Medical injection molding is a highly precise manufacturing process used to create durable, high-quality components for the medical industry. This technique plays a vital role in producing medical devices that meet strict standards for safety, functionality, and reliability. Thermoplastic injection molding medical components must comply with FDA regulations to ensure they are safe for patient use. The process often occurs in cleanroom environments to avoid contamination, and the parts are produced with strict tolerances to guarantee optimal performance. By leveraging advanced thermoplastic materials and injection molding techniques, manufacturers can produce complex medical devices that meet the rigorous demands of modern healthcare. Thermoplastic injection molding medical creates durable, precise devices by molding molten medical-grade plastics like polyethylene into shapes.
Low-Volume to High-Volume Production Capabilities
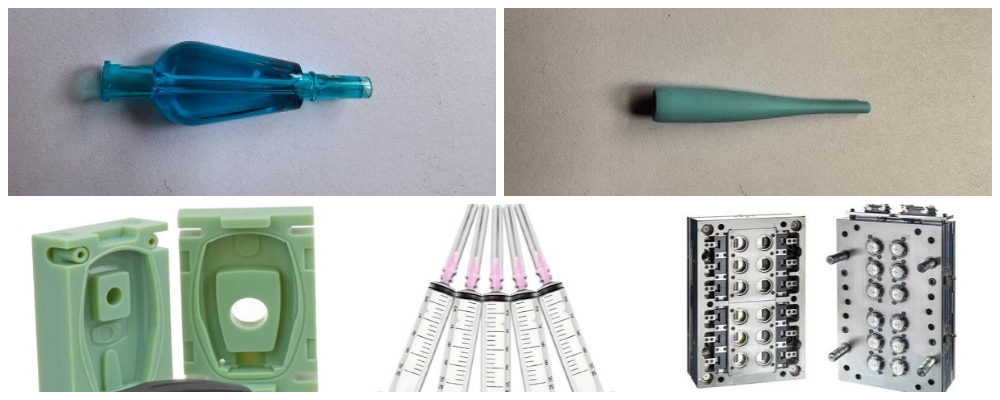
Attributes | Details |
---|---|
Place of Origin | Dongguan, Guangdong, China |
Brand Name | LY Medical Injection Mold |
Product Name | Thermoplastic Injection Molding Medical |
Material | Medical Plastic |
Application | Medical Industry |
Service | Plastic Parts Molding; Customized Services Available |
Size/Color | Customized |
Shape | Customized Shape |
Logo | Customized Logo Acceptable |
Processing Services | Molding, Cutting |
Certification | ISO9001 |
Surface Treatment | Customized Surface Texture |
Production Process | CNC, High Speed Engraving, EDM, Wire Cutting, Drilling, Injection Molding, etc. |
Technology | Thermoforming |
Drawing Format | STP STEP IGS CAD |
What is Thermoplastic Injection Molding Medical
The injection molding process for medical devices, specifically thermoplastic injection molding medical, is a highly controlled method that ensures precision and quality in the production of medical components. This process, often utilizing precision mold medical techniques, involves several key steps that contribute to producing durable, accurate, and functional medical parts. Below is an overview of the general process and materials used in thermoplastic injection molding for medical applications.
