Wholesale molding medical is a crucial process in the manufacturing of medical devices, components, and equipment. It involves the mass production of high-quality plastic parts through techniques like injection molding, overmolding, and insert molding. Precision and quality are essential in medical molding, as even the slightest defect can lead to critical failures in medical applications. These parts must meet stringent safety and performance standards, making quality control a top priority. Common materials used in wholesale medical molding include medical-grade plastics like ABS, PP, PA, and PC, which are chosen for their durability, biocompatibility, and moldability. The widespread use of these materials ensures that medical products maintain their integrity in demanding healthcare environments. Wholesale molding medical is vital for devices, with FUJIU Medical providing ISO-certified design, injection molding, and manufacturing solutions.
Low-Volume to High-Volume Production Capabilities
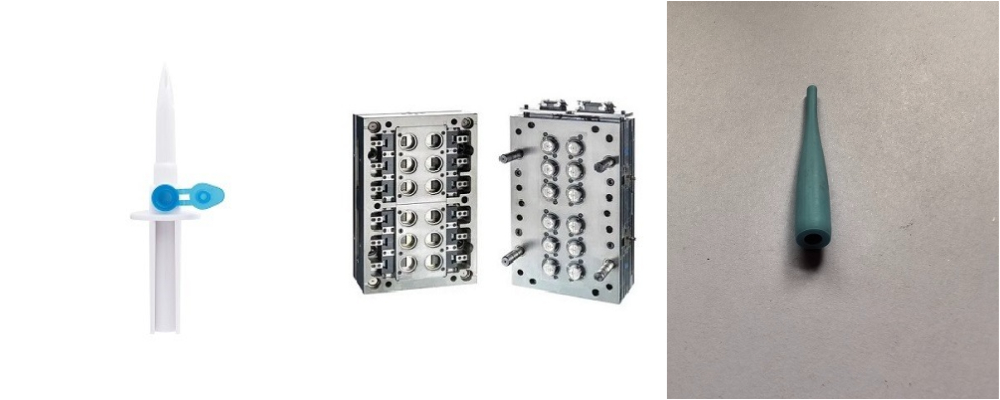
Attributes | Details |
---|---|
Place of Origin | Dongguan, Guangdong, China |
Brand Name | LY Medical Injection Mold |
Product Name | Molding Medical |
Molding Mode | Plastic Injection |
Product Material | Plastic |
Color | Customized |
Size | Customized |
Length | Customized |
Style | Customized |
Service | OEM ODM |
Processing Service | Molding, Cutting |
Features | High Precision |
Logo | Customized Logo Acceptable |
Certification | ISO9001/ISO13485 |
Supplier | Manufacturer |
Design Software | 2D/3D/CAD/DWG//STEP/PDF/UG |
Packing Details | Outer Packaging Carton Inner Packaging According to Customer Requirements |
Sales Unit | Single Item |
Port | According to Your Requirements |
Supply Capacity | 2000000 Pieces Per Month |
What is Wholesale Molding Medical and Its Importance in Healthcare?
Wholesale molding medical refers to the large-scale production of medical-grade components and devices using specialized molding techniques, such as those employed in precision mold medical. These molding processes ensure consistent quality, precision, and efficiency in the medical manufacturing industry.
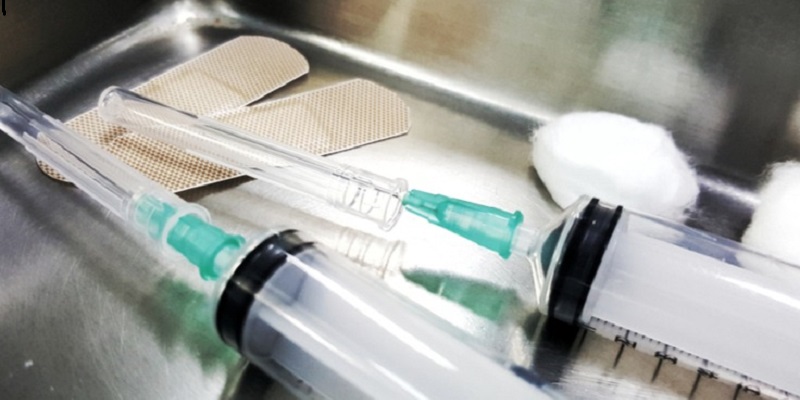
Key Processes
- Injection Molding: A versatile process where molten plastic is injected into molds to create detailed and complex components.
