demanding medical applications.
- Polypropylene:
- Lightweight and versatile.
- Commonly used for its durability and flexibility in prototypes medical molded plastic.
- Silicone:
- Provides excellent biocompatibility and flexibility.
- Ideal for medical devices requiring soft-touch surfaces.
Example of Process Flow
Material Selection
- Choose appropriate plastics based on device requirements.
- Consider factors like biocompatibility, durability, and flexibility for prototypes medical molded plastic.
Mold Creation
- Design and fabricate molds tailored to the specific prototype design.
- Utilize CAD software for precision in prototypes medical molded plastic.
Injection
- Inject molten plastic into the prepared molds under high pressure.
- Ensure consistent quality and detail in the prototypes medical molded plastic.
Refinement
- Trim and finish the molded prototypes to remove any excess material.
- Conduct quality checks to ensure the prototypes medical molded plastic meet specifications.
Plastic Prototypes in Medical Device Manufacturing
Precision and Accuracy
- High-Quality Standards:
- Plastic prototyping in manufacturing medical devices ensures each component meets exact specifications and tolerances.
- Critical for devices that require precise functionality and reliability.
Material Versatility
- Diverse Material Testing:
- Plastic prototyping in manufacturing medical devices allows for the evaluation of different materials.
- Ensures the final product is both durable and safe for medical use.
Innovation Facilitation
- Encouraging Creativity:
- Plastic prototyping in manufacturing medical devices provides the flexibility to experiment with innovative features.
- Enables designers to explore new functionalities without significant cost implications.
Cost Efficiency
- Reduced Development Costs:
- Plastic prototyping in manufacturing medical devices minimizes the need for expensive tooling early in the development process.
- Helps in identifying and addressing design flaws before large-scale production.
Enhanced Collaboration
- Improved Communication:
- Plastic prototyping in manufacturing medical devices offers a tangible model for teams to discuss and refine designs.
- Enhances collaboration between designers, engineers, and stakeholders.
By following the structured manufacturing process for prototypes medical molded plastic and leveraging plastic prototyping in manufacturing medical devices, manufacturers can achieve high-quality, compliant, and innovative medical devices efficiently.
Key Prototypes Medical Molded Plastic Manufacturers
FUJIU Medical Injection Mold
- Innovation in Prototyping:
At FUJIU Medical Injection Mold, we are an employee-owned, third-generation company with over 20 years of expertise in medical injection molding. Specializing in OEM contract manufacturing for medical devices, we produce high-precision plastic consumables for equipment and diagnostic kits. Our clean room injection molding capabilities ensure that all components are produced in a controlled environment, meeting the highest standards for cleanliness and contamination control. Guided by our visionary President and CEO, Dr. Linda Wu, we operate state-of-the-art facilities, including Class 8 clean rooms, and adhere to ISO 13485, FDA, and global standards to ensure exceptional quality. - Our mission is to combine precision, integrity, and innovation to deliver custom solutions and build strong partnerships with our clients. By understanding and addressing the specific medical molding requirements, we are able to tailor our approach to meet the highest standards of quality and safety. We believe in continuous improvement and fostering collaboration to meet the unique challenges of the medical industry.
- With a foundation of family values and employee empowerment, we stands out as a trusted partner committed to excellence and sustainability in the medical molding sector.
- Comprehensive Material Selection:
We offer an extensive range of materials, including high-performance polymers and specialized plastics, enabling the production of prototype medical equipment molds that meet diverse medical device specifications. Our material expertise ensures durability, biocompatibility, and precision in every prototype. - Advanced Manufacturing Capabilities:
Equipped with the latest medical injection molding machinery and automation technologies, Group efficiently produces prototypes medical molded plastic with superior detail and repeatability. Their streamlined processes reduce lead times and accelerate the prototyping phase. - Collaborative Development:
We fosters close collaboration with clients, providing expert guidance and support throughout the prototyping process. This partnership approach ensures that prototypes medical molded plastic are optimized for performance, regulatory compliance, and market readiness. - Sustainability Initiatives:
Committed to sustainable manufacturing practices, Group integrates eco-friendly materials and processes in the creation of prototypes medical molded plastic, aligning with industry standards for environmental responsibility.
Comprehensive Material Selection. Our company provides an extensive selection of high-performance polymers and specialized plastics. This versatility ensures that prototypes medical molded plastic meet varied requirements such as durability, biocompatibility, and precision, tailored to the unique specifications of medical devices.