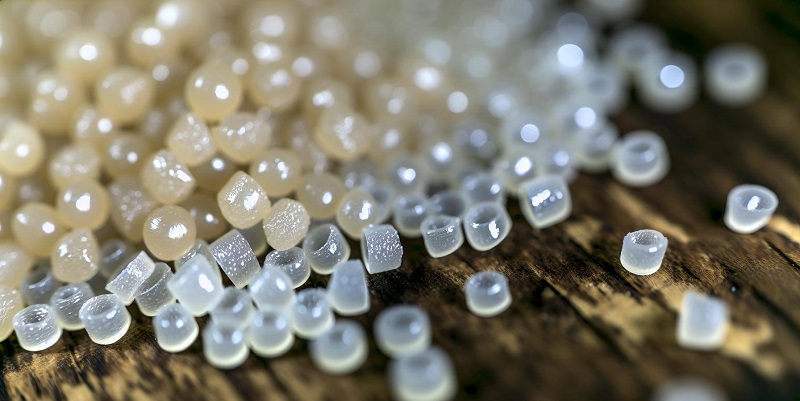
Thermoplastic Molding Overview
Thermoplastic injection molding is a manufacturing process where thermoplastic materials are melted and injected into molds to create specific shapes. This technique is ideal for producing large quantities of consistent and durable parts. Compared to thermoset molding, thermoplastic injection molding is more versatile and cost-effective, especially for medical devices that require tight tolerances and high precision. The ability to re-melt and re-shape thermoplastics makes it suitable for rapid prototyping and mass production, ensuring that thermoplastic injection molding medical components can meet both high-performance standards and regulatory requirements.
Thermoplastic Injection Molding General Process
Melting Plastic Resin Pellets: The process begins with the heating of plastic resin pellets. These materials are selected for their durability, flexibility, and ability to withstand medical use. The pellets are melted into a viscous liquid that can be injected into molds.
Injection into Molds: The molten plastic is then injected into a mold under high pressure. The molds are custom-designed to create the precise shape of the medical device. Accurate control over the temperature and pressure during this step ensures that the components maintain consistent quality.
Cooling and Solidification: After injection, the plastic is cooled and solidified within the mold, retaining the shape formed during the molding process. This is a critical step, as it ensures the medical device maintains its intended size and structure.
Removal and Finishing: Once cooled, the molded part is removed from the mold, and any excess material is trimmed or finished to meet the exact specifications required for medical applications. The final product is then tested for compliance with medical standards and specifications.
Thermoplastic Injection Molding Steps to Steps
- Material Selection:
The first step in the process is selecting the appropriate thermoplastic material based on the desired properties for the medical device. Materials like polycarbonate, polyethylene, polypropylene, and PEEK are often chosen for their strength, biocompatibility, and chemical resistance. - Melting:
The selected thermoplastic material, usually in pellet or granule form, is heated in a barrel until it reaches its molten state. The temperature is carefully controlled to ensure the material flows smoothly without degradation. - Injection:
Once the material is melted, it is injected into a precisely designed mold under high pressure. This step requires accuracy to ensure the molten material fills the mold completely, forming the part’s exact shape. - Cooling and Solidifying:
After the injection, the mold is cooled, and the material solidifies into the final shape. The cooling process is carefully managed to prevent defects like warping or shrinkage. - Ejection:
Once the component has cooled and solidified, the mold opens, and the part is ejected. The part is then ready for any necessary secondary operations, such as trimming or finishing.
Thermoplastics, Thermoset Plastics and Elastomers (rubbers)
Thermoplastic injection molding is a widely used process for manufacturing high-precision components in various industries, including the medical sector. With thermoplastic injection molding medical, manufacturers can produce components that meet the stringent standards required for medical applications, such as durability, safety, and regulatory compliance. This process is efficient for mass production and offers several advantages over other molding techniques like thermoset molding.
- Thermoplastics: Common thermoplastics used in thermoplastic injection molding medical include polycarbonate, ABS (Acrylonitrile Butadiene Styrene), and PVC (Polyvinyl Chloride). These materials are chosen for their excellent mechanical properties, biocompatibility, and the ability to be sterilized for medical use.
- Thermoset Plastics: While thermoplastics are widely used, thermoset plastic accepted for medical device manufacturing is also utilized for certain applications. Thermosets have unique properties, such as high heat resistance and the ability to maintain structural integrity under stress, making them ideal for components that require durability in demanding medical environments. By carefully selecting thermoset plastic used for medical device manufacturing, plastic medical device manufacturers can ensure the production of high-quality, durable components that meet stringent industry standards.
- Elastomers (rubbers): Rubbers are materials that exhibit elastomeric properties. They can be stretched to extension and will spring back when the stress is released.