- Overmolding: Combines two or more materials, such as rubber and plastic, to enhance functionality and comfort.
- Insert Molding: Embeds metal or other materials into the plastic during the molding process, creating integrated and durable components.
Applications in the Medical Sector
- Medical Devices: Includes syringes, catheters, and housings for electronic devices.
- Diagnostic Equipment: Plastic parts for laboratory tools, test kits, and imaging devices.
- Surgical Instruments: Handles, cases, and protective covers for tools used in surgery.
Cleanroom Environments and Certifications
- Cleanroom Standards: Essential to prevent contamination during the molding process.
- Certifications: Manufacturers often adhere to ISO 13485 and FDA registration requirements to ensure product safety and compliance.
Wholesale molding medical and wholesale medical plastic molding play a vital role in delivering reliable, high-quality components for the healthcare industry.
Key Benefits of Wholesale Molding Medical for the Healthcare Industry
Wholesale molding medical offers numerous advantages for the healthcare industry, ensuring efficiency, reliability, and customization for various applications. Below are the key benefits of wholesale medical molding:
Cost Efficiency
- Bulk production significantly reduces per-unit costs, making it an economical solution for manufacturers.
- Optimized material usage and streamlined processes contribute to further cost savings.
Customization
- Wholesale medical molding provides tailored solutions, allowing manufacturers to design components that meet specific medical device requirements.
- Custom molds can accommodate intricate designs, unique functionalities, and various material combinations.
Scalability
- The process supports seamless scalability, from producing prototypes to transitioning into mass production for large-scale medical applications.
- Scalability ensures manufacturers can quickly respond to market demands and product development needs.
Precision
- High tolerance levels and repeatability are critical for medical parts, ensuring consistent quality and adherence to strict industry standards.
- Wholesale molding medical ensures precision in the creation of critical components, minimizing the risk of errors or defects.
By leveraging wholesale medical molding, healthcare manufacturers gain access to cost-effective, customized, and precise production solutions, enabling them to meet the stringent demands of the medical industry.
Essential Features of Reliable Wholesale Molding Medical Suppliers
When selecting a wholesale molding medical supplier, several key features ensure that the company can deliver high-quality, compliant, and efficient solutions for medical device plastic manufacturing.
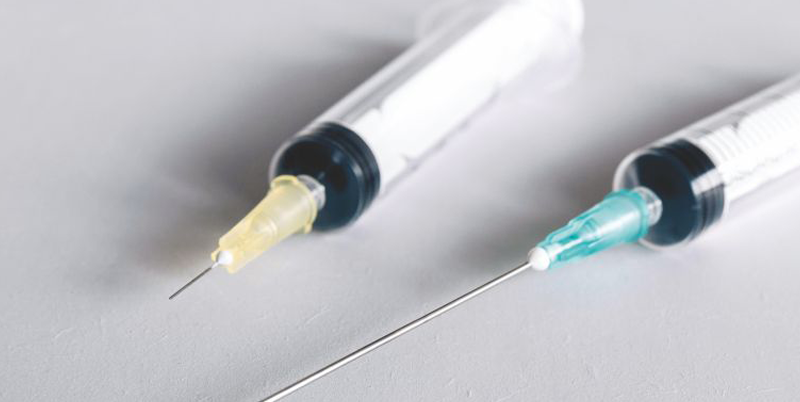
Below are the essential attributes to consider:
Certifications
- ISO 13485 Certification: Ensures that the supplier meets quality management system standards for medical devices.
- FDA Registration: Indicates that the supplier complies with FDA regulations for manufacturing medical products.
- cGMP Compliance: Adherence to current Good Manufacturing Practices ensures that all products are made in a controlled and consistent manner.
Material Expertise
- Wholesale molding medical suppliers must have a deep understanding of materials suitable for medical applications.
