Wholesale precision medical machining is an essential service in the medical device manufacturing industry, providing high-quality, accurate components that are critical for patient safety and performance. The increasing complexity of medical technologies has led to a growing demand for precision machining to ensure that each part meets stringent regulatory standards. CNC machining plays a crucial role in this process, offering unparalleled precision and consistency in the production of medical components such as surgical instruments, implants, diagnostic equipment, and precision mold medical applications. As the need for advanced, reliable medical devices continues to rise, wholesale precision medical machining remains a cornerstone of the industry, ensuring the supply of high-quality parts for a wide range of applications. Wholesale precision medical machining provides high-quality, precise components for medical devices, including surgical instruments, implants, and catheters.
Low-Volume to High-Volume Production Capabilities
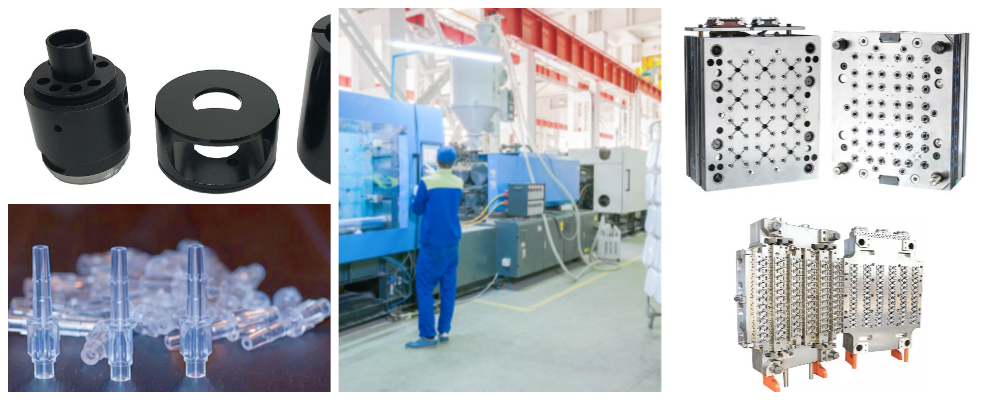
Attributes | Details |
---|---|
Place of Origin | Dongguan, Guangdong, China |
Brand Name | LY Medical Injection Mold |
Type | Drilling, Milling, Other Processing Services, Turning, Wire Cutting, Rapid Prototyping |
Is Micro-machining | Micro-machining |
Material | Plastic |
Processing | CNC Machining Center Parts |
Surface treatment | Customer Requirements |
Certification | ISO9001, ISO14001, High-tech Enterprise |
Quality Control | Inspection Report / Strict Inspection Prototype |
Application | Widely Used |
Service | OEM/ODM Service |
Size | Customized Size |
Packing Details | As Per Your Requirement |
Color | White, Black, Red, Blue, Silver, Gold, Multi-color, etc.; As per requirement |
Our Service | One-stop Service |
Logo | Customized Logo Accepted |
Shipping | DHL, Fedex, UPS, TNT, EMS, Mail, Truck, Train, Sea Shipping |
What is Wholesale Precision Medical Machining
What is Precision Medical Machining?
Precision medical machining refers to the process of manufacturing high-accuracy components used in medical devices and equipment. These components must meet strict regulatory standards, ensuring that they function flawlessly within the human body or in medical diagnostic tools. The process relies on advanced technologies such as Computer Numerical Control (CNC) machining, which uses computer programs to control the movement of tools that cut, shape, and finish materials with incredible precision.
The types of CNC machining used in medical device manufacturing include CNC drills (for creating holes and slots), CNC lathes (for shaping cylindrical parts), CNC milling (for creating complex 3D shapes with multi-axis machines), CNC routers (for cutting and drilling sheets of material), and CNC waterjet cutting (which uses high-pressure water to cut materials without generating heat). These technologies allow manufacturers to create intricate, high-tolerance parts from various materials, including metals like titanium and stainless steel, and non-metallic materials like PEEK and polycarbonate.
Precision medical machining plays a crucial role in ensuring the reliability, safety, and functionality of medical devices, such as implants, surgical instruments, and diagnostic equipment. The accuracy and repeatability of these processes are vital for ensuring that every component fits precisely and performs as intended.