Thermoplastics represent 90% by weight of all plastic used worldwide. Unlike most thermoset plastics, thermoplastics are processable without any serious loss of properties. By carefully selecting thermoset plastic used for medical device manufacturing and closely controlling the injection molding process, manufacturers can produce medical devices that meet both functional and regulatory requirements, ensuring safety and performance in critical healthcare applications.
Machines Used in Thermoplastic Injection Molding
Injection Molding Machines
The key equipment in thermoplastic injection molding medical is the injection molding machine. These machines consist of several components that work together to ensure high-quality parts:
- Clamping Unit: Holds the mold in place during the injection process.
- Injection Unit: Melts and injects the thermoplastic material into the mold cavity.
- Cooling System: Controls the temperature to ensure the material cools uniformly.
- Mold Tools: Custom-designed molds that shape the component to the desired specifications.
- Ejection System: Removes the molded part after cooling.
Molds
Precision-engineered metal molds define the shape of the final product. Molds typically consist of a cavity (female part) and a core (male part) and may include cooling channels for temperature regulation.
Hopper Dryer
Prepares thermoplastic pellets by removing moisture to ensure consistent melting and molding quality.
Temperature Controllers
Maintain precise heating in the injection unit and molds, ensuring even material flow and proper cooling.
Robotic Arms
Automate part removal, assembly, or secondary operations, improving efficiency and consistency.
Quality Inspection Tools
Include sensors, cameras, and automated systems to ensure parts meet precise dimensions and industry standards.
These machines work together to deliver precise and reliable thermoplastic injection molding results.
Manufacturing & Assembly: Thermoplastic Injection Molding Medical
In the medical device manufacturing process, assembly is a crucial stage that ensures all components are integrated correctly to function as intended. The use of thermoplastic injection molding medical plays a pivotal role in creating highly accurate and durable parts, while advanced techniques such as insert injection molding help combine different materials for more complex medical devices. Below, we explore the key processes in manufacturing and assembly.
Insert Injection Molding
- Combination of Metal and Plastic: Insert injection molding is a specialized process that involves placing metal components, such as pins, inserts, or clips, into the injection mold before injecting the molten thermoplastic material. This method is particularly useful for producing medical components like needles, EKG leads, and other parts that require both strength and precision.
- Benefits for Medical Devices: The combination of metal and plastic in a single part improves the overall functionality and durability of the medical device. For example, metal inserts can provide structural strength, while thermoplastic materials, molded around the metal, offer flexibility, resistance to wear, and ease of sterilization.
- Precision and Durability: Insert injection molding allows for exacting tolerances in the final product. This is essential for medical devices where any slight imperfection could impact performance or safety. The thermoplastic materials used in this process are often designed to meet stringent requirements for biocompatibility, chemical resistance, and temperature stability.
Thermoset Plastic Accepted for Medical Device Manufacturing
Thermoset plastic accepted for medical device manufacturing is also a critical component in certain medical applications. Unlike thermoplastics, thermoset plastics cure during molding and cannot be remolded. These materials are known for their excellent chemical resistance, high thermal stability, and durability, which make them suitable for components that must withstand harsh conditions, such as in surgical instruments or medical device housings. As part of the broader medical device plastic manufacturing process, thermoset plastics play a vital role in producing long-lasting, high-performance medical components.
Thermoset plastics, including epoxy and phenolic resins, offer the advantage of superior structural integrity and heat resistance. In combination with thermoplastic injection molding medical techniques, manufacturers can produce parts that require a combination of properties—such as flexibility, strength, and resistance to chemical exposure—while maintaining the required performance standards.
Assembly of Medical Devices
- Component Integration: After molding, individual components are assembled to form complete medical devices. This often involves the integration of various parts, such as molded plastic components, metal inserts, electronic sensors, and seals, into a final product. The role of the medical device assembler is crucial in this process, as careful assembly is essential to meet the stringent requirements of medical devices.