- Common materials used in medical device manufacturing include medical-grade silicone, PP (polypropylene), and PETG (glycol-modified polyethylene terephthalate), which offer durability, biocompatibility, and moldability.
Quality Control
- Suppliers use strict validation processes, such as IQ (Installation Qualification), OQ (Operational Qualification), and PQ (Performance Qualification) to ensure products meet regulatory and performance standards.
- Automated inspection systems and regular quality audits help maintain the precision and consistency required for medical devices.
Cleanroom Molding
- Class 8 Cleanrooms: Many wholesale molding medical suppliers operate Class 8 cleanrooms (ISO 100,000) for controlled production environments.
- ISO Class 7 and 8 Environments: These cleanroom standards ensure that parts are produced in sterile, contaminant-free conditions, which is critical for medical device manufacturing.
Medical Mold Injection Molding Wholesale
Wholesale molding medical companies that specialize in medical mold injection molding wholesale are experts in mass-producing medical components with precision. This process involves injecting melted material into molds to create consistent and detailed medical parts. A supplier that offers medical mold injection molding wholesale services is often equipped with advanced technology and expertise in high-volume production, ensuring timely and cost-effective solutions for large-scale medical device manufacturing.
These key features ensure that wholesale molding medical suppliers can deliver reliable, high-quality products that meet the stringent requirements of the medical industry.
Exploring the Various Types of Wholesale Molding Medical Services
Wholesale molding medical services offer a range of specialized solutions for the production of medical components. These services are designed to meet the stringent requirements of the healthcare industry, ensuring that medical devices are safe, functional, and compliant with regulations. Below are the main types of medical molding services provided by suppliers:
Custom Injection Molding:
- Custom Injection Molding, a key aspect of wholesale medical injection molding, is a versatile process used to create precise and complex medical device components.
- It is commonly used for producing medical packaging, housings for diagnostic equipment, surgical tools, and other essential components.
- This method ensures high-volume production with consistent quality and the ability to mold materials like medical-grade silicone, thermoplastics, and other medical-safe materials.
Overmolding
- Overmolding involves molding a material around another part (usually metal or plastic) to create a single component with enhanced functionality.
- This technique is often used to produce ergonomic handles for medical devices, ensuring that products are comfortable and easy to use.
- It can also be applied to seals that offer improved durability and protection for sensitive medical devices.
Insert Molding
- Insert Molding involves placing metal or other materials (such as inserts or wire forms) into a mold before the plastic is injected.
- This process creates stronger components, combining the durability of metal with the flexibility and formability of plastic.
- Insert molding is commonly used in medical devices where strength and precision are critical, such as in connectors, housings, and surgical instruments.
Micro Injection Molding:
- Micro Injection Molding is a highly specialized service used for producing miniaturized medical devices or medical precision parts.
- This method is ideal for creating tiny components with intricate details, such as those used in micro-surgical instruments or implants.
Value-Added Services
- Many wholesale molding medical suppliers offer value-added services to streamline production and reduce lead times. These services can include:
- Assembly: Combining molded components into a finished product or sub-assembly.
- Packaging: Specialized packaging to ensure product integrity during transportation and handling.
- Labeling: Compliance-driven labeling to meet regulatory standards.
- Sterilization: Providing sterilization services to ensure that medical products are safe for use in healthcare environments.
Plastic Molds and Products for Medical Devices Wholesale
For companies looking for plastic molds and products for medical devices wholesale, suppliers provide a wide variety of custom molding solutions to meet specific industry needs. This service includes the production of medical-grade plastic molds for everything from IV components to implantable devices. Plastic molds and products for medical devices wholesale enable efficient mass production of medical components, ensuring that these parts meet high safety and performance standards. Suppliers offering these services often provide a range of mold types, materials, and custom options to support diverse medical device requirements.
These molding services ensure that wholesale molding medical suppliers can provide comprehensive solutions for the medical device industry, from the initial medical mold design to the final, ready-for-market product.
Top Companies Specializing in Wholesale Molding Medical Solutions
When looking for reliable wholesale molding medical suppliers, it is essential to consider companies with a strong reputation in the industry, vast experience, and certifications that guarantee high-quality standards. Below are some of the top companies in the wholesale medical molding sector, known for their expertise in medical-grade plastic molding, certification standards, and client satisfaction.