Applications of Prototypes Medical Molded Plastic in Medicine
Examples of Medical Devices and Components
Diagnostic Equipment
- Petri Dishes: Utilized in laboratories for culturing microorganisms, prototypes medical molded plastic ensure precision and clarity for accurate diagnostics.
- IVD Devices: In Vitro Diagnostic devices rely on high-quality prototypes medical molded plastic for reliable performance and consistent results in medical testing.
Surgical Tools and Implants
- Surgical Instruments: Prototypes medical molded plastic are used to design and test ergonomic and functional surgical tools, enhancing surgeon efficiency and patient outcomes.
- Orthopedic Implants: Creating prototypes medical molded plastic allows for the development of customized implants that fit perfectly and provide optimal support for patients.
Drug Delivery Systems
- Insulin Pumps: Prototypes medical molded plastic enable the design and testing of user-friendly insulin pumps, ensuring accurate dosage delivery and ease of use for diabetic patients.
- EpiPens: Developing prototypes medical molded plastic for EpiPens ensures reliability and quick response in emergency situations, enhancing patient safety.
Medical Tubing for Fluid Transport
- IV Lines: Prototypes medical molded plastic are essential in creating flexible and durable IV lines that ensure smooth and safe fluid transport in medical settings.
- Catheters: Designing prototypes medical molded plastic for catheters ensures they are biocompatible and effective for long-term use in various medical procedures.
Plastic Prototyping in Manufacturing Medical Devices
Precision Design
- Exact Specifications:
Plastic prototyping in manufacturing medical devices ensures that each component of the prototype meets precise design specifications, which is critical for the functionality and safety of medical devices. Plastic prototypes in medical device manufacturing ensure that each component meets exact specifications and tolerances, which is crucial for medical applications. The use of precision mold medical techniques allows for the production of highly accurate prototypes, ensuring that every detail aligns with the stringent requirements of the healthcare industry.
Material Testing
- Durability and Safety:
Plastic prototyping in manufacturing medical devices allows for extensive testing of different materials to ensure that the final product is both durable and safe for medical use.
Rapid Iteration
- Quick Design Changes:
Plastic prototyping in manufacturing medical devices facilitates rapid iterations, enabling designers to quickly implement and test design changes based on feedback and testing results.
Cost Efficiency
- Minimized Material Waste:
Plastic prototyping in manufacturing medical devices helps reduce costs by minimizing material waste through efficient design and testing processes, ensuring that resources are used effectively. By utilizing high quality medical plastic parts during the prototyping phase, manufacturers can also ensure the durability and performance of the final product, further optimizing production and reducing the likelihood of costly revisions.
User-Centric Development
- Enhanced Usability:
Plastic prototyping in manufacturing medical devices allows for the creation of user-friendly designs by incorporating feedback from healthcare professionals and end-users during the prototyping phase. A medical plastic molding trader plays a key role in providing the necessary materials and expertise to ensure that these prototypes meet the specific requirements for functionality, safety, and regulatory compliance. This collaboration helps refine the designs and bring them closer to the final product.
Regulatory Compliance
- Standards Adherence:
Plastic prototyping in manufacturing medical devices ensures that prototypes meet necessary regulatory standards, facilitating smoother approval processes and compliance with industry regulations.
By leveraging prototypes medical molded plastic in various applications within the medical field, manufacturers can enhance the design, functionality, and reliability of medical devices. Additionally, integrating plastic prototyping in manufacturing medical devices streamlines the development process, ensuring that products are safe, effective, and ready for market introduction.
Why are Prototypes Medical Molded Plastic important
Prototypes in medical molded plastics are crucial for several reasons, particularly in the development and manufacturing of medical devices and components. Here’s a detailed explanation of their importance:
Design Validation
- Functionality Testing: Prototypes allow engineers and designers to test the functionality of a medical device or component before mass production. This ensures that the design meets the intended purpose and performs as expected in real-world scenarios.
- Ergonomics and Usability: Medical devices often need to be user-friendly, especially for healthcare professionals who may use them frequently. Prototypes help in assessing the ergonomics and usability, ensuring that the device is comfortable and easy to handle.
Material Selection
- Biocompatibility: Medical devices must be made from materials that are biocompatible, meaning they do not cause adverse reactions when in contact with the human body. Prototyping allows for the testing of different materials to ensure they meet regulatory standards and are safe for use.
- Durability and Strength: Different medical applications require different material properties. Prototypes help in evaluating the durability, strength, and flexibility of the materials used, ensuring they can withstand the stresses of their intended use.