- Testing and Quality Control: During the assembly process, devices undergo rigorous testing to ensure they meet all performance, safety, and regulatory standards. This may include visual inspections, dimensional checks, and functional testing to verify that all components work together seamlessly.
- Packaging and Sterilization: Once assembled, the medical devices are packaged in sterile conditions to ensure they remain contamination-free until they are ready for use in medical settings. Packaging also plays a key role in maintaining the integrity of the device during transport and storage.
By combining the advantages of thermoplastic injection molding medical with other manufacturing techniques such as insert injection molding and the use of thermoset plastic accepted for medical device manufacturing, medical device manufacturers can produce parts that meet the highest standards of quality, precision, and safety.
FUJIU Medical Injection Mold’ Capabilities: Thermoplastic Injection Molding Medical
We are a leader in providing cutting-edge manufacturing solutions, specializing in thermoplastic injection molding medical components for the healthcare industry. With advanced capabilities and a commitment to quality, We offers a full spectrum of services that support the production of precise, safe, and reliable medical devices. Below are the key services and examples of medical injection molding applications that demonstrate their expertise.
Prototyping and Development
- Rapid Prototyping: We provides rapid prototyping services, allowing clients to quickly develop and test medical device concepts before moving into full-scale production. Using thermoplastic injection molding medical, our company can produce prototypes with high precision and accuracy, which is crucial for ensuring that devices meet stringent medical standards.
- Clinical Trials Support: Our company assists in the creation of prototypes for clinical trials, ensuring that devices are ready for testing in real-world medical environments. This service includes the fabrication of critical components that require FDA approval, ensuring we adhere to necessary regulatory guidelines.
Cleanroom Injection Molding
- Cleanroom Manufacturing: We operates advanced cleanroom facilities designed to meet the strict standards for medical device production. Our cleanroom capabilities ensure that components are manufactured in a contaminant-free environment, which is essential for producing parts used in sensitive medical applications.
- Sterility and Precision: The controlled environment allows for the production of high-precision medical devices, such as surgical tools and components that must be sterile and defect-free. Cleanroom injection molding guarantees that thermoplastic injection molding medical parts are manufactured to the highest levels of quality and safety.
Medical Device Applications
- Multi-purpose Needles: We have experience producing high-quality needles used in various medical applications. We use of thermoplastic injection molding allows for the creation of precise, durable, and sterile needles that are integral in medical procedures.
- Catheters and Pacemaker Components: Our company also manufactures critical components for catheters and pacemakers, ensuring we meet the demanding requirements of the medical industry. The use of thermoplastic injection molding medical ensures that these components are both functional and reliable, with the appropriate flexibility and strength.
- Other Medical Applications: Ours’ expertise extends to a wide range of medical device components, from surgical instruments to diagnostic tools. Our ability to customize materials and processes allows to serve diverse needs across the healthcare industry, delivering high-performance products tailored to specific medical applications.
Common Thermoplastics in the Medical Industry: Thermoplastic Injection Molding Medical
In the medical industry, thermoplastic injection molding medical plays a crucial role in manufacturing components that are both durable and safe for patient use. Various thermoplastics are utilized for their specific properties, ensuring that medical devices meet performance, safety, and regulatory standards. Below are some of the most commonly used thermoplastics in medical applications and their properties.
