Medical atomization masks play a critical role in healthcare, particularly in respiratory therapy. These masks are used to administer medication in aerosol form, helping patients with respiratory conditions like asthma or COPD. The precision and quality of these devices are essential for patient safety and effective treatment. Wholesale injection molding of medical atomization masks is a key manufacturing method, enabling the production of high-quality, precise components at scale. This process relies on precision mold medical technology to ensure consistency and accuracy in the creation of medical devices, meeting strict regulatory standards like FDA approval. In today’s healthcare market, wholesale injection molding of medical atomization masks provides a cost-effective solution for manufacturers, allowing them to produce large volumes without compromising on quality.
Low-Volume to High-Volume Production Capabilities
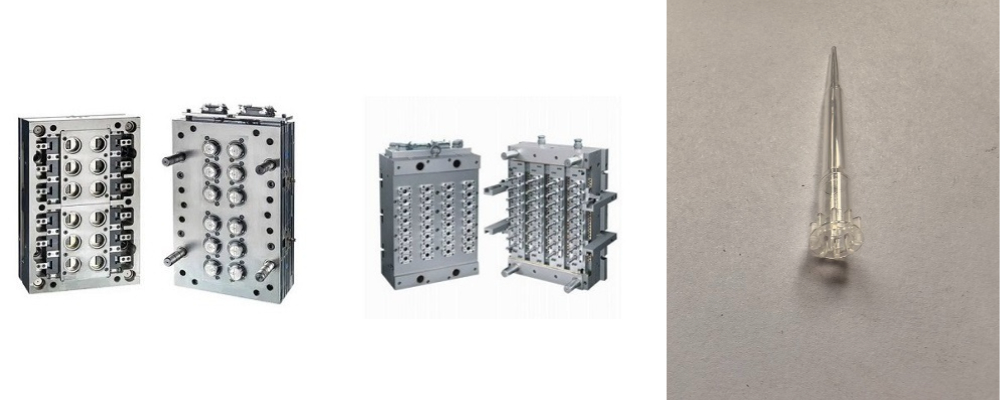
Attributes | Details |
---|---|
Place of Origin | Dongguan, Guangdong, China |
Brand Name | LY Medical Injection Mold |
Product Name | Injection Molding of Medical Atomization Masks |
Process | Injection Molding Plastic Parts |
Micro-machining or Not | Non-micro-machining |
Material | Plastic |
Tolerance | 0.01-0.05mm |
OEM/ODM | Yes |
Drawing Format | 2D/(PDF/CAD)3D(IGES/STEP) |
Logo | Customized Logo Accepted |
Product Usage | Medical Use |
Certificate | ISO13485 and ISO9001 |
Surface Treatment | Mirror Polishing |
Mold Life | 250000-300000 Shots |
Features | High Precision Injection Molded Parts |
Advantages of Wholesale Injection Molding of Medical Atomization Masks
Wholesale injection molding of medical atomization mask offers a range of advantages, particularly in terms of production efficiency, consistency, and cost-effectiveness. The medical injection molding process allows for the precise manufacturing of high-quality medical components, ensuring that each mask meets stringent healthcare standards. Let’s explore the key benefits in detail:
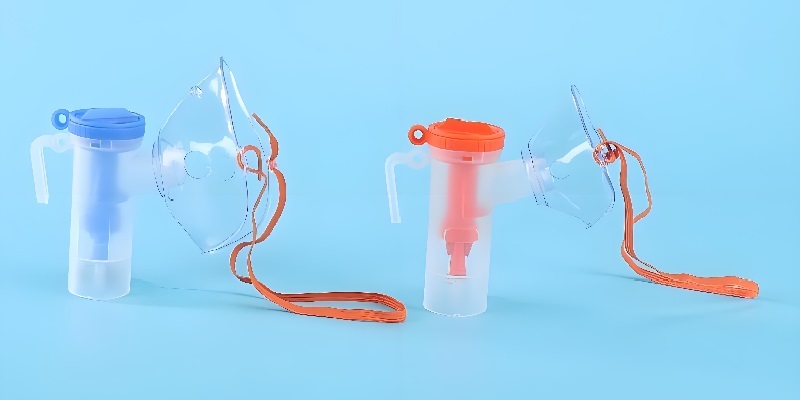
High-Volume Production with Consistency
One of the most significant advantages of wholesale injection molding of medical atomization mask is the ability to produce large quantities of masks without compromising on quality. Once the initial mold design is finalized, the medical injection molding process can be scaled up rapidly to manufacture high volumes. This is crucial for meeting the growing demand in healthcare, especially in situations where medical supplies are required in bulk.
The process also ensures repeatability, meaning that every mask produced will maintain the same high-precision standards. This consistency is essential in the medical industry, where even slight variations in design can affect the mask’s functionality and, ultimately, patient safety. Wholesale injection molding of medical atomization mask guarantees that each unit is manufactured with exacting standards, making it a reliable choice for mass production.