Regulatory Compliance
- Testing and Certification: Medical devices must comply with stringent regulatory standards (e.g., FDA in the United States, CE marking in Europe). Prototypes are essential for conducting the necessary tests and obtaining certifications before the product can be marketed.
- Documentation: Prototyping helps in creating detailed documentation that regulatory bodies require, including design specifications, material data, and test results.
Cost Efficiency
- Identifying Design Flaws Early: Prototyping helps in identifying and rectifying design flaws early in the development process, which can save significant costs that would otherwise be incurred if the flaws were discovered during mass production or after the product launch.
- Reducing Waste: By refining the design through prototypes, manufacturers can minimize material waste and optimize the production process, leading to cost savings.
Stakeholder Communication
- Demonstrating Concepts: Prototypes provide a tangible representation of the product, making it easier to communicate the design and functionality to stakeholders, including investors, healthcare professionals, and regulatory bodies.
- Feedback Collection: Prototypes allow for the collection of feedback from potential users and stakeholders, which can be used to make iterative improvements to the design.
Speed to Market
- Rapid Iteration: Prototyping enables rapid iteration and testing of different design concepts, accelerating the development process and reducing the time to market.
- Parallel Development: While the prototype is being tested and refined, other aspects of the product development, such as packaging and marketing, can be developed in parallel, further speeding up the overall process.
Customization and Innovation
- Patient-Specific Solutions: In some cases, medical devices need to be customized for individual patients. Prototyping allows for the creation of patient-specific solutions, which can be critical in fields like orthopedics and dentistry.
- Innovative Features: Prototyping encourages innovation by allowing designers to experiment with new features and technologies without the risk of large-scale production failures.
Risk Mitigation
- Safety Testing: Prototypes are essential for conducting safety tests to ensure that the device will not fail in critical situations, thereby mitigating the risk of harm to patients and users.
- Performance Under Stress: Prototypes can be subjected to stress tests to evaluate their performance under extreme conditions, ensuring reliability and safety.
Prototypes in medical molded plastics are indispensable for ensuring that medical devices are safe, effective, and ready for market. They facilitate design validation, material selection, regulatory compliance, cost efficiency, stakeholder communication, speed to market, customization, innovation, and risk mitigation. Without prototyping, the development of reliable and effective medical devices would be significantly more challenging and risky.
FAQs about Prototypes Medical Molded Plastic
Injection molding is a versatile manufacturing process that produces a wide range of medical products with high precision and quality. Many medical devices and components are created using this technique, including syringes, surgical instruments, diagnostic components, and implantable devices. It is also used to manufacture parts for medical imaging equipment, laboratory tools, and personal protective equipment. The reason injection molding is so prevalent in the medical industry is due to its ability to produce complex shapes with stringent dimensional requirements, ensuring the reliability and consistency required for medical applications. The materials used in medical injection molding are often biocompatible plastics, which can withstand sterilization processes and meet the regulatory standards of the healthcare industry. This manufacturing approach not only ensures high-volume production at relatively low costs but also maintains the hygiene and quality needed for medical products.
A medical prototype is an initial version of a medical device or product created to test its design, functionality, and performance before it goes into full-scale production. Prototyping is a critical phase in the medical device development process as it allows designers, engineers, and healthcare professionals to evaluate the device in practice. Through prototyping, stakeholders can identify potential design flaws, usability concerns, and performance issues that may not be apparent during the design phase. This iterative process encourages improvements and refinements based on real-world testing and feedback, ensuring that the final product is safe, effective, and user-friendly. Types of medical prototypes can include 3D-printed models, early-stage injection molded parts, or functional versions built with similar materials intended for the final product. These prototypes are vital for demonstrating compliance with regulatory requirements, such as those set by the FDA, before the product can be brought to market.
A production mold and a prototype mold differ primarily in their purpose, design, and durability—factors that are especially critical when manufacturing medical devices. A production mold is engineered for high-volume, long-term manufacturing. It is typically constructed from hardened tool steels or other durable materials to ensure that the mold can withstand thousands to millions of injection cycles without significant wear. In medical device manufacturing, production molds must meet stringent quality and regulatory standards (such as those from the FDA or ISO) to ensure that each part, whether it is a component of an implantable device or a disposable syringe, is produced with consistent dimensions, biocompatibility, and surface finish. Because the production mold is used continuously over an extended period, even minor imperfections could lead to costly recalls or, worse, adverse patient outcomes.