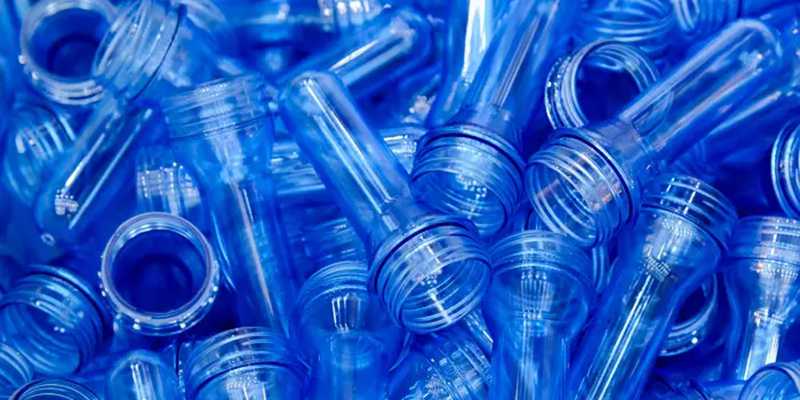
Polycarbonate (PC)
- Properties: Polycarbonate is known for its high impact resistance, optical clarity, and strength. It is a versatile material that is highly durable and can withstand extreme conditions.
- Applications: Polycarbonate is often used in the production of eyeglass lenses, medical devices like surgical instruments, X-ray shields, and other components that require transparency and durability. It can be easily molded using thermoplastic injection molding medical to create precision parts.
Acrylonitrile Butadiene Styrene (ABS)
- Properties: ABS is a tough and rigid thermoplastic that offers excellent impact resistance and is relatively easy to machine. It also has good chemical resistance and can tolerate higher temperatures.
- Applications: ABS is commonly used in the production of medical equipment housings, surgical instruments, and safety helmets. Its strength and ability to withstand frequent use make it a popular choice for medical applications requiring robust, long-lasting materials.
Polyvinyl Chloride (PVC)
- Properties: PVC is a flexible yet strong thermoplastic that is resistant to chemicals, making it ideal for use in medical devices. It can be made rigid or flexible depending on the requirements of the application.
- Applications: PVC is frequently used for medical tubing, blood bags, catheters, and IV components. Its versatility and ability to be molded precisely make it a preferred choice in medical packaging and fluid management systems.
Polypropylene (PP)
- Properties: Polypropylene is a lightweight, chemical-resistant thermoplastic with high fatigue resistance and low moisture absorption. It is known for its excellent thermal stability and resistance to sterilization processes.
- Applications: Polypropylene is widely used in the medical industry for items such as syringes, surgical trays, and medical device components that need to withstand repeated sterilization cycles. It is also commonly used for disposable medical products due to its cost-effectiveness and durability.
These materials, when used in thermoplastic injection molding medical, help ensure that medical devices meet the high standards required for safety and efficacy in patient care. Each material has specific benefits suited to different medical applications, allowing manufacturers to produce components that are both functional and reliable.
Thermoplastic Injection Molding Medical: Types, Benefits
Injection molding for medical devices is a critical process in the manufacturing of precise, durable, and reliable components used in healthcare. By utilizing thermoplastic injection molding medical, manufacturers can produce medical parts that meet stringent regulatory standards and perform consistently in real-world applications. Below, we outline the various processes, materials, and benefits of injection molding for medical devices.
Types of Thermoplastic Injection Molding Medical
- Regular Plastic Injection Molding: This is the most common method used in medical device production. The process involves injecting molten thermoplastic material into a mold to create a precise shape. Thermoplastic injection molding medical allows for high-volume production of components like syringes, surgical tools, and catheters, all with high accuracy and durability.
- Insert Molding: In insert molding, pre-formed metal or plastic inserts are placed into the mold cavity before the thermoplastic material is injected. This process is often used to create medical parts like needles and electronic connectors where both metal and plastic need to be integrated for functionality.
- Overmolding: This technique involves molding a secondary layer of thermoplastic material over a base material, such as a metal or plastic insert. Overmolding is commonly used for creating soft-touch grips or ergonomic handles on medical instruments, ensuring comfort and functionality.
- Liquid Medical Silicone Injection Molding: Liquid silicone rubber (LSR) is injected into molds to create flexible, biocompatible parts. LSR is often used for medical devices that require flexibility and resistance to high temperatures, such as seals, gaskets, and tubing.
Thermoplastic Injection Molding Medical Benefits
- High Precision: Thermoplastic injection molding medical offers extremely tight tolerances, ensuring that medical components are manufactured to the exact specifications required for functionality and safety. This precision is crucial in devices like surgical tools, implants, and diagnostic equipment.