Cost-Effectiveness for Bulk Orders
Another key benefit of wholesale injection molding of medical atomization mask is its cost-effectiveness, particularly for bulk orders. The ability to produce large quantities efficiently helps reduce the per-unit cost significantly, making it an affordable solution for manufacturers. With the use of automated machinery and optimized production processes, the overall costs for materials, labor, and time are minimized, resulting in significant savings for manufacturers.
Furthermore, by maintaining high-quality standards throughout the production process, manufacturers can reduce the risk of defects and rework, which helps in controlling additional costs. This combination of cost savings and quality assurance makes wholesale injection molding of medical atomization mask an ideal solution for medical mask manufacturers looking to meet both their budget and performance requirements.
Material Options for Wholesale Injection Molding of Medical Atomization Masks
When it comes to the wholesale injection molding of medical atomization mask, selecting the right materials is crucial to ensuring that the masks meet both medical and patient safety standards. The materials used for injection molding must not only be durable and resistant to wear and tear but also provide comfort, chemical resistance, and ensure biocompatibility. Below, we will dive into the key material options and their specific benefits.
Choosing the Right Material for Medical Applications
In the wholesale injection molding of medical atomization mask, selecting the right material is crucial to ensuring both performance and safety. Different materials offer distinct benefits depending on the functional requirements of the medical mask.
- Polypropylene (PP):
Polypropylene is one of the most widely used materials in medical applications due to its excellent chemical resistance, low cost, and high-temperature tolerance. These properties make it ideal for producing medical atomization masks, which need to endure exposure to various cleaning agents used in sterilization processes. Its durability ensures that masks maintain structural integrity even under frequent cleaning. - Polycarbonate (PC):
Polycarbonate is known for its strength, transparency, and impact resistance. It is an excellent material choice when visual inspection is required during use, as it allows healthcare professionals to monitor the patient’s treatment progress. Additionally, polycarbonate ensures that medical atomization masks retain their structural integrity over time, even under conditions of frequent use, making it perfect for long-lasting medical components. - Silicone:
Silicone is widely favored for its flexibility, comfort, and high-temperature resistance. These qualities make silicone an ideal material for creating medical atomization masks that need to fit snugly and comfortably on the patient’s face, especially during long-term respiratory treatments. Its biocompatibility and soft touch help improve patient comfort while ensuring that the mask can endure the required conditions without degradation.
Each material choice in the wholesale medical molding of medical atomization mask is influenced by several factors, including durability, comfort, chemical resistance, and ease of cleaning. These elements are all critical for ensuring the safety and effectiveness of the mask during use in sensitive medical environments. Selecting the right material ensures the long-term performance and patient comfort, vital for successful therapeutic outcomes.
Medical-Grade Materials
In the wholesale injection molding of medical atomization mask, using medical-grade materials is essential for ensuring safety, reliability, and compliance with strict industry standards such as those set by the FDA and ISO. These materials are specifically engineered to meet the high standards required for healthcare applications, guaranteeing that the atomization masks are safe and effective for use in medical environments.
- Compliance with Industry Standards:
Medical-grade materials used in the wholesale injection molding of medical atomization mask must adhere to rigorous regulatory requirements. These include certifications from governing bodies like the FDA and ISO, ensuring that the materials are safe for prolonged exposure to patients. Compliance ensures that the masks can withstand frequent sterilization processes, which is crucial for maintaining hygiene and preventing cross-contamination in healthcare settings. - Biocompatibility:
One of the primary characteristics of medical-grade materials is biocompatibility. This ensures that the materials do not cause adverse reactions when in contact with human tissues. For example, medical-grade silicone is commonly used because it is non-toxic, hypoallergenic, and safe for extended skin contact. This is particularly important for atomization masks that need to be worn for extended periods, ensuring they don’t irritate or harm the patient’s skin. - Non-Toxicity:
The non-toxicity of medical-grade materials is another critical factor in the wholesale injection molding of medical atomization mask. These materials are designed not to release harmful substances, even when exposed to the body for long durations. This is particularly important in sensitive medical applications like respiratory therapy, where exposure to harmful chemicals can compromise patient health. Non-toxic materials ensure that masks remain safe throughout their use in medical settings, contributing to better health outcomes.
By choosing biocompatible, non-toxic materials and adhering to regulatory standards, manufacturers can produce high-quality and reliable medical atomization masks. This approach not only ensures patient safety and comfort but also supports effective healthcare outcomes, enhancing the overall efficacy of respiratory treatments.
Key Benefits of Wholesale Injection Molding of Medical Atomization Masks
The wholesale injection molding of medical atomization masks offers significant advantages in the production of high-quality, reliable medical devices. Injection molding is an efficient, precise, and cost-effective manufacturing method, and it plays a pivotal role in ensuring that medical atomization masks meet the strictest industry standards. This process also adheres to critical medical molding requirements, ensuring that each mask is produced with the necessary specifications for safety, performance, and regulatory compliance. Here are some of the key benefits of using injection molding for medical mask production.