In contrast, a prototype mold is designed for short-run production or for verifying design concepts in the early stages of product development. Prototype molds are generally made using less expensive materials such as aluminum, which can be machined quickly and modified as design iterations occur. In a medical context, prototype molds allow engineers and clinicians to test the ergonomics, functionality, and biocompatibility of a new device before committing to full-scale production. The rapid turnaround of prototype molds enables iterative testing and design modifications based on clinical feedback or pre-clinical trials. While they may not have the longevity or precision of production molds, prototype molds are indispensable for refining designs, ensuring that the final product meets both technical specifications and regulatory requirements. Overall, the choice between prototype and production molds in medical manufacturing is a balance between speed, cost, quality, and safety.
Molds can generally be classified into three primary categories, which are particularly relevant in the context of medical device manufacturing: prototype molds, short-run (or pre-production) molds, and production molds. First, prototype molds are designed to produce a small number of parts for the purpose of design validation and early-stage testing. In the medical field, these molds allow designers to test the fit, function, and biocompatibility of devices such as surgical instruments, implantable components, or diagnostic tools. The materials used for these molds are typically less expensive and easier to modify, such as aluminum, which offers rapid turnaround despite having a shorter lifespan.
The second category, short-run or pre-production molds, bridges the gap between early prototypes and full-scale production. These molds are often used to produce limited batches of a device for pilot clinical trials or for market testing. In medical manufacturing, short-run molds must meet higher quality and precision standards than prototype molds because the parts produced may be used in clinical settings, albeit in limited quantities. This phase helps ensure that any issues related to manufacturing or device performance can be identified and resolved before large-scale production begins.
Finally, production molds are designed for high-volume, long-term manufacturing. They are engineered to be highly durable and precise, often constructed from hardened tool steels to endure millions of injection cycles. In the medical device industry, production molds must adhere to rigorous regulatory standards and quality controls because any deviation can have serious implications for patient safety and treatment efficacy. The consistent quality and reliability of parts produced from these molds are paramount, as they often form the backbone of life-saving medical devices and diagnostic equipment. By classifying molds into these three categories, manufacturers can choose the appropriate tool for each phase of product development, ensuring safety, functionality, and regulatory compliance in the medical field.
The difference between prototype design and production design lies in their objectives, level of detail, and refinement—factors that are especially crucial when developing medical devices. Prototype design is an early-stage process where engineers and designers create a preliminary version of a product to test and validate ideas. In the medical field, prototypes might include early models of surgical instruments, diagnostic devices, or implantable components. The primary goal of a prototype is to assess functionality, ergonomics, and overall performance. Engineers often use rapid prototyping techniques like 3D printing, CNC machining, or low-volume molding to quickly iterate and refine the design. Feedback from clinicians, regulatory consultants, and even patients can be integrated into successive prototypes to improve safety, usability, and biocompatibility. Because the prototype is not intended for long-term use, materials and manufacturing methods may be less durable or expensive compared to final production models.
On the other hand, production design is the finalized version that has been optimized for mass production. In the medical device industry, production designs are subject to rigorous quality control, detailed engineering tolerances, and compliance with stringent regulatory standards. Production design involves refining the material selection, optimizing the manufacturing process, and ensuring repeatability and consistency. The design is usually adjusted to meet not only the functional requirements but also the cost-effectiveness and efficiency needed for high-volume manufacturing. Safety is paramount in production design; therefore, every component, whether it’s part of a critical life-support system or a disposable testing device, must be manufactured to exact specifications. Moreover, production design includes considerations such as sterilization, shelf life, and the integration of quality assurance measures that are essential for devices used in healthcare settings. Ultimately, while prototype design is about exploration and innovation, production design is about precision, reliability, and regulatory compliance in the delivery of safe medical products.
When it comes to prototyping or low-production molds, particularly for medical devices, material selection is crucial to balance cost, speed, and functionality while meeting biocompatibility and regulatory requirements. For prototypes, engineers often opt for materials such as aluminum for mold construction due to its ease of machining and lower cost compared to hardened tool steels. Aluminum molds are excellent for rapid iterations when developing medical components like housings for diagnostic instruments or ergonomic handles for surgical tools. Additionally, soft tooling materials, including certain types of urethane, are used for low production runs where the volumes are limited, and the focus is on verifying design functionality rather than achieving extended tool life.