- Regulatory Compliance (FDA): Medical devices manufactured using injection molding must meet strict regulatory standards, including FDA approval. The materials and processes used in thermoplastic injection molding medical are designed to comply with these regulations, ensuring the safety and reliability of the final products.
- Cost-Effective: Injection molding is an efficient process, especially for high-volume production. It reduces material waste and labor costs while maintaining high-quality standards. This makes it an ideal solution for mass-producing medical devices and components while keeping costs manageable.
- Suitable for Mass Production: Once the mold is created, thermoplastic injection molding medical allows for the rapid production of large quantities of medical components, making it an excellent choice for companies needing to produce devices at scale without sacrificing quality.
By combining these advanced processes, materials, and benefits, thermoplastic injection molding medical ensures that medical devices are produced efficiently, economically, and to the highest standards of quality.
Thermoplastic Injection Molding Medical: Importance of Materials and How to Choose
The Role of Materials in Thermoplastic Injection Molding Medical
Materials are critical in thermoplastic injection molding medical because they directly impact the functionality, safety, and effectiveness of the final products. Medical-grade plastics are chosen for their versatility, durability, and resistance to wear and tear, making them ideal for crafting precise and reliable medical devices. These materials are biocompatible, allowing devices to meet strict healthcare standards and ensuring safe interaction with human tissues.
Their compatibility with imaging technologies enhances diagnostic accuracy, while properties like abrasion resistance and sterilizability reduce contamination risks. Additionally, the adaptability of thermoplastics enables the production of innovative and specialized medical components, ensuring that healthcare devices evolve with industry needs.
Medical-grade plastics are cost-effective, supporting the scalable production of essential equipment to address global healthcare demands, making materials a cornerstone of the process.
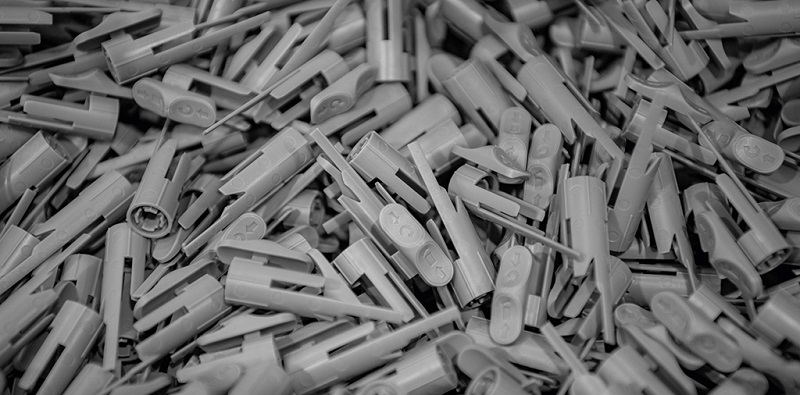
How to Choose Suitable Materials for Thermoplastic Injection Molding Medical
Selecting the right materials for thermoplastic injection molding medical requires balancing performance, safety, and regulatory compliance.
- Biocompatibility and Sterilization Requirements
- Ensure the material is biocompatible, meaning it won’t harm or irritate living tissues.
- Check sterilization compatibility to withstand processes like autoclaving, gamma radiation, or chemical disinfection. Materials must resist high heat and chemicals.
- Regulatory Compliance
- Adhere to standards like ISO 13485 for medical device production.
- Consider device classification (Class I, II, or III) to determine the material’s safety and performance requirements based on risk levels.
- Mechanical and Chemical Properties
- Evaluate hardness, flexibility, stiffness, and weight to meet functional demands. For example, hard plastics for implants or flexible materials for wearable devices.
- Ensure chemical resistance to withstand cleaning agents and bodily fluids for long-term reliability.