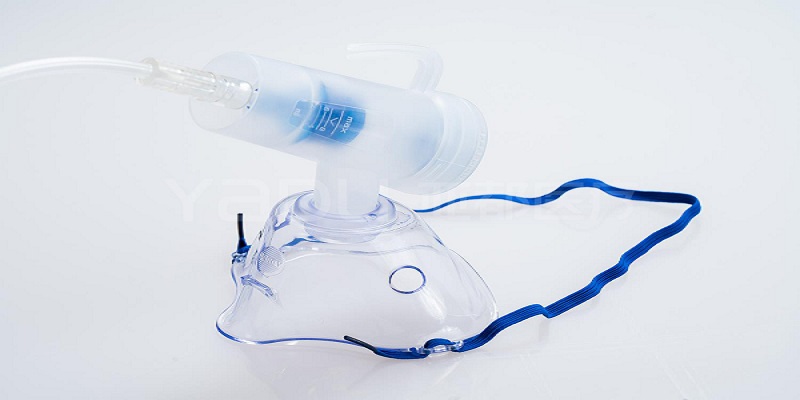
Precision and Accuracy
One of the primary benefits of customization wholesale injection molding of medical atomization mask is the ability to achieve exceptional precision and accuracy in the production process. Injection molding uses highly accurate molds and controlled injection processes, ensuring that each medical mask is manufactured to exact specifications. This is crucial in medical applications where even small deviations can result in failure to meet patient safety requirements or functional standards.
In the production of medical atomization masks, precise dimensions are vital to ensure a proper fit, consistent performance, and ease of use. The injection molding process allows manufacturers to produce components with tight tolerances, enabling the creation of highly detailed and functional designs. This ensures that medical masks are not only effective but also comfortable and reliable for patients during their treatment.
Traceability and Regulatory Compliance
Traceability and regulatory compliance are fundamental aspects of medical device manufacturing, especially for products like medical atomization masks. The wholesale injection molding of medical atomization mask ensures full traceability throughout the production process, which is crucial for tracking the batch of materials, the manufacturing conditions, and the final product’s specifications. Traceability helps maintain a record of each product’s journey from raw material sourcing to the final product, enabling swift identification and resolution of any quality issues or recalls.
Adherence to stringent regulatory standards, including FDA, ISO 13485, and CE certifications, is another key benefit of injection molding in the production of medical masks. These standards ensure that medical devices are safe, reliable, and effective for patient use. The wholesale injection molding of medical atomization masks is designed to meet these regulatory requirements by ensuring that manufacturing processes follow the prescribed guidelines, ensuring compliance with safety, quality, and performance criteria. This approach extends to other medical molding products, where strict adherence to regulatory norms ensures that every product meets the highest standards of safety and efficacy.
Durability and Functionality
Durability and functionality are essential when it comes to medical devices, particularly those used in respiratory care. Wholesaling injection molding of medical atomization masks allows manufacturers to create products that can withstand frequent sterilization processes and repeated use without compromising on performance. The robust materials used in injection molding are resistant to wear and tear, maintaining their structural integrity even under extreme conditions.
Moreover, injection molding enables the production of medical masks that provide enhanced patient safety and comfort. The precision of the molding process ensures that masks fit securely and comfortably, reducing the likelihood of leaks and improving the efficiency of medication delivery. The durability of the materials used also ensures that masks continue to function optimally throughout their intended lifecycle, providing effective treatment for patients and minimizing the risk of contamination.
Applications and Use Cases of Wholesale Injection Molding of Medical Atomization Masks
The wholesale injection molding of medical atomization mask plays a vital role in the healthcare industry by enabling the mass production of high-quality, reliable devices used in respiratory therapy. Medical atomization masks are designed to facilitate the delivery of medications in aerosol form, providing significant benefits for both patients and healthcare providers. These masks are utilized in various therapeutic applications and are integral to improving patient outcomes in respiratory care.
Role in Respiratory Therapy
One of the primary functions of wholesale injection molding of medical atomization mask is in the administration of medication through aerosol therapy. Atomization masks are essential tools for converting liquid medications into fine mist or aerosol, which can then be inhaled into the respiratory system. This method of medication delivery is particularly beneficial for patients with respiratory conditions such as asthma, COPD, or other pulmonary diseases, where it is critical to deliver medication directly to the lungs for maximum efficacy.
These masks are most commonly used in nebulizers and other respiratory devices designed to treat conditions like asthma, chronic obstructive pulmonary disease (COPD), and cystic fibrosis. By using wholesale injection molding of medical atomization mask, manufacturers can produce large volumes of high-precision masks that ensure effective drug delivery, improving the patient’s ability to breathe easier and promoting better overall health outcomes. The precise design and functionality of atomization masks produced through injection molding help ensure consistent medication dosage and efficient treatment.