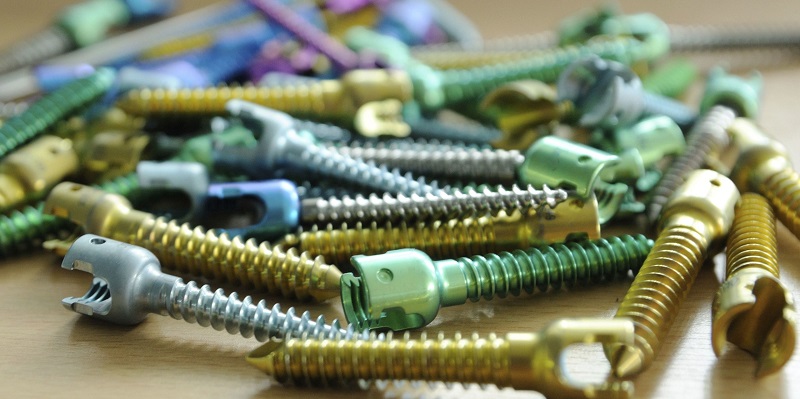
The Importance of Wholesale Precision Medical Machining
Wholesale precision medical machining is the backbone of large-scale production in the medical device industry. Its significance goes beyond just producing individual components; it enables the efficient, cost-effective, and high-quality manufacturing of complex medical devices on a mass scale.
- Material Flexibility: Wholesale precision medical machining allows manufacturers to work with a wide variety of materials. This includes both metallic materials like titanium, stainless steel, and aluminum, and non-metallic materials such as PEEK, polycarbonate, and even ceramics. Different medical devices require different materials for optimal performance, and CNC machining offers the versatility to handle these diverse materials with equal precision.
- High Tolerance and Precision: One of the main advantages of wholesale precision medical machining is the ability to achieve incredibly tight tolerances, often as small as +/- 0.025mm (0.001”). This level of accuracy is essential for components like surgical tools, implants, and other medical devices where even minor discrepancies can compromise the safety or functionality of the device.
- Repeatability and Consistency: In medical device manufacturing, consistency is paramount. Wholesale precision medical machining ensures that each part produced is identical to the last, which is essential for large-scale production. With CNC machines operating 24/7, manufacturers can meet the high-volume demands of the medical industry while maintaining consistent quality across all parts.
- Cost Efficiency: While the initial setup for precision medical machining may be high, the long-term benefits of repeatable, high-volume production make it cost-effective. The efficiency of CNC machines, combined with automated programming and skilled labor, ensures that production costs remain manageable. Additionally, precision machining minimizes material waste and reduces the risk of errors, leading to lower scrap rates and fewer defective parts.
- Support for Innovation: Wholesale precision medical machining plays a significant role in driving innovation in the medical field. As new materials and technologies emerge, CNC machining evolves to meet these challenges, helping medical device manufacturers keep pace with advancements. From new implant designs to cutting-edge surgical instruments, precision machining supports the continuous development of more effective treatments and tools.
- Regulatory Compliance: Medical device manufacturers must adhere to strict regulatory standards, including FDA regulations and ISO certifications. Wholesale precision medical machining ensures that parts are produced to meet these high standards, with rigorous quality control checks at every stage of production. This level of compliance is necessary to ensure that medical devices are safe and effective for patient use.
The Role of Wholesale Precision Medical Machining in Advancing Healthcare
Wholesale precision medical machining is essential to the production of high-quality, reliable medical devices. Through its ability to handle a variety of materials, deliver tight tolerances, and ensure consistent production, it plays a vital role in advancing the healthcare industry. Accurate medical precision machining quotes are a key factor in planning large-scale production, helping manufacturers balance cost and quality while meeting the growing demand for innovative medical technologies. As technology continues to evolve, wholesale precision medical machining will remain at the forefront of the industry, pushing the boundaries of medical device development and ultimately improving patient outcomes.
Wholesale Precision Medical Machining Near Me
Finding reliable providers of wholesale precision medical machining services locally is crucial for businesses in need of high-quality, customized medical components. The right machining provider can significantly impact product development, from the initial design to final production. Below, we discuss how to find reputable local providers, the advantages of choosing a nearby company, and tips for selecting the best service for medical applications.
How to Find Reliable Local Providers of Wholesale Precision Medical Machining Services
When searching for a local provider of wholesale precision medical machining, it’s essential to focus on several key factors to ensure the company meets your requirements. Here are some steps to guide your search:
- Research Online and Offline: Start by searching online for local machining companies. Websites, industry directories, and forums can be helpful. Offline methods, like asking for referrals from other businesses or attending trade shows, can also provide leads.
- Verify Certifications and Standards: Ensure the machining provider adheres to industry standards such as ISO 13485, which is specific to medical devices. Certification guarantees the provider’s commitment to quality control and regulatory compliance.
- Evaluate Equipment and Capabilities: Look for a company that has the necessary machinery and expertise in precision machining for medical applications. Companies with up-to-date equipment and capabilities are more likely to produce high-quality components.