For the actual parts produced from these molds, a variety of plastics and resins are commonly employed. Medical-grade polycarbonate, polypropylene, and polyethylene are popular choices because they offer excellent clarity, durability, and chemical resistance, which are important for devices such as IV components, inhalers, or blood storage containers. Thermoplastic elastomers (TPE) may also be used for components requiring flexibility and a soft touch, like seals or grips in surgical instruments. Additionally, stereolithography (SLA) resins or selective laser sintering (SLS) materials are frequently utilized in 3D printing prototypes for devices where fine details and complex geometries are necessary. These materials are chosen for their rapid curing times, precise detail resolution, and, in some cases, biocompatibility certifications.
In a medical context, the materials used for prototyping must not only simulate the performance of final production materials but also allow for sterilization and compatibility with biological tissues when necessary. This is vital when developing devices that come into contact with patients, as they must adhere to stringent health and safety regulations. The ability to quickly switch materials during prototyping enables iterative testing and validation of a device’s performance, ultimately leading to a more robust and reliable production design.
The terms “molded” and “moulded” are fundamentally identical in meaning, with the primary difference being regional spelling conventions. In American English, the word is typically spelled “molded,” while in British English, it is spelled “moulded.” In the context of manufacturing—especially when producing medical devices—the process being described remains the same regardless of spelling. Both terms refer to the method by which materials such as plastics, rubbers, or composites are shaped using a mold, which is a tool that imparts the desired geometry onto the material.
In medical device manufacturing, the process of molding (or moulding) is critically important. For instance, many disposable medical products, such as syringe barrels, IV connectors, or even components of ventilators, are produced using injection molding techniques. Whether the process is documented as “molded” or “moulded” depends on the regional standards and the origin of the documentation, but the quality control, precision, and compliance with health regulations remain consistent. Moreover, the spelling variant does not affect the technical parameters of the process, such as temperature control, pressure, or cycle times, all of which are rigorously defined in the production of medical devices to ensure patient safety.
Furthermore, when collaborating internationally, companies involved in the production of medical devices must be aware of these spelling differences in their technical documentation, regulatory submissions, and quality manuals. Understanding that “molded” in the United States and “moulded” in the United Kingdom or other Commonwealth countries refer to the same process helps in standardizing communication and ensuring that all stakeholders are on the same page regarding manufacturing processes. This clarity is crucial in maintaining the high standards required for medical products, where even minor ambiguities can have significant regulatory implications.
Yes, in the world of injection molding and manufacturing—especially within the medical industry—there is a significant difference between what is considered a “good mold” and a “bad mold.” A good mold is one that has been carefully designed, constructed, and maintained to produce consistent, high-quality parts that meet stringent specifications and regulatory standards. In medical device manufacturing, a good mold is paramount because it directly impacts the performance, safety, and reliability of products that may be used in life-critical applications. For example, a well-designed mold used to produce components for heart valves, insulin pumps, or diagnostic equipment ensures that every part meets precise dimensional tolerances, surface finishes, and material properties necessary for biocompatibility and functionality. These molds are typically built from high-grade tool steels, undergo rigorous quality inspections, and are maintained through a systematic preventive maintenance schedule.
Conversely, a bad mold is one that may have design flaws, improper material selection, or wear and tear that leads to defects in the final product. In medical manufacturing, even minor defects such as surface irregularities, dimensional inconsistencies, or contamination can compromise device performance, potentially resulting in malfunction or adverse patient outcomes. A bad mold can lead to a high rejection rate of parts, increased waste, and additional costs associated with rework or recalls. Additionally, if a mold does not comply with regulatory standards, it could delay product approval, jeopardize patient safety, and tarnish a company’s reputation.
From a broader perspective, the distinction between good and bad molds in medical device production is often determined by the level of precision, repeatability, and reliability that the mold delivers. Manufacturers invest considerable resources in mold design, simulation, and validation to ensure that each tool is optimized for the intended production volume and application. This meticulous process is essential in the medical field, where quality control is not only a business necessity but a regulatory mandate. In summary, the quality of a mold is a critical factor in the overall success of the manufacturing process, and in medical device production, the stakes are particularly high, underscoring the importance of investing in “good molds.”
A product prototype and a virtual prototype serve distinct roles in the product development process, especially in the development of medical devices. A product prototype is a physical, tangible model that represents the design of a device. In the medical field, this could be a physical model of a surgical instrument, an implantable device, or a diagnostic tool. Product prototypes are created to assess the real-world performance, ergonomics, and functionality of a design. They allow engineers and clinicians to perform hands-on evaluations, such as verifying the fit of a prosthetic device or testing the tactile response of a hand-held instrument. Physical prototypes are crucial for usability studies and for meeting regulatory requirements, where the actual material properties, surface finishes, and manufacturing tolerances are evaluated in a clinical or simulated environment.