Impact on Healthcare
The wholesale injection molding of medical atomization mask significantly impacts healthcare by improving the effectiveness of treatments and reducing potential complications. These masks are integral to respiratory therapy and have a direct influence on patient safety, comfort, and recovery.
- Reducing Infection Rates:
One of the key benefits of wholesale injection molding of medical atomization mask is its ability to create masks that help reduce infection rates. A well-designed atomization mask provides a controlled environment for the delivery of medication, which minimizes the risk of cross-contamination. This is especially important in medical settings where sterile conditions are vital. By ensuring that medication is delivered safely and accurately, the mask also helps protect both healthcare providers and patients from the spread of harmful pathogens. - Improved Drug Delivery:
The precision achieved through wholesale injection molding of medical atomization mask enhances the efficiency of drug delivery. These masks are designed to ensure that each treatment session delivers the right dosage of medication to the patient. This leads to better management of chronic respiratory conditions, such as asthma or COPD, and ensures that the medication is properly absorbed, promoting faster recovery. The accuracy in dosage also means that patients receive consistent and reliable care, which is vital for managing long-term conditions. - Enhancing Patient Care and Recovery:
With consistent and accurate drug delivery, patients experience improved care and faster recovery times. The design and functionality of atomization masks help ensure that medication is delivered effectively, which in turn aids in better overall health outcomes. By reducing the risks associated with improper medication administration, these masks contribute to improved long-term health, fewer complications, and a decrease in hospital readmissions. This leads to a more efficient healthcare system with better patient outcomes. - Affordable and Accessible Treatment:
The wholesale injection molding of medical atomization mask helps make high-quality atomization masks more accessible and affordable for healthcare providers. Mass production of these masks ensures that they are readily available for respiratory therapy, reducing the cost of treatment for patients and improving access to essential medications. This makes ongoing respiratory care more sustainable for healthcare providers, as it enables them to provide reliable and effective treatments without significant financial burdens. - Patient Comfort and Safety:
In addition to improving treatment outcomes, the wholesale injection molding of medical atomization mask also enhances patient comfort. The materials and design of these masks are tailored to ensure a secure, comfortable fit, reducing discomfort during treatment sessions. This contributes to better patient satisfaction and a more positive healthcare experience overall. By combining safety, precision, and comfort, atomization masks improve the quality of care and foster trust between healthcare providers and patients.
The Manufacturing Process of Wholesale Injection Molding of Medical Atomization Masks
The wholesale medical injection molding of medical atomization mask is a highly specialized manufacturing process, crucial for producing large quantities of high-quality, precise medical components. The process involves several stages, each of which contributes to the final product’s accuracy, durability, and functionality. This section will detail the key steps in the manufacturing process, from design and prototyping to the actual injection molding procedure, ensuring the production of top-notch medical atomization masks.
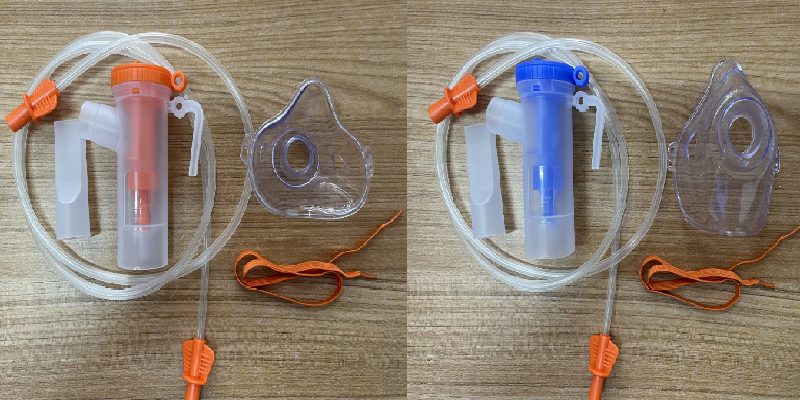
Design and Prototyping
In the wholesale injection molding of medical atomization mask, the first and perhaps most crucial step is the design and prototyping phase. The design must adhere to very specific standards to ensure that the final product performs effectively in medical applications. A precise design ensures that the atomization mask fits the nebulizer or other respiratory equipment, allowing for efficient medication delivery. During this phase, the engineers and designers work closely to create detailed blueprints of the mask, considering factors like airflow, material compatibility, and ease of use.
The prototyping process is equally important, as it involves the creation of a sample model to test the design before full-scale production begins. This prototype is thoroughly tested for factors like comfort, effectiveness in medication delivery, and durability. This step allows manufacturers to make any necessary adjustments to the design before moving forward with large-scale production.
Modern tools and technologies, such as Computer-Aided Design (CAD) software and 3D printing, are used to create accurate molds and prototypes. These technologies ensure that the custom molds used for the wholesale injection molding of medical atomization mask are highly precise, reducing the likelihood of defects during mass production and ensuring that the final product meets strict regulatory standards.