- Review Client Testimonials and Case Studies: Checking reviews and testimonials from previous customers can provide insights into the company’s reliability, performance, and customer service. Case studies that highlight successful projects can also demonstrate the company’s ability to handle complex medical machining tasks.
Advantages of Choosing Local Machining Companies for Faster Turnaround and Easier Communication
Selecting a local wholesale precision medical machining provider offers several advantages, particularly when it comes to quicker production timelines and more seamless communication. Here are some of the benefits:
- Faster Turnaround Time: Proximity allows for quicker transportation of materials and products, reducing lead times and improving project efficiency.
- Easier Communication: Being nearby means you can have face-to-face meetings, which can enhance clarity and understanding of project requirements. This often leads to fewer misunderstandings and more effective problem-solving.
- Local Knowledge and Expertise: Local companies may have a better understanding of regional medical industry standards and regulations, ensuring that your products meet compliance requirements.
- Cost Savings: By choosing a local provider, you may save on shipping and logistics costs, making the overall process more cost-effective.
Tips for Selecting the Best Local Precision Machining Service for Medical Applications
Selecting the best wholesale precision medical machining provider is a crucial decision. Here are some tips to help guide your choice:
- Look for Specialized Experience: Choose a provider with experience in medical machining. Specialized expertise in machining for medical devices ensures that the company understands the unique requirements, such as biocompatibility, sterilization processes, and precision tolerances.
- Assess the Quality Control Process: Quality is paramount in medical machining. Ensure the company has a robust quality control system in place, such as automated inspection systems, 100% testing, and traceability throughout production.
- Request a Prototype: Before committing to a large order, ask for a prototype or sample. This will allow you to evaluate the provider’s machining quality and ability to meet your specifications.
- Check Support and After-Sales Services: Ensure that the provider offers good customer support throughout the manufacturing process and after delivery. A responsive company can help resolve issues quickly and keep your project on track.
By following these tips and focusing on the specific needs of your medical applications, you can find a local wholesale precision medical machining provider that best suits your business.
Wholesale Precision Medical Machining Companies
When selecting a wholesale precision medical machining company, it’s important to evaluate several factors that ensure the provider can meet your specific needs. Below is an in-depth look at some of the leading companies in this field, what to consider when choosing a reputable provider, and case studies or examples of successful projects that demonstrate the capabilities of top-tier machining companies.
Discussion of Leading Wholesale Precision Medical Machining Companies
The market for wholesale precision medical machining includes a wide range of companies specializing in high-precision manufacturing for the medical device industry. These companies provide machining services such as CNC machining, turning, milling, and surface grinding to create components used in medical devices, surgical instruments, implants, and diagnostic equipment. Leading companies in this space are known for their expertise in meeting the stringent requirements of the medical industry, including biocompatibility, regulatory compliance, and tolerance precision, often integrating medical device automation to enhance efficiency.
Some of the top providers of wholesale precision medical machining have built a strong reputation for delivering high-quality components that adhere to medical industry standards. These companies often offer a comprehensive range of services, from prototyping and custom machining to full-scale production, making them key partners for medical manufacturers.
What to Look for in a Reputable Company: Certifications, Experience, Equipment, and Customer Service
When selecting a wholesale precision medical machining company, several key factors should be considered to ensure you are working with a reputable provider capable of delivering high-quality results:
Certifications
- ISO 13485 certification: This standard is specifically for medical device manufacturers, ensuring that companies adhere to the highest quality and regulatory standards.
- FDA registration: A provider registered with the FDA is crucial for ensuring compliance with medical device regulations.
- ISO 9001 certification: This standard helps guarantee the company’s overall quality management system meets global standards for operational excellence.
Experience
- Look for companies with extensive experience in medical machining, as they will have a deep understanding of the industry’s specific challenges and requirements.
- Experience with diverse materials such as titanium, stainless steel, and PEEK is particularly valuable in the medical sector.
- A company with a proven track record in working with complex designs and tight tolerances is essential for success in precision medical machining.
Equipment
- A reputable provider should have state-of-the-art equipment such as multi-axis CNC machines, laser cutting tools, and EDM machines. This equipment ensures that they can handle complex geometries and tight tolerances, critical for medical machined components.
- The company should also have inspection tools like coordinate measuring machines (CMM) for quality control, ensuring the precision and consistency of each part.
Customer Service
- Strong customer service is essential for smooth communication throughout the machining process. A good company will provide timely responses, clear communication, and dedicated project management.
- It’s also helpful if the company can offer post-production services such as assembly, packaging, and shipping.