- Aesthetic and Usability Factors
- For visible or wearable devices, choose materials like colorable polycarbonate for appealing aesthetics.
- Opt for ergonomic and comfortable materials like silicone for patient-friendly designs.
- Common Medical-Grade Plastics
- Consider options like polyethylene, polypropylene, PVC, and polystyrene for their durability, biocompatibility, and cost-effectiveness.
By focusing on these factors, you can ensure that the materials chosen align with the specific functional and safety needs of medical devices.
FAQs about Thermoplastic Injection Molding Medical
Thermoplastics commonly used in medical devices include polyethylene (PE), polypropylene (PP), polyvinyl chloride (PVC), polycarbonate (PC), and acrylonitrile butadiene styrene (ABS). These materials are chosen for their durability, flexibility, and biocompatibility. They can be sterilized easily and meet strict regulatory standards required for medical applications. Each type of thermoplastic has unique properties that make it suitable for different medical devices, such as catheters, syringes, implants, and diagnostic equipment.
Injection molding is a versatile manufacturing process widely used to produce a variety of medical products. These include surgical instruments, IV components, medication delivery systems, diagnostic devices, and casings for medical electronics. The ability to produce complex, high-precision components in large volumes makes injection molding ideal for medical applications. The process ensures consistency, reliability, and cost-efficiency, which are critical factors in the healthcare industry.
Medical grade thermoplastic refers to materials specifically formulated and tested to meet stringent medical standards. These standards ensure the material’s safety, biocompatibility, and performance in medical applications. Medical grade thermoplastics must be able to withstand sterilization processes, resist bodily fluids, and avoid causing adverse reactions when used in or on the human body. Examples include medical grade polycarbonate, polyethylene, and polypropylene. These materials undergo rigorous testing as per FDA or ISO guidelines to ensure their suitability for medical use.
Thermoplastic injection molding is a manufacturing process used to produce parts by injecting molten thermoplastic material into a mold. The material cools and solidifies, taking the shape of the mold. This method is highly efficient for making large quantities of precise, complex parts. It is widely used in various industries, including medical, automotive, and consumer goods, due to its versatility and cost-effectiveness. The process involves several steps: melting the thermoplastic material, injecting it into a mold cavity, cooling it to solidify, and then ejecting the finished part.
Medical injection molding is a specialized manufacturing process used to produce high-precision plastic components for the healthcare and medical industry. This technique employs thermoplastic materials, which are melted and injected into custom molds under high pressure. Once cooled, the molded parts solidify into the desired shapes, such as syringes, IV connectors, or surgical instrument components.
This process is tailored for medical applications to meet strict industry standards, including biocompatibility, sterility, and mechanical integrity. Medical-grade thermoplastics like polycarbonate, polyethylene, or PEEK are commonly used due to their durability, chemical resistance, and suitability for sterilization. Precision and repeatability are critical, as these parts often perform life-critical functions. The process ensures the components are free of defects and meet stringent FDA or ISO regulations, making medical injection molding an essential manufacturing method in healthcare.
Injection molding for medical applications is costly due to several factors. First, the molds used in this process are highly intricate and require precision engineering to meet the tight tolerances and specific designs needed for medical components. These molds are often made from durable materials like hardened steel or aluminum, which adds to their cost.
Second, medical-grade thermoplastics are more expensive because they must comply with stringent regulatory standards, such as ISO 10993 for biocompatibility. These materials undergo extensive testing to ensure they are safe for medical use.
Additionally, the production environment often requires cleanrooms to prevent contamination, further increasing operational costs. The equipment must also meet high standards of accuracy and reliability, and regular quality checks are needed to ensure compliance with regulatory requirements.
Finally, the initial setup costs and the need for high precision and certification contribute to the expense of medical injection molding. These investments ensure that every part produced is safe, reliable, and meets industry regulations.
Contact our professional team now for a same-day quote and risk-free project evaluation. Benefit from ISO 8 cleanrooms, advanced machines, and 12-hour fast response in medical injection molding.