Injection Molding Process
nce the design and prototyping are finalized, the actual medical atomization mask injection molding processing can begin. This process involves the creation of the masks from raw materials using specialized injection molding machines. The process starts with selecting the appropriate materials for the mask, such as medical-grade plastics like Polypropylene (PP) or Polycarbonate (PC), which offer durability, biocompatibility, and resistance to wear and tear.
In the injection molding process, the raw material is heated to a molten state and then injected under high pressure into a custom mold using a medical molding machine. The mold is designed to shape the mask into its final form. This process allows for high precision, ensuring that each mask is identical in size, shape, and functionality. The masks are then cooled and solidified before being removed from the mold.
The quality of the medical atomization mask is heavily reliant on the precision of the molding process. Each batch undergoes strict quality checks, including visual inspections, measurements, and tests for material properties like tensile strength, flexibility, and resistance to sterilization. These checks ensure that the masks are free from defects, and that they meet the necessary regulatory requirements, including those set by the FDA and ISO standards.
Factory Wholesale Injection Molding of Wholesale Injection Molding of Medical Atomization Masks
The factory wholesale injection molding of medical atomization mask is an essential process for large-scale production of these critical healthcare components. Factories that specialize in this type of manufacturing are equipped with advanced injection molding machines capable of handling high-volume production without sacrificing precision or quality. These facilities play a key role in ensuring that medical atomization masks are produced efficiently, in compliance with strict regulatory standards, and with consistent quality across each batch.
Advanced machinery and robotics are often employed in the factory setting to streamline the manufacturing process. These technologies help improve production speed while maintaining high standards of accuracy and repeatability. Automated systems also allow for real-time quality monitoring, ensuring that every mask meets the design specifications.
Supply Injection Molding of Medical Atomization Mask Wholesale
The supply wholesale injection molding of medical atomization mask plays a crucial role in meeting the growing demand for high-quality, reliable medical masks used in respiratory therapies. This service involves the bulk production and distribution of medical atomization masks through an efficient supply chain, ensuring that healthcare providers receive the components they need in a timely manner and at competitive prices.
By utilizing supply injection molding of medical atomization mask wholesale, manufacturers can meet the healthcare industry’s need for large quantities of consistent, precise components. This process allows for the production of a wide range of medical atomization masks, each tailored to meet specific therapeutic needs, such as drug delivery via nebulizers or aerosolized medication administration.
How to Choose a Suitable Factory for Wholesale Injection Molding of Medical Atomization Masks
Selecting the right factory for wholesale injection molding of medical atomization masks is a critical step in ensuring high-quality, cost-effective, and compliant production. Given the medical nature of atomization masks, the factory must meet stringent industry standards, utilize advanced manufacturing processes, and have robust quality control mechanisms. A reliable manufacturer should possess specialized expertise in medical-grade injection molding, use certified materials, and demonstrate efficiency in large-scale production. Below are key factors to consider when choosing the right factory, categorized into essential aspects:
Compliance with Medical Standards and Certifications
Since atomization masks are medical products, the factory must comply with international health and safety regulations. A manufacturer’s certifications determine its ability to produce safe and reliable masks for medical use.
- ISO 13485 Certification – Ensures that the manufacturer adheres to medical device quality management systems.
- FDA Approval (for U.S. Market) – Required for medical devices sold in the United States.
- CE Certification (for European Market) – Demonstrates compliance with European safety and health regulations.
- GMP (Good Manufacturing Practices) – Ensures hygienic production conditions, critical for medical devices.
- Cleanroom Facilities (ISO 7 or ISO 8) – Necessary to prevent contamination during mask production.
Without these certifications, the products may not meet market regulations, leading to potential legal and safety risks.
Advanced Injection Molding Equipment and Technology
The factory must have modern injection molding machines and automation capabilities to ensure efficiency, precision, and cost-effectiveness in large-scale production.
- High-Precision Injection Molding Machines – Ensures accurate molding of mask components, preventing defects.
- Multi-Cavity Molds – Essential for mass production to improve efficiency and reduce costs.
- Automated Production Lines – Reduces human error, increases consistency, and ensures faster turnaround.
- Medical-Grade Raw Material Processing – The ability to handle FDA-approved plastics like polypropylene (PP) and thermoplastic elastomers (TPE).
- Rapid Prototyping Capabilities – Important for quick design validation before full-scale production.
Factories equipped with robotic arms, automated material feeders, and real-time monitoring systems can significantly improve production efficiency and quality.
Strict Quality Control and Testing Capabilities
Quality control is critical when producing medical atomization masks, as defects can impact patient safety. A trustworthy manufacturer must have a rigorous quality assurance system in place.
- Material Testing – Verifies that the raw materials meet medical-grade standards.
- Dimensional Accuracy Inspection – Ensures each mask meets exact specifications.