Case Studies or Examples of Successful Projects
Many wholesale precision medical machining companies have successfully completed challenging projects that showcase their expertise. Here are some examples:
- Custom Surgical Instrumentation: A leading machining company worked with a plastic medical device manufacturer to produce custom surgical tools. The company utilized high-precision milling and turning to produce instruments with very tight tolerances. The project was completed ahead of schedule, and the tools passed all required sterilization and durability tests.
- Orthopedic Implant Components: In this case, a machining company manufactured components for an orthopedic implant system using titanium. The company’s advanced CNC milling machines allowed them to achieve the required tolerances and surface finishes, resulting in components that met both FDA standards and the client’s specifications.
- Diagnostic Equipment Parts: A manufacturer of diagnostic equipment partnered with a machining company to produce complex components for a new medical imaging device. The provider used a combination of CNC turning and precision grinding to achieve the necessary surface finish and dimensional accuracy. The final product met the client’s quality requirements and was delivered on time, helping to ensure the timely launch of the device.
- Medical Device Prototyping: A company specializing in prototyping collaborated with a wholesale precision medical machining provider to create early-stage prototypes for a new medical device. The machining provider worked closely with the design team to adjust the components to meet regulatory requirements and mechanical specifications, leading to a successful design validation.
By selecting a reputable wholesale precision medical machining company, businesses in the medical industry can ensure that their components are made to the highest standards of precision, quality, and regulatory compliance.
CNC Medical Parts: The Backbone of Wholesale Precision Medical Machining
CNC (Computer Numerical Control) machining plays a critical role in the field of wholesale precision medical machining by enabling the production of high-precision components used in medical devices, implants, and diagnostic equipment. CNC machines allow manufacturers to create complex geometries with unparalleled accuracy, making them an essential tool for the medical industry. Below, we will explore the significance of CNC machining in medical parts production, the types of CNC machines commonly used, and the advantages of using this technology for custom medical components.
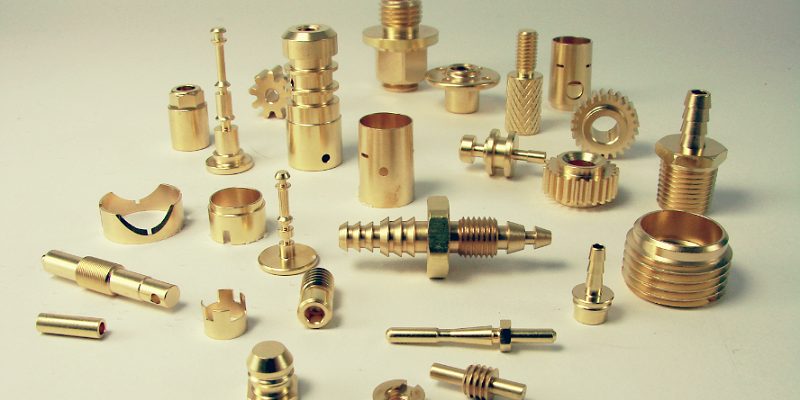
The Role of CNC (Computer Numerical Control) in Producing High-Precision Medical Components
CNC machining revolutionizes the production of medical components by automating the machining process, which improves precision, consistency, and repeatability. CNC machines use programmed instructions to control the movement of tools and machinery, allowing manufacturers to achieve tight tolerances and intricate shapes required for medical applications. This precision is essential for ensuring the safety and functionality of medical devices, which often involve small parts, complex geometries, and stringent regulatory standards.
The use of CNC machines in wholesale precision medical machining allows for the production of parts such as surgical instruments, orthopedic implants, and diagnostic components with high dimensional accuracy. CNC machines can handle a wide variety of materials, including stainless steel, titanium, and medical-grade plastics, ensuring that the components meet the material requirements for biocompatibility, strength, and durability.
Types of CNC Machines Commonly Used in Medical Machining
There are several types of CNC machines that are commonly used in wholesale precision medical machining. Each type of CNC machine has its unique capabilities and is chosen based on the complexity and material requirements of the part being produced. Here are the most commonly used CNC machines for medical applications:
- CNC Milling Machines: CNC milling machines are used to cut, drill, and shape materials with high precision. They are ideal for producing parts with intricate shapes, such as surgical instruments or custom implants. These machines operate using rotating cutting tools to remove material from a workpiece, creating complex geometries with tight tolerances.
- CNC Lathe Machines: CNC lathes are used to produce cylindrical components by rotating the workpiece against a cutting tool. These machines are commonly used in the production of medical parts such as stents, shafts, and connectors. CNC lathes provide excellent surface finishes and precise diameters, which are crucial for medical applications.