In contrast, a virtual prototype is a digital representation of the product, typically created using computer-aided design (CAD) software and simulation tools. Virtual prototypes enable engineers to model and analyze the behavior of a device under various conditions without the need for physical fabrication. For medical devices, virtual prototypes can simulate fluid dynamics in a heart valve, stress distribution in an orthopedic implant, or even thermal behavior in diagnostic equipment. The key advantages of virtual prototypes are the speed and cost-effectiveness of iterating designs. They allow for extensive testing and refinement of complex geometries and performance parameters before any physical mold is made.
Both types of prototypes play integral roles in the iterative development process. Virtual prototypes are often used in the early stages to identify potential design issues and optimize performance through simulation and analysis. Once the virtual design is validated, a physical product prototype is produced for hands-on testing, clinical evaluation, and further refinement. In the highly regulated medical field, this dual approach helps ensure that the final product not only meets technical specifications but also adheres to strict safety and efficacy standards required for patient care. Together, virtual and product prototypes streamline the development process, reduce costs, and help accelerate the time-to-market for innovative medical devices.
Prototyping a plastic product, especially for medical applications, involves a multi-step process that balances design innovation, material selection, and compliance with regulatory standards. The first step is conceptualization and design, where engineers use computer-aided design (CAD) software to develop detailed 3D models of the device. For medical devices, these models must incorporate precise dimensions, ergonomic features, and considerations for biocompatibility. Once the design is finalized, the next step is to choose the appropriate prototyping method. Rapid prototyping techniques such as 3D printing (using SLA, SLS, or FDM methods) are popular because they allow for quick fabrication of complex geometries. These techniques enable medical device developers to produce functional prototypes for preliminary testing, such as verifying the fit of a surgical instrument or assessing the ergonomic comfort of a handheld diagnostic tool.
After the initial 3D printed prototype, further refinements might be made based on feedback from clinical experts or usability studies. For more advanced testing, low-volume production molds may be used. In this stage, prototype molds—often made from aluminum—can produce parts that mimic the properties of the final production material. This is particularly important in medical applications where factors like sterilization, chemical resistance, and biocompatibility are critical. Engineers will often test these prototypes for mechanical properties, durability, and performance under simulated clinical conditions.
In parallel with physical prototyping, virtual prototyping and simulation play a key role. Finite Element Analysis (FEA) and Computational Fluid Dynamics (CFD) simulations can predict how the product will behave under stress, pressure, or in contact with bodily fluids, which is vital for devices such as implantable components or fluid delivery systems. Once all testing confirms that the prototype meets both design and regulatory requirements, the product can progress to full-scale production using hardened production molds designed for high-volume manufacturing.
Throughout this process, meticulous documentation is maintained to ensure that every change complies with medical regulatory standards. The iterative approach of prototyping not only refines the design but also helps identify potential issues early in the development cycle, ensuring that the final product is safe, effective, and ready for clinical use.
Plastics can be formed using several techniques, and in the realm of medical device manufacturing, four primary methods are widely recognized: injection molding, compression molding, blow molding, and thermoforming. Each method offers unique advantages and is selected based on the specific requirements of the device being produced.
Injection Molding: This is perhaps the most common method for manufacturing high-precision plastic parts. In injection molding, melted plastic is injected into a mold cavity under high pressure. For medical devices, injection molding is used to produce components such as housings for electronic devices, components of surgical instruments, or even parts of diagnostic equipment. The process is highly repeatable and allows for intricate details and tight tolerances, which are crucial in medical applications.
Compression Molding: In compression molding, a pre-measured amount of plastic material, often in the form of a powder or preform, is placed into an open, heated mold cavity. The mold is then closed with a top plug, and pressure is applied to shape the plastic. This method is particularly useful for producing large, complex shapes and is used in manufacturing components like seals or gaskets that are critical in medical devices such as ventilators or infusion pumps.
Blow Molding: Blow molding is primarily used to create hollow plastic parts, such as bottles or containers. In the medical industry, blow molding is often employed for manufacturing items like IV bags, blood storage containers, and certain types of diagnostic equipment housings. The process involves inflating a heated plastic tube within a mold until it conforms to the shape of the cavity, ensuring uniform wall thickness and a seamless finish.
Thermoforming: Thermoforming involves heating a plastic sheet until it becomes pliable, then forming it over a mold by applying vacuum or pressure. This method is particularly advantageous for creating large, thin-walled parts and is often used to manufacture disposable medical trays, packaging for sterile instruments, or protective covers for diagnostic devices.