- Leak and Airflow Testing – Confirms that the atomization masks function properly when used with nebulizers.
- Batch Traceability System – Tracks production batches for recalls or quality checks.
- Automated and Manual Inspection – Combines AI-driven defect detection with human oversight.
Factories implementing Six Sigma and Lean Manufacturing principles demonstrate strong quality management and minimal defects.
Production Capacity and Lead Time Efficiency
The ability to handle large-scale orders while maintaining short lead times is crucial for wholesale injection molding of medical atomization masks. The right factory should offer:
- High-Volume Production Capacity – The ability to manufacture millions of units per month.
- Short Lead Times – Efficient workflows to ensure timely delivery, especially during high-demand periods.
- Flexible Manufacturing Capabilities – Capacity to scale production up or down based on demand.
- Logistics & Supply Chain Integration – A well-organized supply chain to prevent material shortages.
Manufacturers with Just-in-Time (JIT) production models and optimized workflow automation can meet tight deadlines without compromising quality.
Experience in Medical Injection Molding
Experience in the medical sector is essential, as medical-grade injection molding requires specialized knowledge and adherence to strict standards. When assessing a manufacturer, consider:
- Years of Experience in Medical Injection Molding – A factory with a long track record is more likely to have refined processes and regulatory compliance expertise.
- Previous Clients and Case Studies – A reputable manufacturer should have a history of supplying major medical brands.
- Customization Capabilities – Ability to adjust mold designs, materials, and specifications for unique requirements.
- Material Expertise – Deep knowledge of medical-grade plastics and compliance with sterilization requirements.
An experienced manufacturer will also have in-house design engineers to assist with mold optimization and product enhancement.
Cost-Effectiveness and Competitive Pricing
While quality and compliance should be the top priorities, cost considerations are also important for wholesale buyers. A good manufacturer should provide:
- Transparent Pricing – Breakdown of mold costs, material costs, machine time, and labor.
- Bulk Production Discounts – Lower per-unit cost for high-volume orders.
- Mold Amortization Options – Spread out mold costs over multiple production runs.
- Waste Reduction Strategies – Factories using efficient molding techniques (such as hot runner systems) can reduce material waste and costs.
A cost-effective manufacturer balances competitive pricing with high-quality output, ensuring long-term profitability for wholesale buyers.
Customer Support and After-Sales Service
Strong customer support and after-sales service are critical in maintaining a smooth partnership with the manufacturer. When evaluating a factory, consider:
- Technical Support – Availability of engineers for troubleshooting and process optimization.
- Proactive Communication – Regular updates on production progress and potential delays.
- After-Sales Support – Assistance with product defects, replacements, or mold maintenance.
- Intellectual Property Protection – Ensuring designs and molds remain exclusive to the client.
A manufacturer that prioritizes long-term partnerships will be more reliable in ensuring consistent quality and service.
Selecting the right manufacturer for wholesale injection molding of medical atomization masks requires a comprehensive evaluation of compliance, technology, quality control, production capacity, experience, cost, and customer service. The ideal factory should have ISO-certified cleanroom facilities, advanced injection molding technology, rigorous testing capabilities, and scalable production to meet high-volume demands. Additionally, competitive pricing and strong after-sales support will ensure a long-term, beneficial partnership. By carefully assessing these factors, wholesale buyers can secure a reliable, cost-effective, and high-quality supplier for medical atomization masks, ensuring success in the competitive healthcare market.
Would you like me to format this into a structured document for professional use?
FAQs about Wholesale Injection Molding of Medical Atomization Masks
The medical injection molding market is a rapidly growing sector driven by the demand for high-precision, sterile, and cost-effective medical devices. As of recent reports, the global medical injection molding market is valued at several billion dollars, with expectations for continued expansion due to the increasing need for disposable medical products, including atomization masks. Factors such as advancements in biocompatible materials, automation, and stringent regulatory standards contribute to this growth. The market includes various applications like respiratory care, drug delivery systems, and surgical instruments. The COVID-19 pandemic significantly boosted demand for respiratory masks and nebulizer components, accelerating production in this sector. The industry is further bolstered by trends in sustainability, with manufacturers exploring recyclable and bio-based polymers. Companies investing in cutting-edge injection molding technologies, such as micro-molding and high-cavitation tooling, gain a competitive edge in meeting the healthcare sector’s strict requirements.
The cost of injection molding for medical atomization masks depends on several factors, including mold design, material selection, cycle time, and production volume. The primary cost components include:
Material Costs – Medical-grade plastics such as polypropylene (PP) or thermoplastic elastomers (TPE) are commonly used, with prices varying based on quality and regulatory compliance.
Machine Time – The cost per hour of running an injection molding machine depends on machine tonnage and energy consumption.
Labor and Overhead – Skilled labor, factory overhead, and maintenance influence pricing.
Mold Costs – Initial investment in a high-precision mold can be expensive, but amortized over high-volume production.