Industry Leaders in Wholesale Medical Molding
- FUJIU Medical Injection Mold
- Expertise: Specializes in injection molding for medical devices, including diagnostic equipment and surgical instruments. Known for using high-quality materials like medical-grade silicone and polypropylene (PP).
- Certifications: ISO 13485, FDA registered, and cGMP compliant.
- Services: Custom injection molding, overmolding, and insert molding. Also offers value-added services like sterilization and packaging.
- MedPlast
- Expertise: Known for its precision molding and offering complete turnkey solutions for medical device manufacturing.
- Certifications: ISO 13485, FDA registered, and certified cleanroom molding.
- Services: High-precision molding for miniaturized devices, with a focus on creating sterile packaging solutions.
Wholesale Medical Connector Mold
When it comes to wholesale medical connector mold, several companies stand out for their ability to produce high-quality, durable connectors used in medical devices. Wholesale medical connector mold requires precision, as connectors play a crucial role in ensuring the safe and reliable operation of medical devices.
- FUJIU Medical Injection Mold
- Certifications: ISO 13485, FDA registered, with extensive cleanroom capabilities.
- Notable Services: Custom mold design, production of medical connectors with stringent tolerance levels, and rapid prototyping.
- Precision Connectors Inc.
- Expertise: Focuses on providing high-quality medical connector molding solutions for various medical applications, including patient monitoring systems.
- Certifications: ISO 13485, FDA registered, with a strong emphasis on cleanroom conditions for sensitive mold production.
These companies are leaders in the field of wholesale medical connector mold, known for their consistent quality, reliable delivery, and ability to meet the rigorous standards required for medical device manufacturing.
Comprehensive Factors Influencing Wholesale Molding Medical Prices
Understanding the factors that affect the price of wholesale molding medical products is crucial for users seeking cost-effective solutions without compromising quality.
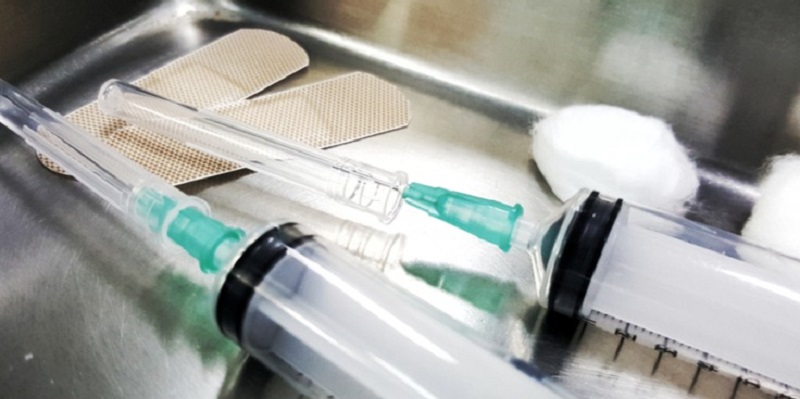
Here are detailed descriptions of the key influencing factors:
Material Selection
The choice of material is fundamental in medical molding. Medical-grade plastics like polycarbonate, polypropylene, or biocompatible materials are often required to meet strict health and safety standards.
Impact on Price: High-quality, medical-grade materials are more expensive due to their superior properties and compliance certifications. The cost of these materials directly increases the overall production cost, thereby elevating the wholesale price.
Mold Complexity and Design
The intricacy of the mold design, including the number of cavities, part geometry, and tolerances, significantly affects manufacturing.
Impact on Price: Complex molds require advanced engineering and precision machining, leading to higher initial tooling costs. These costs are amortized over production volumes, so more intricate designs result in a higher per-unit cost, affecting the wholesale price.
Production Volume
The quantity of units produced in a single run influences economies of scale.
Impact on Price: Larger production volumes spread fixed costs over more units, reducing the cost per piece and lowering the wholesale price. Smaller runs have less cost distribution, leading to higher per-unit prices.
Regulatory Compliance and Quality Standards
Compliance with medical industry regulations such as ISO 13485 and FDA guidelines is mandatory.