- CNC Swiss Machines: CNC Swiss machines are highly precise and are typically used for producing small, complex parts with high accuracy. They are commonly used in the production of micro-medical components such as implantable devices, connectors, and micro-surgical tools. Swiss machines are known for their ability to work with extremely tight tolerances and handle small part sizes.
- CNC Wire EDM (Electrical Discharge Machining): CNC wire EDM machines use a wire electrode to cut through conductive materials by generating electrical sparks. These machines are ideal for producing intricate, detailed parts with small diameters or thin walls, such as specialized medical tools or components used in diagnostic equipment.
Advantages of CNC Machining for Producing Complex and Custom Medical Parts
CNC machining offers several advantages when it comes to producing complex and custom wholesale precision medical machining parts. These advantages make CNC machining the go-to solution for many medical manufacturers:
- High Precision and Accuracy: CNC machines can consistently produce parts with extremely tight tolerances, often within microns, which is essential for ensuring that medical devices function correctly and meet regulatory requirements.
- Ability to Produce Complex Geometries: CNC technology allows for the creation of intricate and detailed shapes that would be impossible or difficult to achieve using traditional machining methods. This capability is particularly important for the medical industry, where parts such as surgical tools, implants, and diagnostic components often have complex geometries.
- Customization for Specific Medical Needs: CNC machines allow for easy customization of parts to meet the specific needs of a medical device. Whether it’s adjusting the dimensions of a component or creating a one-of-a-kind prototype, CNC machining offers flexibility in design and production, making it an ideal solution for custom medical parts.
- Consistency and Repeatability: Once a program is set up, CNC machines can produce large batches of parts with identical specifications, ensuring consistency and quality throughout the manufacturing process. This repeatability is essential for mass production of medical components where uniformity is critical for performance and safety.
- Material Versatility: CNC machines can work with a wide variety of materials, including metals, plastics, and composites, ensuring that the right material can be selected for each medical part. Materials such as titanium, stainless steel, and medical-grade polymers are commonly used in the production of medical components due to their biocompatibility and strength.
- Shorter Lead Times: The speed of CNC machining allows manufacturers to complete custom parts and prototypes more quickly, reducing lead times and accelerating the time-to-market for medical devices. This is particularly advantageous in the fast-paced medical industry where new products must be developed and brought to market efficiently.
By utilizing CNC machining, medical manufacturers can achieve the precision, quality, and customization required for wholesale precision medical machining, enabling the creation of complex and reliable medical components that meet industry standards.
Wholesale Precision Medical Machining: Precision Medical Ventilator Parts Injection Mold Wholesale
In the world of wholesale precision medical machining, producing high-quality medical components like ventilator parts is a critical task. Injection medical molding is a key manufacturing process used to produce these parts, ensuring both high precision and efficient production. This process is particularly vital for components in life-saving devices like ventilators, where every detail must meet stringent medical standards. Below, we explore the details of precision medical ventilator parts injection mold wholesale, the process of creating injection molds, the importance of injection molding for ventilator parts, and key considerations when sourcing these parts.
Detailed Explanation of Precision Medical Ventilator Parts Injection Mold Wholesale
Precision medical ventilator parts injection mold wholesale refers to the bulk production of ventilator parts using injection molding techniques, specifically designed to meet the high-precision needs of the medical industry. The wholesale aspect refers to the mass production of these parts in large quantities, which is critical for meeting the demand for ventilators, especially during periods of high need, such as healthcare crises.
Injection molds used for ventilator parts are designed to create components with exacting specifications, ensuring that each piece can perform its intended function with high reliability. These parts may include valves, connectors, housings, and other critical components, which require stringent tolerances and biocompatible materials to ensure safety and effectiveness in medical applications.
The Process of Creating Injection Molds for Ventilator Parts Using Precision Machining
The process of creating injection molds for ventilator parts using wholesale precision medical machining involves several key steps, which are crucial for achieving high-quality, reliable parts:
- Designing the Mold: The first step in the process is designing the mold for the ventilator parts. Using CAD (computer-aided design) software, engineers design the mold with precision, taking into account the size, shape, and functionality of the components. This design must be perfect to ensure that the parts fit together seamlessly and function as intended in the ventilator system.
- Material Selection: Once the mold design is finalized, selecting the right materials for the mold is the next critical step. The material must be durable enough to withstand the repeated cycles of the medical injection molding process while ensuring that the medical-grade plastics used in the ventilator parts are properly formed.
- Mold Creation and Machining: After the material is selected, the mold is created using CNC machining or EDM (electrical discharge machining). These processes provide the precision needed to create complex shapes with tight tolerances. The mold itself must be meticulously crafted to ensure that each part is produced to the exact specification required for medical applications.