Cycle Time & Cavitation – Faster cycle times and multi-cavity molds reduce per-unit cost.
A standard formula for estimating cost per unit:
Total Cost=[Mold Cost+(Material Cost+Machine Cost+Labor)×Units Produced]/Total Units
For wholesale production of atomization masks, economies of scale significantly reduce per-unit costs.
The time required to manufacture an injection mold for medical atomization masks varies based on complexity, material, and design intricacies. On average, it takes 4 to 12 weeks to complete a high-precision mold for medical applications. The key stages include:
Design & Prototyping (1-3 weeks) – CAD modeling, material selection, and regulatory approvals.
Mold Fabrication (4-8 weeks) – CNC machining, electrical discharge machining (EDM), and polishing.
Testing & Refinement (1-3 weeks) – Trial runs, quality control, and modifications.
Medical-grade molds must comply with FDA or ISO standards, requiring additional validation steps. Factors like multi-cavity designs and high-tolerance specifications can extend lead times. However, experienced manufacturers with advanced automation can streamline the process, reducing delays and ensuring efficient mass production of nebulizer masks and respiratory components.
The hourly cost of running an injection molding machine for medical atomization masks depends on machine tonnage, energy consumption, and operational efficiency. On average:
Small Machines (50-150 tons): $30–$70 per hour
Medium Machines (150-500 tons): $70–$150 per hour
Large Machines (500+ tons): $150–$300 per hour
Factors influencing costs include:
Energy Usage – Modern servo-driven machines are more efficient.
Labor Costs – Automated production lines reduce labor expenses.
Cycle Time – Faster cycles reduce total hours needed.
For wholesale production, manufacturers optimize machine utilization to minimize downtime and reduce per-unit costs. By using high-cavitation molds, companies can increase output per cycle, improving efficiency in mass-producing atomization masks.
The cost of an injection mold for medical atomization masks ranges from $5,000 to $100,000 depending on complexity, materials, and production needs. Key factors affecting cost include:
Cavity Count – Single-cavity molds are cheaper, while high-cavity molds for mass production cost more but lower per-unit expenses.
Material – Steel molds (e.g., stainless steel or hardened steel) are more durable but expensive, while aluminum molds are cost-effective for low-volume production.
Precision & Tolerance – Medical molds require extreme precision, increasing costs.
For large-scale manufacturing, investing in a multi-cavity, high-precision mold is cost-effective in the long run, enabling bulk production of atomization masks with consistent quality.
The total cost of injection molding per hour for medical atomization masks depends on machine type, material, and labor. Typically, the cost ranges between $50 and $300 per hour, broken down as follows:
Machine operation – $30–$150 per hour based on size.
Material cost – Medical-grade plastics range from $2 to $10 per kg.
Labor & Overhead – Automated systems lower labor costs.
For high-volume production, cost per unit can be minimized by optimizing cycle time and using high-cavitation molds. Advanced robotics and automation further reduce labor expenses, making wholesale production more cost-efficient.
For medical atomization masks, the cost of an injection mold depends on material, size, and complexity. General estimates:
Basic single-cavity mold: $5,000–$20,000
Multi-cavity production mold: $20,000–$100,000
High-precision medical-grade mold: $50,000+
Medical molds require tight tolerances, biocompatible materials, and regulatory approvals, increasing costs. While initial investment is high, wholesale manufacturers benefit from lower per-unit costs over time.
For medical atomization masks, injection molding is more cost-effective than casting for mass production. Here’s why:
Speed – Injection molding cycles are much faster, producing thousands of units per day.
Precision – Medical components require tight tolerances, which injection molding achieves better than casting.
Automation – Unlike casting, injection molding integrates automation for bulk production, reducing labor costs.
While casting is viable for low-volume or metal parts, for high-volume plastic medical products, injection molding is the superior choice due to efficiency, cost savings, and consistency.
For medical atomization masks, injection molding is significantly cheaper than machining for mass production.
Per-Unit Cost: Machining is expensive for large volumes, while injection molding drastically reduces cost per part.
Material Waste: Injection molding minimizes waste, whereas machining removes excess material, increasing costs.
Production Speed: Injection molding cycles are under 30 seconds, while machining takes minutes per part.
While machining is ideal for prototyping or low-volume, high-precision components, injection molding is the most cost-effective solution for wholesale mask production due to its ability to rapidly produce millions of units at a low cost.
Plastic injection molds are expensive due to the high cost of precision tooling, durable materials, and complex manufacturing processes. Medical atomization masks require molds made from high-grade steel or aluminum to withstand high pressures and temperatures while maintaining tight tolerances. Design complexity, sterilization requirements, and compliance with medical regulations add to the cost. Despite the initial expense, the long-term cost benefits of mass production make injection molding the most efficient and reliable method for manufacturing medical devices.