Each of these forming methods plays a vital role in the medical device industry. They allow manufacturers to choose the best technique based on factors such as the complexity of the design, the material properties required, and the volume of production. Selecting the right method ensures that the final product meets the stringent safety, reliability, and regulatory standards necessary for medical applications. The process is not only about shaping plastic; it is about ensuring that every component used in patient care is manufactured to the highest quality.
Building a prototype, particularly for a medical device, requires careful selection of materials that meet both design and regulatory requirements. At the core, you will need a combination of structural, functional, and sometimes even biocompatible materials to ensure that the prototype not only mimics the final product’s functionality but also adheres to stringent medical standards. For the prototype itself, you may begin with medical-grade plastics such as polycarbonate, polypropylene, or polyethylene, which are commonly used in devices that come into contact with patients. These materials are chosen because they have been proven to be durable, safe, and resistant to various sterilization methods, which is essential for any device used in a healthcare setting.
For rapid prototyping, you might also use materials suitable for 3D printing, such as biocompatible resins, ABS, or PLA. Although these materials may not match the final production properties, they are ideal for early-stage testing and design validation. If the device requires components with flexible or soft properties, thermoplastic elastomers (TPE) or silicone might be necessary. These materials are often used in medical applications like seals, gaskets, or even wearable devices, where comfort and flexibility are critical.
In addition to the plastics used for the parts, you may need mold materials for creating prototype molds if you opt for low-volume injection molding. Aluminum is a common choice for prototype molds due to its machinability and lower cost compared to hardened steels. Alongside these, you might also require adhesives, fasteners, or even specialized coatings that ensure the device is compatible with bodily fluids or sterilization processes.
Furthermore, in a medical prototype, it’s essential to consider any ancillary components such as sensors, microelectronics, or even specialized inks for labeling. These components should also meet medical regulatory standards and be compatible with the primary materials. Documentation, such as Material Safety Data Sheets (MSDS) and biocompatibility certifications, will be required to verify that the materials are safe for medical use.
In summary, the materials you choose for prototyping a medical device must support the design, allow for rapid iterations, and eventually transition into a production-ready form that meets all relevant health and safety standards. The right mix of materials is key to creating a prototype that is both functional and compliant with the rigorous demands of medical applications.
Injection molding is widely recognized as the most common method for manufacturing plastic products, particularly in high-volume and high-precision applications such as those found in the medical device industry. In injection molding, molten plastic is injected under high pressure into a mold cavity that is designed to form the final shape of the product. This method is prized for its ability to produce complex shapes with high dimensional accuracy and excellent surface finish, which are critical for many medical devices—from components used in surgical instruments to housings for diagnostic equipment.
For medical applications, injection molding offers several distinct advantages. First, it enables the use of biocompatible and sterilizable materials such as medical-grade polycarbonate, polypropylene, and polyethylene. These materials are essential when manufacturing devices that come into direct contact with patients or are used in sterile environments. The process is highly repeatable, ensuring that every part produced meets stringent quality and regulatory standards. Consistency is paramount in medical manufacturing, where even minor deviations can compromise the safety or functionality of a device.
Moreover, injection molding allows for the integration of complex features such as micro-texturing, thin walls, and precise tolerances, which are often required in sophisticated medical devices. With advanced computer-aided engineering (CAE) and simulation tools, engineers can optimize mold design and process parameters to reduce cycle times and minimize waste, further enhancing efficiency. This method also supports the incorporation of over-molding and insert molding techniques, which are useful for integrating multiple materials or components into a single medical device.
While the initial investment in mold design and fabrication can be high, the per-part cost in injection molding decreases significantly with volume, making it cost-effective for large-scale production runs typical in the medical field. The method’s ability to produce high-quality, consistent parts makes it indispensable in the production of life-saving devices and diagnostic tools. In summary, injection molding is the backbone of modern plastic manufacturing, especially in the healthcare sector, where quality, precision, and safety are non-negotiable.
The life expectancy of a plastic injection mold can vary widely depending on several factors such as the mold material, the complexity of the design, the production volume, and the type of plastic being used—all of which are particularly important in medical device manufacturing. High-quality production molds, typically made from hardened tool steel, can last for millions of cycles if properly maintained. In a medical context, where the parts produced—such as components for surgical instruments, diagnostic devices, or implantable components—must meet extremely high standards, the durability and longevity of the mold are critical. A well-designed and maintained mold ensures that each part conforms to exacting tolerances and surface finish requirements, reducing the risk of defects that could compromise patient safety.