- Injection Molding: Once the mold is ready, it is used in the injection molding process. During injection molding, heated medical-grade plastic is injected into the mold at high pressure. The plastic then cools and solidifies into the final part. The molding process ensures that each part is identical, meeting both functional and regulatory requirements.
- Quality Control: After the parts are molded, they undergo a series of rigorous quality control tests. These tests ensure that each component meets the required specifications for precision, durability, and safety. Any deviations from the expected standards are corrected before the parts are shipped out for assembly into ventilators.
Why Injection Molding is Crucial for Ventilator Parts and Other Medical Components
Injection molding is crucial for producing ventilator parts and other medical components due to the following reasons:
- Precision and Accuracy: The high precision of injection molding ensures that each component is made to the exact dimensions required, which is critical for parts that must function seamlessly in complex medical devices like ventilators.
- Material Versatility: Injection molding can work with a wide variety of materials, including medical-grade plastics, metals, and elastomers, which are essential for producing components that meet the strict biocompatibility and performance standards required in the medical industry.
- Cost-Effective for High-Volume Production: Injection molding is highly efficient for producing large volumes of parts. Once the mold is created, producing hundreds or thousands of parts becomes relatively cost-effective, making it ideal for wholesale production.
- Complexity and Customization: Injection molding allows for the production of complex geometries and custom designs that are often required in medical applications. Ventilator parts, for example, may include intricate channels, precise fittings, and specialized designs that cannot be easily produced with other methods.
- Consistency: The injection molding process ensures consistency across large production runs, which is essential for maintaining the reliability of medical devices like ventilators. Each part is produced to the same standards, ensuring high-quality and uniformity.
Key Considerations When Sourcing Ventilator Parts Through Wholesale Precision Machining Services
When sourcing wholesale precision medical machining services for ventilator parts, there are several important factors to consider to ensure that the parts meet the required standards:
- Certifications and Compliance: Ensure that the supplier follows industry standards and holds relevant certifications such as ISO 13485 for medical devices, FDA registration, and other applicable quality standards. These certifications demonstrate the company’s commitment to meeting the regulatory requirements of the medical industry.
- Material Quality: Ventilator parts must be made from high-quality, biocompatible materials that meet medical-grade specifications. It’s important to verify that the supplier uses materials that are proven to be safe and effective for use in medical devices.
- Manufacturing Capabilities: The supplier should have advanced manufacturing capabilities, including high-precision CNC machining, injection molding, and other processes necessary for producing medical components. This ensures that they can handle complex designs and tight tolerances.
- Experience with Medical Applications: Choose a provider with experience in the medical device industry. They should be familiar with the specific requirements of medical components, such as sterilization, biocompatibility, and regulatory compliance.
- Quality Assurance and Testing: A reputable supplier should have a robust quality assurance process in place to ensure that every part meets the required specifications. This includes rigorous testing for performance, durability, and safety.
- Turnaround Time: When sourcing ventilator parts, especially during times of high demand, it’s essential to ensure that the supplier can meet tight deadlines. Timely production and delivery are critical to ensure that medical devices are available when needed.
By considering these factors when sourcing wholesale precision medical machining services, manufacturers can ensure that they are receiving high-quality, reliable ventilator parts that meet the stringent requirements of the medical industry.
Commonly Used Plastics in Precision Medical Machining
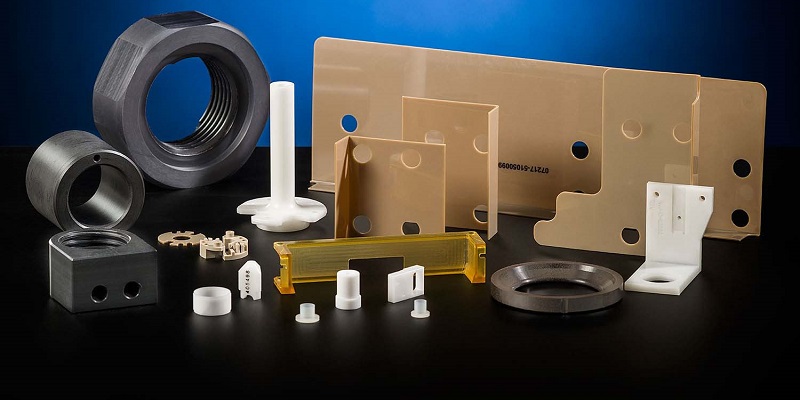
Precision medical machining involves the use of highly specialized materials designed to meet stringent requirements for biocompatibility, durability, and performance in medical devices and components. Below is an overview of some commonly used plastics in this field, focusing on their unique properties and roles in precision medical machining:
PVC (Polyvinyl Chloride)
PVC is a versatile thermoplastic widely used in the medical industry due to its excellent chemical resistance and ease of fabrication. In precision medical machining, PVC is often used for making components like tubing, blood bags, and medical device housings. Its rigidity and ability to be sterilized by heat make it ideal for applications requiring durability and resistance to a variety of solvents and biological fluids.