Impact on Price: Meeting these standards involves additional testing, documentation, and quality control processes. The extra resources required increase production costs, which are reflected in the higher wholesale price to ensure product safety and efficacy.
Manufacturing Environment
Medical products often need to be produced in controlled environments like cleanrooms to prevent contamination.
Impact on Price: Operating cleanrooms incurs additional expenses for specialized equipment, filtration systems, and monitoring. These operational costs contribute to the overall wholesale price of the medical molded products.
Labor and Automation
The balance between manual labor and automated machinery affects efficiency and cost.
Impact on Price: Automation reduces labor costs and increases production speed but requires significant upfront investment. Facilities relying more on manual processes may have higher ongoing labor expenses, influencing the wholesale price accordingly.
Tooling and Maintenance
The quality and upkeep of molds and machinery impact product consistency and lifespan.
Impact on Price: High-quality tooling ensures better product quality but at a higher cost. Regular maintenance prevents defects and downtime but adds to operational expenses, which are factored into the wholesale price.
Customization and Secondary Processes
Additional features like custom colors, surface finishes, or assembly services add value.
Impact on Price: Each customization step requires extra time, materials, or equipment, increasing the production cost. These enhancements raise the wholesale price but can provide competitive advantages or meet specific client needs.
Geographical Location and Supply Chain
The location of the manufacturing facility affects labor rates, taxes, and shipping logistics.
Impact on Price: Manufacturing in regions with higher labor or utility costs leads to increased production expenses. Additionally, longer supply chains can raise shipping costs and delivery times, all of which influence the final wholesale price.
Market Demand and Competitive Landscape
Fluctuations in market demand and the number of suppliers affect pricing strategies.
Impact on Price: High demand with limited suppliers can drive prices up, while intense competition may force prices down. Understanding market trends helps in negotiating better wholesale prices.
By thoroughly considering these factors, users can better navigate the pricing landscape of wholesale molding medical products, making informed decisions that align with their budget and quality requirements.
Key Factors Affecting Supplier Pricing for Wholesale Molding Medical
Suppliers determine their pricing for wholesale molding medical based on a variety of factors that influence production costs, market competition, and value-added services. These factors shape their ability to set competitive yet profitable wholesale prices. Below is a detailed breakdown of these factors:
Raw Material Costs
Suppliers often rely on medical-grade plastics and biocompatible materials like polypropylene, polycarbonate, and silicone, which are certified for safety and durability.
Impact on Pricing: Fluctuations in raw material prices directly affect production costs. Premium materials or price spikes in the global plastics market can lead to higher wholesale pricing to maintain supplier margins.
Tooling and Mold Development
The initial cost of creating molds, especially for custom designs, is a significant investment for suppliers.
Impact on Pricing: Complex molds with tight tolerances require advanced engineering, driving up the upfront tooling costs. Suppliers recover these expenses by incorporating a portion of the mold cost into the wholesale price, especially for low-volume orders.
Production Volume Commitments
Larger order volumes reduce the per-unit cost due to economies of scale, while smaller orders are less cost-efficient.
Impact on Pricing: Suppliers typically offer lower wholesale prices for bulk orders to incentivize high-volume production. Conversely, small orders may carry higher per-unit pricing to offset fixed costs.
Manufacturing Technology and Automation
The use of advanced machinery, robotics, and automated systems increases efficiency but requires significant investment.
Impact on Pricing: Suppliers with highly automated facilities can offer lower prices due to reduced labor costs, while those relying on manual processes may have higher operational expenses reflected in their wholesale pricing.
Regulatory Compliance and Certifications
Adhering to standards like ISO 13485 and FDA requirements involves rigorous testing, validation, and cleanroom manufacturing.
Impact on Pricing: Suppliers factor in the cost of audits, certifications, and compliance measures into their wholesale prices, as these ensure product safety and market eligibility.
Customization and Additional Services
Custom molding services, post-molding assembly, or packaging add value but increase production complexity.
Impact on Pricing: Suppliers charge higher wholesale prices for tailored solutions due to the added labor, equipment adjustments, and time required for customization.
Geographical Location and Overhead Costs
The supplier’s location influences labor rates, utility costs, and access to raw materials.