In contrast, molds used for prototyping or short-run production, often made from materials like aluminum or softer steels, might only be suitable for a few thousand to tens of thousands of cycles. These molds are typically used during the early stages of product development or for pilot clinical trials where rapid iteration is more important than long-term durability. Although these prototype molds are less expensive and quicker to produce, they are not intended for the rigorous demands of mass production.
Other factors that can affect a mold’s life expectancy include the type of plastic used (some resins are more abrasive or require higher injection pressures), the design complexity (intricate details may cause localized wear), and the maintenance practices employed by the manufacturer. In the medical field, where regulatory compliance and consistent quality are paramount, any degradation in mold performance can have serious implications. Regular maintenance, including cleaning, inspection, and repair, is essential to extend the life of the mold and ensure that it continues to produce parts that meet stringent medical standards. Overall, while a production mold in a high-volume medical manufacturing setting may be expected to last for millions of cycles under optimal conditions, every aspect of its use—from material selection to maintenance—must be carefully managed to maintain quality and safety.
Plastic injection molding, while a well-established process, can be considered challenging, especially in the context of medical device manufacturing where precision, consistency, and regulatory compliance are paramount. The process itself involves injecting molten plastic into a mold cavity at high pressure, a procedure that requires meticulous control over numerous variables. In the development of medical devices, engineers must pay close attention to factors such as material selection, mold design, cooling rates, and injection pressures. Any deviation can lead to defects like warping, incomplete filling, or surface imperfections, which may compromise the safety or functionality of a device intended for patient use.
The difficulty in plastic injection molding is not solely in the actual molding process but also in the design and fabrication of the molds themselves. Molds used for medical products often need to achieve extremely tight tolerances and smooth surface finishes to meet stringent biocompatibility and regulatory standards. Additionally, many medical devices have complex geometries that require advanced mold designs, including features like slides, lifters, or hot runners. These design complexities add layers of difficulty and require extensive simulation, testing, and iterative refinement before production can commence.
Moreover, once the process is in production, continuous monitoring and maintenance are essential. Variations in material batches, changes in environmental conditions, or even minor wear in the mold can lead to inconsistencies. In a medical setting, where even a small defect can have serious implications for patient safety, these challenges underscore the need for rigorous quality control and validation procedures. While the fundamental principles of injection molding are straightforward, achieving the level of precision required for high-quality medical devices requires specialized knowledge, experience, and state-of-the-art equipment. Therefore, while plastic injection molding is a well-understood and widely used process, it demands a high level of technical expertise and attention to detail to overcome its inherent challenges in a medical manufacturing environment.
When comparing injection molding and 3D printing, especially in the context of medical device manufacturing, it’s important to consider both upfront costs and long-term production expenses. Injection molding typically involves a high initial investment because of the cost of designing and fabricating a precision mold. This mold, which must meet strict quality and biocompatibility standards for medical applications, can be expensive to produce—sometimes costing tens of thousands of dollars. However, once the mold is created, the per-part cost of injection molding is very low, making it highly cost-effective for high-volume production. In medical manufacturing, where thousands or even millions of components like housings for diagnostic equipment or disposable syringe parts are produced, the economies of scale make injection molding a financially sound option.
On the other hand, 3D printing, also known as additive manufacturing, has a much lower initial cost since it does not require the creation of a mold. This method is ideal for rapid prototyping and low-volume production, allowing for quick iterations and design adjustments. In the medical field, 3D printing is often used for creating prototypes of devices such as surgical guides, implant models, or custom prosthetics, where the ability to quickly produce a functional model outweighs the higher per-unit cost. However, as production volumes increase, the cost per part in 3D printing remains relatively high compared to injection molding. Additionally, the surface finish and mechanical properties achievable with 3D printing may not always meet the stringent standards required for final medical products.
Therefore, while injection molding is more expensive upfront due to the cost of mold fabrication, it becomes significantly more economical at scale. In the medical industry, where regulatory compliance, consistency, and high-volume production are critical, injection molding is often the preferred method for final production. In contrast, 3D printing is an excellent tool for early-stage development, custom applications, and low-volume runs where flexibility and speed are more important than per-part cost. Both methods have their place in the development lifecycle of a medical device, and the choice ultimately depends on the production volume, complexity of the design, and the specific requirements of the application.
Contact our professional team now for a same-day quote and risk-free project evaluation. Benefit from ISO 8 cleanrooms, advanced machines, and 12-hour fast response in medical injection molding.