Polypropylene (PP) is the most commonly used raw material for injection molding medical atomization masks due to its affordability, flexibility, and chemical resistance. Other commonly used materials include polycarbonate (PC), polyethylene (PE), and thermoplastic elastomers (TPE), depending on the specific requirements of the mask, such as comfort, durability, and biocompatibility.
The lifespan of an injection mold depends on factors like material, maintenance, and production volume. High-quality steel molds can last for over a million cycles, making them ideal for high-volume production of medical atomization masks. Aluminum molds are cheaper but have a shorter lifespan. Proper maintenance, including regular cleaning and lubrication, extends mold longevity and ensures consistent product quality. For medical-grade molds, durability is crucial to maintaining precision and sterility.
Polyetheretherketone (PEEK) is one of the hardest plastics used in injection molding, offering high strength, chemical resistance, and thermal stability. However, for medical atomization masks, hard plastics like polycarbonate (PC) or acrylonitrile butadiene styrene (ABS) may be preferred due to their durability and cost-effectiveness. The choice of plastic depends on the balance between rigidity, flexibility, and biocompatibility needed for medical applications.
The future of injection molding for medical atomization masks is focused on automation, sustainability, and advanced materials. The use of AI and robotics in production lines is increasing efficiency and reducing labor costs. Biodegradable and antimicrobial plastics are being explored to improve safety and environmental impact. Innovations in 3D printing and hybrid manufacturing are enhancing customization and rapid prototyping. The demand for precision, cost reduction, and high-quality medical devices will drive advancements in injection molding technology, making it an essential process for the healthcare industry.
Injection molding is a specific type of molding that involves injecting molten plastic into a mold cavity under high pressure. This method is ideal for mass production of precise, complex shapes like medical atomization masks. Other molding techniques include compression molding, blow molding, and rotational molding, each suited for different applications. Compression molding involves pressing plastic into a heated mold, while blow molding is used for hollow objects like bottles. Injection molding is preferred for medical devices due to its high accuracy, efficiency, and ability to produce consistent, sterile components in large quantities.
Polypropylene (PP) is the most affordable material for injection molding medical atomization masks. It is widely available, lightweight, and offers good chemical resistance, making it suitable for medical applications. Other cost-effective options include polyethylene (PE) and polystyrene (PS), but they may not provide the necessary durability and compliance required for medical-grade products. The choice of material depends on factors like sterility, strength, and regulatory approval. Using cheaper materials may reduce costs but can compromise quality, making it essential to balance cost and performance.
The best plastic for injection molding medical atomization masks depends on biocompatibility, durability, and regulatory compliance. Polypropylene (PP) is widely used due to its lightweight, chemical resistance, and cost-effectiveness. Thermoplastic elastomers (TPE) provide flexibility and a comfortable fit, making them ideal for mask components. Polycarbonate (PC) is another option when higher strength and clarity are needed. Medical-grade ABS (Acrylonitrile Butadiene Styrene) offers durability and impact resistance. Compliance with FDA and ISO standards is crucial when selecting materials for medical devices. Choosing the right plastic ensures safety, comfort, and functionality while maintaining cost efficiency for large-scale production.
For medical atomization masks, alternative manufacturing methods like thermoforming, 3D printing, and compression molding can be cheaper for low-volume production. Thermoforming involves heating plastic sheets and shaping them over a mold, offering a lower initial investment but lacking the precision and scalability of injection molding. 3D printing is another cost-effective option for prototyping or custom designs, though it is not practical for mass production due to longer production times and material limitations. Compression molding, while suitable for some medical applications, lacks the intricate detailing and efficiency that injection molding provides. Ultimately, for wholesale production, injection molding remains the most cost-efficient option over time due to its speed and consistency.
Despite its advantages, injection molding has some drawbacks when applied to medical atomization masks. The most significant disadvantage is the high initial cost of mold creation, which can be expensive due to the precision and durability required for medical-grade production. Design modifications after mold fabrication can also be costly and time-consuming. Additionally, the process has limitations in terms of complex geometries, which may require additional processing or multi-part assembly. Material selection is critical, as only specific plastics meet medical-grade standards. The production process also requires stringent quality control to maintain sterility and prevent contamination. While it excels in mass production, it may not be suitable for limited runs or rapid prototyping due to the cost and time involved in mold creation.
Injection molding for medical atomization masks can be both cost-effective and expensive, depending on factors such as mold complexity, production volume, and material choice. While the initial cost of designing and manufacturing molds is high, the process becomes cost-efficient when producing large volumes. Since medical atomization masks require precision and consistency, injection molding is preferred due to its ability to produce high-quality, sterile components at scale. The economies of scale significantly reduce the per-unit cost, making it an affordable option for wholesale production. However, for smaller batches, the high upfront tooling costs can make it less viable. The long-term benefits, including minimal material waste and rapid production, often outweigh the initial investment.
Contact our professional team now for a same-day quote and risk-free project evaluation. Benefit from ISO 8 cleanrooms, advanced machines, and 12-hour fast response in medical injection molding.