Impact on Pricing: Suppliers in regions with lower labor and operational costs may offer more competitive prices, while those in high-cost areas pass these expenses on to the wholesale price.
Supply Chain Stability and Logistics
The availability of raw materials and shipping logistics significantly impact production timelines and costs.
Impact on Pricing: Disruptions in supply chains or increased freight costs raise the supplier’s overall expenses, reflected in higher wholesale prices for end-users.
Market Competition and Demand
The number of competitors and current market demand for medical molding influence pricing strategies.
Impact on Pricing: In competitive markets, suppliers may lower prices to attract buyers, while high demand with fewer suppliers can lead to price increases.
Supplier’s Reputation and Value Proposition
Established suppliers with a strong track record of quality and reliability often charge a premium for their products and services.
Impact on Pricing: Higher prices are justified by their ability to meet stringent quality standards, provide excellent customer service, and deliver consistent performance.
By understanding these factors, suppliers of wholesale molding medical products strategically price their offerings to balance production costs, market conditions, and customer expectations. This ensures sustainable operations while maintaining competitiveness in the market.
FAQs about Wholesale Molding Medical
Injection molding in the medical sector is highly profitable due to its ability to produce high-precision parts in large volumes. The profitability depends on factors such as the complexity of the mold, material costs, and production efficiency. For medical applications, margins are often higher because of stringent regulatory requirements and the demand for high-quality, sterile components like syringes, surgical tools, and implantable devices. These specialized requirements increase the value of the products and justify higher prices. Companies investing in advanced machinery and automation can further enhance profitability by reducing labor costs and minimizing defects.
The molding process in medical manufacturing involves creating medical-grade components by injecting molten material, typically plastic or silicone, into a precision mold under high pressure. This process ensures the production of sterile, biocompatible, and highly accurate parts. It is used to manufacture items such as catheters, IV components, and diagnostic test kits. Medical-grade molding adheres to strict industry standards like ISO 13485 to ensure safety and reliability. Techniques such as overmolding (combining materials) and micromolding (creating tiny parts) are common in the medical field to meet the specific needs of complex devices.
Injection molding costs per hour vary based on machine size, complexity, and region. For medical-grade production, costs are higher due to strict quality and regulatory requirements. The hourly rate can range from $50 to $200 for standard machines, with advanced medical-grade machines costing more due to additional validations and cleanroom settings. Costs also depend on mold design, material selection (e.g., biocompatible plastics), and production volume. Investing in high-efficiency machines and automation can help manufacturers reduce costs and improve throughput in the medical sector.
In the pharmaceutical industry, molding refers to creating precise and sterile components essential for drug delivery and diagnostic tools. Common applications include producing inhalers, prefilled syringes, and vial closures. These components must meet strict medical standards for sterility, durability, and chemical compatibility. The molding process often occurs in cleanroom environments to maintain hygiene and comply with regulatory requirements such as FDA or EU MDR. Techniques like silicone molding are frequently used for their biocompatibility and flexibility, essential for drug interaction safety.
Molding and casting are both manufacturing techniques but differ in methodology and applications. Molding involves injecting or compressing material, usually plastic or silicone, into a pre-designed mold under pressure. It is ideal for high-volume production of precise, lightweight medical components like surgical tools and catheters. Casting, on the other hand, involves pouring liquid material, such as metal or resin, into a mold and allowing it to solidify without pressure. Casting is more suited for making larger, less precise parts like orthopedic implants. Molding is more prevalent in medical applications due to its ability to meet sterility and precision requirements.
Yes, injection molding offers a promising career in the medical sector. This field combines engineering, manufacturing, and quality assurance to create critical medical components. Professionals with expertise in medical-grade materials, mold design, and cleanroom manufacturing are in high demand. Career growth opportunities include roles in quality control, process engineering, and R&D. As the medical device industry continues to expand due to aging populations and advancements in healthcare, skilled workers in injection molding are well-positioned for stable, lucrative careers. Training in regulatory compliance and advanced molding technologies can further enhance career prospects.
Contact our professional team now for a same-day quote and risk-free project evaluation. Benefit from ISO 8 cleanrooms, advanced machines, and 12-hour fast response in medical injection molding.