Nylon (Polyamide)
Nylon is a strong, wear-resistant plastic known for its high mechanical properties. It is frequently used in medical devices that require strength, flexibility, and durability, such as surgical instruments, gears, and mechanical parts. In precision medical machining, nylon is selected for its ability to withstand repeated stress, its low friction properties, and its suitability for molding and machining into intricate parts. It also has moderate chemical resistance and is often used in parts that need to be lightweight but robust.
Delrin (Acetal or Polyoxymethylene, POM)
Delrin is a high-performance thermoplastic known for its exceptional dimensional stability, low friction, and resistance to wear. It is widely used in precision medical machining for components like gears, bearings, and valves, where tight tolerances and mechanical precision are critical. Delrin is also valued for its resistance to moisture absorption, making it suitable for devices that must maintain performance in humid or wet environments, such as pumps and fluid management systems.
PTFE (Polytetrafluoroethylene)
PTFE is a highly inert plastic known for its excellent chemical resistance, non-stick properties, and electrical insulation capabilities. In precision medical machining, PTFE is used for making components that come into contact with harsh chemicals, pharmaceuticals, or body fluids, such as seals, gaskets, and tubing. Its low friction coefficient makes it ideal for use in devices that need smooth operation, like catheters and pumps. PTFE is also valued for its biocompatibility and resistance to bacterial growth, which is essential for medical devices that must meet hygiene standards.
UHMW (Ultra High Molecular Weight Polyethylene)
UHMW is known for its outstanding abrasion resistance, low friction, and high impact strength. It is commonly used in medical applications where components are subject to high wear, such as in joint replacements, surgical instruments, and prosthetics. In precision medical machining, UHMW is used to manufacture long-lasting components that need to perform well under continuous motion and stress. Its high resistance to wear and impact ensures that parts remain functional even in the most demanding medical environments.
Ultem (Polyetherimide)
Ultem is a high-performance thermoplastic known for its strength, thermal stability, and excellent dimensional stability under both high and low temperatures. In precision medical machining, Ultem is used in applications that require durability and thermal resistance, such as sterilizable medical instruments, connectors, and structural components for medical devices. It also exhibits good electrical insulating properties and resistance to harsh chemicals, making it suitable for devices in critical medical systems where reliability is paramount.
PEEK (Polyetheretherketone)
PEEK is a high-performance polymer that offers exceptional strength, chemical resistance, and biocompatibility, making it one of the most sought-after materials in the medical field. In precision medical machining, PEEK is often used for high-stress components like orthopedic implants, spinal fusion devices, and surgical instruments. PEEK’s excellent mechanical properties, along with its ability to withstand extreme temperatures, make it ideal for demanding medical applications where performance and reliability are critical. It is also highly resistant to radiation, which makes it suitable for devices that need to be sterilized using gamma or electron beam irradiation.
Acetal (Polyoxymethylene, POM)
Acetal, like Delrin, is known for its high strength, low friction, and excellent wear resistance. In precision medical machining, Acetal is often used for manufacturing gears, bearings, and other components where precision and durability are necessary. Acetal’s low moisture absorption and good chemical resistance make it ideal for use in medical devices like pumps, valves, and diagnostic instruments. Its ability to be machined to very tight tolerances is critical in precision medical applications where dimensional accuracy is crucial.
Each of these plastics plays a specific role in precision medical machining, where material properties such as strength, biocompatibility, wear resistance, and chemical resistance are essential for ensuring the safety, durability, and functionality of medical devices. Choosing the right material depends on the specific requirements of the medical device, as well as the processing techniques needed to achieve the required precision and performance.
FAQs about Wholesale Precision Medical Machining
Wholesale precision medical machining refers to the bulk production of highly accurate, custom-designed medical parts using advanced machining technologies like CNC (Computer Numerical Control) machines. These parts can include surgical instruments, implants, diagnostic equipment, and ventilator components. The process is critical for ensuring that medical devices meet the stringent regulatory standards of quality, safety, and functionality. Wholesale production helps meet the increasing demand for medical devices and ensures that parts are available in large volumes, which is essential for mass production. The importance of precision in this field cannot be overstated, as even small deviations in measurements can compromise the safety and effectiveness of medical devices. By leveraging high-precision machining, manufacturers can produce parts that perform reliably and are compliant with industry standards such as ISO 13485 and FDA regulations.
Wholesale precision medical machining utilizes a variety of materials, depending on the specific requirements of the medical device or component being produced. Common materials include stainless steel, titanium, aluminum, and biocompatible polymers, all of which are chosen for their durability, strength, and compatibility with the human body. Stainless steel and titanium are commonly used in implants, surgical tools, and prosthetics because they are corrosion-resistant and can withstand the harsh conditions of the medical environment. Biocompatible plastics and polymers, on the other hand, are used for components that require flexibility, such as connectors and housings for diagnostic devices. Each material is selected based on the particular functional, safety, and regulatory requirements of the intended medical application. The ability to machine these materials with high precision ensures that parts are produced with the necessary quality for medical use, whether for implants, surgical tools, or diagnostic devices.
In nursing, CNC typically refers to a Clinical Nurse Consultant, not a machining term. A Clinical Nurse Consultant is a specialized nurse who provides expert advice on clinical practice, helping healthcare teams improve patient care and outcomes. CNCs play a crucial role in healthcare by developing and implementing clinical policies, offering guidance on complex cases, and supporting nursing staff in improving their practice. They may work in various specialties, including surgical, pediatric, or emergency nursing, and their duties often include education, research, and leadership. This role helps ensure that nursing practices adhere to the highest standards of care, and CNCs often collaborate with other healthcare professionals to enhance patient safety and care delivery. The term CNC in nursing, therefore, focuses on advancing clinical knowledge and practice in healthcare settings.
A precision machinist is a highly skilled professional responsible for crafting precision components used in various industries, including medical device manufacturing. In the context of wholesale precision medical machining, a precision machinist uses advanced CNC machines to produce parts with exceptional accuracy and tight tolerances, ensuring that components meet the required specifications. Machinists interpret blueprints and technical drawings to set up and operate machinery, including lathes, mills, and grinders, to create parts made from metals, plastics, and composites. In the medical device industry, these parts could include surgical instruments, implants, or medical equipment components. Precision machinists must adhere to strict quality control standards, performing inspections and testing to ensure that each part functions correctly and meets regulatory requirements. Their expertise in machining processes and precision tools ensures the reliability and safety of medical devices.
CNC precision engineering refers to the use of Computer Numerical Control (CNC) machines to manufacture components with extremely high accuracy and precision. In wholesale precision medical machining, CNC precision engineering is crucial for producing parts that must meet stringent regulatory standards and tight tolerances, such as those found in the medical device industry. This technology allows for highly automated and repeatable manufacturing processes, reducing the risk of human error and ensuring consistent quality. CNC precision engineering can be used to machine a wide variety of materials, including metals, plastics, and composites, and is essential for producing intricate components used in medical devices like implants, surgical instruments, and diagnostic tools. The combination of advanced CNC machinery, software programming, and skilled technicians makes CNC precision engineering a cornerstone of high-quality, high-accuracy manufacturing in the medical field.
To calculate CNC machining cost per hour for medical device manufacturing, it’s essential to account for specific factors relevant to the medical industry, where precision and regulatory compliance are critical. Here’s a breakdown:
Labor Costs: The cost of skilled labor, including CNC machinists and quality control inspectors, should be factored in. Medical device manufacturing requires specialized expertise to ensure adherence to strict standards like ISO 13485. The labor cost can vary depending on the technician’s experience and location.
Machine Operating Costs: CNC machines in the medical industry often work with precision tolerances, requiring frequent calibration. Operating costs include energy consumption, machine maintenance, and tooling wear. Advanced machines used for medical devices may require more frequent calibration or more expensive tooling, which increases operational costs.
Material Costs: Medical-grade materials like biocompatible metals (titanium, stainless steel) or specialized polymers are often used. These materials can be more expensive than standard machining materials. Material waste, due to the need for highly precise cuts, should also be accounted for.
Regulatory Compliance and Quality Assurance: The medical device industry requires that parts meet strict regulatory standards, including FDA regulations. The cost of quality assurance (QA) processes, including testing, inspections, and certifications (like ISO 9001 or FDA approval), should be included in the hourly rate. These activities can add substantial overhead, depending on the complexity of the device.
Overhead Costs: This includes the cost of the facility, administrative support, and insurance, especially in the medical industry, where liability and insurance premiums may be higher due to the nature of the products being produced.
Once these costs are determined, divide the total by the number of productive machine hours to get the CNC machining cost per hour. For example, if all costs total $1,500 for 8 hours of operation, the cost per hour would be $187.50.
Contact our professional team now for a same-day quote and risk-free project evaluation. Benefit from ISO 8 cleanrooms, advanced machines, and 12-hour fast response in medical injection molding.